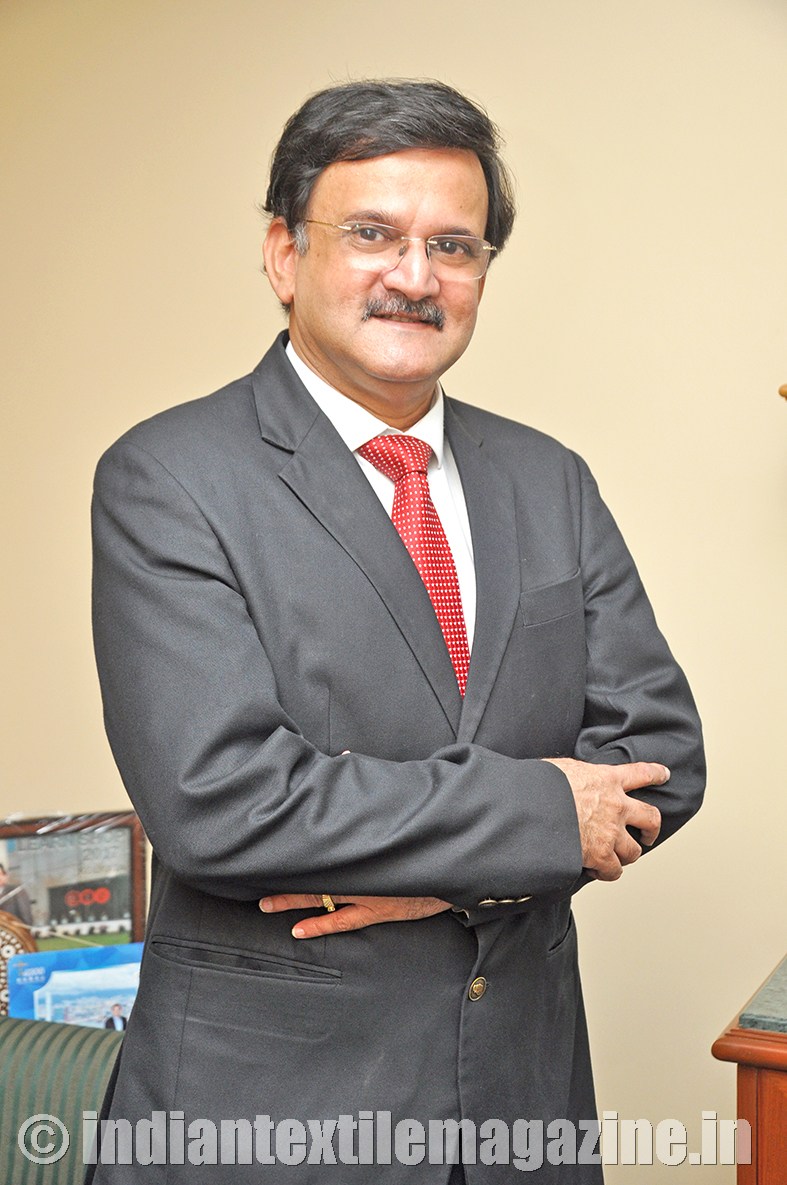
Back in 1939, A.T.E. was known as Associated Textile Engineers and the promoter of the company, Mr. Shyamlal Bhagwati’s sole intention to begin the company was to hurt the business interest of the British Empire. Patriotism wasn’t just about fighting a war on the battlefield, and hence Mr. Bhagwati got in German agencies, selling German machinery in India. This was the first step of initiating the long-standing relationship between A.T.E. and German companies began. And, it has been nearly over 70 years since the first solid relationship was established.
In conversation with Mr. G.V. Aras, Director of A.T.E., who gave some valuable insights on the long-standing relationship between the company and its German principals. He says, “Our DNA is probably German because we work with most of the German companies and we have been working with them for nearly seventy years.”
In recent times, A.T.E. also has liaisons with quite a few Italian, Chinese and Japanese companies, even outside of the textile industry. Mr. Aras, however, admits that their style and ethics of working are more favorable to the Germans. And today, they work with nearly 15 German principals.
