The Hirdaramani Group together with the Ellen MacArthur Foundation’s Make Fashion Circular initiative hosted a transformative workshop, specifically designed for academics and students in the fashion industry to raise awareness, build knowledge, and stimulate dialogue within the context of a circular economy – one that designs out waste and pollution, keeps products and materials in use and regenerates natural systems.
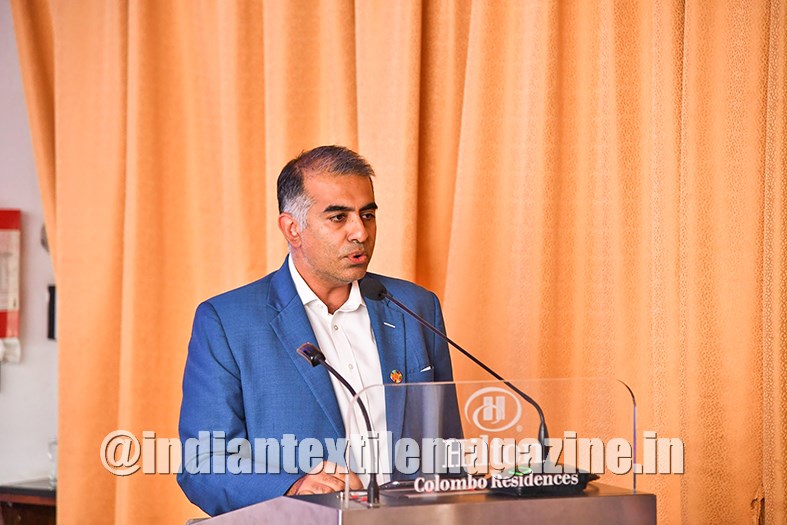
The circularity workshop enabled students from the Academy of Design and the University of Moratuwa to gain precious insight from visiting delegates from the Ellen MacArthur Foundation, as well as leaders from the Hirdaramani Group.
Among the group of representatives from the foundation were Francois Souchet, Lead of Make Fashion Circular, Project Managers Francesca Brkic and Elodie Rousselot, Senior Research Analyst Marilyn Martinez, and Research Analyst Lukas Fuchs. Informative presentations from both organisations were followed by an illuminating panel discussion and Q&A session.
Commenting at the event, Francois Souchet said: “We were delighted to be hosted by Make Fashion Circular participant Hirdaramani at their facilities in Sri Lanka this week. Hirdaramani played a key role in the making of the Jeans Redesign project and this visit proves a great opportunity to see how they are using technology in their manufacturing processes to realise the ambitions of the Jeans Redesign guidelines.”
“We are delighted to welcome the team from the Ellen MacArthur Foundation’s Make Fashion Circular initiative to Sri Lanka. We are extremely optimistic that our participation in initiatives like the Jeans Re-design project will positively impact all industry stakeholders in joining our journey towards a circular economy,” added Nikhil Hirdaramani, Group Director of the Hirdaramani Group.
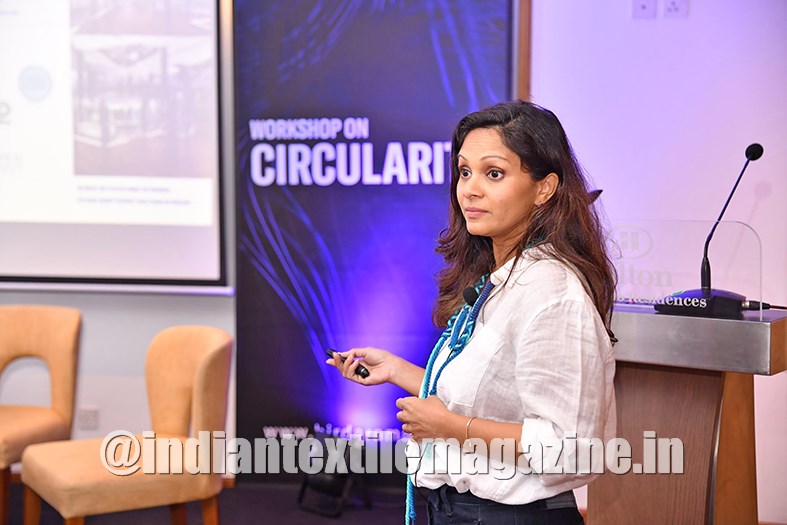
Earlier this year the future-focused apparel conglomerate further cemented its long-standing commitment towards the circular economy by becoming one of few manufacturers globally to participate in the Ellen MacArthur Foundation’s Make Fashion Circular initiative, and pledging to incorporate innovative operational solutions that challenge the current ‘take-make-waste’ industry model. Launched in 2017 at the Copenhagen Fashion Summit, the initiative aims to accelerate the level of collaboration and innovation necessary to create a textiles economy fit for the 21st century; one that is aligned with the principles of a circular economy. Its ambition is to ensure clothes are made from safe and renewable materials, new business models increase clothing use and old clothes are turned into new, thus unlocking enormous economic opportunity.
