Benninger is continuing to expand its world-leading offer to the textile wet processing sector, with recent innovations in fabric dyeing and singeing technology – as well as strengthening its services and support for customers in India and beyond.
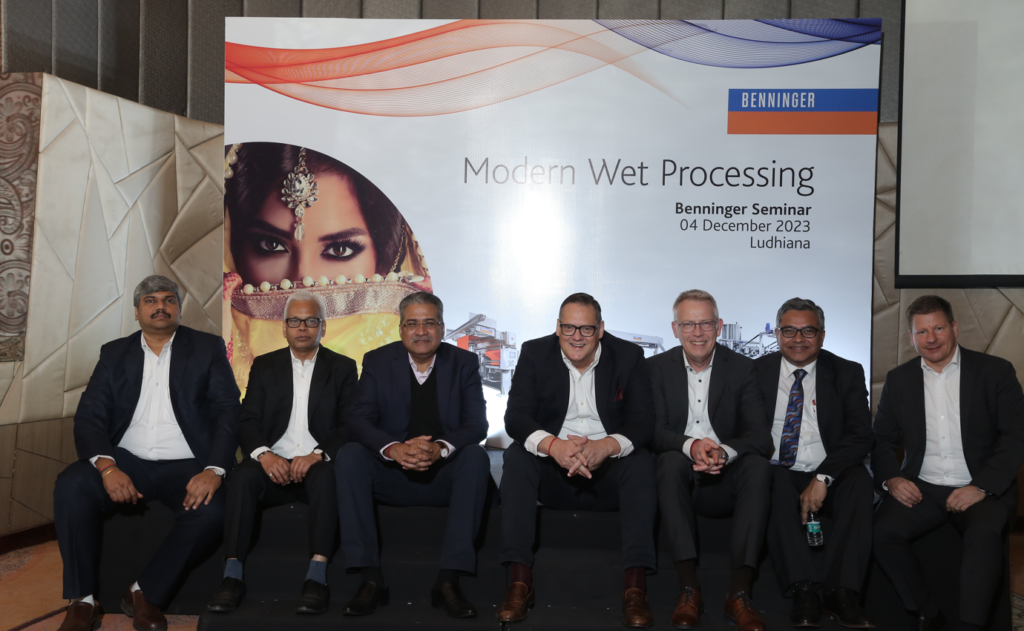
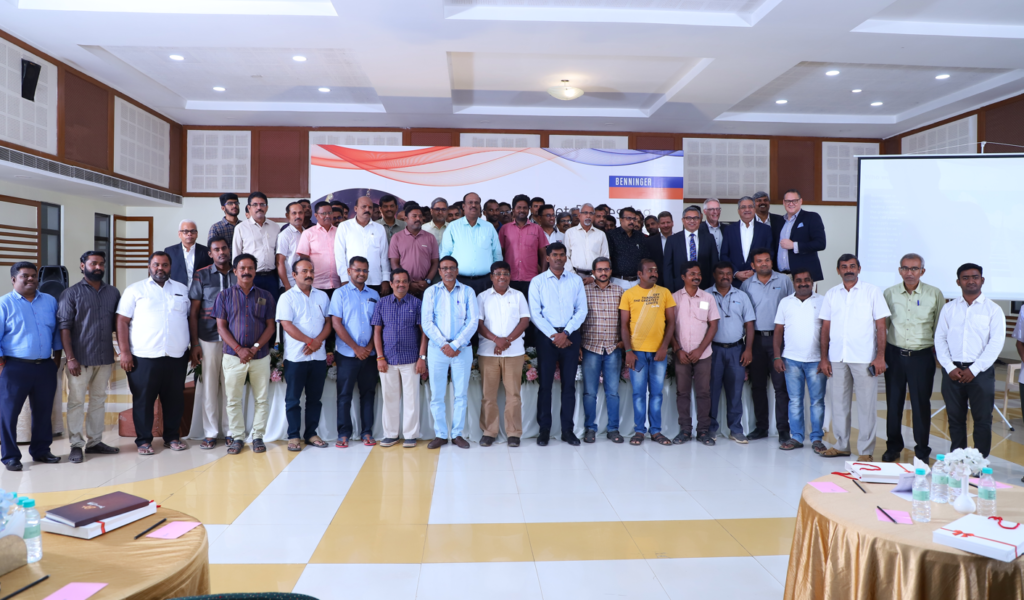
Benninger specializes in machinery and solutions for both continuous and discontinuous wet finishing of woven, knitted and technical textiles. Its heritage of 160 years is the foundation for ongoing progress, with today’s systems embracing sustainable production towards zero environmental impact for its global customer base.
