The long-term goal of the Paris climate agreement is to limit global warming to well below 2°C compared to the pre-industrial age, including efforts to limit global warming to 1.5°C. The essential measure to achieve this goal is to reduce CO2 emissions worldwide. This increases the pressure on energy-intensive industries.
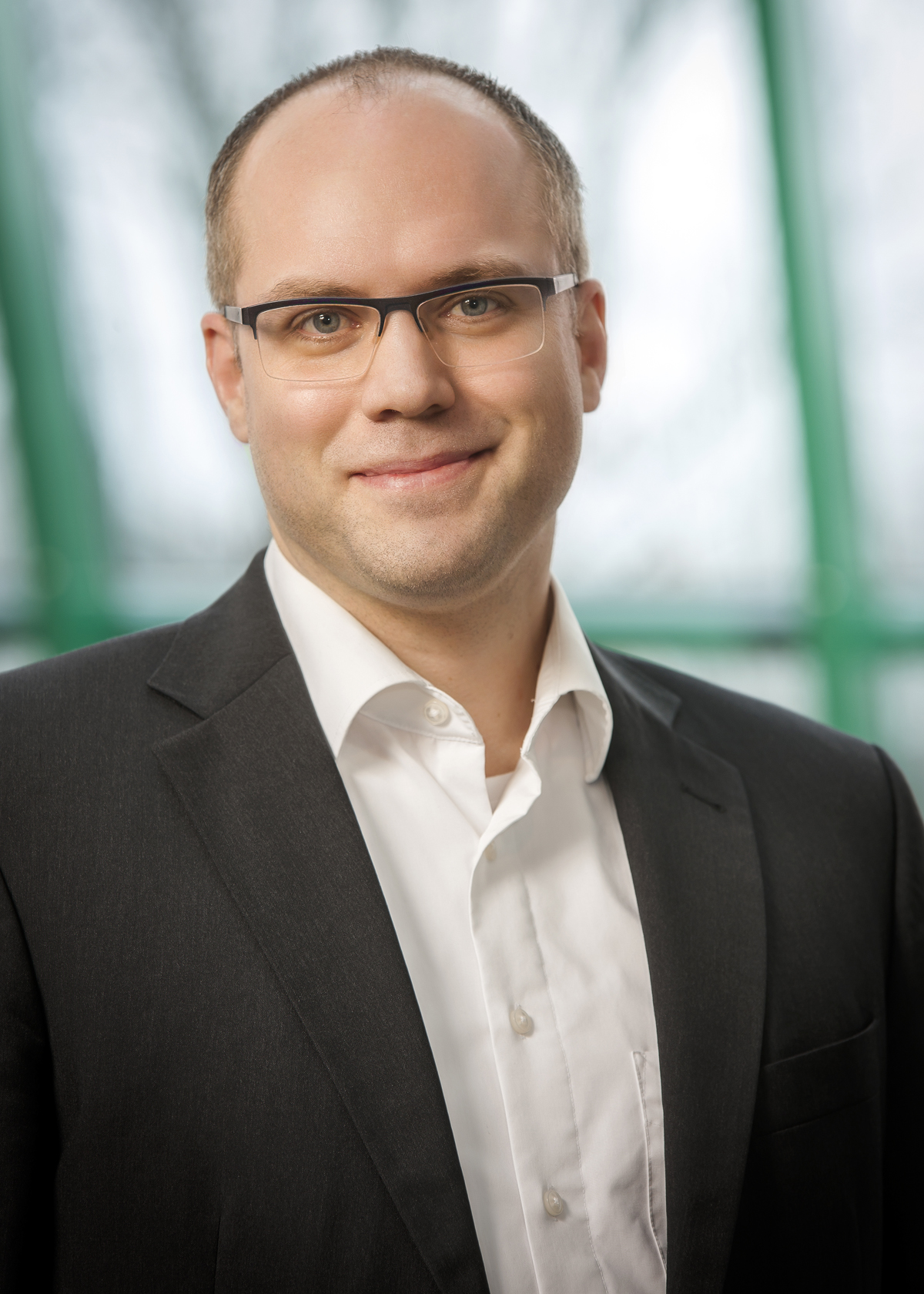
Textile finishing is by nature very energy-intensive and therefore cost-intensive. Stenter frames are operated at temperatures of up to 200°C, depending on the finishing process and fabric type. To achieve the high temperatures inside the stenter frame large amounts of fossil fuels are necessary. This has a negative effect on the carbon footprint and the LCA of the production. Concrete figures illustrate this: With the parameters of the client case study described below, 2,603 tons of CO2 are emitted annually. The energy costs for the stenter frames only are 520,598 € (0.04 €/kWh gas).
