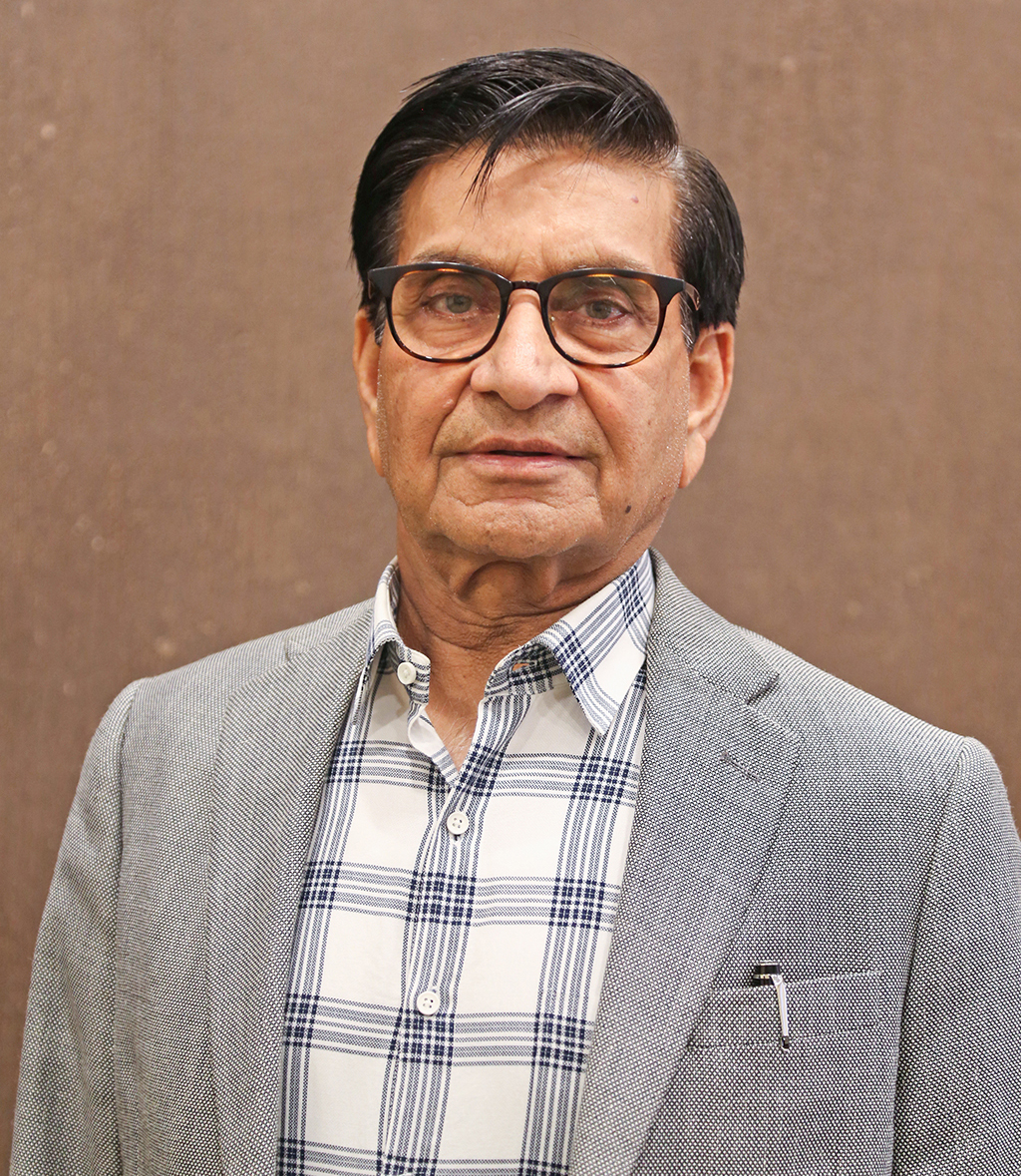
While producing high-quality jute and jute allied products, Gloster ensures optimum use of renewable resources, adopts various energy-efficiency related measures across their operations, and tries to maximise the application of recyclable products. It believes in true accountability, and always maintains a transparent disclosure to their stakeholder universe
Gloster Limited, is engaged in manufacturing and exporting of all types of jute and jute allied products. The manufacturing unit was originally set up in the year 1873. The House of Bangurs, one of the leading business conglomerates, acquired Gloster in the year 1954. Gloster has been endorsing sustainability since the time sustainability was just another term in environmental science. In fact, jute, Gloster and sustainability have become almost synonymous over the years. Gloster tries its best to sustain the resources of the society by opting for sustainable development.
