Fashion for Good launches the Renewable Carbon Textiles Project bringing together a pioneering consortium to accelerate the development of Polyhydroxyalkanoates or PHA polymer fibres; a promising biosynthetic alternative to fossil based fibres with the potential to reduce carbon emissions in the fashion supply chain.
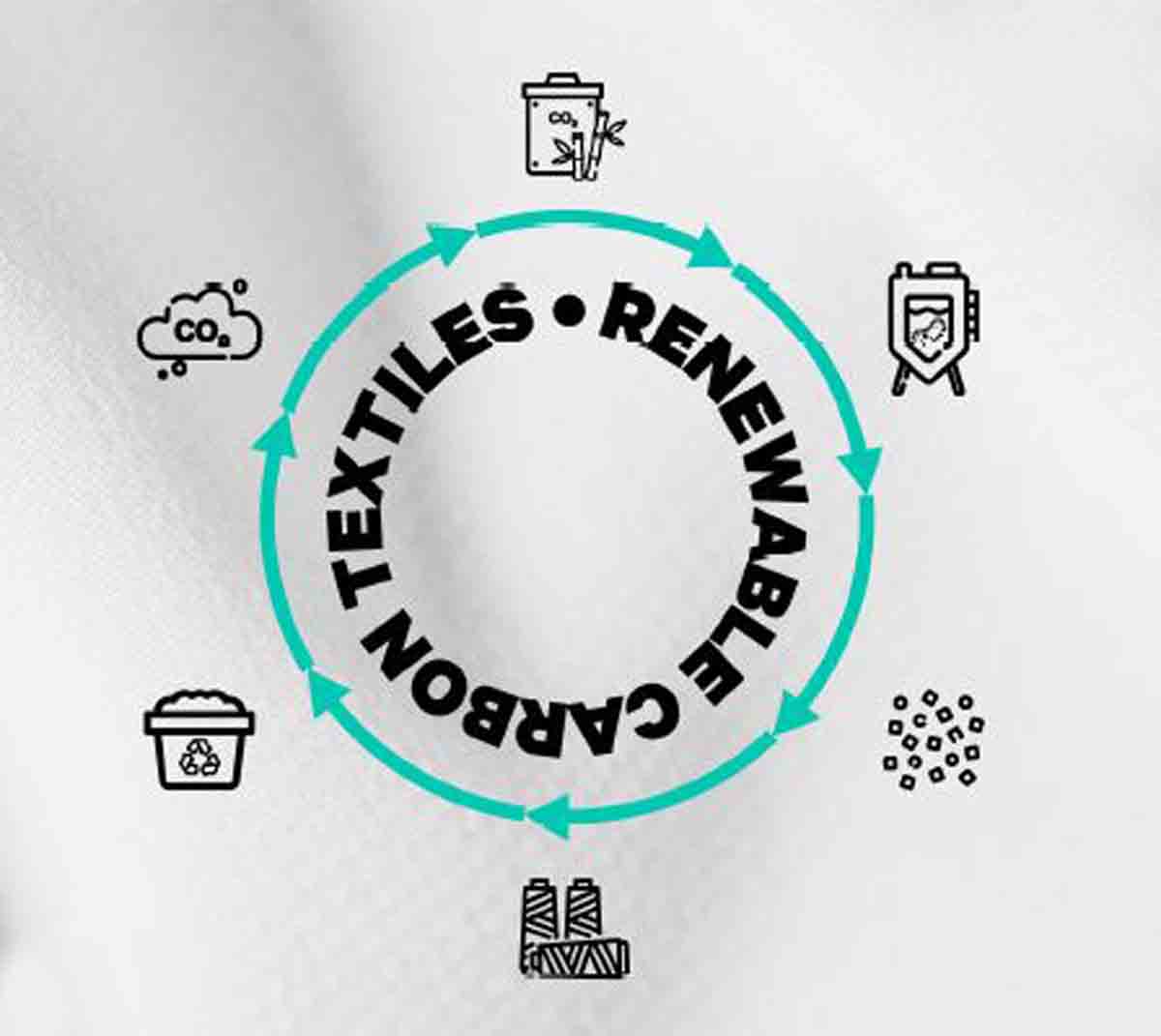
The project brings together key industry players to investigate, test and validate the solutions provided by innovators in the PHA polymer space. With catalytic funding provided by Laudes Foundation, collaborating partners include BESTSELLER, Norrøna, PVH Corp. and the Fabrics Division of W. L. Gore & Associates providing industry expertise and financial support. Participating innovators Bio Craft Innovation (formerly Biomize), Full Cycle Bioplastics and Newlight Technologies contribute their solutions to validate their potential, providing insights to scale the industry in the long term.
