Benninger is the global leader in the development, design, manufacturing and service of technologically advanced, highly engineered textile finishing and tire cord solutions serving the global textile, chemical fibre, tire and conveyor belt producers. It supplies tailored process solutions with innovative and reliable products as well as comprehensive textile process technology knowhow.
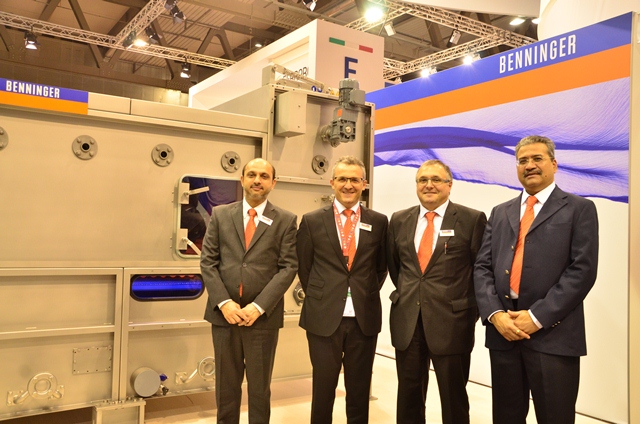
With its many years of experience and sound textile competence, Benninger creates long-term added value for its customers. It is able to make use of the extensive experience gained from a large number of reference installations for individual application processes.
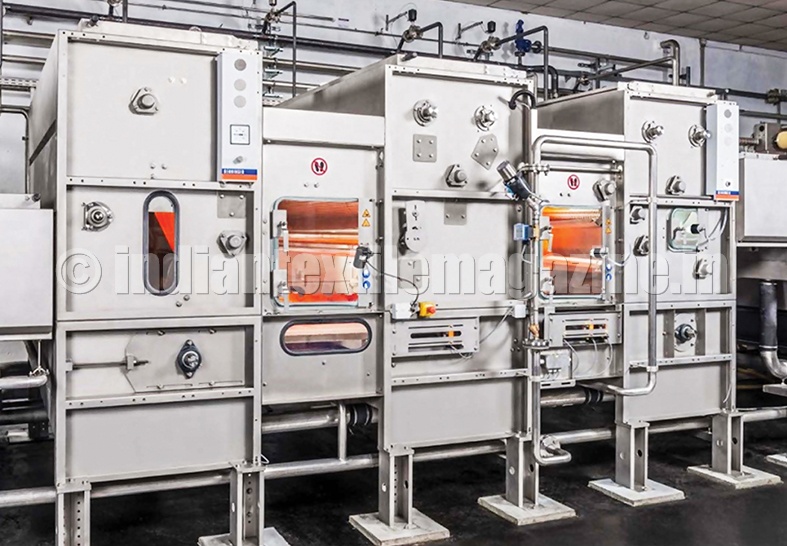
Benninger operates as a full-service solutions provider. It plans and implements technologically optimized and individually designed process and system solutions and is a trustworthy and reliable partner for customers in all respects, starting from process consulting through to the entire life cycle.
For Benninger, assuming responsibility is a matter of course. Fully committed to sustainability, it demonstrates this commitment by investing in the development of high quality products as well as ecologically sound processes. A holistic approach to the relevant factors is just as important to the company as the balance between ecological and economic concerns.
At ITMA Benninger is highlighting the topics of open-width dyeing of knitwear on the original Küsters DyePad, the newly developed Technical Textiles Division as well as the topic of Resource Management, an area becoming increasingly important.
