Story by Prabhakar | Concept & pictures by Mohanraj
Shiva Texyarn has carved a niche of its own in the Indian textile industry through its wide range of products. A strong commitment to innovation and the ability to boldly tread new paths has seen the company grow from strength to strength. From being one among the early movers into technical textiles to the success of its branded products, a lot seems to be happening in the company. The Textile Magazine takes a closer look at how innovation is accelerating Shiva Texyarn team’s growth.
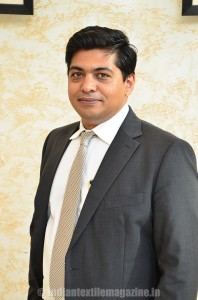
Shiva Texyarn Ltd. is part of the well-known Bannari Amman Group of companies, a diversified industrial conglomerate with interests in fields ranging from textiles and education to wind power generation and automobiles production. Bannari Amman Spinning Mills, part of the group, is one of the largest textile companies in the South.
A strong infrastructure focus has been one of the key factors behind Shiva Texyarn’s remarkable growth. The company has two spinning mills, both of which are located in Tamil Nadu. The spinning unit I at Dindugal, started in 1989, has a capacity of 39,072 spindles and a production capacity of 20 tons of cotton yarn per day. Spinning unit II at Karanampettai, Tiruppur district, started in 2009, is having 50,400 spindles and is manufacturing 100 per cent cotton yarn in the count ranges from Ne.16s to Ne.40s. The production capacity is 38 tons of cotton yarn per day. The unit boasts of an array of state-of-the-art machinery, including blowroom and carding machinery from Truetzchler Germany, comber and drawframe from Rieter Switzerland, ring frames with autodoffer from LMW India, linkconer from Murata, Japan, and testing equipments from Uster, Switzerland.
The knitting, coating and lamination divisions are also located in Karanampettai. The modern coating facility enables the company to offer a wide range of coating products which includes acrylic coated, PU coated, artist canvas and digital canvas, catering both to the Indian and export markets.
As part of the lamination division, Shiva Texyarn has a one-of-its-kind Gravure roll-based moisture cured polyurethane lamination system. The unit can bond various types of fabrics together for advanced applications, for military, outdoor, waterproof/incontinence bed products, and lingerie applications. Shiva Texyarn had established an exclusive manufacturing unit at Ganeshapuram for technical textiles in 2012. The modern processing division of the company is located at the SIPCOT industrial estate in Perundurai, Erode, Tamil Nadu.
Foray into technical textiles
The Indian textile industry has now been passing through an exciting phase with the introduction of several innovative technologies. Technical textiles is now considered the sunrise segment of the textile industry. Industry estimates point out that the country’s technical textile market would be over $30 billion by 2020. Shiva Texyarn has emerged as one of the names to watch out for in this specialized segment. Once again, the penchant for innovation has been instrumental in the company entering the fray in this rapidly growing market segment.
Shiva Texyarn’s entry into technical textiles makes for an interesting reading. Going into details regarding the phase when expansion and diversification towards technical textiles took place, Mr. Sundararaman, Executive Director of the company, said: “Our big jump into expansion started in 2005 in the case of Bannari Amman Spinning and in 2008 in Shiva Texyarn. There was more than doubling of capacity in Shiva Texyarn and tripling of capacity at Bannari Amman Spinning. We also tried to study in detail to find out where we could make a difference. We found that there were two conventional things that we were doing, fabrics and the second thing was dyeing. We found out that what we were calling “processing” in the industry was only “dyeing”. There is much more to processing than just dyeing. There is much more to processing in terms of specialized finishes. The approach to specialized finishes is what took Shiva Texyarn into technical textiles.”
Mr. Sundararaman also commented: “When we looked into the market we found out that there were two universal application technologies, namely, coating and lamination, which had excellent potential, and which would allow us to do a wide range of products. We were already strong in these areas.”
