Launch of new stenters at ITMA 2015 planned
Earlier this month, the Ahmedabad-based Inspiron Engineering Pvt. Ltd. inked an agreement with Batliboi Ltd., under which Batliboi will market their stenters and heat recovery systems in various markets of India. Under the terms of the agreement, except for a few pockets of the Delhi NCR region, Surat and decentralised pockets around Mumbai, Batliboi will market these stenters across the rest of India.
Revealing details of the deal to The Textile Magazine, Mr. Prakash Bhagwati, Chairman at Inspiron, says: “Batliboi will market our existing stenter, Motex, as well as a new stenter model, Sprinton, which we will introduce in the Indian market shortly. Alongside, they will also market our heat recovery system, Kaprec, which we have already launched.”
Mr. Amol Bhagwati, Director at Inspiron, adds: “Except in a few markets where our existing marketing partners will continue to operate, Batliboi will market our stenters and heat recovery systems in the rest of India. However, the new stenter model Sprinton will be exclusively marketed by Batliboi across all Indian markets.”
Mr. Nirmal Bhogilal, Chairman at Batliboi Ltd., adds: “A well-engineered and energy efficient stenter was what Batliboi was looking for, to complete our textile finishing machine product portfolio. This also goes very well in line with the Batliboi belief and commitment to promote well-made Indian products.”
According to Mr. Prakash Bhagwati, the main reason for choosing Batliboi is because they are very strong in the knits segment, since they represent German knitting machine manufacturer Mayer & Cie in India, and alongside Batliboi also has in its portfolio various knit fabric processing machines, except the stenter, which gives him optimism that sales of their stenters will receive a boost from the partnership and they will also be able to fully utilise their production capacity for stenters in the 2015-16 fiscal year.
“Secondly, since Batliboi is a very old company, they have good contacts with large process houses, including renowned composite textile mills. Our association with Batliboi and our existing marketing partners will further strengthen sales of stenters and, with the orders on hand and new orders from Batliboi, we expect stenter sales to surge by 30-40 per cent in the current fiscal,” Mr. Amol Bhagwati quips.
The senior Bhagwati is of the opinion that looking at the market size of stenters in India, they have not been able to capitalise on the same, so he expects this partnership to help increase sales of stenters and thereby, also help raise their market pie of the Indian stenters market.
Both the Bhagwatis expect the results of the partnership to deliver fruits beginning from the third quarter of the current fiscal year and while Batliboi will only market the machine, after sales service will continue to be offered by the technical service team at Inspiron.
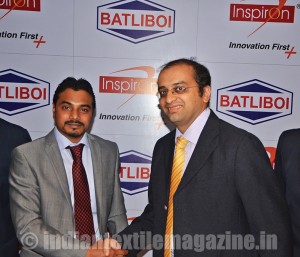
The new stenter model Sprinton and a heat recovery system, Kaprec, also a recently launched product, are fruits of the R&D efforts put in by Inspiron in recent years. Earlier in the past Inspiron has relied upon borrowed technology. When the licensing arrangement expired in September 2012, it was necessary to look inwards for development and better features. This prompted them to start R&D activities two years back, to offer fabrics processors an advanced stenter.
They began by outsourcing several R&D activities to various reputed companies in India. For instance, they began by giving an appealing, aesthetic and ergonomically designed look to the Sprinton, which was done by a company in Pune. Additionally, a German consultant, Nirma Institute of Technology and a software company from Pune all pitched in to make the Sprinton an advanced and innovative stenter.
The stimulation software installed in the Sprinton helps in computing and analysing fluid dynamics and also helps control the volume and passage of hot air to dry the fabrics. Inspiron also redesigned nozzle holes through which the hot air passes, which helped the efficiency of the drying process improve by 15 per cent, when compared with the Motex. The higher drying efficiency helps run the Sprinton stenter at higher speeds, which in turn also increases the productivity by 10-15 per cent at the same operating costs.
