The contribution of the textile industry and its extensive use of water resources require more environmentally friendly means of production to ensure sustainability. Companies such as DuPont provide water solutions, enhancing the productivity and minimising the environmental impact of textile plants. In fact, with is new and advanced technology, DuPont is taking sustainable water solutions to an all new level
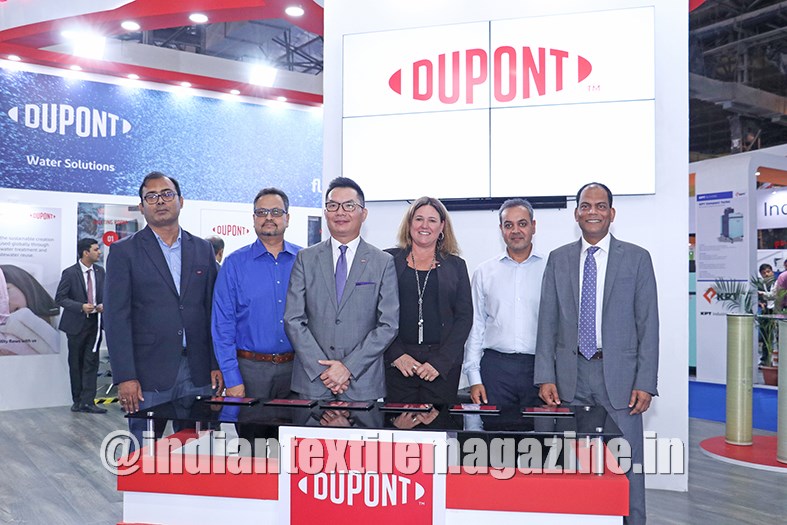
As one of the largest industrial sectors in India, the textile industry has certainly recognised the importance of sustainability. Businesses have been encouraged to use sustainable ideas of reduce, reuse and recycle in the face of growing depletion of natural resources. In the textile industry, there is a high demand for pure water required for the manufacturing and dyeing of natural, synthetic and nonwoven fabrics on a daily basis. This need for huge volumes of water for production also calls for greater use of energy sources and may create environmental issues such as toxicity in contaminated water. Therefore, many companies are now moving towards providing water solutions to the textile industry in order to allow more sustainable and environment-friendly methods to manufacture their products.
In this respect, DuPont has always been an active part of the water industry in India, providing water solutions to various market segments, including the textile industry. The company provides highly efficient and effective technologies, including reverse osmosis (RO), ultra-filtration (UF) and nano-filtration (NF). In fact, creating and implementing water solutions has been a longstanding legacy for DuPont that has played a major role in the water treatment industry with a history spanning more than 40 years. Formerly known as Dow Water and Process Solutions, the company’s business underwent a major transition after it merged with DuPont in September 2017.
The Board of Directors of these two companies re-shuffled the portfolios and the new identity of DuPont emerged as a specialty products’ company focusing on differentiated products and technologies. In the re-shuffling process, the water solutions business, a technology-led innovation-oriented portfolio, moved from Dow Water and Process Solutions and became a part of the new DuPont. Now, when it comes to water solutions, the strategic focus is ‘growth’ with a goal to resolve customers’ challenges better, faster and more cost-effectively. This includes extending advanced sustainable wastewater treatment solutions to the Indian subcontinent. For the textile industry, in particular, with reduced access to reliable, low-cost water sources as well as the higher costs associated with water discharge, investing in wastewater reuse systems to recover and recycle 70% or more of the water in textile plants has become common practice.
The wastewater from textile companies goes through various levels of treatment until it is processed in an evaporator. This leads to excessive use of energy as well. Due to the challenges of treating this water composition, thermal evaporation and condensation was considered the only option. However, even with the most advanced energy-efficient evaporators, the operation is very expensive and cost-prohibitive. Additionally, the upfront capital cost to install these systems is significant. With advanced wastewater treatment and reduction of the amount of water entering the evaporators, companies can eventually have zero liquid discharge (ZLD) in a manner that not only conserves energy but is also extremely cost-effective.
Taking the lead
This is where companies such as DuPont can assist by providing efficient solutions for recovering the water that goes into evaporators and further allow its reuse, leading to lower energy usage and lower cost of production. Through such ZLD wastewater treatment solutions, the Indian textile industry is moving towards a more sustainable water future by reclaiming and reusing waste streams. As Chrys Fernandes, Regional Marketing Manager, DuPont, states: “There have been scenarios where power plants in the country have shut down due to severe shortage of water. It leads to lack of energy, which in turn slows down the smooth functioning of industries. This realisation plays a major role in directing textile companies towards ensuring sustainable water operations. Self-driven initiatives are being taken by industries now and over the next few years we will see a lot of fresh approaches towards finding the right solutions.”
