Karl Mayer presents its new corporate design, a stylish, ultramodern stand and impressive, groundbreaking technical innovations at the ITMA.
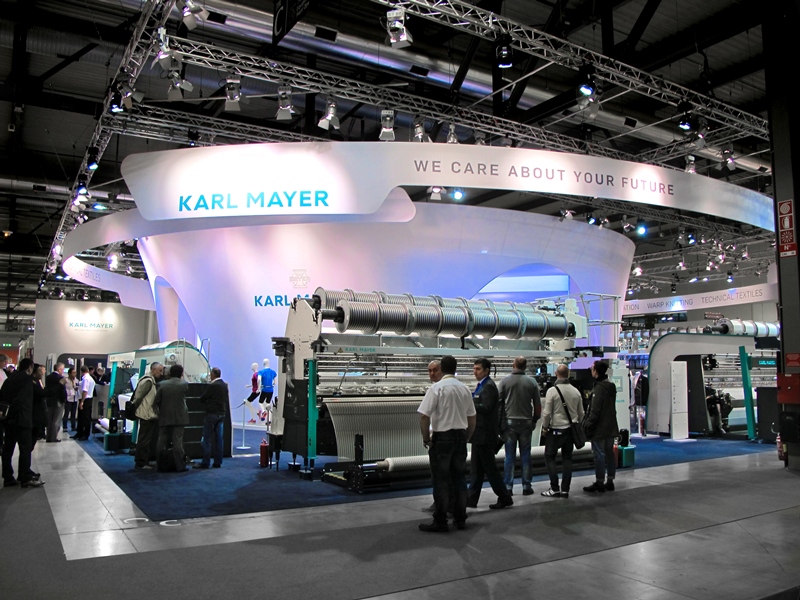
Karl Mayer’s stand has a lighthouse effect, trend-setting, eye-catching even from some distance and is outstanding. At ITMA, the innovative market leader in the fields of warp knitting and warp preparation, machines is present in Hall 5, Stand C 101, expecting its guests with a futuristic stand, the first port of call for the trade. Important cornerstones with great appeal is a multimedia presentation, the release of a completely revamped corporate design and, of course, a choice of technical innovations which definitely attracts experts’ attention.
Innovations in the HKS sector
In the tricot machine sector Karl Mayer is showing a stylish, energy-efficient and ergonomic HKS 2-SE and a HKS 4-M of the next generation which will be processing patterned sectional beams produced on the new DS Opto-EC.
The HKS 2-SE with a width of 130″ and a gauge of E 36 produces an elastic locknit (charmeuse) for sportswear. This newcomer is the flagship that typifies all of Karl Mayer’s innovations in the tricot machine sector, including, a new, ergonomic machine design with a high-tech appearance, with an unique look.
The Low Energy Option LEO based on an improved interplay of drive technology, oil viscosity, heat-resistant machine components and operating temperature, reduces the energy consumption by up to 10% compared to similar, conventional models, which reduces costs and improves the sustainability of materials, thus, being a contribution to environmental protection.
An integrated camera system for complete fabric inspection provided as standard equipment, ensuring total coverage, i.e. 100% monitoring of the finished fabric, the monitoring zone now starts much closer to the knitting point. Defects can therefore be spotted much earlier and the machine can be stopped sooner.
An LED lighting system as standard in two colours, i.e. bright white for a clear view of the yarn sheet, the knitting elements and the fabric, as well as red, which is visible from some distance away, for signalling a machine stoppage in the event of a fault.
The HKS 4-M EL complements the four-bar high-speed tricot machine with N pattern drive which had already been presented to a wide audience at ShanghaiTex 2015. The speed of the EL version, same as that of the model with N drive, has been increased, so that it is up to 25% faster than its predecessor, at the same time it also offers the usual high level of flexibility. The EL configuration enables the patterns to be changed very quickly and easily by inputting data at the machine’s display unit. In this way, the machine can process even small batches efficiently, and can reduce the amount of time needed to develop new and innovative fabrics. Moreover, the EL feature opens up completely new design possibilities due to shog paths of 2″ and almost unlimited repeat lengths. But this new machine does not occupy any pile position, since it is one of the seldom-selected types. The version with the pile mechanism, the HKS 4-M P, will continue to be included in the range.
In the show, the HKS 4-M EL is producing a fabric for outerwear at a width of 180″ and a gauge of E 28. It processes sectional warp beams (SWBs) with a sequence of colours in the warp to match the pattern. The SWBs were produced on a newly developed warp preparation machine, the DS Opto-EC.
