Sustainability has become a form of hygiene and at Birla Cellulose Grasim’s global leadership position is embedded in its sustainable forestry, water management and production process management. This is well-recognised by both global and Indian brands and is a key factor in the company’s growth story and the reason why brands and consumers are backing it
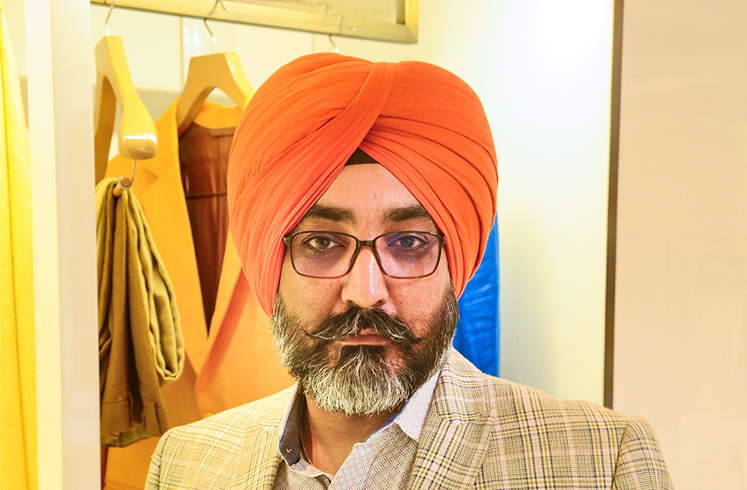
Birla Cellulose is a name that needs no introduction to anyone familiar with the Indian textile fraternity. The company, a part of the Aditya Birla Group and one of the largest global manmade cellulosic fibre (MMCF) producers, has been setting the standards in the industry for quite some time now. It has 12 manufacturing plants of which five are pulp manufacturing plants in Canada, Sweden and India and seven are fibre manufacturing plants in India, China, Indonesia and Thailand. “We are one of the largest producers of viscose staple fibre globally with a capacity of ~ 3,500 tonnes per day (TPD), including the recent expansion of 600 TPD capacity at one of our facilities in India,” informs ManMohan Singh, Sr. President (Marketing and Business Development).
When queried about the company’s new products, innovations and technological advantages, Singh replies: “New products, innovation and technological upgrades are important for every industry. Innovation has always been the core of Birla Cellulose and we have proved our mark with innovations like Livaeco, Liva Reviva, anti-microbial viscose and other array of products. Birla Cellulose was the first company to launch viscose fibre made using recycled content, commercially under the brand name Liva Reviva. We have used 20% input from next-generation feedstock leading to the saving of natural resources.”
“The innovation has been much appreciated by global brands and we are looking forward for co-branding and co-launch with some of the leading global brands. Meanwhile, continuous upgrades of technology for quality improvement have helped us in sustaining and growing markets, which is the key objective of the Birla Cellulose team. Our manufacturing sites in India – Nagda, Vilayat and Kharach – spearheaded innovation in closed-loop technologies for water and these were widely adopted by all our viscose fibre manufacturing sites,” Singh adds.
The technologies for water have helped in the following ways:
• Reduce water consumption by better technologies that require less water.
• Reuse water in the process or other applications multiple times. Circular technologies have enabled water to be used several times in finishing and recovery processes.
• Recycle water with innovations in wastewater recycling technologies and advanced membrane-based technologies. The water quality achieved after recovery is better than raw water quality from the river.
• Regenerate water through harvesting by building dams and reservoirs to store water in the rainy season that can be used later in the year.
According to Singh, the company’s share of share of domestic and exports business is almost equal. “In the last five years, our consumption in India market has grown almost 2.5 times because of our marketing efforts and the pull created through the ingredient brand LIVA. Our key customers are premium retail brands in India and across the world,” he adds.
Advantages Galore
Pointing out the advantages offered by the company vis-à-vis its competitors, Singh mentions that fibres from Birla Cellulose are differentiated at three levels:
• Raw Material: Birla Cellulose has sustainable forestry sourcing policy in place and 100% of the wood that it uses comes from certified forests. This ensures that ancient and endangered forests are protected. While harvesting wood, sustainable practices are followed.
• Manufacturing: The manufacturing site adopts best-in-class processes to minimise resource consumption through recycling of chemicals. It has achieved more than 93% score in Higg FEM’s evaluation done by Sustainable Apparel Coalition.
• Traceability: Birla Cellulose offers end-to-end traceability through two pillars of source verification – molecular tracer inside the fibre helps in source verification of the fibre at any later stage whether it is yarn, fabric or garment while block-chain-enabled GreenTrack™ tool helps in end-to-end supply chain transparency from forest to fashion.
Leadership in Sustainability
The company has always been known for its strong sustainability focus. Going into details regarding some of the key sustainability initiatives of the company, Singh informs, “Sustainability has become a form of hygiene and at Birla Cellulose Grasim’s global leadership position is embedded in our sustainable forestry, water management and production process management. This is well-recognised by both global and Indian brands and is a key factor in our growth story and the reason why brands and consumers are backing us. Consumers are demanding that companies and brands care beyond revenue and no longer perceive businesses purely as profit-driven entities.”