Benninger has consistently extended its product portfolio and developed new products in all these fields, and the most important innovations are presented at ITMA for the first time:
* TEMPACTA washing steamer for knitwear
* Benninger-Küsters DyePad for knitwear and woven fabrics
* TRIKOFLEX drum washing machine that is now also available for large widths and is therefore particularly suitable for technical textile applications
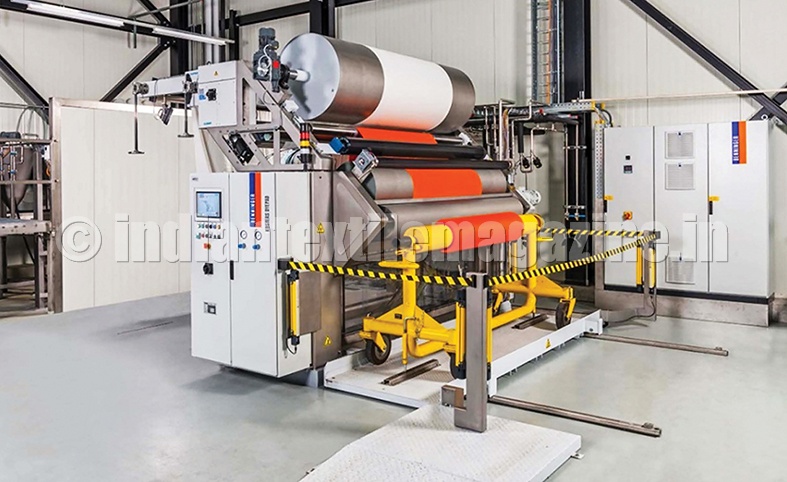
Important Innovations
The TEMPACTA washing steamer was especially developed for all low-tension washing processes and is mainly used for diffusion washing (fastness washing) and for relaxation of knitwear. As a washing drum can be integrated, an intermediate rinsing process or additional intensification of washing is possible.
With the newly-developed original Benninger-Küsters DyePad dyeing padder, great emphasis was placed on optimum accessibility and short, guided fabric runs. The nip dyeing option helps minimise dye liquor consumption and facilitates economical dyeing of extremely short batches. Perfect, absolutely reproducible dyeing results are guaranteed by the use of the original Küsters S-roller technology.
With the front and back washing effect, based on the patented double drum technology, the newly redesigned TRIKOFLEX drum washing compartment guarantees high mechanical washing efficiency. It not only enables low, controlled fabric tension, but also crease-free fabric transport, even with sensitive fabrics. The drum washing compartment also offers another advantage by controlled relaxation of synthetic and elastane fibres.
All these advantages also predestine the TRIKOFLEX drum washing compartment for use with technical textiles. To meet all requirements in this field, the compartment is available with a working width of 5,400 mm. The range for technical textiles is supplemented by the HYDROVAC water removal system and the original Küsters finishing padder. This offers customers new options in the technical textile field, not only with regard to the technological processes but also with minimum use of resources.
The name Benninger is synonymous with environmentally-friendly textile finishing. For this reason, Resource Management is a central topic at ITMA. Individual concepts and solutions for minimising resources are presented at individual, topic-related island displays. The main areas of focus are zero discharge production, exhaust air and waste water heat as well as lye recovery.
In the so-called zero-discharge production, waste water is recycled. With a Benninger system it is possible to lower the waste water quantity to achieve zero discharge, i.e., complete waste water free production can be achieved.
Exhaust air and waste water heat recovery starts with simple reduction of the radiated heat by means of innovative isolation and continues through to high-efficiency systems for exhaust air heat recovery on cylinder dryers. Benninger uses individually optimised heat exchangers in the waste water heat recovery systems that are already in widespread use, depending on the application process and waste water volume.
Lye recovery, which Benninger recently included in its portfolio, offers considerable advantages during mercerisation. The weak lye is concentrated by evaporating the water and is then available for reuse in the mercerisation process. This enables customers to benefit from both inexpensive and environmentally-friendly production.
Another area of focus in the field of finishing is always minimum use of chemicals. Intelligent application systems such as the IMPACTA modules guarantee the precise application of chemicals for the respective process without having to draining off the excess liquor. A particularly resource-saving process in this respect is the CPB reactive dying process. After the take-over of KÜSTERS in 2007, Benninger was able to successfully combine the Küsters and the Benninger technologies, especially in the padder, bleaching and dyeing steamer fields.