With the company’s renewed focus and financial profile combined with its state-of-the-art production facility, BRFL Textiles is poised to be the leader in fabric processing in India, catering to domestic and international fashion trends
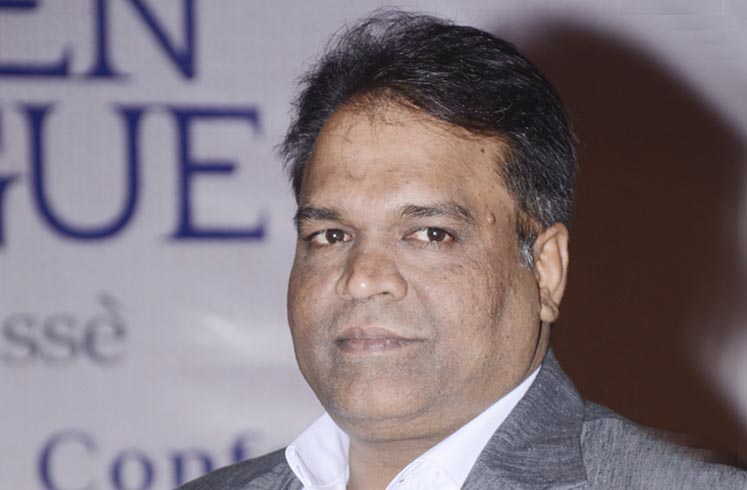
BRFL Textiles Pvt Ltd (BTPL) was established as a new entity in August 2020. The entity was formed as part of a restructuring process undertaken by Bombay Rayon Fashions Limited, in which it hived-off its yarn dyeing and fabric processing units located in Tarapur into BTPL by way of a slump sale on a going concern basis, along with all associated brands, employees, assets, etc. This was followed by a private equity infusion funding of about Rs 240 crore from a consortium of marquee financial investors. Since the funding, in just these three months of operations, the company has ramped up its production significantly to reach 40% utilization levels already, even in these tough market conditions.
With an annual processing capacity of 144 million meters (400,000 meters per day), BRFL Textiles Private Limited (BTPL) today houses the largest single roof fabric processing unit in India at its plant located at Tarapur in Maharashtra, India. With the company’s renewed focus and financial profile combined with its state-of-the-art production facility, BRFL Textiles is poised to be the leader in fabric processing in India, catering to domestic and international fashion trends.
Giving an insight into the company’s products, Prashant Agrawal, Managing Director, mentions that the Tarapur plant is engaged in multi-fiber fabric processing, and utilizes raw materials such as cotton, linen, Giza, viscose, polyester, tencel, modal, Lycra and a combination of fabric blends. BTPL is engaged in the processing of fabrics using world’s best state-of-the-art European technology. “The advanced technology stack at our plant complemented with the skilled manpower enables us to process multi-fibre fabrics at our Tarapur unit,” he adds. BTPL has a strong presence in the B2B and B2C space along with long-standing relations with leading brands across the globe, and sells through large garmenters across India who also sell to domestic brands. On the domestic branded sales front, the distribution network of BTPL is spread across its own EBOs, over 100 distributors and over 8,000 retailers.
Manufacturing Infrastructure
The Tarapur plant is adequately supported by its captive power, effluent treatment, RO water and other utilities enabling cost competitiveness.
• Prints Capacity – 1, 25,000 meters/day.
• 11 Rotary machines of make “MHM” and 16 digital printers of make “MONA LISA” for printing.
• Solids – 1, 50,000 meters/day.
• 4 CDRs of make “MANFORTS”
• 13 exhaust dyeing of make “THEIS SOFT FLOW” \
• 10 Jigger dyeing machines of make “THEIS”.
• Yarn Dyed – 1, 25,000 meters/day.
• 65 yarn dyeing machines of make “LORIS BELLINI” ranging from 1.6 kgs to 1,056 kgs.
When queried about any recent investments or expansion of capacity, Prashant Agrawal, answered in the affirmative. “Since the funding, the company has ramped up its production significantly at the Tarapur plant from 1,00,000 meters per day to now 1,50,000 meters per day as a consequence of improved capacity utilization. The funding raised has enabled the company to make certain capital expenditures and maintenance expenses towards our state-of-the-art machineries. Also, we have utilized the funding to add to the technology side of our operations. Our immediate plan is to utilize the installed capacity of 4, 00,000 meters/day, and we are looking at expanding to reach full capacity over the next two years. We will also look at simultaneously dominating the domestic market through robust distribution networks, driving innovative products across linen, cotton and viscose fabrics and strengthening our brands,” he says.