The right technology
DuPont’s smallest project includes a single membrane with just one cubic metre of water, while their largest project can go beyond 160 MLD (minimal liquid discharge). One of the major companies that DuPont has provided a solution for includes Reliance Industries, with 168 MLD consuming up to 20,000 elements. Reliance Industries – Textile Division uses large amounts of water while producing polyester yarn. DuPont has thus provided it with water solutions through desalination processes in which sea water is converted into pure water that can be used to manufacture textile-related products. In fact, DuPont’s Water Solutions can claim to have the industry’s longest history with its pioneering innovations in reverse osmosis technology. In 1985, Water Solutions acquired FilmTec Corporation, which held the patent for game-changing, thin-film FilmTec™ RO membranes.
Since then, Water Solutions has advanced the FilmTec™ thin film RO membrane design technology for making spiral wound RO elements, and the automation of both membrane manufacturing and element fabrication. The FilmTec™ Fortilife™ family of products and spiral wound ultra-high pressure reverse osmosis (UHP RO) membranes are next-generation RO membranes designed to tackle the most challenging wastewaters. These elements incorporate the advanced membrane technology developed over years of innovation in membrane chemistry, module design, and in-field application development. The availability of multiple element types provides the flexibility for system designers to achieve the most efficient and reliable, high-recovery system.
Case studies and prospects
Over the last 3-4 years, DuPont’s increasing interaction with companies in the textile industry value chain has suggested a growing awareness about the depleting water resources and increasing demands. This has played a significant role in the creation of the FilmTec™ Fortilife™ product family. This portfolio, consisting of RO and NF, is designed for application in large-scale plant facilities. A challenge is that many membranes can be too delicate for wastewater with high organic and colour load. FilmTec™ Fortilife™ membranes are more sturdy, offering extra fouling resistance technique to help tackle such problems related to wastewater from textile industries.
“In our work here in India, while talking to our customers in the value chain of textiles, we realised the solutions they required and this led us to create the FilmTec™ Fortilife™ series because we know that effluent water is very challenging to treat and we also know how important it is,” says Nanette Hermsen, Global Leader, DuPont, while commenting on the application of their water solutions in the Indian textile industry. Even if certain companies cannot afford a ZLD policy, DuPont has assisted them to ensure MLD. An alternative for textile industry consumers who use ZLD, in areas such as Tirupur and Gujarat, is to employ a pressure-driven, membrane-based MLD approach in conjunction with ZLD. This approach lowers the overall cost by 60% and environmental impact of thermal evaporation by concentrating and purifying up to 95% of the water before thermal treatment.
On the other hand, for states which do not do ZLD, the company offers solutions to recover maximum amount of water. The FilmTec™ Fortilife™ product portfolio that consists of reliable and durable membranes allows MLD in such cases. For instance, to adhere to local requirements while remaining profitable, a textile mill in the Tamil Nadu region implemented an innovative MLD approach that utilised DuPont Water Solutions’ spiral wound UHP RO membranes. An 80-day trial evaluated the new system’s ability to minimise freshwater withdrawals, decrease wastewater discharge, and treat high concentration brine waters. The high-pressure RO membranes removed colour from water sources, decreased wastewater output, and lowered overall system cost by more than 50%.
As a result, the mill meets strict discharge regulations, reduces freshwater use, remains profitable, and ensures environment safety to mitigate water scarcity challenges and preserve economic security. “We are offering a myriad range of solutions to recover water in innovative ways. Depending on the industry we try to drive our innovations towards them and keep pushing the barrier,” says Somil Mehta, Technical Development Manager, DuPont. And with the Indian market having become significantly important with major growth opportunities, the company has now set up labs in Mumbai, Hyderabad, Delhi and Chennai. The lab in Hyderabad focuses on testing different kinds of water, testing water quality, and also providing an experience centre for customers.
The other labs have a strong team of employees, handling technical and commercial aspects while being engaged in the continuous building of resources. DuPont is still on an expansion spree and the company anticipates that it will soon have a wider appeal in the market for the technologically advanced water solutions it offers to various industries. As for future prospects, DuPont sees organic and inorganic opportunities due to the growing need to advance wastewater treatment solutions. The company also sees good prospects in new geographical locations in India that have been facing a water crisis. In fact, DuPont expects the turnover of its Water Solutions’ business to grow in double digits for several years to come.