The DS Opto-EC as such is not presented at ITMA, only its products. This innovative direct warper for processing non-stretch yarns combines sectional and direct warping, thus, offering highest flexibility. Yarn warp for yarn warp, the winding guarantees a high level of efficiency when warping short warps for developing new products. At the same time, short runs, processing trials on expensive yarns and patterned SWBs can be worked economically. Other advantages include cone warping with limited space requirements, since a minimum number of packages is needed. On the other hand, the DS Opto-EC can be used for the rapid warping of SWBs in the piece which is especially useful with long running lengths. The DS Opto-EC also offers optimum quality and a resulting high level of efficiency during the subsequent processing stages.
Innovations from the lace machinery field
Karl Mayer’s new lace machines are the TL 79/1/36 Fashion and the MLF 46/24.
The new TL 79/1/36 Fashion machine can produce innovative Textronic lace looks never seen before in the lace sector. These eye-catching products include lightweight fabrics based on jacquard constructions, featuring relief-like patterns with a distinct three-dimensional look, the result of a new way of incorporating the heavy liners. This makes the thick cord yarns look as if they have been sewn on, without any top cording. Moreover, the TL 79/1/36 Fashion can also be used as a fall plate raschel machine. All the standard Textronic patterns can be worked using the 76 pattern bars that are available, without using the heavy cord option. The design of the TL 79/1/36 Fashion makes it ideal for producing exclusive, high-end lace bands and panels for dresses, blouses and jackets.
At the show the TL 79/1/36 Fashion is producing a cross band flounce at a working width of 134″ and a gauge of E 18 by using a three colour chine mélange yarn.
With its new MLF 46/24 in a width of 242″, the manufacturer shows an exceptionally wide Multibar lace machine with fall plate and without jacquard bars, offering an impressive level of productivity for a low investment outlay. The concept of this new machine is based on considerably increasing its speed compared to its predecessor at a gauge of E 18. The last fall plate raschel machine was the MRGSF 31/16, having a working width of 210″ and a summation drive system.
The MLF 46/24, 242″ can produce several lace panels side-by-side, as well as wide, all-over-patterned textile webs and also bordered fabrics with long repeats. At the show, the MLF 46/24, with a working width of 242″ and a gauge of E 18, simultaneously works four bordered webs with 145 cm widths of the finished fabric and 150 cm long patterns. The non-stretch panels are intended to be used in outerwear.
Innovations for warp preparation
In the warp preparation section Karl Mayer is showing the stylish, flexible “best of” sectional warper PRO WARP and the new MM 128/3.600 in a wider width. Besides, the company is presenting high-tech solutions such as the Double Vario technology for the denim sector and the VSB Size Box, the heart of the PRO SIZE sizing machine.
With its PRO WARP Karl Mayer is offering a study in concept and design in the shape of its new, stylish, flexible sectional warper. This new machine, which features the company’s new corporate design, combines the performance features of the Opt-O-Matic and the ERGOTEC. It is designed to successively replace these successful models when it goes into production. Equipped with the “best of” technology, the PRO WARP is intended to offer maximum design flexibility throughout the production process. For example, the rotating direction of the warping drum on this innovative machine can be adjusted to suit the warping requirements of the client, and the job can be adjusted to suit the type of yarn being processed. In general, the new PRO WARP can cater to a broad range of applications, during beaming, yarns can be processed for producing shirtings, whilst technical yarns can also be processed. The maximum beaming speed is 500 m/min. This high-performance sectional warper is available with a full beam diameter of 800 to 1,250 mm and with a working width of 2,200 to 5,600 mm. The tensile force values may vary from 20 to 1,800 N during warping.
The new MM 128/3.600 is based on the successful machine concept of the MM 128. Like its predecessor, it can process 128 yarns but, with a working width of 3,600 mm, is 1,350 mm wider. This larger format extends the applications of the Multi-Matic, so that it can now produce sample and production warps of average running lengths for use in the production of high-end upholstery and soft furnishings.
The principles of producing fabrics for the high-end market are based on a successful machine concept and owe much to the exceptional performance profile of the Multi-Matic series. The special performance features include the possibility of producing a wide range of designs as a result of the extended pattern options, the processing of a wide range of colours and yarns, a high level of productivity and the production of warp beams of the highest quality.
High-quality, flexible and sustainable sizing, all these advantages are offered by the VSB Size Box, the heart of the PRO SIZE sizing machine.
