While the government is doing its best to support the textile industry in India to face the challenges, the players themselves need to pump up the investment to become technologically superior in order to establish a stronger footprint in the global arena
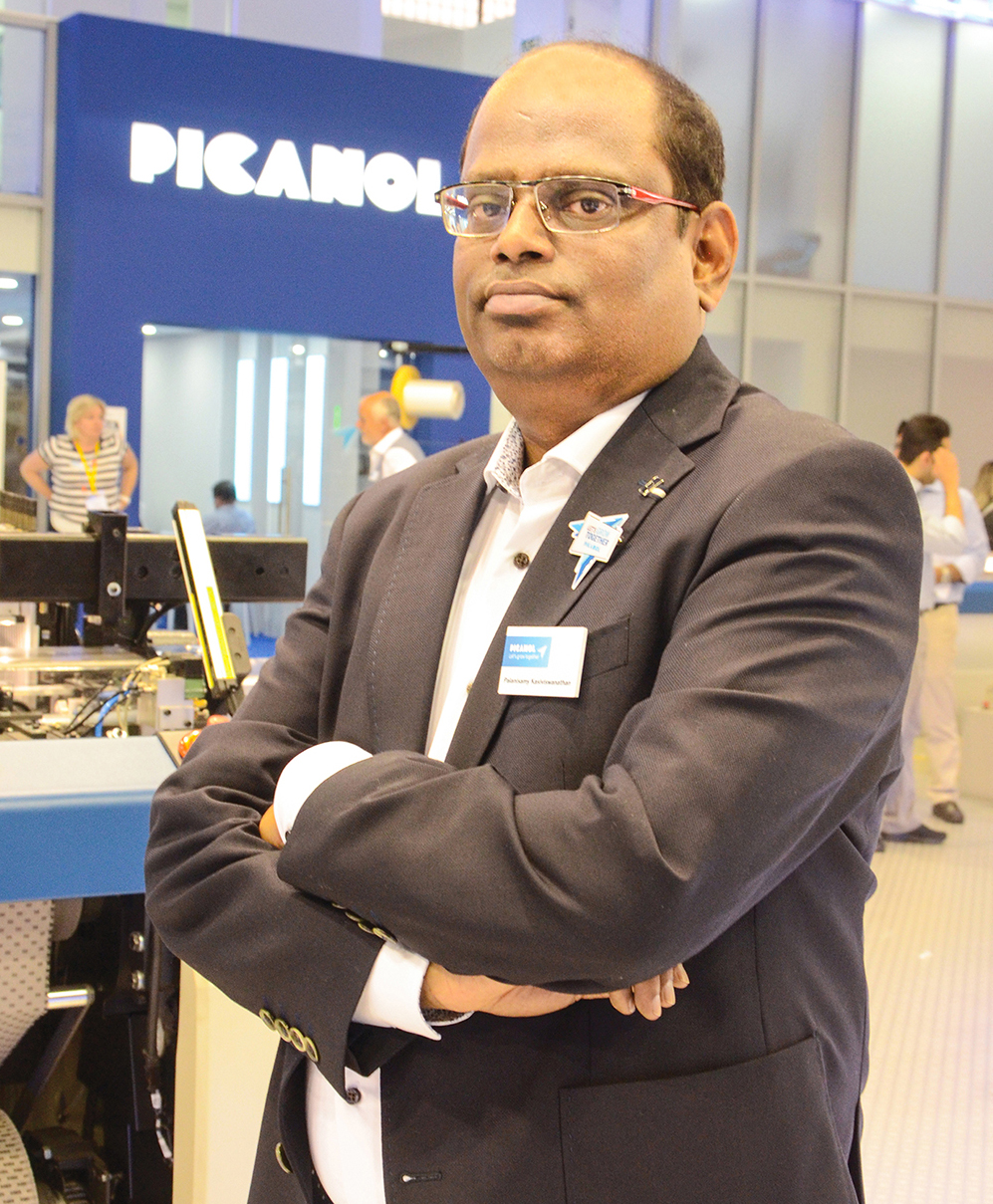
The textile and apparel industry is one of the earliest industries to have developed in India. Its inherent and unique strength is its incomparable employment potential owing to the presence of the entire value chain from fibre to apparel manufacturing within the country. The latest economic survey indicates that the textile and apparel industry contributed 2% of the overall GDP and 11% of total manufacturing gross value added in FY20. It is the biggest employer after agriculture and provides direct employment to 4.5 crore people and another 6 crore in allied sectors. India is the second-largest manufacturer of textiles and clothing in the world.