As the textiles pass through the stenter frames, it produces large quantities of highly contaminated and hot exhaust air. Often this is indicated by an unpopular plume of smoke over the chimneys. Strict legal requirements therefore make the use of exhaust air purification systems indispensable. In addition to air pollutants, valuable process waste heat is also emitted via the exhaust air stream. Conventional exhaust air purification systems clean the exhaust air, but destroy this valuable waste heat in the same process. A combination of electrostatic precipitators for exhaust air purification and heat exchangers for heat recovery solves precisely this challenge: The smoke plume disappears reliably and the waste heat is recovered. The thermal energy in it can be reused for production in the form of heated air or heated water. There are many possibilities here: For example, the energy can be fed back into the stenter frame. The energy can also be used to heat washing water, water for the dyeing works or the hall in the winter months. A combination is also possible.
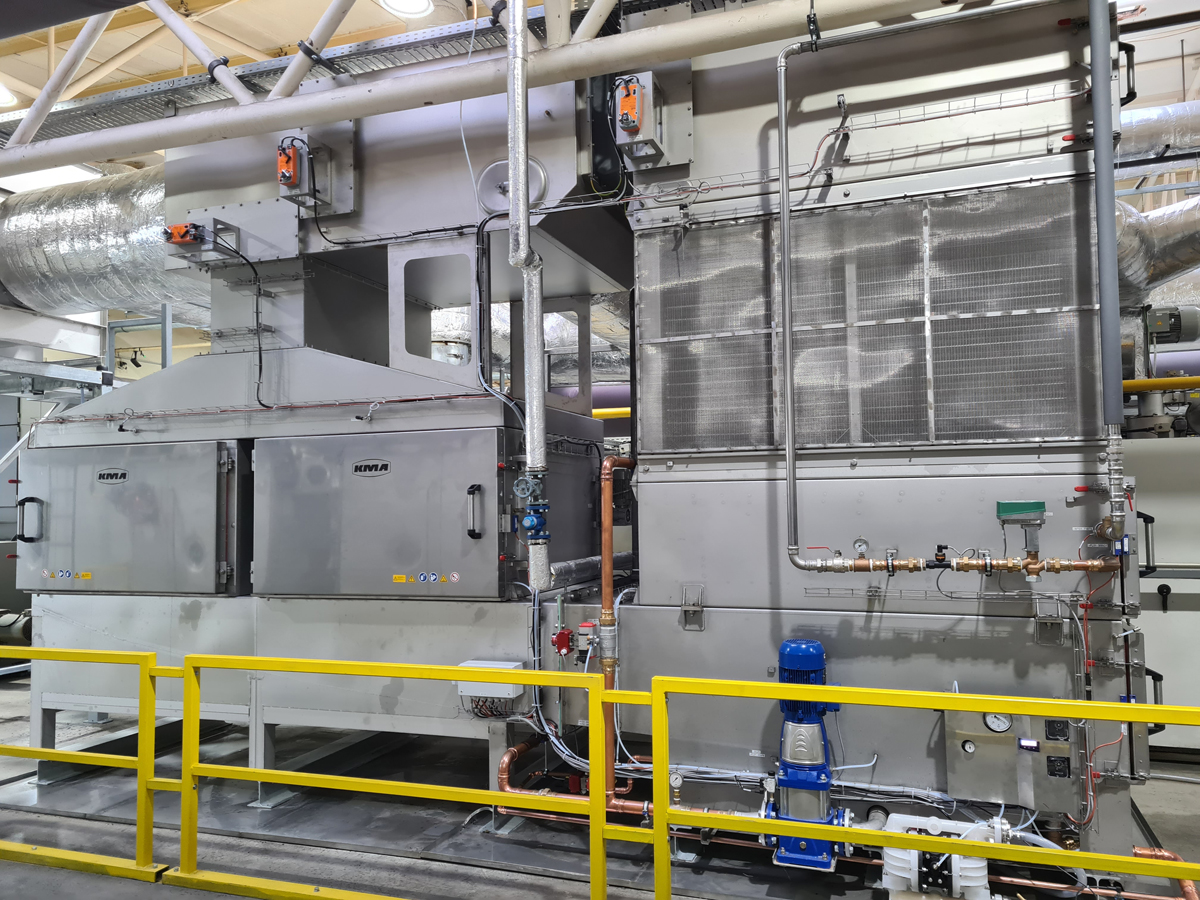
This unique energy yield reduces the energy costs of production immensely. Therefore, operating costs are increasingly included in the overall consideration of the investment decision. In view of additional CO2 levies due to emissions trading, reducing energy consumption will encourage more and more companies to rethink.