As part of its customer commitment, Benninger has further grown its service teams of technicians, electricians, technologists and local sales personnel in India. Currently, over 20 experienced and dedicated professionals are ready to assist customers on the subcontinent and in Asia. Benninger also staged customer seminars in Tirupur and Ludhiana on December 2 and 4. “We wanted to introduce our local team and take the opportunity to present Benninger’s modern wet processing solutions that ensure decarbonization while boosting the customers’ top line and securing their bottom-line,” says Rolf Erik Schoeler, Global Head of Sales and Marketing at Benninger.
Pioneering FabricMaster
A game-changing solution in Benninger’s portfolio for discontinuous dyeing is the new FabricMaster, proven in practice to be the fastest, most versatile, and economic jet dyeing machine in the industry. It produces a wide range of fabrics with unmatched low water consumption levels. Furthermore, it ensures dramatically shorter process times and an excellent first-time-right rate. The robust and reliable system with its harmonic versatility ensures that customers can process today’s and tomorrow’s fabrics and blends.
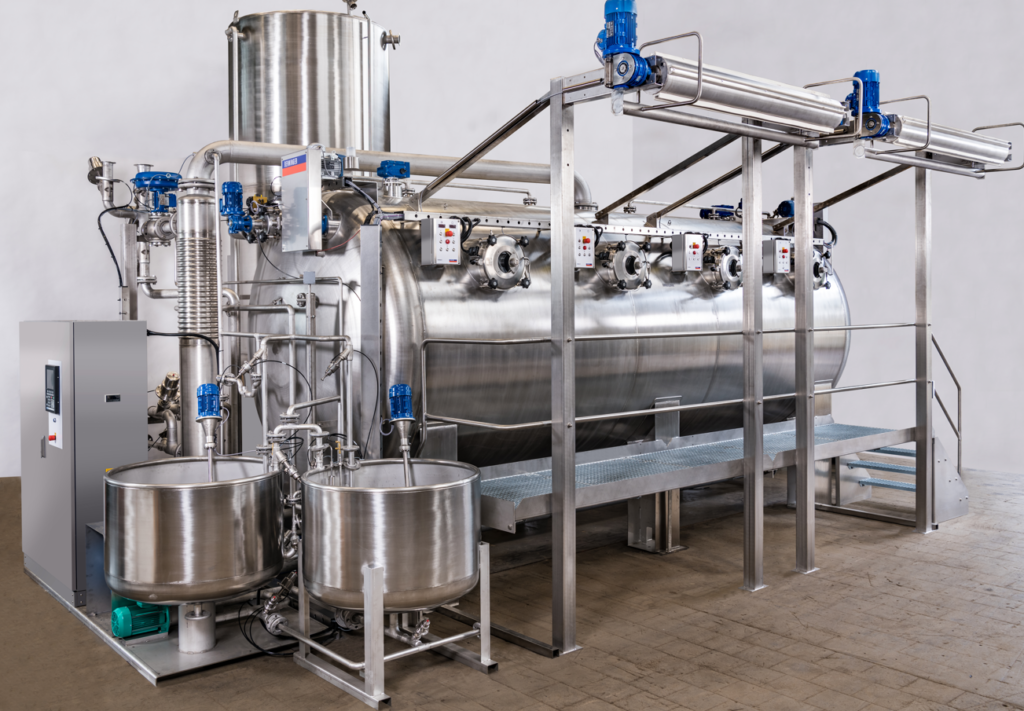
Benninger’s experience means it fully understands the challenges of the wet finishing industry, as reflected in its development priorities for new machinery. Key factors are minimal consumption of water, steam, chemicals and dyestuff, to ensure right-first-time results with lowest waste.
Specifically, the company’s discontinuous dyeing technology has precise control of processes and chemical distribution (DDS, CDS, PDSD), setting new standards for shortened process times, and accuracy in maintaining the required batch sizes, weight and liquor ratio. The carbon footprint of the FabricMaster is designed to be the future industry benchmark for sustainability.