While producing high-quality jute and jute allied products, Gloster ensures optimum use of renewable resources, adopts various energy-efficiency related measures across their operations, and tries to maximise the application of recyclable products. The journey for Gloster has not always been smooth, but in 1986 under the steadfast leadership of Dharam Chand Baheti the company was able to make a significant turnaround due to the rightful importance placed by him on modernizing, whilst subsequently bringing about a boost to the workers’ morale.
Gloster now employs 4,775 people across all its sites with an annual revenue of USD 67.28 million annually. Gloster, led by Hemant Bangur and Dharam Chand Baheti, has increased production capacity from 70 metric tonnes in the 1980s to 180 metric tonnes per day in 2021. Gloster has an impressive 88-92% utilisation rate, which is only matched by a few other companies.
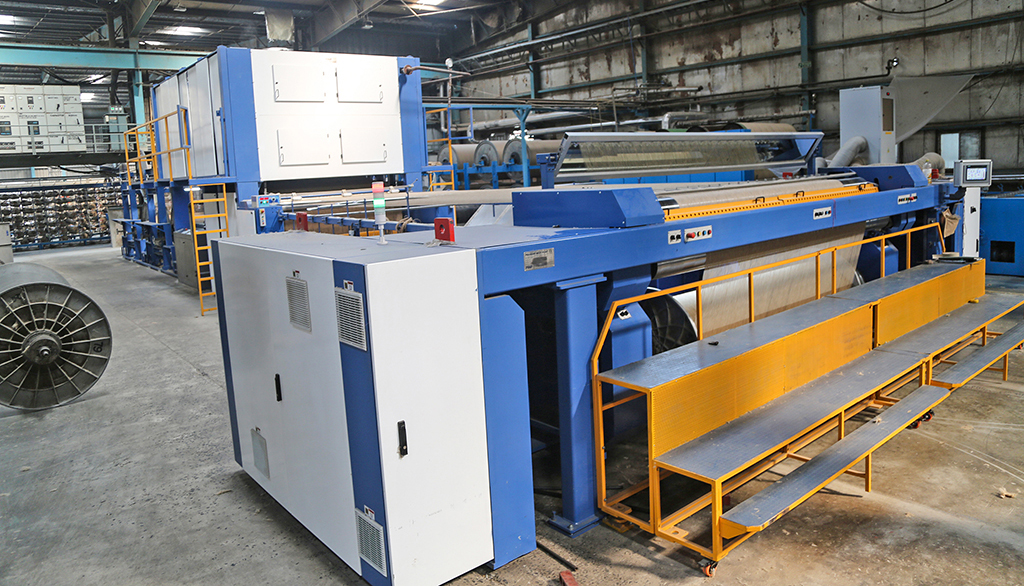
This impressive production efficiency, combined with their determination to provide only the highest quality, has attracted many foreign and domestic buyers, enabling them to now export to 43 countries. They primarily focus on the packaging industry, where they previously used to sell to local customers including the Government of India for food grain packing. But with the introduction of plastic into the market, several users switched to this cheaper substitute. Despite this, due to recent awareness about health and environmental concerns attributed to the use of plastic, farmers and others in the chain, primarily coffee, cocoa, potato and other food grains, have decided to return to jute.
This trend is not limited to farmers and even large multinational corporations (MNCs) have recognised the benefits of jute as well. In the early nineties, Nestle approached Gloster and others and asked if they could adhere to their strict manufacturing standards, which stated that Gloster should change to vegetable oil from its practise of using mineral oil as a lubricant in the manufacturing process. Baheti, former Chairman of the Indian Jute Industries Research Institute, along with the research and development team developed a method for substituting mineral oil for an organic alternative – rice bran oil. With this change and Gloster’s unique ability to provide all three types of jute (white, brown and golden), several European countries have increased their orders.
Wide Product Range
Gloster currently boast a diverse product range having three essential product classifications. Aside from their primary and still largest packing textiles, they also offer geo textiles, both woven and nonwoven, and other lifestyle products which despite being the youngest are one of the fastest growing ones as the recent green trend has pushed the demand for green eco-friendly bags. Their largest purchasers so far have been French, Swiss, German and Japanese companies which buy around 20-30 million bags a year. Presently, Gloster’s main buyer is the Government of India that purchases bags to store food grains while the remaining 50% of their sales are to international clients.