This innovative piece of sizing equipment operates with no immersion whatsoever. It consists of three highly turbulent, uniform application zones with patented application and squeeze rollers and a spray bar system. The result is a considerable number of advantages, compared to the immersion bath technique, up to 10% fewer sizing additives are needed, energy consumption is reduced during desizing and less effluent is produced. Applying the size from a spray nozzle under pressure also results in an extremely uniform application. This is due to uniform concentrations, temperatures and viscosities as a result of the high size circulation rate. Efficient size filtration produces a more uniform size film and generates less dust, which increases weaving efficiency. The uniform liquor application also enables the double size box to be converted to a single size box, a switch that makes further processing even more economical. The VSB also offers advantages in terms of its ergonomics and clear layout. The special design enables the warp sheet to be operated vertically during delivery, which provides enough space for easy access to the machine. The operator also has an unrestricted view of the entire processing sequence. Last but not least, the VSB is extremely flexible. The working range of the size bath, which depends on the number of yarn ends and the yarn count, may be as much as 20% higher than conventional systems.
Karl Mayer can offer the ProDye flexible dyeing machine for warp preparation in the jeans sector. The heart of this innovative equipment for denim production is a dyebath featuring the Double Vario technology. The machine feeds the warp yarns into two chambers having a yarn capacity of 11.2 m through the dyebath, and this ensures that the liquor penetrates the yarn optimally. The liquor circulates at a rate of up to 10 times an hour. The result is high, uniform dyeing, deep indigo shades and a marked reduction in the overall number of products being classed as seconds. Another advantage is that nitrogen technology can also be incorporated into the process, which enables the total dyebath volume to be reduced by as much as 20%. A roller-raising system simplifies handling when dealing with broken yarn ends and also facilitates cleaning.
Innovations in technical textiles
The next generation of the HKS MSUS – the new Wefttronic HKS
Karl Mayer has improved and revamped the tried-and-tested concept of its Wefttronic RS series and transferred it to the HKS MSUS. The result is the Wefttronic HKS. The weft-insertion system and the fabric take-up were at the heart of the steps taken to optimize this machine platform. On one hand, the design (arrangement) of these two components guarantees accurate, high-quality processing of the weft yarns. On the other hand, the machine is easy to assemble, which enables it to be integrated quickly into the production process. This reduces the assembly time. Other features of the Wefttronic HKS are its new, modern look, which is in keeping with Karl Mayer’s new corporate machine design, the integration of the KAMCOS 2 system and the implementation of the company’s own CFRP concept. This all adds up to the new weft-insertion machine having an excellent price-performance ratio and being highly efficient with speeds of up to 1,500 min-1.
This new machine is also equipped with the unique gauge of E 40, which gives much more room for manoeuvre when designing products, as the machine on show is demonstrating. A Wefttronic HKS, with a width of 213″, produces a fine interlining fabric in Milan. This is lighter than any interlining ever produced before and has a comparable weight to a woven fabric. When used in clothing, this new interlining provides an excellent fit without creasing, dimensional stability and optimum comfort.
KAMCOS 2 – a platform for mastering the technology
To offer its customers maximum benefits, Karl Mayer makes sure that it is always on the ball when it comes to automation technology as well. Just in time for ITMA 2015 this textile machinery manufacturer presents the KAMCOS 2 system. It is the successor to the Karl Mayer Command System which was introduced in 2003 and is designed to organize and structure the control concepts of all the machines produced by the Karl Mayer Group.
Right from the word go, this new automation platform, which is based on the latest industry standards, offers a man-machine interface with the same sort of operating functions that are used in smartphones and tablets all over the world nowadays. This makes learning as easy as child’s play. The operating display is based on using the machine in practice and shows the user all the application parameters relating to the desired functions in a clearly laid-out way. The design is fun and the user can learn to use and master it intuitively. User errors are virtually ruled out by the integrated monitoring functions and by controlled access via data chip. It is simply a matter of placing an access key in front of the relevant counterpart next to the display and the machine’s data are revealed to the user, tailor-made for specific functions. KAMCOS 2 also offers advantages in terms of its well-thought-out solutions for system integration. For example, the Laserstop system of yarn monitoring has been completely integrated into the new platform. Yarn breakages are detected instantly in the sensor and evaluated by the machine control system. A newly developed camera monitoring system for inspecting the textile web has been integrated into the new KAMCOS 2 system and makes all the relevant information available to the user. The machine’s new lighting system with status indicator function is also controlled via KAMCOS 2. For example, by switching to red when there is a problem, a signal is sent to the user, even some distance away in the production hall, which provides information on the operating status of the machine. As a control centre, KAMCOS 2 also provides an optimum basis for all the functions, so that they can be accessed via the new Karl Mayer Connect smartphone app. This enables data to be accessed via mobile devices and represents an entry into the world of mobile communication. The data are still protected and only available to authorized users.