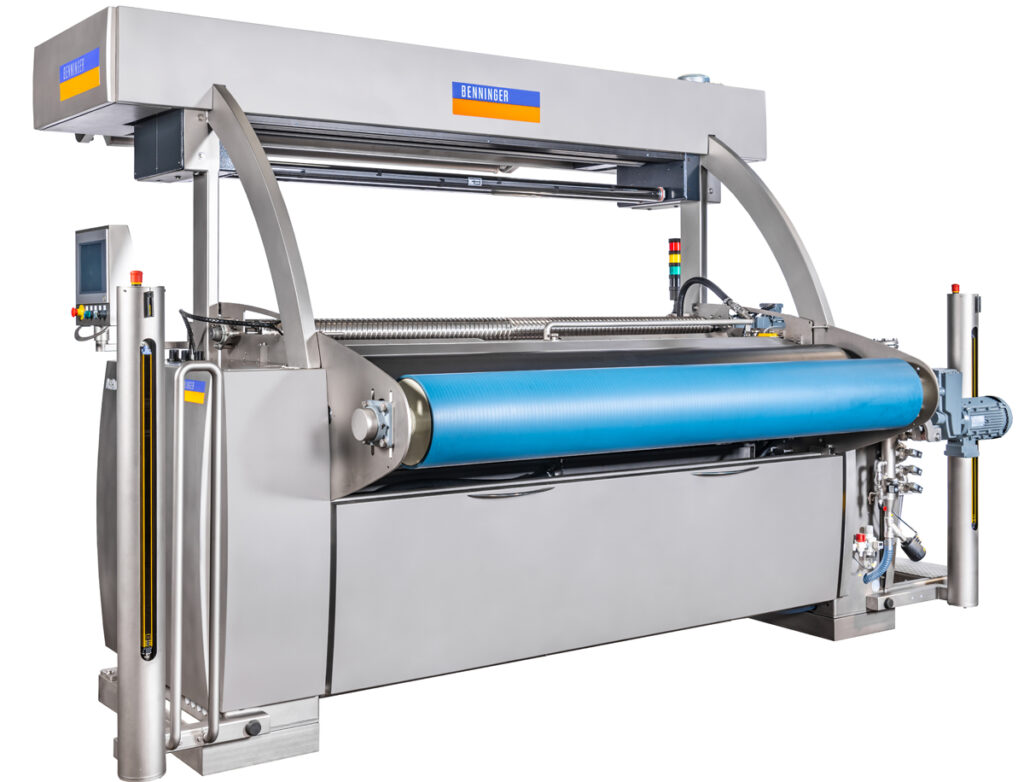
Foundation for uniform quality
The latest Benninger fabric singeing machine, known as the SingeRay, lays the foundation for uniform quality to produce a perfectly dyed and finished fabric. The high-performance burner ensures a flame with high energy density over the complete width, for incomparable singeing effects. Its unique flame width setting allows finishers to work with even smaller fabric widths economically, saving energy. Thanks to the super-smart burner design, which also prevents deformation due to its 2×2 cooling system, it ensures longevity. The SingeRay is made in Germany and certified by the German Technical and Scientific Association for Gas and Water (DVGW) to the highest safety standards.
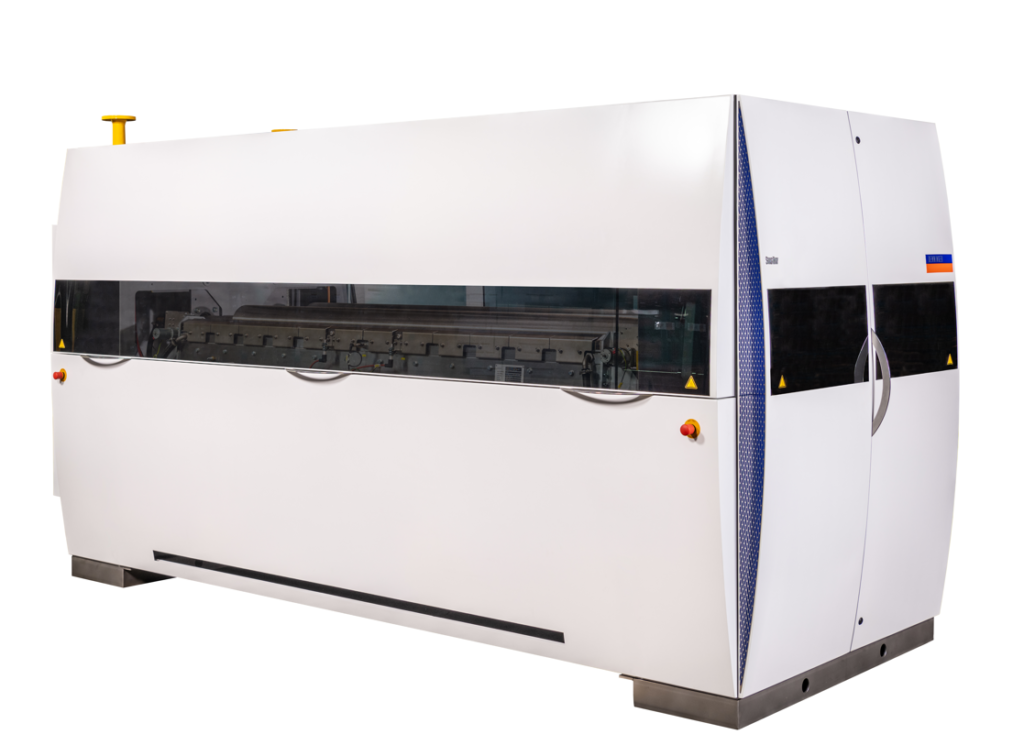
For knitted fabric processing, Benninger’s Knitline solutions are installed at more than 120 mills of major producers worldwide, demonstrating great standards of performance with highest quality results in demineralization and bleaching. Recent technical enhancements have made a significant contribution to reducing operating costs for users.
