Welspun India has achieved yet another milestone by inaugurating India’s largest spinning unit under one roof at its Anjar manufacturing site. The world class spinning facility housing 1,70,000 spindles was unveiled in the presence of Ms. Anandiben Patel, Gujarat Chief Minister, and other State dignitaries.
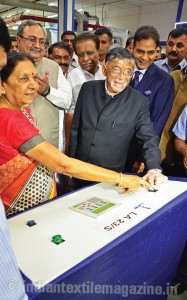
The Rs. 800-crore modern facility is part of Welpun’s overall Rs. 2,500-crore expansion plan for the textiles business in Gujarat. The newly-incubated facility will be instrumental in taking the total spinning capacity of the textile major to over three lakh spindles, thereby fulfilling nearly 70 per cent of its internal yarn requirement.
Welspun, a leading exporter of home textile products, intends to produce finer counts of yarn which has become growingly difficult to procure domestically. This new investment into backward integration is to improve the company’s supply chain with lesser dependency on external sourcing.
At the inaugural ceremony, the Group Chairman, Mr. Balkrishna Goenka, said: “Our home textile business is the second largest in the world. Our pipe business is considered as one of the best among global oil and gas companies. Welspun Energy has the largest installed capacity in solar power with more than 350 mw already installed. This is projected to grow to 2000 mw installed capacity in the next three years. All this makes Welspun one of the fastest growing companies in the country.”
The Welspun Group is indeed one of India’s fastest growing conglomerates with businesses in areas like home textiles, pipes, plates & coils, steel, energy and infrastructure. The $3.5 billion company has a strong foothold in 50 countries with over 25,000 employees worldwide.
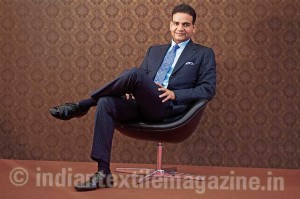
Welspun houses the largest integrated towel manufacturing unit in Asia and is a leading supplier to 14 of the top 30 US-based retailers in the home textile sector. Out of the overall Rs. 20,000-crore topline, the textile division contributes to about Rs. 6,000 crores with more than 95 per cent being generated through exports.
The new spinning unit is expected to meet the in-house demand for fine counts and superfine counts ranging between 60s and 140s. The backward integrated unit will help Welspun keep tabs on the quality parameters, right from the fibre stage till packaging.
At the sheeting division, Welspun has a current installed capacity of two lakh metres a day which will soon be expanded to three lakh metres a day. With hundreds of products in its portfolio, Welpun is considered a ‘Single Stop’ for all their home textile needs by numerous retail giants in the US. The company currently holds a market share of 18 per cent in this segment within the State.
With an ultrawide road surrounded by plantation and state-of-the-art infrastructure, the transformation of the 2,500 acres of earthquake-shattered province into a beautiful township at Anjar is worth special appreciation. It has taken Welspun more than 10 years of relentless effort to reach this level of greatness. “The expansion of our Anjar plant is a major milestone that represents our long-term commitment to the Indian economy and the government’s ‘Make in India’ vision,” stressed Mr. Goenka.
*******************
*******************
MAG testing tools for Anjar plantMAG is happy to be associated with Welspun which is always looking for quality products. MAG has supplied basic testing instruments to Welspun, including the wrap block, wrap reel, count software, twist tester, yarn appearance board, yarn splice strength tester, speed checking tester, etc. Its instruments are being used not only for the existing products but for in-process materials also. |
*******************
——————————
———————————–
Decade-long Luwa-Welspun co-operationMr. P. K. Singh, General Manager, Luwa India and Mr. Gottfried Abrell, Managing Director, LUWA AG Luwa’s strong relationship with Welspun started more than a decade ago when Luwa supplied Humidification plants for its Vapi unit. At the same time, Welspun had laid the foundation for its new greenfield project at Anjar, to become today’s largest home textile company in the world. Luwa is quite proud of being the preferred supplier of the automatic controlled high efficient humidification & waste collection system to Welspun India for its recently inaugurated India’s largest spinning mill having 170,000 spindles under single shed located at Anjar. The Luwa system is working in all the units of Welspun Anjar, which is having approximately 243,000 spindles, 470 sheeting looms and 300 plus terry towel looms. Presently, Luwa is executing its new expansion project with 36,000 spindles ring spinning, 2,000 rotors OE spinning, 200 looms sheeting and 175 looms terry towel weaving, cut & sew process and finish folding. Luwa has supplied the complete range of its products to Welspun, whether it is air-conditioning and humidification system, waste collection system for its spinning mills, high pressure hygienic humidification system, also known as TexFog for nonwoven units, OHTCs for looms, air-conditioning system for the synthetic fiber unit, precision lab units, or loomsphere systems for the terry towel and sheeting weaving mills. Luwa