Best practice shows: ecology and economy not a contradiction
The textile company AUNDE Achter & Ebels GmbH has installed a heat recovery system with integrated exhaust air filter system from KMA Umwelttechnik GmbH at its German site in Mönchengladbach to utilize the waste heat from the stenter frames. The conditions for heat recovery were ideal, as 100 per cent of the recovered energy can be directly reused in-process at the same place and at the same time.
The two stenter frames at AUNDE have a combined exhaust air volume of 24,500 m³/h on average with an average exhaust air temperature of approx. 140°C. A common heat recovery system was installed for both stenter frames, primarily to heat the water for two upstream washing machines. The heat exchanger used for this purpose, based on the air-water principle, heats the water with an input temperature of 16°C to an output temperature of 72°C.
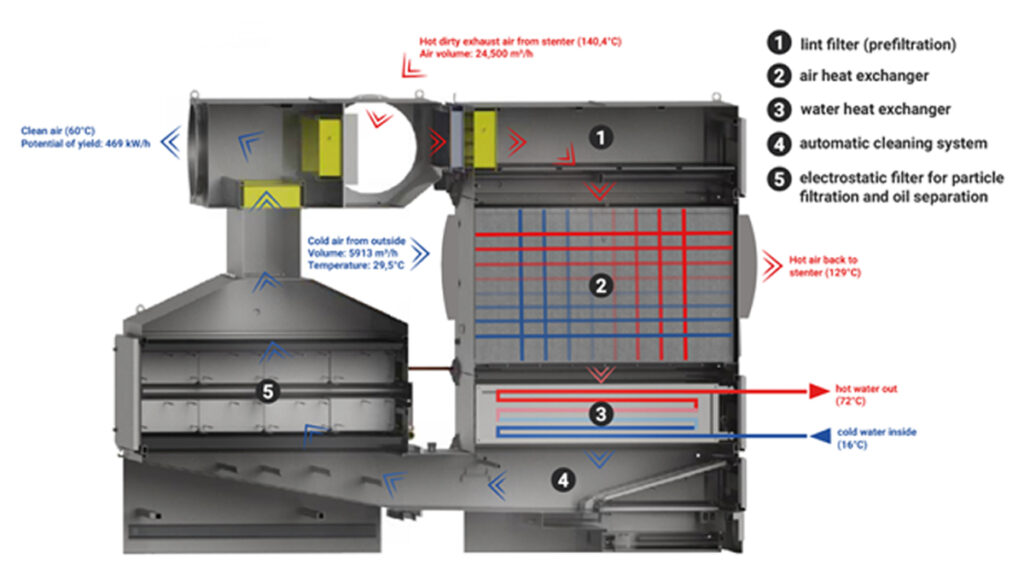
In parallel, approx. 10 to 20 per cent of the energy goes back into the stenter frame as heated fresh air. The heat exchanger based on the air-air principle ensures that ambient air is heated from 29.5°C to 129°C. The energy consumption for the KMA system is only 150,000 kWh per year.
The textile company recovers 469 kW of energy per hour through this system. Normally, 276 kW of the recovered energy heats 8.5 m³/h of water – without supplying electricity or gas. With the help of the remaining energy, air is preheated and added to the stenter frame, which also reduces gas consumption here. Annually, the company saves 2,345,000 kWh of energy. This is equivalent to an annual cost saving of 93,800 € (0.04 €/kWh gas). This means that the system pays for itself within a very short time. But a look at the CO2 footprint is even clearer: the heat recovery system reduces the company’s annual CO2 emissions by around 469 tons.
In addition, with the KMA system, AUNDE cleans the stenter exhaust air with the help of powerful and energy-efficient electrostatic precipitators. A strong electric field is built up by ionizing the air with the aid of many electrodes arranged in the air flow. Due to the resulting charge difference, fine particles and aerosols in the exhaust air stream are retained on metal plates in the subsequently arranged collector zone and thus removed from the air stream. All this is done with a very low energy input, because the power consumption of the electrostatic precipitator cells is in the range of less than 1.25 kW. The liquid part of the filtered substances drips off the collector plates and is collected in a depot tank. The second type forms a greasy, oily or encrusted deposit on the filter surface. This means that, in addition to less CO2, significantly fewer air pollutants and process oil are released into the environment.