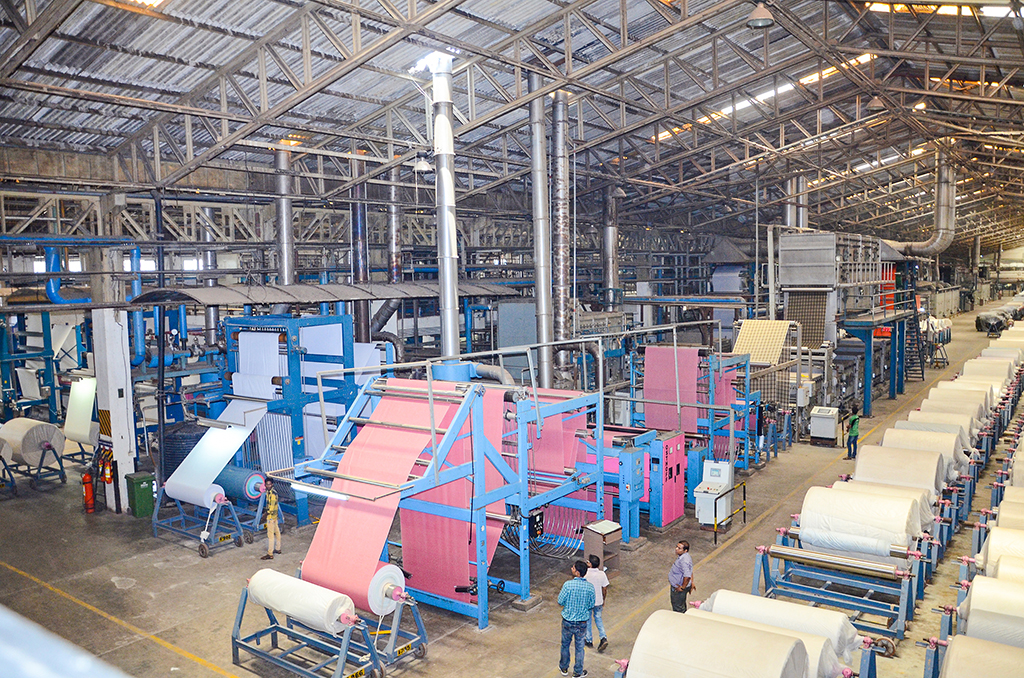
“We strive to improve our production and are looking to scale it based on the growth and demand from the industry. We now stand as a debt free company which gives us enough flexibility and liquidity to expand the range of services that we provide, and to make further investments within the company”, he shares. Speaking about new products he quotes: “We are currently concentrating on utilizing the installed capacity of 4,00,000 meters/day, but we do have plans to diversify into new products, which we will explore at a later stage. We have recently collaborated with world-renowned fashion designer Manish Malhotra to unveil a limited edition of designs under our fabrics brand, “Linen Vogue – La Classé”. We are also continuously developing blended fabrics for various price points catering to mass brand markets.”
Global Presence
BTPL supplies its fabrics to Indian and International markets, including USA, Mexico, Japan, Netherlands, UAE, Saudi Arabia, South Africa, Indonesia, Hong Kong, Vietnam, Malaysia, Cambodia, Sri Lanka, Bangladesh, Thailand, Myanmar and others. In terms of domestic brands, Allen Solly, AND, Arrow, Benetton, Blackberry, Fab India, Indian Terrain, Jack & Jones, Levis, Numero Uno, Pantaloons, Reliance Trends, Only, Shopper Stops, US Polo, Vero Moda, and Westside are some of the major names that the company supplies its fabrics to. The company’s products are also supplied to a number of international brands as well, such as, A&F, American Eagle, Ann Taylor, Belk, Carrefour, Cecil, George, JC Penny, K-Mart, M&S, Macy, TJ Maxx & Tom Taylor.
Key Strengths
Listing the key advantages offered by the company over other competitors, he points out that over the years, BTPL has been a supplier of choice for clients due to the company’s design capabilities, market intelligence, innovation, cost effectiveness and efficient lead times. The Tarapur plant is one of the most technologically advanced and leading fabric processing plants in India, which makes it a preferred unit in the country. “We are a customer-centric company and, hence, rather than chasing growth we have been advising our customers to play safely in this volatile market. This approach of standing by the customer in difficult times has in turn given us more business from our customers as they are confident of us meeting their expectations and commitments,” he states.
“We strive towards continuous product development and innovation and consistent investment in technology and sustainability. With our global standards and certifications, our customers can be assured that the products they receive are nothing short of the very best. Additionally, servicing our customers with timely deliveries makes us a preferred choice in the industry. We have the largest production capacity in the country currently, and have the capability to utilize them and deliver any large scale order before the deadline. We are capable of delivering volume orders in a short span of 2-3 weeks to meet the sudden gush of demand and repeat orders,” he remarks.
“We have always focused on high value-added design centric products and, hence, in this tough market of rising prices of various raw materials, we are able to still absorb these costs by bringing in more value additive products to compensate for lower volumes. One of our biggest advantages is that we provide greater flexibility in terms of product offerings at various price points and rapid responsiveness,” he adds. The company is among the select few who have done good business even during the pandemic. Prashant Agrawal proudly says: “During the pandemic, we did a business of around Rs 300 crore.”
The company has taken steps to strengthen its workforce in recent times. Going into the details, he reveals: “Recently, we have added several senior management to our team and grown our workforce from 1,300 to over 2,000 employees. We have hired over 14 people in senior management roles across functions. We will continue to further invest in people to ensure that our state-of-the-art plant is efficiently run and reaches its optimum processing capacity.” The company engages 301 women employees in its workforce with 272 contract female workers and 29 full time employees at present. The female employees in the organization hold important positions across departments including domestic marketing, design & development, audit, power plant, fabric design and public relations.