Quick dry, a grand success
Thus started a process where the think tank of Shiva Texyarn started experimenting with various substrates to see what value could be added. That is when the game changer for Shiva Texyarn – ‘Quick Dry’ – happened. Continuing, Mr. Sundararaman said: “We created a product which was not available in the market. While people had put film on fabric, nobody had used a quick drying, polyester pile fabric which was comfortable for a child. The product we conceived was uniquely Indian because the concept of using rubber sheet is found only in India”.
According to Mr. Sundararaman, when you stick two different things together, unless there is a unique difference brought about by these two things struck together, the value of the materials being used being fairly high, there is no value addition in the ultimate product. Going further into details, he observed: “So we started using a technically advanced piece, i.e., breathable polyurethane membrane which could be struck with a fabric. Similar products were already being used by international armies at that time for the jackets of armed personnel. It was also being used in specialized sportswear. We made our entry using ‘Quick Dry’ into the mattress protector segment”.
Quick Dry is manufactured using the ‘PUR’ technology, considered the most advanced lamination technology in the world. Quick Dry, which is a reusable and washable sheet, comes with an ‘OEKO Tex Standard Certification’.
Dwelling on the key trigger behind the concept of Quick Dry, Mr. Sundararaman explained: “The Indian market is very value conscious. So we thought instead of manufacturing an entire mattress protector, why not a small piece format? Why would you want to cover an entire bed when all that you need is a half a meter by half a meter fabric that will keep a child comfortable?”
There has been no looking back ever since for the Quick Dry brand. It is now the undisputed market leader in its product segment.
According to Mr. Sundararaman, the step from being a commodity manufacturer to taking a branded product into the retail market was a difficult but exciting process. A distribution network had to be created. Exclusive R&D was another aspect that needed to be taken care of. “We learnt a lot of things in the process. You can say that this process paved the way for Shiva Texyarn moving in a significant manner into the technical textiles domain”, he said.
Betting big on ‘Wulf’
The success of Quick Dry was followed by the launch of the ‘Wulf’ brand recently. The Wulf brand offers a complete range of back packs and outdoor gears and other travel products, including rucksacks, tents and sleeping bags. The range also covers clothing like jackets, tees, sweatshirts, pants and shirts. One of the key challenges that the company had to surmount was the fact that the baggage sector in India was highly unorganized, with only a handful of organized players in the fray. Shiva Texyarn did a detailed study of the market and found out that bags were moving from being perceived as mere carriers of materials to becoming fashion accessories or style statements.
“We saw a huge opportunity waiting to be tapped. We saw an opportunity for an organized player to come into this segment and satisfy the evolving aspirations of the market,” pointed out Mr. Sundararaman going into details about the initial launch of the brand.
And so the ‘Wulf’ brand was launched. Wulf incidentally is the Germanic version of the English ‘Wolf’ and was chosen because the animal had always symbolized the spirit of wilderness and adventurism.
While there were a handful of organized big name players already competing in the field, Shiva Texyarn came in with the Wulf brand with a major inherent advantage. “The advantage that we have over others is that while some of them stitch their products, some get it outsourced to contract manufacturers. So, none of them have any scope of playing at the fabric stage. Being a full-fledged player in the textile domain with the capability to dye nylon and polyester fabrics, which are the mainstay fabrics that go into backpacks, we have a upper hand over the competition,” mentioned Mr. Sundararaman, while pointing out the edge that Shiva Texyarn has over the competition.
While the Wulf brand is presently being supplied in four States – Tamil Nadu, Kerala, Karnataka and Maharashtra – the company has ambitious plans lined up for the future. It wants to focus on establishing a robust value chain first, for it already has the requisite capabilities to scale up operations. Its immediate plans include increasing the product portfolio under the Wulf brand to cover outdoor accessories, clothing such as dry fit t-shirts, cold weather insulation clothing, trolley-based soft luggage, etc. The company is also catering to specific customers with customized options in sub-segments such as camping tents and sleeping bags, as part of the Wulf brand.
A very strong R&D focus and a keen eye for detail, from the end-user point of view, have been driving product development in the company. These factors are what give the top management of Shiva Texyarn the confidence about the Wulf brand making it big, just as the Quick Dry brand.