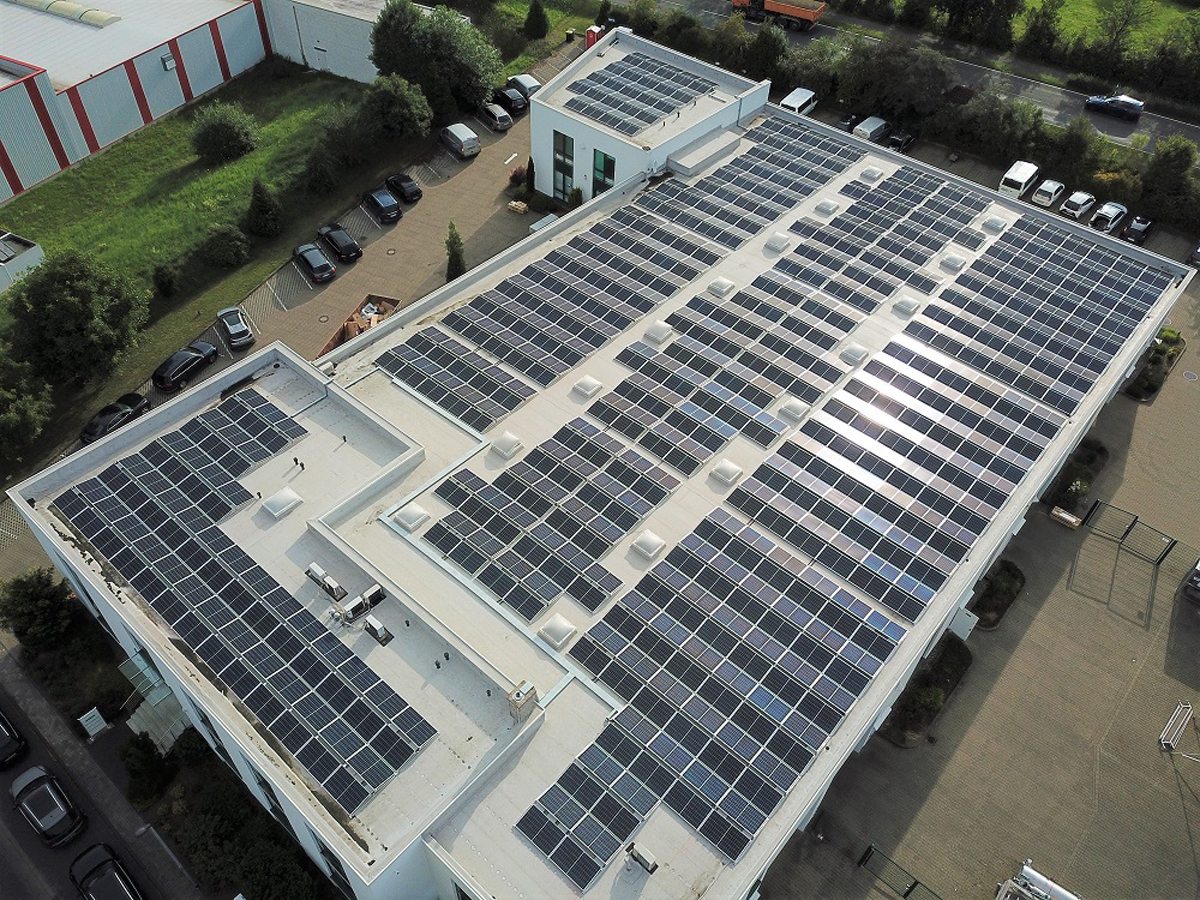
To ensure that the high efficiency of the heat recovery and exhaust air purification is permanently maintained, the system has an integrated cleaning in place (CIP) system with which the surfaces of the heat exchangers and the electrostatic precipitators are regularly cleaned without affecting production. An online cleaning of the heat exchangers takes place every 60 minutes during operation. In case of batch change or other production stop, a more extensive cleaning of all modules is carried out.
Conclusion
The example of AUNDE shows that leading companies in the textile finishing industry are already committed to taking measures to help reduce CO2 emissions. The ULTRAVENT® system developed by KMA Umwelttechnik combines all the components for exhaust air purification and heat recovery, thus not only protecting the environment but also reducing companies’ operating costs.