Provides important technology solutions for the new flooring plant
A.T.E.’s relationship with Welspun dates back to 1994 when A.T.E. arranged for the supply of blowroom machinery and cards for its spinning project at Vapi through its partners, Trützschler, Germany. The relationship has been growing from strength to strength ever since, with A.T.E. playing a role in Welspun’s subsequent expansions into sheeting, terry towel, bath rugs, and non-wovens in Vapi and Anjar.
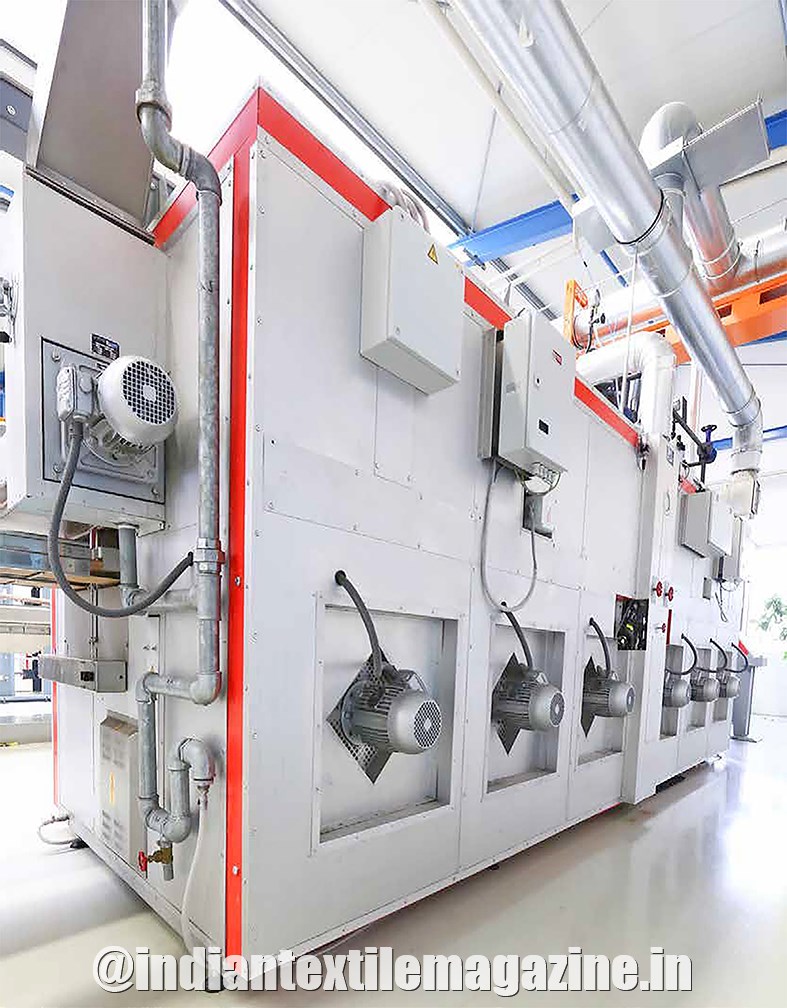
The quintessential aspect of the relationship is the mutual trust developed between A.T.E. and Welspun over the years, with A.T.E.’s role transcending the agent-supplier-customer equation to being a part of Welspun’s team. What’s common between Welspun and A.T.E. is that the former desires only top-notch machinery and services, and the latter is a reliable partner exactly suited to this role.
A.T.E. takes pride in being associated with Welspun once again, this time for their new integrated carpet flooring project in Telangana – Welspun Flooring Limited. A majority of the machinery for this project has been supplied by A.T.E.’s principals. Here is a quick walk-through the machinery supplied by A.T.E.’s principals for this project:
• Carpet yarn heat setting machines from Power-Heat-Set, Germany
• Tufting machines from Card-Monroe Corp., USA
• Digital printing machines from Zimmer, Austria
• Supporting equipment (for digital printing line) from Yamuna Machine Works, India
• Carpet shearing machines from Sellers Textile Engineers, UK
• Contract winders from Matthys Group, Belgium
Heat-setting of carpet yarn is one of the 4 major steps in the carpet manufacturing process. One carpet yarn heat setting machine, GVA type 8.0+, has already been supplied to Welspun while one more machine is on the way. The GVA type 8.0+ heat setting machine allows heat setting on 6 different conveyor belts, giving Welspun the flexibility to heat set small as well as big lots on different belts, even different colours of the same yarn, or straight set and frieze, all at the same time.