The Sprinton, which is compatible with both knit and woven fabrics also features a user-friendly touch screen graphic interface, through which an operator needs to just input the formulas, which will help him to calculate the volume of inputs needed for processing the fabric. The system also stores and recalls earlier recipes, when processing the same type of fabric. Additionally, the control panels of the Sprinton stenter also have been incorporated into the console.
Inspiron has also made changes in the chain, which holds the fabric when it is moving in the stenter and also stretches it in heated conditions to make the fabric stable and moves it through the entire length of the machine. The new chain developed by Inspiron in collaboration with the Nirma Institute of Technology, is lower in weight by 10 per cent, without affecting the properties and usefulness of the chain, which in turn, saves electric energy to run the chain.
Mr. Amol Bhagwati discloses that they have already installed the first of the Sprinton model at an Arvind Mill group company, Ankur Mills in Ahmedabad, and the efficiency figures quoted, have been derived from the actual operation of the Sprinton stenter at Ankur Mills.
“Motex is pegged between Indian suppliers and imported suppliers and is a machine of Indian origin, with European quality standards, but offers value, a proposition Asian client’s look for. The investment costs may seem relatively high, however the operating efficiency and better evaporation capacity create a situation of faster payback period, which is the USP of Motex,” Mr. Prakash Bhagwati observes.
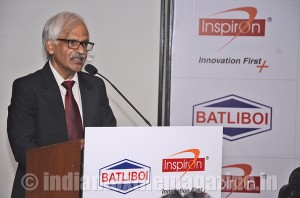
“On the other hand, Sprinton, the newly-developed machine, will be positioned at the top end of the global market with European equivalents like Bruckner, Monforts, etc. In short, both Motex and Sprinton will win higher acceptance vis-à-vis competitors, as both offer a unique ‘Value-for-Money’ proposition to the end user,” he explains.
Kaprec, the newly-launched heat recovery solution, is also a result of Inspiron R&D efforts. Normally; a heat recovery system needs to be cleaned once a month or bi-monthly, due to fluff accumulation and alongside, is also a cumbersome process. Additionally, the stenter has to be cooled down before cleaning begins and once the cleaning process is over, the stenter once again needs to regain the required temperature, before the fabric processing can be restarted.
“All this leads to loss of at least 12-16 working hours for the stenter, while with the Kaprec, one needs to clean only once every 10-11 months, due to the way it has been designed, leading to reduced down times for the stenter machine, resulting in higher productivity. Secondly, the Kaprec can also be installed in various other textile processes where heat recovery systems have been installed,” Mr. Amol Bhagwati explains.
Alongside stenters and heat recovery systems, Inspiron, an ISO 9001:2008 company, also manufactures flyers for roving machines, with OEM revenues making up for a major part of the sales. Buyers of their flyers include the likes of LMW, Rieter, Marzoli, Electrojet, Saurer, etc.
According to Mr. Amol Bhagwati, the flyers division is completely dependent on the business of roving machines of these companies, and alongside, it also serves the replacement market for flyers across the world, which however is very small compared to the OEM business.
After having achieved success with its outsourced R&D activities, Inspiron is now setting up an in-house R&D facility, which will house the Sprinton stenter. Researchers at the facility will be tasked with constantly bringing innovations into the stenter.
It will also have a laboratory, where finishing chemicals will be tested and new recipes will be developed. Potential clients will be invited to conduct trials on the Sprinton before they finalise the purchase of the stenter. Inspiron will also invite suggestions from its existing user base to make future Sprinton models more innovative.
Inspiron, which was set up way back in 1974, with its considerable experience of non-ferrous foundry is also working with mid-sized European companies as their sub-contracting partners. This concept was extended to supply calibrated sub-assemblies to make Inspiron a full-fledged sub-contracting partner.
In order to offer a total precision engineered solution (PES) as a sub-contracting partner, a facility for mechanical engineering design services like Knowledge Process Outsourcing (KPO) was added. Through which, its European partners have derived advantages like time to market, spare critical design personnel to do core work and finally reduction in engineering costs.