“There is an urgent need to find replacements for the predominantly fossil based fibres in the fashion industry through solutions such as biosynthetics from renewable sources. PHA polymers represent an exciting, yet challenging solution for reducing carbon emissions in the fashion industry, and this project aims to drive further innovation in this space to bring them to scale.” – Katrin Ley, Managing Director, Fashion for Good
The fashion industry accounts for around 4% of global greenhouse gas emissions (GHG-e), with 38% of these emissions coming from raw material production, preparation and processing and 3% from end-of-use. Polyester fibre is one of the most widely used in the fashion industry making up 52% of global fibre production.
The production of these virgin fossil-based polyester fibres are responsible for increased greenhouse gas emissions and its use results in the release of microplastics into the natural environment. Under the umbrella of the Renewable Carbon Framework initiated by nova-Institute, Biosynthetics made from renewable sources, such as agricultural byproducts, provide a solution to reduce plastic production and, ultimately, a brand’s overarching carbon footprint. In particular, PHA polymers provide a bio-based, marine and soil compostable solution to fossil-fuel derived polyester fibres, and could be a possible holy grail to decarbonising the fashion industry.
“Laudes Foundation is excited to support this consortium as a first step towards reducing fashion’s dependence on oil-based synthetics. This initiative is critical to unlocking the potential of renewable sources of fibres for the future and demonstrating their viability to the industry.” – Lakshmi Poti, Senior Programme Manager, Laudes Foundation
The Renewable Carbon Textiles Project is orchestrated by Fashion for Good, with catalytic funding provided by Laudes Foundation, in collaboration with partner brands BESTSELLER, Norrøna, PVH Corp., parent company of Calvin Klein and Tommy Hilfiger, and Gore, participating in testing and developing output materials, as well as providing their technical expertise and industry insights. This will enable the evaluation of the suitability of PHA polymers, accelerate fibre development and production, and determine scalability in the traditional supply chain. The end-of-use pathways for the fibres will be evaluated through third-party degradation and recyclability testing, to ensure circularity.
“Biopolymers represent an exciting area of innovation to help tackle both the use of virgin resources whilst opening up potential solutions for other sustainability challenges. Within this space, the family of PHA polymers is particularly exciting as they have a variety of performance characteristics, many of which are still to be explored. This project is a fantastic opportunity to drive forward fibre development which has the potential to be incredibly disruptive to the industry.” – Sophie Mather, biov8tion, a Fashion for Good Advisor
Bio Craft Innovation, Full Cycle Bioplastics and Newlight, leading innovators in the field of biopolymers, join the project applying its expertise in biology, chemistry and engineering to not only produce the fibres, but also further develop fibre melt-spinning, a traditionally challenging, yet critical step in PHA production. Until now, commercial melt-spinning trials have not used PHA polymers. As such, there are still some manufacturing challenges and additional technical assessments needed to compare and evaluate the different polymers.
This project focuses on validating the technical feasibility of the output, working with the Nonwovens Innovation & Research Institute (NIRI) to run the melt-spinning trials. This allows for a comparative evaluation which can provide key learnings on how to best support and bring these technologies to scale.
“One of the key pillars of our vision to create fashion that Wastes Nothing and Welcomes All is reducing our negative impacts to zero, with targets on eliminating carbon emissions and innovating for circularity. With initiatives like this, we are helping to drive tangible, meaningful change. It’s fantastic to be working with these companies and fellow Fashion for Good partners to drive fashion forward, for good.” – Kashif Noor, Director of Innovation, Tommy Hilfiger
Alongside the technical feasibility study, the project includes a range of degradation testing that will be conducted by Organic Waste Systems (OWS). Leading in biodegradability, compostability and ecotoxicity testing, OWS will run tests in marine, soil, freshwater and landfill environments in mid 2022 to assess the biochemical properties of the fibres and whether they break down in these environments.