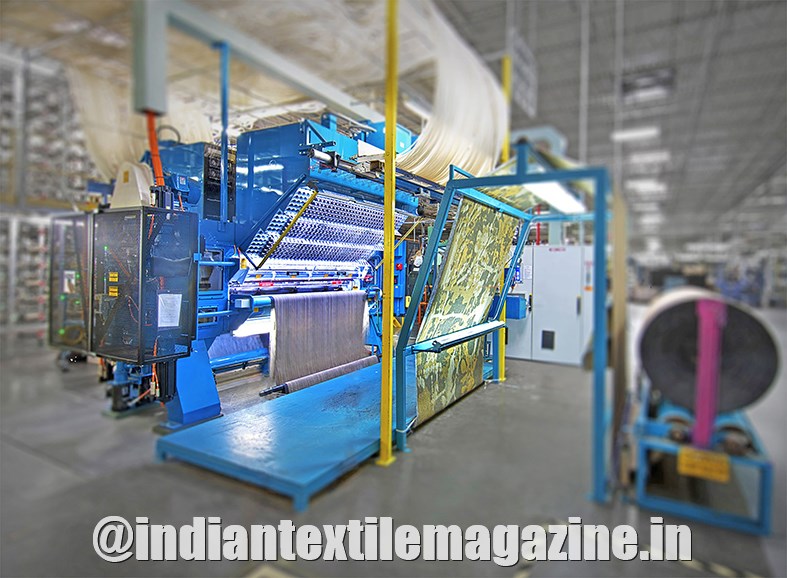
The Power-Heat-Set equipment operates with overheated steam, which offers many advantages, amongst others, a higher stain and soil resistance of the yarn.
Card-Monroe Corp. or CMC, has supplied 2 tufting machines to Welspun. These state-of-the-art tufting machines are designed to produce carpets with multiple colours, multiple pile heights, and a variety of textures. One of the machines supplied to Welspun Flooring has the unique feature of producing high loop over small cut pile, which is uncommon in the carpet industry.

CMC has been associated with Welspun Group since the inception of their rugs plant in Vapi. CMC has supplied several tufting machines with different gauges and styles like plain cut pile, plain loop pile, MLCL, loop over cut, Infinity, etc., to the Welspun Group.
Zimmer’s digital printing machines supplied to Welspun are based on the COLARIS.96-4200 printer model and are designed for the production of high-end contractual carpets and carpet tiles.
A complete COLARIS roll to roll print line with integrated horizontal steamer and post print washer has been added with a dryer from Yamuna Machine Works Ltd.
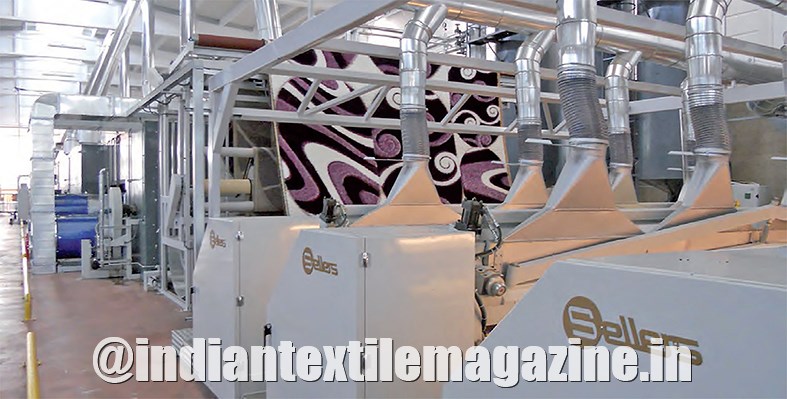
A lead time of just about 8 months from order to the start-up of production was quite challenging for the 91-metre long production line. Nevertheless, the COLARIS installation could be completed in time by mid -March. The commissioning too was completed within the scheduled time. Going above and beyond in the time of the COVID-19 lockdown, A.T.E.’s engineers commissioned the entire Zimmer printing line with remote support from Zimmer’s engineers in Austria. “At one point of time, even Zimmer thought that it would not be possible for the A.T.E. engineers to commission the machine. However, motivated by the encouragement from Welspun, our engineers proved their mettle and commissioned the machine successfully to Welspun’s and Zimmer’s delight”, pointed out Mr. S. Rajendran, Business Head, Processing, who is in charge of service.
