With its established market leadership in spunlace nonwoven fabrics, which have applications in the personal care and medical industries, Ginni Filaments has also been a pioneer in the domestic and global markets for manufacture and promotion of consumer and institutional wipes. The Textile Magazine presents a profile
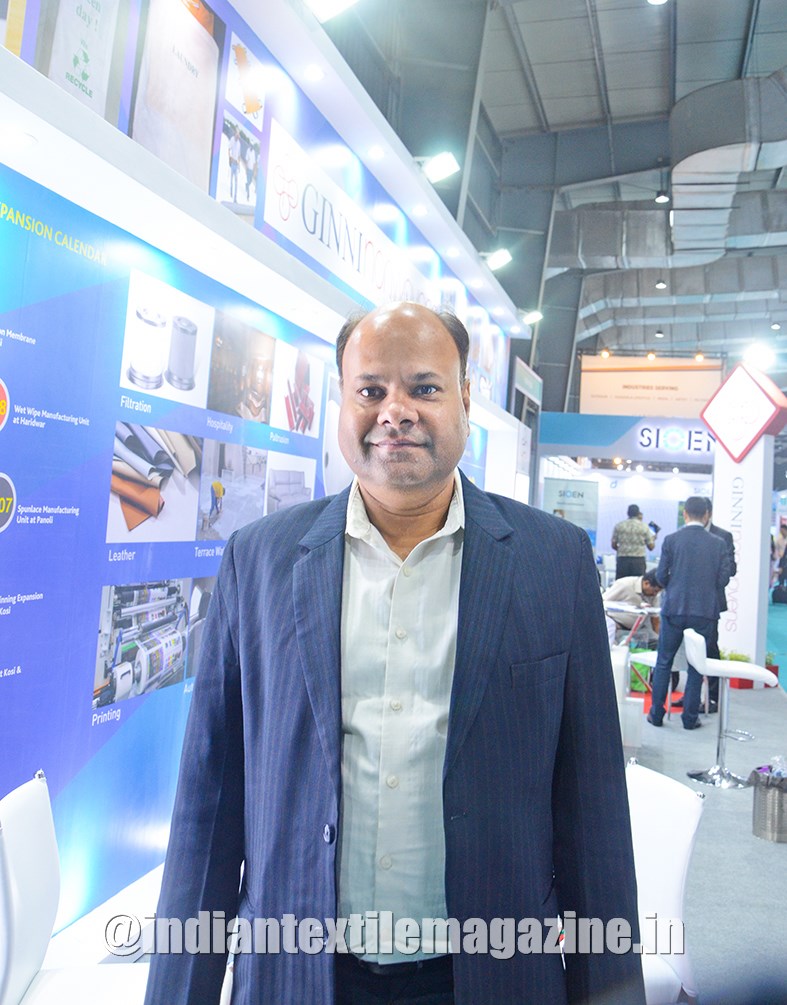
When it comes to nonwoven fabrics, Ginni Filaments Ltd. has been a force to reckon with. It was set up by Dr. Rajaram Jaipuria in 1990, born out of his vision to create a purely textile-based company that would operate specifically in the sectors of spinning, knitting and garments. The first plant was set up at Chatta in Uttar Pradesh to produce 100% combed cotton yarns. It was a 100% export-oriented unit with the capacity to operate more than 1 lakh spindles.
The company is now headed by Shishir Jaipuria, Chairman and Managing Director, who has 30+ years of experience in the textile industry. Identifying the changes in the Indian textile market way ahead of its peers, Ginni Filaments forayed into the nonwoven segment as a greenfield project in 2007-08. This plant is located at Panoli in Gujarat.
One of the unique features of its plant for nonwoven fabrics is that it employs state-of-the-art hydro-entanglement technology with a prime focus on sustainability. The company’s spunlace nonwoven fabric has a wide range of applications, especially in the hygiene sector, with manufacturers of wet tissues and baby wipes showing a strong preference for this product. “It is the quality and the cost that makes it popular. Along with India, we sell our spunlace nonwoven fabric in more than 25 countries, including the US, Europe, the Middle East, Korea and Japan,” informs Sudeep Agarwal, General Manager (Marketing), Ginni Filaments. What has also helped is the continuous development of the product over the years.
The Gujarat plant’s capacity is 12,000 metric tons per annum and it can produce a wide variety of roll goods. The technology and equipments have been provided by world’s leading nonwoven machinery supplier, Andritz Perfojet, France. “The quality produced in the plant is truly world-class with very wide acceptability and validation,” says Agarwal. The product range includes plain, aperture, embossed, coloured, printed, impregnated and chemical-treated spunlace roll goods. Strict hygienic conditions are maintained throughout the manufacturing process of spunlace for wet wipes, wound care and hygiene product applications. The products include viscose-polyester blends, 100% polyester, 100% viscose, and cotton-enriched blends.
Meanwhile, led by Senior Vice President Arun Nag, the company has now developed spunlace for other sectors such as healthcare, waterproofing, automobiles and leather as well as specific industrial applications. Spunlace nonwoven fabric is a vital component of many composites and Ginni Filaments has exploited its basic nature of being lightweight and chemically inert. Meanwhile, in its effort to create facilities for forward integration, the company has set up a conversion facility at Haridwar, which claims to have implemented the best manufacturing practices, at par with international players. The products made here include face masks, anti-bacterial kitchen towels, and various home and baby care products.
The company has also been a pioneer in using its expertise in nonwovens to make products for the medical sector. As for example, eye pads. They are absorbent cotton wrapped in absorbent nonwoven fabric. They are non-adherent to wound and ideal to protect the eyes during surgery, disease, or any injury. The softness of the nonwoven cover gives comfort during healing. It also makes swabs with 70% Isopropyl Alcohol as active ingredient that makes it antiseptic in nature. These are used for preparation of the skin prior to injection and as first aid to decrease germs in minor cuts, scrapes and burns. Yet another specialty product is laparotomy sponges that are absorbent pads used in surgical procedures. They are commonly used to absorb fluids around the surgical field. These sponges can also be used to distribute the pressure and stop bleeding.
Further, one of the key aspects of operations at Ginni Filaments has been sustainability. Informs Agarwal: “At all our plants, both water and waste management systems ensure that our processes are environmentally friendly. Our processes are designed for higher recovery, lower waste, lower energy, and lower water consumption. Our production process is able to operate with zero discharge of water and zero discharge of solid fabric waste while our power consumption may be a global benchmark for the industry.”
Presently exporting more than 75% of its products to various countries, Ginni Filaments supplies wet wipes converters to companies in the US and Europe, including Rockline Industries, Nice-Pak and Albaad. It also caters to the demand of reputed baby wipe brands like Johnson and Johnson, Reckitt Benckiser and Unicharm.