Grasim Industries’ Viscose business recorded another year of exceptional performance contributed by viscose staple fibre (VSF) as well as viscose filament yarn (VFY). The company’s strong thrust on sustainability is demonstrated by the substantial investments committed towards the same.
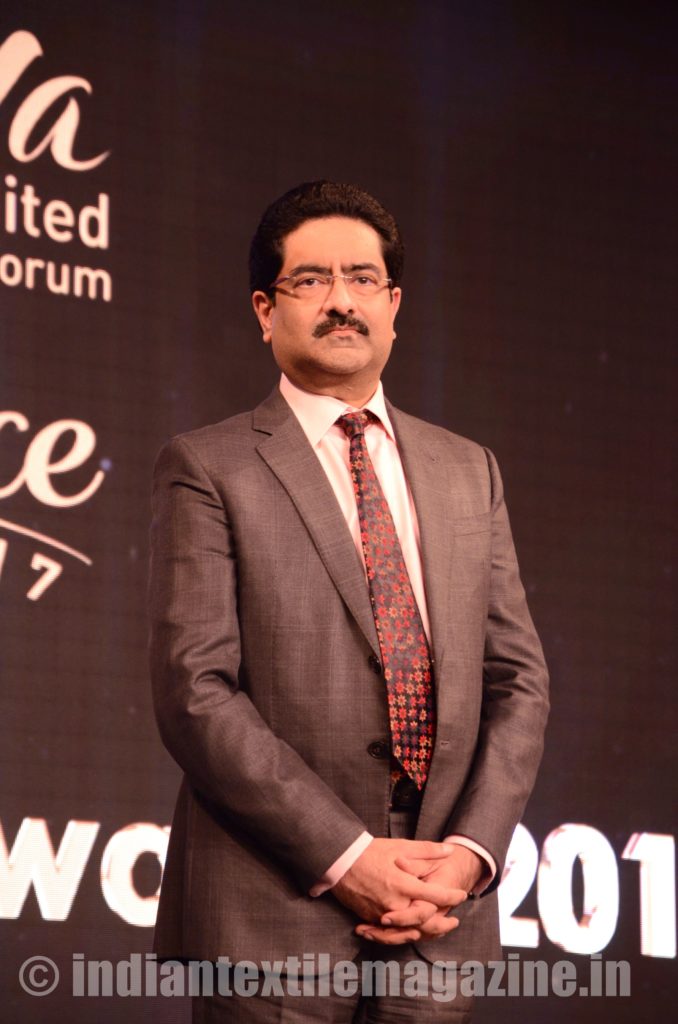
The tremendous success of the company brand LIVA can be attributed to Grasim’s relentless focus on customer centricity over the years. LIVA, predominantly a women’s apparel brand, has been extended to the home textile space-furnishing, bed linen and carpets. Liva Home offers the same brand promise. It’s a nature-based, high quality fabric from an accredited manufacturing value chain.
The launch of ‘Livaeco’ as an eco-enhanced variant of ‘Liva’, is a step towards giving further boost to its sustainability credentials, while retaining the fashion quotient of the brand.
The capacity expansion at the Vilayat plant is progressing well. Post expansion (FY21) it will be the single largest location plant of VSF in Asia (ex-China). The total VSF capacity will get enhanced to 788 KTPA from 566 KTPA. In FY19, Viscose net revenue grew by 23% YoY to Rs. 10,325 crores.
Production efficiency and improved customer experience are prime focus areas for innovations in VSF production facilities. One key initiative has been expanding the gradual implementation of technologies that reduce in-process material consumption. Process developments reducing the usage of energy and water are also reducing costs, while enhancing sustainability.
Grasim’s work to improve its customers’ experience includes specific technologies to improve non-woven spunlacing process performance, dope-dyed fibre uniformity leading to higher efficiency yarn spinning and quality, and improved spinning performance for greige fibres. In addition, the company’s higher effort for differentiated products has resulted in several new offerings at different stages of commercialisation.
Liva Sno, a fibre with high whiteness, is now produced in regular campaigns for applications like uniforms, melange and patterned fabrics. This provides an environmentally friendly alternative to customers’ existing downstream processes for producing yarns and fabrics with high whiteness. Livaeco, a fibre recently launched with molecular tagging, provides supply-chain traceability for its branded products that incorporate special sustainability attributes.
