Swiss textile machinery manufacturer Rotorcraft AG., the inventor of ‘Green Compact’, which is an innovative compact yarn spinning attachments, offers benefits of lower electricity consumption as well as lower maintenance costs, when compared with conventional compact yarn spinning technologies and is co-made in India.
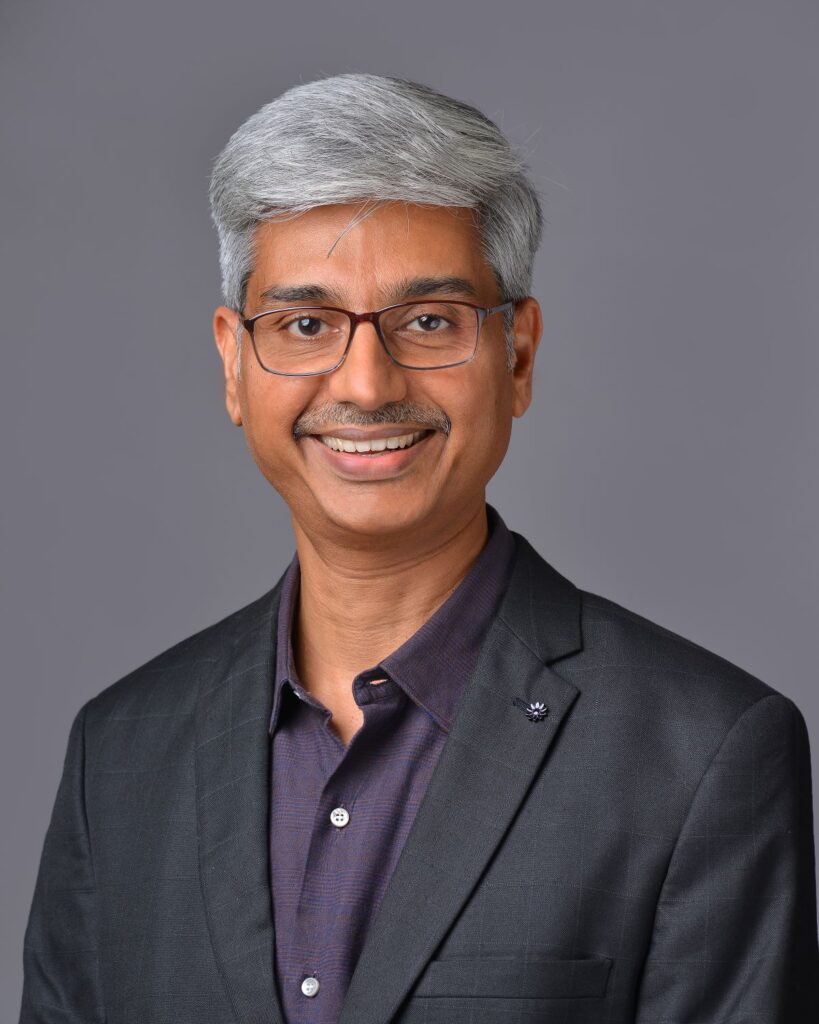
“In a world driven by rapid technological advancements and shifting market demands, the survival and long-term success of spinning manufacturers depend on their ability to optimize existing capabilities while exploring innovative solutions,” Mr Maheswaran. V, Brand Auditor, Green Compact at Rotorcraft told The Textile Magazine.
To optimize existing capabilities, RotorcraftGreen Compact, an advanced compacting system offers a superior alternative to traditional suction compacting, especially for counts below 60s Ne. While suction compacting has been a conventional choice, Green Compact brings new efficiencies, sustainability, and cost savings—a step forward for spinners looking to stay competitive.
Green Compact: Compacting a Wide Range of Fibres, Including Recycled Fibres
“Suction compacting systems often struggle with certain fibre types, limiting the flexibility of manufacturers. Green Compact, on the other hand, efficiently compact’s all types of fibres, including recycled fibres, linen, hemp, viscose and polyester blends. With the rising demand for sustainable textiles, this capability allows manufacturers to explore new markets and meet eco-friendly production goals without compromising yarn quality,” Mr Maheswaran explained.
Lower Maintenance Costs
Suction-based compacting requires continuous air suction, leading to frequent cleaning due to lint and dust accumulation, high maintenance costs and increased downtime due to wear and tear. Green Compact eliminates suction entirely, reducing maintenance costs significantly. By using a streamlined mechanical and magnetic system, it ensures longer service life, fewer breakdowns and uninterrupted production.