Already a pioneer in the industry, through its collaboration with the Ellen MacArthur Foundation, the Hirdaramani Group joins an A-list of global industry stakeholders, corporations, NGOs and fashion houses – Burberry, NIKE Inc., PVH and Stella McCartney, to name a few – who have pledged to incorporate circularity into the core of their business.
The fashion industry is the second largest polluter in the world, just after the oil industry. The Hirdaramani Group is conscious in particular of its position as one of the largest global manufacturers of jeans, and in this view the group has signed up as one of only 16 global drivers of the Ellen MacArthur Foundation’s Make Fashion Circular Jeans Redesign project. Launched at Première Vision in New York in July 2019, the Jeans Redesign Guidelines set out minimum requirements on garment durability, material health, recyclability, and traceability. Based on the principles of the circular economy, the guidelines will work to ensure jeans last longer, can easily be recycled, and are made in a way that is better for the environment and the health of garment workers.
Hirdaramani has made considerable advancements in the sustainable manufacturing space. In its washing plants the company has drastically reduced water usage by employing low liquor ratio washing machines and waterless washing through ozone technology. Chemical usage is optimized using state-of-the-art machinery. Furthermore, dry processes have been substituted with laser finishing, and 60% of output water is recycled. The company also places great significance in utilizing only Green Screen Chemicals in the manufacturing process, and meeting ZDHC standards. Across the group there is a strong focus on reducing waste to landfills and currently waste reduction is at 70%.
Hirdaramani Group is also approaching the issue at the design stage by taking into consideration the entire lifecycle of the garment, with a focus on eliminating 80% of waste and incorporating process efficiency at this stage. They are also focused on developing new fabrics and technologies working in collaboration with partners and customers.
In addition to the workshop, the delegates from the Ellen MacArthur Foundation were given a two-day tour of the Hirdaramani washing plant at Seethawaka, as well as the manufacturing facilities Hirdaramani Knit Mihila and Hirdaramani Industries Kahathuduwa. More than just a knowledge sharing exercise, the visits also served as an opportunity to showcase the Hirdaramani Group’s incorporation of sustainable manufacturing practices from the design stage upwards.
By prioritizing sustainability in its business model, the Hirdaramani Group has set an industry benchmark, encouraging all apparel manufacturers across Sri Lanka to invest in restorative and regenerative processes in creating sustainable products for the betterment of their own practices, the country, and the environment.
The 100-year-old start up
From tailors to the sailors of the early 20th century to a multi-national apparel industry leader. Here’s how the Hirdaramani Group evolved, flourished and stayed competitive through the years.
Beginning as a single retail store in the heart of Colombo’s commercial district, the Hirdaramani Group began as a small tailoring company in the late 1800’s. At just 16, Parmanand Hirdaramani set up the first Hirdaramani retail store in Fort, Colombo. He made a name for himself in the early 1900s by introducing the concept of same-day tailoring to the passengers of cruise liners that docked at the Colombo Harbour. And so, the innovative Hirdaramani spirit took flight.
The company soon evolved into a growing merchant of garments, textiles, carpets and jewellery – opening retail stores in Colombo and Kandy in the mid 1940s.
It was in the early 1970s when Hirdaramani broke into the international export market with the creation of Ceylon Knit Trend Ltd. As globalisation of the fashion industry rapidly increased Hirdaramani expanded with the demand, building facilities throughout Sri Lanka and opening ventures in Bangladesh, Vietnam and in recent years Ethiopia.
In an ever competitive industry, Hirdaramani and its Directors attribute the company’s continued success to upholding sustainable and ethical business practices from the very beginning. Caring for their employees and the environment, Hirdaramani’s philosophy is that doing the right thing is simply good for business.
Hirdaramani Woven unit achieves LEED Platinum status
Hirdaramani Woven Puthukudiyruppu was awarded the LEED Platinum certification established by the US Green Building Council and verified by the Green Building Certification Institute (GBCI). The Hirdaramani Woven Puthukudiyruppu facility now joins Hirdaramani Woven Kahathuduwa as the highest LEED point scoring projects in Sri Lanka in the Industrial Manufacturing category, making Hirdaramani an industry leader. Hirdaramani continues to lead the way in sustainable manufacturing in Sri Lanka with 06 LEED certified facilities across the island.
LEED, or Leadership in Energy & Environmental Design, is a green building certification program that recognises best-in-class building strategies and practices. To receive LEED certification, building projects have to satisfy prerequisites and earn points to achieve different levels of certification.
Commenting on this significant achievement, Akshay Hirdaramani, Director, Hirdaramani Group, said: “We are very proud of this accomplishment by the team at Woven Puthukudiyruppu and how fast this factory has progressed in a short period of time. The LEED certification was achieved with minimal incremental investment thanks to the optimized design of the factory’s ventilation and lighting system. Once again, this demonstrates that investing into a good design at the outset pays rich dividends in the end.”
The Hirdaramani Woven Puthukudiyruppu facility scores high on sustainable use of resources. It achieves a high rate for water efficiency, substantial reduction in energy use, use of recycled materials in its construction, good indoor air quality and as a result, achieved operational efficiency and reduced its carbon footprint.