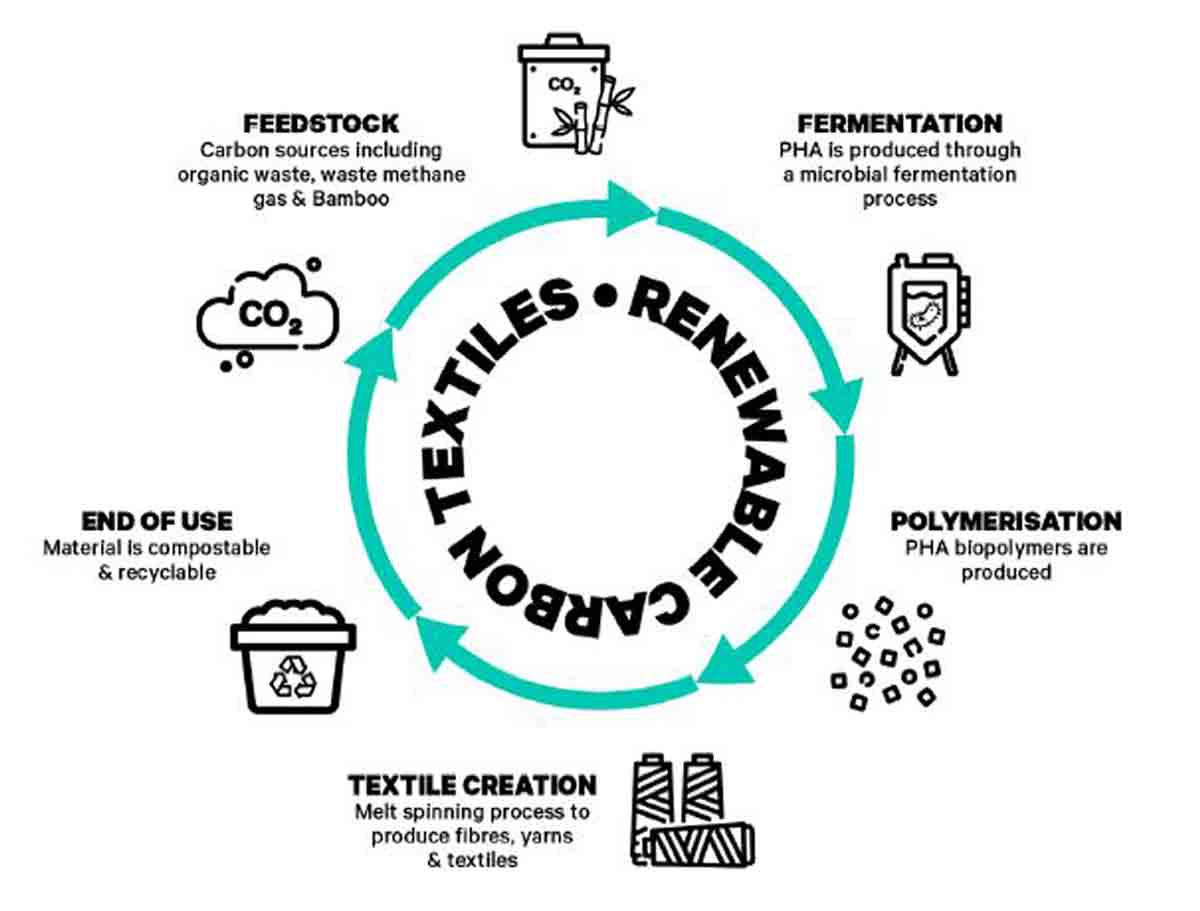
“It is important to consider the circular perspective as well as the end-of-use of plastic and polyester products so they don’t end up in landfills and the environment. The use of fibres such as PHA will ensure that textiles can be effectively composted when entering the ocean, freshwater or soil. And hopefully, PHA will prove successful in a circular economy as well.” – Camilla Skjønning Jørgensen, Sustainable Materials and Innovation Manager, BESTSELLER
PHAs are produced through a fermentation process using various renewable carbon-based feedstocks. Emphasis is placed on using feedstocks that do not directly compete with food and feed crops, diverting biological feedstocks from landfill and utilising waste gases in the production of its fibres. Full Cycle Bioplastics use inedible food waste whilst Newlight’s use of carbon capture technology transforms carbon from greenhouse gases into PHA biopolymers. Bio craft Innovation produces a blended PHA composite using biomass from bamboo production. Material for fibre production will be provided by each of these innovators and they will demonstrate that their product can meet industry requirements in both quality and quantity needed for scalable production.
“When scaling up new fibres we consider all parameters, from the feedstocks, process, technical feasibility as well as impact at end of use. This project brings together all these aspects testing the technical feasibility of these different innovators as well as the resultant fibres in different environments.” – Brad Boren, Director of Innovation and Sustainability, Norrøna Sport AS
NEXT STEPS
In the coming months, the innovators will begin developing their individual PHA formulations, which will be shipped to NIRI for melt spinning trials. Once the trials are complete, environmental degradation testing will commence. At project completion, aimed at the end of 2022 – barring impact from the on-going COVID-19 pandemic, the results from the project will be published by Fashion for Good in a report which will be available to the public.
“PHA is a promising class of polymers which have significant potential for use in textiles. This project provides an opportunity to contribute to the technical development of the fibre and is also a platform to explore possible future applications” – Brian Levy, Open Innovation, W. L. Gore & Associates
What are PHAs and how are they made?
PHAs belong to an emerging class of biobased, marine and soil compostable polymers. They are produced through a fermentation process using various carbon-based feedstocks, including organic food waste, methane gas and captured CO2. They have a wide range of chemical, thermal and mechanical properties and can be engineered to have similar performance characteristics as conventional synthetic fibres. PHA has been used to make films and packaging products but so far there have been limited fibre applications. Alongside this, only a handful of companies currently produce PHA meaning supply is limited.