All-round support – a complete technical service with the customer at the centre

Karl Mayer has strategically restructured its tried-and-tested, all-round technical customer support service and has introduced some specific, complementary new features, which are premiered at ITMA. A particular advantage is the use of online communication. In addition to providing direct, personal customer consultancy and advice, two innovative online services are now available for mobile devices, the Karl Mayer Check Parts app, and the Karl Mayer Connect app, for rapid communication between user and company. Moreover, the company is presenting an online WEBSHOP for spare parts accessible via the Internet. More specifically, 360° support means comprehensive technical support in relation to sales and services, an efficient spare parts supply, first-class textile advice and specific customer training. The modules all interlink with each other and are run by experienced, trained specialists.
Increasing efficiency by providing a service via smartphones and tablets
The Karl Mayer Connect app has been developed to provide faultless, efficient communication between the customer and the service organisation. The app is unveiled at ITMA for the first time. It is the heart of a software platform that covers the first two levels of a service matrix, whose features have been extended in three stages.
With Level 1, the personnel on site can scan a QR code on the operator console of the machine via a mobile phone and, if required, can send off a service request to the Karl Mayer service specialists. Important information for explaining the problem can be transmitted with the QR code.
With Level 2 of the service matrix, the machines and mobile devices can be linked into the customer’s network via the WLAN at the same time. This link also enables the service request to be sent via the Karl Mayer Connect app but with a more extensive package of machine data. There is also an option to insert photos and comments into the service request here. The customer can also look at the machine data within the company network, even outside the machine’s working area. The operating data are also available for checking whilst on the move and these include the notification history, the speed record, and any machine documentation. Anyone who wants to ask Karl Mayer something quickly can open the link to the manufacturer’s homepage via the Connect app. These app-based solutions enable the customer to communicate easily with the experts at the company via smartphones and tablets, and this also applies to those clients involved with mass production.
The features of the app complement Level 3 of the service communication system, the existing Teleservice system. The ability to view things remotely is based on bidirectional exchange, i.e. the customer sends a service request, which links the in-house technical support personnel at Karl Mayer up to the machine control system. In this case, the data are transferred by a secure Internet connection.
Dual protection against copying when procuring spare parts provided by Karl Mayer’s new label of authenticity including the QR code
Karl Mayer has developed a special label of authenticity for certifying the quality of its spare parts, thus, providing protection against copies and this is a two-tier strategy. Security level one is a non-removable sticker, which is used to seal the box. As long as it is intact, this label of authenticity guarantees that the spare parts are original. A hologram on the label, which has been specially designed by Karl Mayer, shows immediately that a delivery is authentic.
Level two of the anti-copying system is based on a QR code. This digital element is also a feature of the seal of authenticity and permits the authenticity of the label to be checked as well. The karl Mayer Check Parts app has to be just loaded from the app store into a smartphone. The QR code is scanned and all the information on the original quality status and on the product is displayed.
If there is any doubt, the customer can contact the manufacturer. The report can be sent to them via a simple menu navigation system on the app display. Once the appropriate function has been selected, the photo mode is activated automatically and a picture of the seal or spare part can be sent to Karl Mayer as an attachment in an e-mail.
Order virtually, profit in reality – with the new SPARE PARTS WEBSHOP
KARL MAYER’s new SPARE PARTS WEBSHOP makes ordering spare parts quicker, easier and more transparent. Just by clicking on the mouse, customers can directly order current wearing parts or they can inquire the relevant technical components not covered by this category via an online glance into the machine documentation. Moreover, before placing his order the customer can also describe the required articles by means of text and pictures to be uploaded, all these offers are easy to handle. The purchase via WEBSHOP is possible both on PC and by mobile devices such as smartphone and tablet. Inviting elements of the new system are easy operation, intuitive menu navigation and easily understandable, richly illustrated design with well-thought-out search and filter functions.
Another feature in terms of user orientation is the display of individual data, after the customer had made his personal registration (log in). When repeat orders have to be made on a regular basis, an efficient document management system makes the ordering even easier, the most recent orders are uploaded and the relevant ones can be sent off again. Payment by credit card ensures a quick and secure payment and thus, the direct delivery of the spare parts on stock.
At ITMA visitors have the first opportunity to try it out. At the launch of KARL MAYER’s new SPARE PARTS WEBSHOP roughly 1,500 directly orderable parts and components for selected machines and markets were available via the B2B platform. The worldwide introduction is scheduled to take place by end of 2017.