“Protecting the health and interests of society and the planet are new expectations in order to ‘build back better. Viscose inherently is a more sustainable fibre compared to other major cellulosic or synthetic fibres. There is scarcity of natural resources – be it water or land – and on the other hand non-bio-gradable textile is a big challenge. Natural cellulosic fibre consumes more resources like land and water while on the other hand most of the synthetic fibres are non-biodegradable. Micro-fibre enters the river systems, river bodies and then the food chain. With Livaeco we have taken this a step further,” Singh adds.
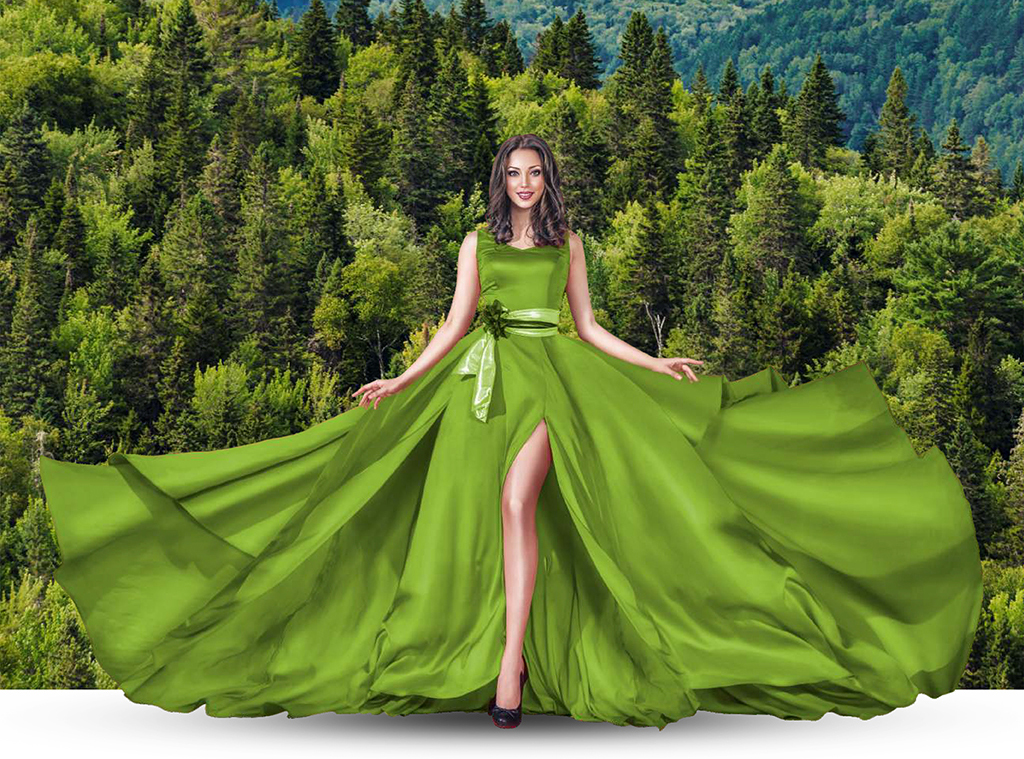
“Livaeco has got certain enhanced credentials of sustainability than regular LIVA. It is ensured that all the wood we use for Livaeco is sourced from FSC®- certified forests in addition to sustainable manufacturing process with clear focus on environment protection. Recently, we have got three of our manufacturing sites approved by the European Best Available Technologies (EU-BAT),” he further states. The company has also been a pioneer when it comes to adopting automation. Sharing more details, Singh mentions that Birla Cellulose has adopted digitalisation in:
• Real-time vertical integration planning in production to optimise production capacity.
• End-to-end logistics visibility for last mile notification.
• Data analytics solution to assess near real-time demand variations.
• End-to-end traceability platforms like GreenTrack™ for complete transparency of the supply chain that targets exponential growth.
Road Ahead
Finally, when asked to share the company’s future growth plans and vision for 2025, Singh comments: “VSF has been one of the fastest growing fibres amongst all the fibres and its growth rate has been close to double digits. We think that this would be a fibre which would continue to grow at the highest rate compared to all other fibres. Keeping the current growth trajectory in mind, the company has already gone ahead with the expansion of the Vilayat unit and with this it will become one of the largest single locations of VSF facilities. This expansion will increase Grasim’s VSF capacity by about 40%, which will cater to the growing demand for sustainable manmade cellulosic fibres in the country. We have recently commissioned the first of two phases with 600 tonnes per day capacity expansion project at Vilayat.”
“This is a state-of-the-art plant with closed-loop technologies in manufacturing to enable the site to get an EU-BAT-compliant status. Between this year and next year, additional 2,20,000 tonnes of sustainable VSF and modal will be brought to the market. Birla Cellulose plans to aggressively scale up the production of circular fibre Liva Reviva to a level of 1,00,000 tonnes per year by 2025. One of our key strategic partners in this journey is environmental not-for-profit canopy – an initiative that is now supported by over 450 brands and retailers,” Singh further states.
—
“We are one of the largest producers of viscose staple fibre globally with a capacity of ~ 3,500 tonnes per day (TPD), including the recent expansion of 600 TPD capacity at one of our facilities in India
– ManMohan Singh, Sr. President (Marketing and Business Development)