Energy Efficiency: No Additional Power Required
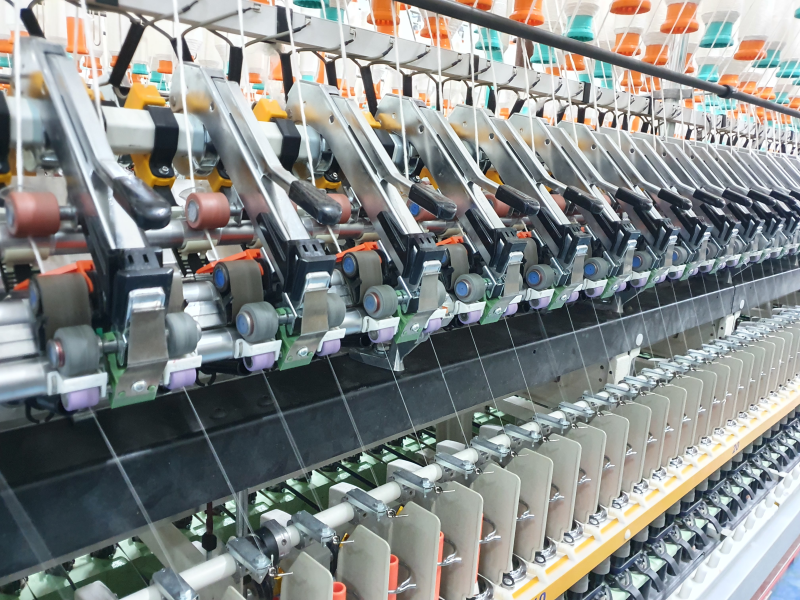
“Suction compacting systems rely on high energy-vacuum suction to create a compact yarn structure. This not only increases electricity costs but also adds to the environmental impact of spinning operations.Green Compact, in contrast, operates without any additional power input. Instead, it uses a smart combination of magnetic and mechanical interactions to achieve the same or better compact yarn structure, without any extra energy burden,” Mr Maheswaran added.
Natural Elimination of the Spinning Triangle for Superior Yarn Quality
In traditional ring spinning, the spinning triangle affects fibre cohesion, leading to weaker yarns and increased hairiness. Suction compacting systems attempt to control this issue using additional power, but Green Compact takes a different approach. It uses a magnetic and mechanical interaction to eliminate the spinning triangle naturally. Delivers a stronger, stable compact yarn without extra power and ensures better consistency in yarn quality and reduced hairiness.
Green Compact: Future for Counts below 60s Ne
For counts below 60s Ne, where fibre control is crucial, Green Compact provides superior performance compared to suction-based systems. In the textile industry, short-term survival depends on maximizing existing capabilities, while long-term success requires the adoption of new, innovative technologies. Green Compact allows manufacturers to do both.
“The Green Compact optimizes existing production lines with a system that reduces maintenance and energy costs, explores new opportunities by processing a wider range of fibres, including recycled materials, linen, hemp, viscose and polyester blends and achieves superior yarn quality while maintaining sustainability and efficiency,” he stated
For manufacturers working with counts below 60s Ne, Green Compact offers an unmatched advantage over suction compacting. Its ability to process various fibres, lower maintenance costs, energy-free operation, and natural spinning triangle elimination makes it a superior long-term investment for textile companies looking to enhance efficiency and sustainability.
As the industry moves towards cost-effective and environmentally friendly production, Rotorcraft AG’s Green Compact leads the way in sustainable manufacturing, offering a smarter, more innovative choice for forward-thinking businesses committed to environmentally friendly production, for the textile industry.
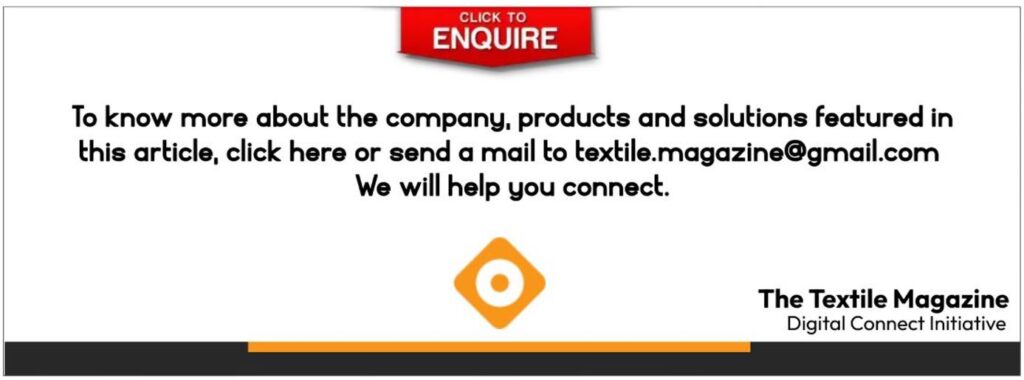