Though the association with German machinery makers began almost solely as an act to hurt the British interest in the pre-Independence era, what is that makes A.T.E. continue its prolonged association with the Germans?
Mr. Aras says: “The best part about the Germans is their engineering expertise and an eye for perfection. Being in this industry for the last 37 years, whatever I have seen with the German machines is nothing but supreme engineering.”
He also credits the manufacturing precision and accuracy with which these machines have been manufactured. For example, he adds that machinery produced by Trützschler have been known to perform at its best capacity for even more than two decades in most cases and that too with consistent quality performance for years. They also have high resale value over their usage lifecycle.
He says: “The second important reason is, like how we Indians value relationships, so do the Germans. If you look at it, there is a reason why we had seven decades of solid relationships with them, and it is mainly due to the trust factor and respect for each other. There’s a lot to learn from the German companies that are usually straightforward, very professional and their emphasis on better planning to the last micro level is a great characteristic for us to imbibe. Our Indian counterparts in the JVs also had a lot to learn and absorb from the German partners with respect to the manufacturing processes and technology. One of our first JVs with Trützschler, known at that time as Trumac Engineering Ltd. and now known as Trützschler India Pvt. Ltd., became successful as a market leader in blow room and cards due to strong support and timely technology transfer from the partner company”.
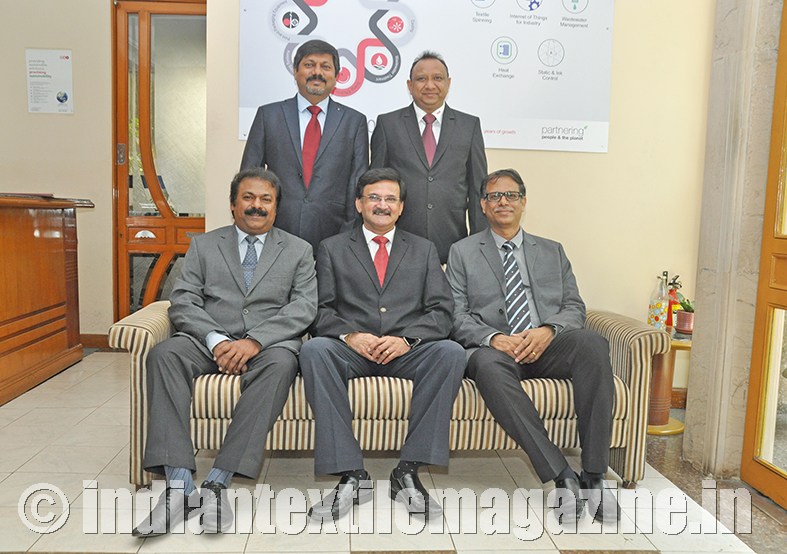
But the superiority of the German technology comes at a price. And, how does A.T.E. keep up with that? Considering that a few decades ago, offering German technology would have come at a premium price, what made A.T.E. sustain that prolonged relationship with the Germans?
Mr. Aras explains that it took more than five years to sell the first Trützschler card in India. Back in the 1980s, there was hundred per cent import duty and foreign machines definitely costed a bomb. But A.T.E. managed to sell their 1st carding machine DK 740 to Bombay Dyeing for the simple reason that, Trützschler machines were one of few that could keep up with the rigorous demands of production and quality, and that’s how these machines started having an upper hand. As a result we have more than 12,000 cards in India supplied from Truetzschler Germany and Truetzschler India so far.
He adds: “The second important aspect is the longevity of these machines over and above the lower running cost. Despite the initial high investments, the returns over a period of time are very high”.
Similar is the experience with machines supplied by Monforts and Karl Mayer. Customers feel happy to own these machines even after a couple of decades as they continue to give a high level of performance and quality for years, helping the customers in keeping ahead of competition in terms of product quality and consistency.
A.T.E. has a long-standing relationship with German companies like the Truetzschler Group, Monforts, Karl Mayer Group and Osthoff-Senge who are some of the best and also the market leaders in the global spectrum. Apart from these, A.T.E. has added some specialist equipment makers like Mahlo, Texpa, Xetma and Schwing in their German folio during the last decade.