The differentiated products pipeline continues to progress with three additional value-added products from its pilot plant, having gone through customer acceptance tests. These will be scaled up to commercial production and sales in the coming year.
Overall the fibre quality continues to improve with the objective of bringing fibre lines to the global benchmark quality levels by adopting the “Product by Process” approach using Six Sigma principles. During FY19, continued upgrades to its production lines has resulted in 78% of capacity now being mechanically capable of producing benchmark quality.
The company is now aggressively addressing a key quality challenge, the growing vortex (MVS) type yarn-spinning demand, which requires especially low fibre imperfection levels. MVS Grade production has been increased from 64% in FY17 to 82% this year, and the goal is to achieve 90% in FY20. As a result of these efforts, customer complaints have been reduced.
The Quality Initiative focus for the coming year will be improving the process stability and product quality of non-benchmark production lines through innovative solutions requiring little new capital.
Grasim’s journey in the Excel® project reached a critical milestone with the commissioning of the new 45 TPD plant based on the environment-friendly solvent spinning technology developed in-house. The new technology offers a higher performance product with improved sustainability as a key growth alternative for its business.
The new plant has set the platform for rapid “take-off” of its technology in the coming years. The Textile Research and Application Development Centre (TRADC) continues to be a significant contributor to ensure global leadership through development of innovative applications, such as the Men’s range, Home Textiles and the Warp knit range which were considered as challenges for VSF.
In collaboration with internal and external customers, TRADC brings contemporary, innovative and cost-effective solutions for the global fashion industry through continuous improvement in quality by process development, with an eye on sustainability. Recently a brand has selected its dope-dyed fibres for blending with polyester for Sportswear. Similarly, Modal and Excel are finding application in the place of 100% cotton in sarees and dhoti.
Pulp business
Grasim Industries Pulp R&D and Technology teams have focused their efforts on increasing capacity, improving quality and opening new specialty markets. The Domsjo plant, a joint venture, is working on increasing the pulp capacity by addressing the bottleneck in evaporation through improved efficiencies and reduced process flows. The plant is also improving the pulp quality through stabilising wood chip uniformity, improved bleaching to reduce viscosity variations, and standardised mill operating strategies. These improvements have also supported increasing its pulp specialty products growth with the introduction of new customers in filament yarn and casing applications.
In addition, the new pulp quality brand Ultra is now fully accepted by a cellulose acetate customer.
Across Pulp JV plants, advanced process control systems in the digester and bleaching areas have been developed to enhance consistency, and the system is being stabilised.
A digitization initiative aimed at seamlessly connecting pulp plant processes with the consuming fibre plants is in progress. The first technology platform to allow sharing real-time pulp quality and dispatch data with the Fibre sites has been piloted successfully. This helps to improve fibre spinning consistency. Full-scale implementation plans are being developed.
A new pulp blending methodology has led to improved pulp ratio control and viscose spinning solution consistency. These systems enable further improvements through the development of models for predictive control.
Enabling capabilities
A multi-disciplinary team is responsible for the innovation agenda of the Pulp and Fibre business. Starting with early tests of concepts in laboratory, a screening process leads to short-listing. The selected concepts are then taken through iterative processes of developments and testings, and then through scale-up in fibre pilot plants. The fibres are taken through customer processes of yarn, fabric and garment making. In-house, external and customer-facilities are all engaged for effective delivery in minimum time. Successful products are then transferred to plants for commercial implementation, and placed in the market.
Kumar Mangalam Birla chosen Century Textiles Chairman
Mr. Kumar Mangalam Birla was elected Chairman of Century Textiles and Industries at the Board meeting held recently.
He joined the Board of Century Textiles in 2006 and became its Vice-Chairman in 2015.
After his election, he said: “It is an honour for me to chair a company that was so ably led by my legendary grandfather. His exemplary standards of ethics and his values will serve as an inspiration to us as we carry forward his legacy.”
Rajashree Birla elected Chairperson of Century Enka
The Board of Century Enka has elected Ms. Rajashree Birla as its Chairperson. Earlier, she was the Vice Chairperson.
On the occasion, she observed: “I am indeed honoured and privileged to be named Chairperson of a company that has been led by an iconic leader like Mr. B. K. Birla. He has been a guide and a mentor for me, and I look forward to carrying forth his legacy and help create value for all stakeholders.”