had also provided the air-conditioning system for motor cooling at the steel plant and the ventilation system for thermal power plants with supply of all these equipments being made from its manufacturing facility in Bangalore. The philosophy of Welspun to provide top quality products and services to its customers and attain market leadership in its businesses speaks very well for the proper and detailed planning of investments. Decisions are made thoughtfully considering all the factors including geo-political, technical and commercial aspects on a long-term basis. There are several areas in which Luwa is already working very closely with the project team of Welspun by being an important partner of the Welvision 2020 Action Plan. Plant efficiency audits, energy audits and technical seminars at regular intervals are the areas where Luwa works diligently with the Welspun team. Luwa also plans to have various interactive and training sessions with Welspun technical and maintenance engineers at its different sites so as to impart proper knowhow and develop skills to extract maximum operational efficiency from the existing installed Luwa plants. |
——————————-
Welspun’s largest compact spinning mill under one roofWelspun has become a “household word” for anybody active in the spinning industry, not just in India but wherever I travel. When they decided to put up a project to spin compact yarns after some comparisons, they opted for SUESSEN EliTe Compact for this project of 1,70,000 spindles. The Welspun top management proved its long-term vision by installing excellent machinery, roving transportation systems, roving frames with automatic doffers, linked spinning – and of course all compact! Today, some may think this is an “overkill”, but Welspun plans long range and in five years all projects will likely be patterned along this model mill. In all their dealings with us, all Welspun people I came in contact with were demanding, but fair! Whatever we were told they would do was done, and was done in a timely manner. I must say it has been a pleasure for me. ![]() One has to visit the site while the machines are being installed to appreciate the jobs of the people on the floor, and to appreciate the jobs of the Welpun guys in charge of making it happen. Out of apparent chaos, these dedicated men and women created, I must repeat, the largest compact spinning mill under one roof. Naturally, I was in almost daily contact with the SUESSEN people on the shop floor while this project was created, and created is the proper word! This way, I learned firsthand how well the people from different suppliers co-operated, how the guys in charge from Welspun facilitated their jobs. Of course, sometimes tension runs high when people are under pressure to accomplish the almost impossible, but always the Welspun leaders in charge managed to get them focused back on their jobs on hand. This attitude depends on the top management’s vision: As long as the associates believe in the vision, they will dedicate all their power to make it happen, and they made it happen! I learned that the Chairman, Mr. Goenka, frequently visited the site while the work was going on, encouraging the people on the floor, giving valuable advice and simply showing his dedication to the project. I must admit I have been impressed by this project: its bold planning, its meticulous execution and, of course, its final successful start, culminating in the inauguration on December 6. (Incidentally, December 6 is a somewhat special day in German mythology: On this day, Santa Claus brings little gifts to the children who have behaved well during the year. Certainly I received the best gift possible: A successful startup of this plant!) I want to wish Welspun, its Chairman and all its associates all the success they deserve! I am convinced that this project will be followed by more in due course. Welspun will not stand still but continue to grow and to lead “my” Indian textile industry to new heights! – Peter Stahlecker |
———————————-
Tata BlueScope Steel’s PEB solution for Anjar![]() The pre-engineered steel building (PEB) solution for this prestigious project has been provided by the Building Solutions Business of Tata BlueScope Steel. The scope of work included design, manufacture, supply and erection of the 46,500 sq. metre PEB structure. Tata BlueScope Steel worked closely with Welspun and its consultant Gherzi Consulting Engineers Pvt. Ltd., to develop a PEB solution meeting the functional and aesthetic requirements of the project. Codes, loads, workflows, and services were the focus of discussions. The successful completion of this project, the third by Tata BlueScope Steel for Welspun, bears testament to the quality of products and solutions provided. Contemporary design practices and software were applied for building design. Modern project management techniques were leveraged for timely project completion. Emphasis on safety awareness, training of site personnel and adoption of best practices ensured there were no safety incidents at site. Tata BlueScope Steel is proud to be the preferred PEB Solution provider for Welspun. Tata BlueScope Steel can be contacted at buildingsolutions@tatabluescopesteel.com |