Having said that, the recent addition of Chinese companies to the portfolio add a bit of a gamble considering the pricing aspect. How does the company maintain the balance and give equal importance to both?
Mr. Aras observes: “We sell Chinese machines mainly if the company is backed up by a European parent or a big leading group. The idea is that these machines are designed in many cases in Germany, and most of their critical components also come from Germany. It is only assembled as a final product in China with strict adherence to the German manufacturing norms. That way the manufacturing cost is reduced by at least 20 per cent, and you get an advantage of getting the latest German technology at an affordable price. And this benefit is passed on to the customer. It’s the best of both worlds. The best examples of these are machines coming from Monfongs, Goller as well as Karl Mayer (China).”
But moving forward from there, the next big thing for the textile business is the Industry 4.0 and, with the advent of the Internet, it’s time for the companies to play catch-up. With this in mind, how prepared is A.T.E. prepared for this?
Mr. Aras says: “The realization about Industry 4.0 happened a couple of years ago. Industry 4.0 is nothing but a combination of digitalization, automation, robotics, Internet of Things (IoT) and artificial intelligence.”
Considering this a couple of years back A.T.E. has set up a division for automation. He says: “Investment in machinery in our industry is highly capital intensive, and in India not everyone can afford to buy new machines every few years. Seeing the large need of the industry for upgrading the old machines for better productivity, quality and monitoring, our automation team tied up with a company in Pune, Softech, who helps us in this endeavor with their process control knowhow. With A.T.E.’s domain knowledge on processes and technology and the software & controls coming from Softech, we have best in the class solutions in automation for the industry”.
A lot of the machines in the mills that are used in the current times are at least two decades old, and despite that they are in good working condition and hence eliminates the necessity to scarp them. This is where the company’s automation division helps where they provide all kinds of solutions for upgradation in the processing and sizing areas.
Our team audits the existing range of machines and upgrades them by changing drives, PLCs and some of the key components in the machines. This comes at around 25% of the cost of a new machine and provides the old machines with a fresh lease of life in terms of better controls, increased productivity and improved quality of production. Even some of the leading mills like Welspun, Raymond, Premier, Arvind, JCT and Soktas implemented our automation solutions for upgrading the older machines in processing or sizing, and it has worked wonders.
The second area where A.T.E. has entered while keeping up with the Industry 4.0 is the “Internet of Things”. A.T.E. has a group company EcoAxis, which has the expertise in industrial processes and systems, data acquisition, algorithms and big data analytics. “EcoAxis provides technology for remote monitoring of the plant and equipment which helps in managing and analyzing the data most efficiently”.
Zenith Silk Mills in Surat has implemented EcoAxis’s IoT solution in its mill in the loom shed, and today they receive real-time data analysis through useful reports without having the need to be physically present.
He adds that, despite industry’s efforts for preparedness for the revolution of Industry 4.0, some areas like artificial intelligence, data security, application of robotics, etc., still have a lot of ambiguity and thus a long way to go for the conventional manufacturers. “Change doesn’t come with a notice. So it is important that we all from the industry gradually adapt to the upcoming changes like Industry 4.0 before the technology disrupts our present manufacturing and make us uncompetitive. This is especially important since the competition for our industry is global now and as a country we have to keep pace with digital technology absorption in manufacturing and supply chain”, he adds.
Going forward, where does A.T.E. see itself and how do they plan to keep up with the pace of growth?
Mr. Aras says: “We have already reached a certain level after growing in the last few years, and obviously it is very difficult to keep on growing at the same pace. The growth could also come due to diversification of our product basket and pursuing with the philosophy of “End to end solution” for our customers. A.T.E. as a company doesn’t have a presence in bigger market size opportunities like ring spinning, weaving machines, etc. Next big growth can happen only if we have a chance to enter this space in the future. Otherwise, we will have to focus on our present businesses, consolidate the gains and work towards retaining the position of a preferred technology supplier for the Indian textile industry”.
There is a lot that the textile industry needs to embrace itself in the coming years for its survival and growth, and A.T.E. as a technology partner to most of the textile companies also has to play its role. However A.T.E. being one the key players in the textile machinery industry is surely quite ahead in the game.