Road to zero
The full range of Benninger technology includes well-established solutions for all aspects of open-width wet processing, as well as discontinuous fabric dyeing, underlining its position as a systems supplier in the forefront of the industry.
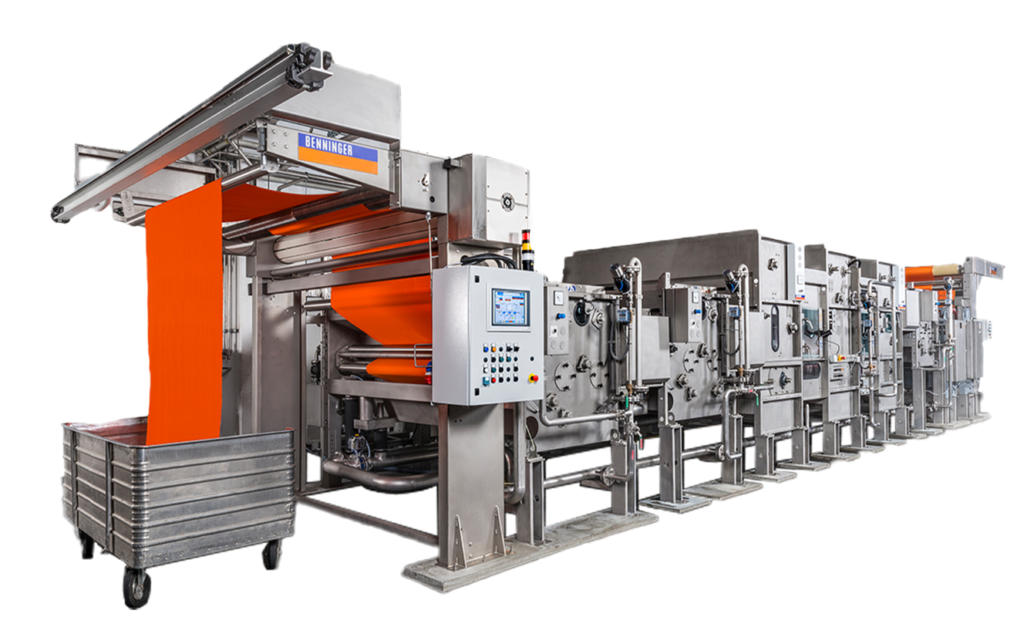
The duty of environmental responsibility in that role is one that the company fully acknowledges: “Benninger solutions always focus on resource efficiency, so textile finishing plants with Benninger machines installed can be assured of particularly low resource consumption and highest productivity,” says Schoeler.
This topic of sustainability was a major theme at the recent seminars in India, where attendees were advised how to make further progress on their own road to zero.
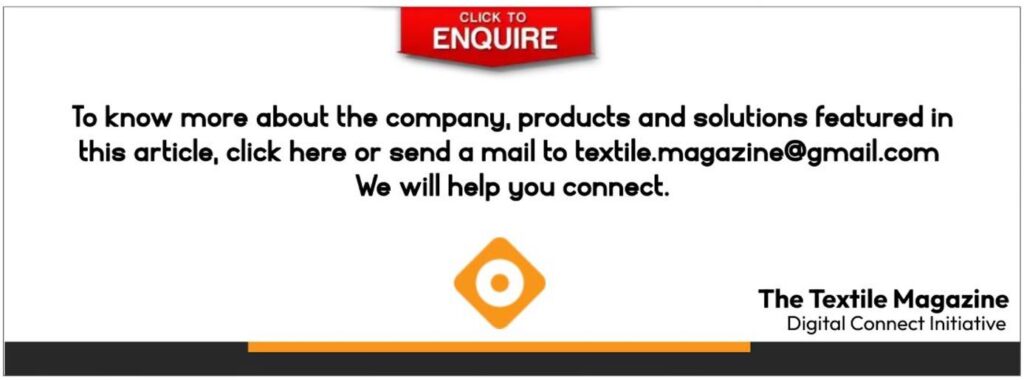