Employee and Technology-Oriented
Baheti had very early on identified the necessity for a skilled and satisfied workforce and hence on their 198-acre property, a majority of which is the main factory, they have allocated areas for a residential unit for workers, a fully functional market, two schools and a small clinic to tend to the needs of their employees, which has led to an all-round improvement of worker morale.
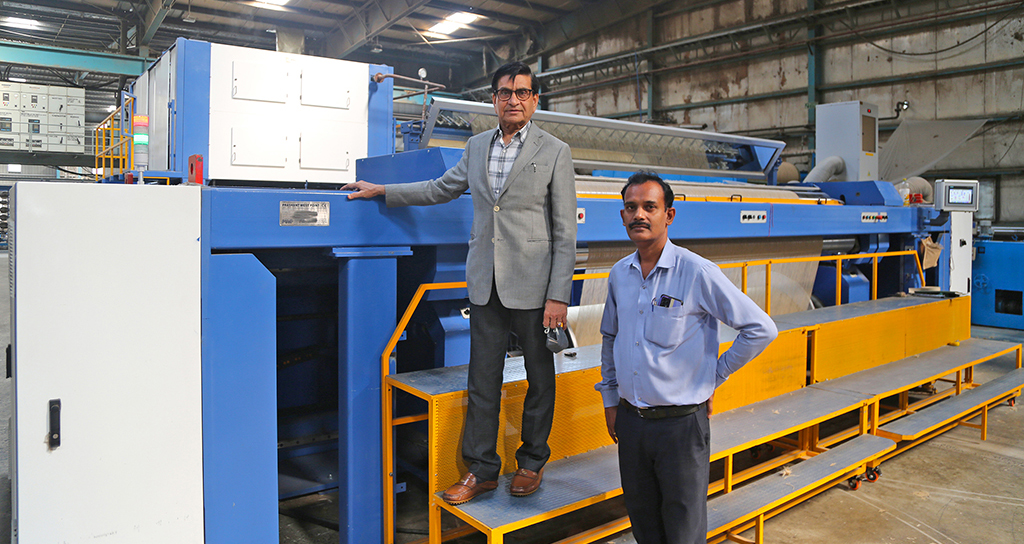
The present workers are given the opportunity to recommend their wards for the training programme, highlighting the importance of employee satisfaction. This innovative hands-on approach with workers has helped Gloster maintain a steady pool of skilled workers who have high morale and as a result are able to meet their production requirements efficiently.
A Productive Association
It was here that his tenure as the chairman of Indian Jute Industries Research Associates and Jute Products Development and Export Promotion Council (JPDEPC) provided him insights into the new technological innovations, many of which were available only abroad. For this reason, he started looking both domestically and internationally for new machines but couldn’t find a manufacturer who shared his vision. In 2018 he was suggested to approach Prashant West Point Gamatex and has never looked back since. Baheti found that Prashant West Point has superior technology in weaving preparatory solutions and so they decided to place an order for direct warper, and sizing and sacking warper machines for jute with them.
Baheti and his team are satisfied with the performance of the above machines, including after-sales services provided by Prashant West Point. Due to Prashant Westpoint’s sizing and warping machines, the productivity of Gloster has improved apart from improvement in quality of products. Gloster is also using material handling equipment from Prashant Ferber – a sister concern of Prashant WestPoint – and this has helped save labour costs. Baheti found Prashant WestPoint’s to be a leader in textile machines as they strived to provide the best goods and services while not compromising on the quality of the machines.
Prashant WestPoint is further going to play a crucial part in Gloster’s expansion plan as they plan to expand into South India and open a couple of more mills. With the help of their research and development department, new areas as well as alternate uses for their existing technology are constantly being explored. The partnership between Gloster and Prashant Group will help the jute industries to employ superior technology in the weaving preparatory department to produce better quality end-products that can be offered to the global jute market which is poised to grow exponentially in the coming years. The company has thus shown consistency about the quality of their products over the years, and their determination to ensure optimal consumer satisfaction is inspiring, to say the least. With their aim to create a sustainable business with a focus on quality and customer satisfaction, the sky’s only the limit for what Gloster jute could achieve in the coming years.