The Zimmer Colaris supplied at Welspun Flooring is a unique machine which can print three polymers – polyester, wool, and nylon. 50% of the machine capacity is for polyester and the remainder is for wool and nylon.
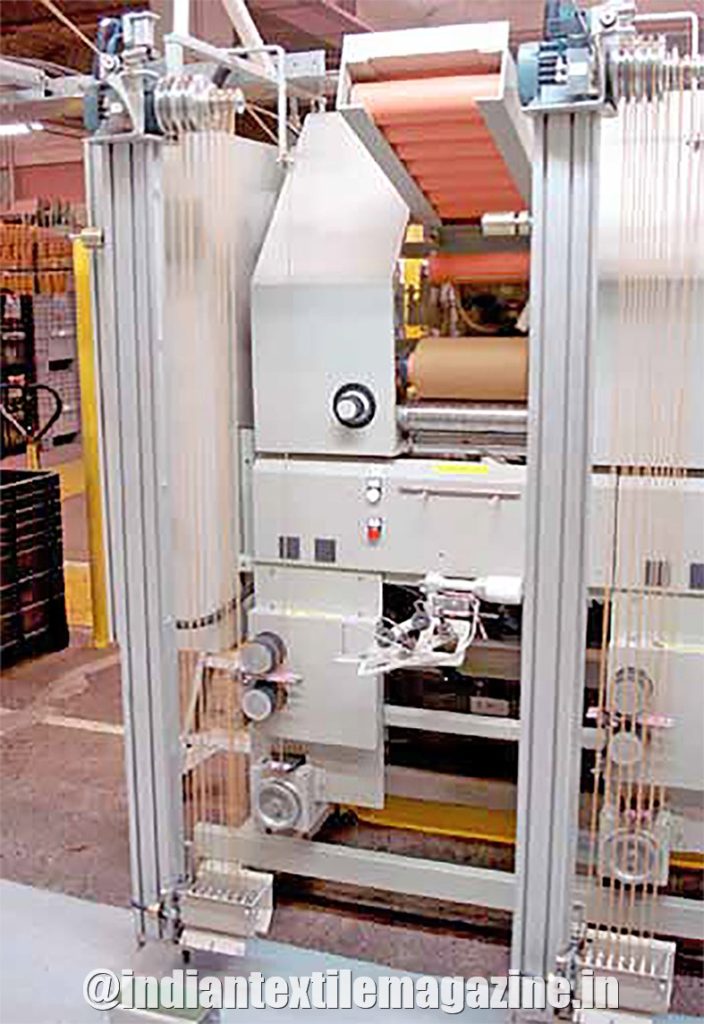
Sellers, UK, has supplied two state-of-the-art carpet shearing lines. The machines are suitable for variety of carpets tufted on tufting machines as well as woven on weaving machines with different fibres. Sellers’ shearing machines are versatile and can be used to shear different types of carpets.
Matthys Group supplied one contract winder for the project. This winder is specially developed for the contract market and is controlled by a PC steering unit. The software creates winding jobs based on information captured from a CAD system. After the winding, when the required yarn length is reached, the bobbin receives a label with the yarn batch number, creel position, length and other user-defined data. This system helps minimize yarn waste and gather production control data.
While there were some challenges in the execution of the project given the tough timeline, the team at A.T.E. and the principals who are a part of this project are extremely happy with the successful execution of this project. The words of Mr. G. V.Aras, Director, A.T.E. Enterprises, succinctly capture the pride A.T.E. associate’s in its relationship with the Welspun Group: “A.T.E. has always enjoyed a relationship with Welspun as a major technology partner irrespective of the textile business line they invest in. Mutual trust is the essence of this successful partnership. We feel fortunate to be a major technology solution provider to the ‘flooring solution’ project of Welspun through our world-renowned principals. We hope to continue with the excellent relationship with Welspun Group in the years to come.”