Going into details about the research and development process, Mr. Sundararaman explained that every part of a back-up in the Wulf brand is a result of careful research. “The most important thing about a backpack is not what color it is or how many zips it has got. The most important thing is the load bearing system. Remember, children these days need to carry about 7-8 kgs on a daily basis. The weight carried does have a long-term effect on a child’s spine. We have done detailed ergonomic studies and come out with bags that are not only aesthetically pleasing and functional, but also won’t have any such long-term impact on the wearer’s spine”.
Such attention to detail, however minute, has always been a hallmark of Shiva Texyarn and has been instrumental in the company’s products standing out from the rest.
When queried on what is next on the agenda of Shiva Texyarn, Mr. Sundararaman said that the next foray would be into activated carbon based fabrics, both for military, as well as civilian uses. India is going to be a very big market for activated carbon fabrics. “With increasing pollution, activated carbon media’s demand would increase, for it is the media that is used to hold back obnoxious fumes, smells, odor from dangerous chemicals, etc. We already have the technology for the field. The future for technical textiles is certainly very bright,” remarked Mr. Sundaraman while talking about the company’s future plans.
The company is betting big on the emerging opportunities in the technical textiles field. Mr. Sundararaman expects about 40 per cent of Shiva Texyarn’s turnover to come from technical textiles by 2017 based on the current rate of growth.
Defence sector emerges major consumer
As mentioned earlier, technical textiles has emerged as one of the fastest growing market segments. The working group report for the XII has projected a growth rate of 20 per cent for technical textiles. The defence sector has emerged as one of the biggest consumers of technical textiles in India. The specialized clothing requirements of the armed and paramilitary forces include bullet-proof jackets, nuclear, biological & chemical (NBC) suits, high-altitude clothing, high visibility clothing and chemical protective coating, among others.
There has been increasing interaction between the industry and the defence sector in recent times which has given a fillip to the growth of the technical textiles segment. In line with the Centre’s ‘Make in India’ campaign, the India Technical Textile Association (ITTA) organised an exhibition-cum-seminar in New Delhi on February 26 and 27 last jointly with the Ministry of Defence.
Mr. Sundararaman, who is a key member of ITTA, while going into details about the event, said: “It was perhaps the most widely represented armed forces procurement services conference that has ever happened in India in the textiles space”. The event saw enthusiastic participation from the Army, Navy, Air Force, paramilitary forces and ITTA members. Around 150 delegates participated in the event which also included a concurrent exhibition where a total of 50 stalls – 35 from the industry and 15 from the Armed Forces and Defence sector – were put up.
According to him, there are companies in India which have been developing technical textiles for the civilian space, which also have applications in the Defence sector, and there is huge scope for product development if the vendors and the various entities of the Defence sector were to collaborate in the field.
‘Made in India’ Conclave
Mr. Sundararaman also referred to the recently-held one-day conclave on indigenization and supply of special clothing to be ‘Made in India’ for soldiers held in New Delhi on March 10. Organized by the National Textiles Corporation (NTC) and the PHD Chamber of Commerce and Industry, with the active participation of senior officials of the Ministries of Textiles & Defence, Indian Army, and NITRA representatives, the event was chaired by Mr. Sanjay Kumar Panda, Secretary – Textiles.
Reiterating the potential that technical textiles have in India, Mr. Panda called for improvement in quality, adherence to time-lines and import substitution in the area of technical textiles, so that the armed and paramilitary forces in the country could get the best solution at the best price.
In his address, Lt. Gen. Ravi Thodge said budget of almost Rs. 2,000-crore was available for purchase of textile-related products every year and that technical textiles have their due role in improving performance and safety of the army personnel. He also suggested that a single-window solution could be worked out where PSUs like NTC can work together with the armed forces for mutual benefit.
With the emerging opportunities in technical textiles, Mr. Sundararaman expressed his confidence of Shiva Texyarn’s further consolidating its position in the industry. “We have the requisite experience, infrastructure, R&D focus and team. Plus the fact that the Government is keen to promote technical textiles augurs well for the future of the entire textile industry,” he added.