—
Gloster Limited is focused on technological innovation while being sensitive to environmental conservation. It is our strong belief that the recent collaboration with Prashant Gamatex will lead to both these criteria being satisfactorily fulfilled.
—
“We believe in upholding sustainability as well as our focus on improvement of human life with our innovative products, which is possible now more than ever with Prashant Gamatex as a trusted ally.
—
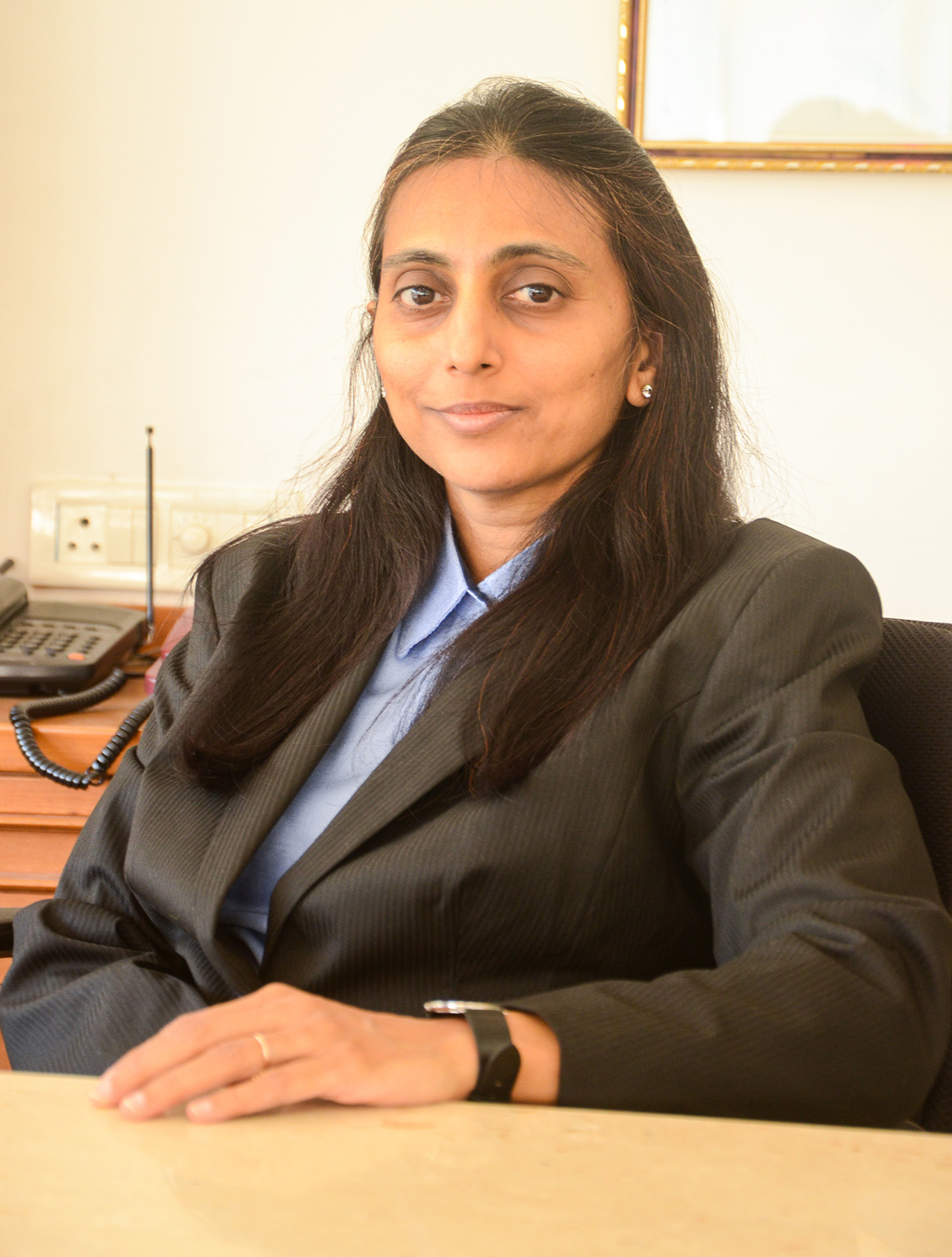
“Partnership between Gloster and Prashant Group will help Jute industries to employ superior technology in Weaving Preparatory department to produce better quality end products to be offered to the Global Jute market which is poised to grow exponentially in coming years.
– Amoli Shah, Prashant Group