Sustainability Initiatives
Speaking about the company’s sustainability focus, Prashant Agrawal comments: “Sustainability is a big factor in our production processes. We have recently introduced a new sulphur dyeing process by continuous dyeing method that does not require water. BTPL is the first company in the textile sector to implement this new process of dyeing, making them the pioneers of this innovative sustainable process.”
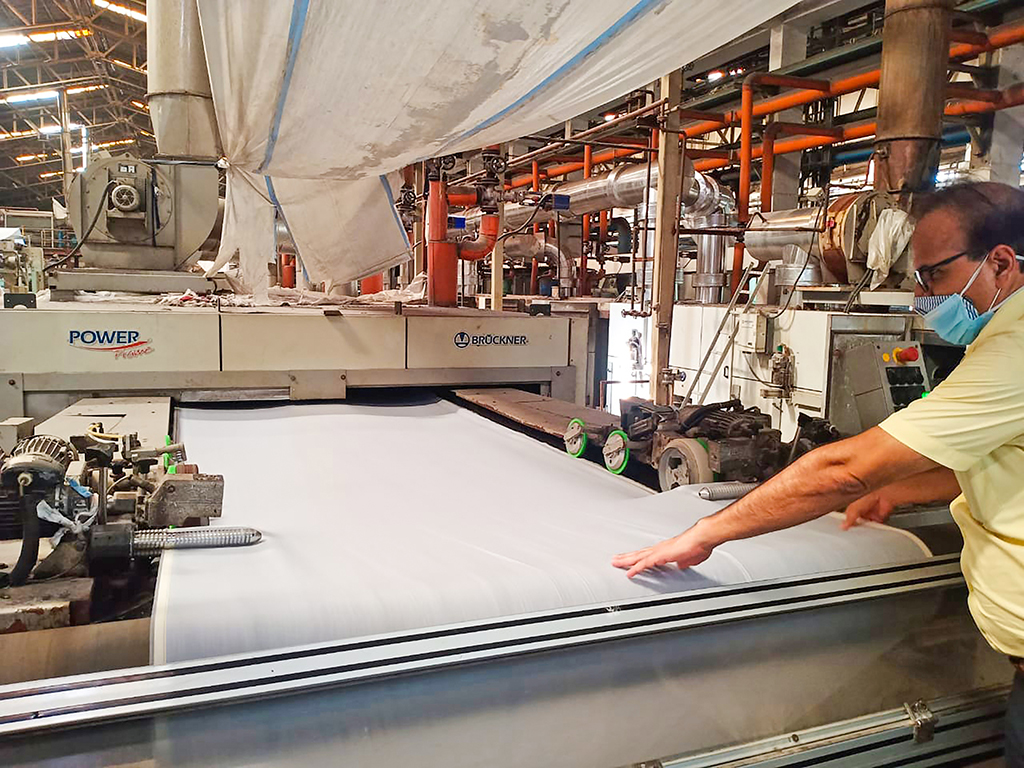
“BTPL, since inception, has taken efforts to limit carbon emission and recycling of water through multiple ways. The current efficiency of the reverse osmosis unit at BTPL’s Tarapur plant facilitates the unit to reuse 50% of the effluent water, enabling the plant to recycle up to 4 million litres of water per day. The company is looking to further strengthen this efficiency and aims to increase the recycling level to 90% in the next three months, enabling the plant to recycle up to 7.2 million litres of water per day. Additionally, most of the reactive dyeing processed in the plant is undertaken with e-control process, thereby avoiding salt which in turn avoids increasing the TDS content of water. BTPL also uses its energy co-generation design at its Tarapur plant, which enables it to reuse 48 tonnes of steam per hour, and save 250 tonnes of coal per day,” he says.
BTPL implements its sustainability measures across its products as well. A majority of the fabrics produced by BTPL, such as linen and cotton, are sold in its natural form, making it a part of the sustainability chain. Likewise, a large part of the linen and linen blended collection is produced by maintaining a natural fibre colour without adding any dye or colour to the fabric. In addition to this, the polyester blended fabric produced by the plant is made using recycled polyester. When it comes to automation, the company is well equipped with state-of-the-art European technology right from pre-treatment of fabrics to dyeing to finished fabrics.
Future Plans
When asked about the company’s future growth plans and vision for 2025 and beyond, Prashant Agrawal confidently states:” With our strong financial backing and state of the art production machinery, we aim to become a market leader in the fabric and textile industry. We aim to not only stand as a name in India, but on the international scale as well. While we have a number of developmental plans for the future, our most immediate plan is to utilize the installed capacity of 4, 00,000 meters/day. We are also looking to expand our reach and production capacity by 2023. By 2025, we aim to achieve total revenue of over Rs 3,000 crore. We want to stand as a prominent name within the domestic market, and want to increase the rate of our distribution networks. We also aim to release new lines of innovative products across the different brands that we work with such as Bombay Rayon, Linen Vogue La Classe’, Giza Classe’ and Dickens & Browne.”