India is also the second-largest exporter of textiles and apparel with a share of 5% of global trade. Exports of textile and clothing products, including handicrafts, from India have slightly increased to USD 40.4 billion during the year 2018–19 from USD 39.2 billion during 2017–18, registering a growth of 3%. However, India’s global share is way behind that of China, which has approximately 38% of the global textile and clothing trade. The share of textile and clothing in India’s total exports stood at 12% in 2018–19. With 48% total textile and apparel export, EU-28 and the United States are India’s major textile and apparel export destinations.
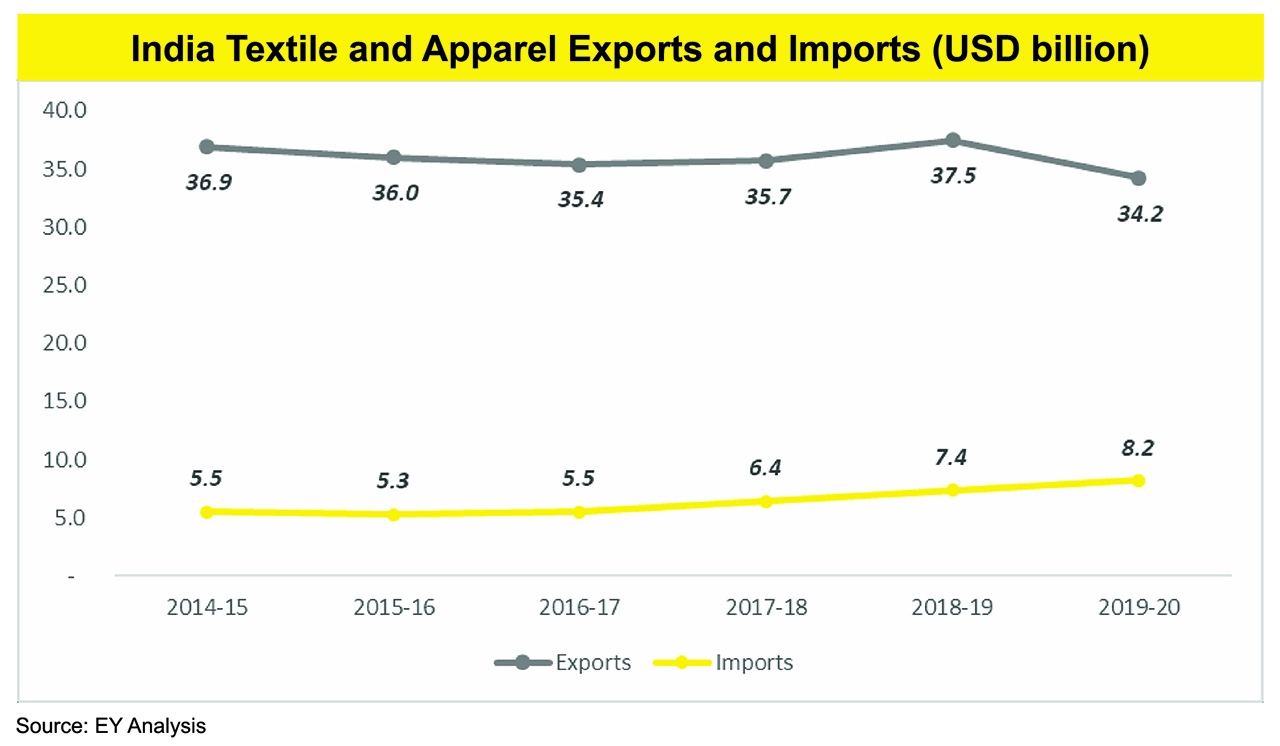
Overview of Textile Value Chain
While India has the advantage of the entire value chain in the industry, currently the value chain is uncompetitive. The figure below indicates the current status of textile value chain (GVC) in India.
India has a very strong raw material base both in natural and manmade fibres (MMFs). The country has emerged as the largest producer of cotton in the world with a production of 370 lakh bales in 2017–18 and the second-largest exporter of cotton. However, high contamination level and poor quality of fibre, both in fineness and length, are major concerns that need focused attention. India has a strong presence in global exports of cotton yarn. But India needs to upgrade its position from a supplier of cotton yarn to a producer of value-added fabrics and garments. As the world export value of cotton yarn has decreased over the years, it is an indication that the cotton textile trade is shifting towards different types of fibre such as MMF.
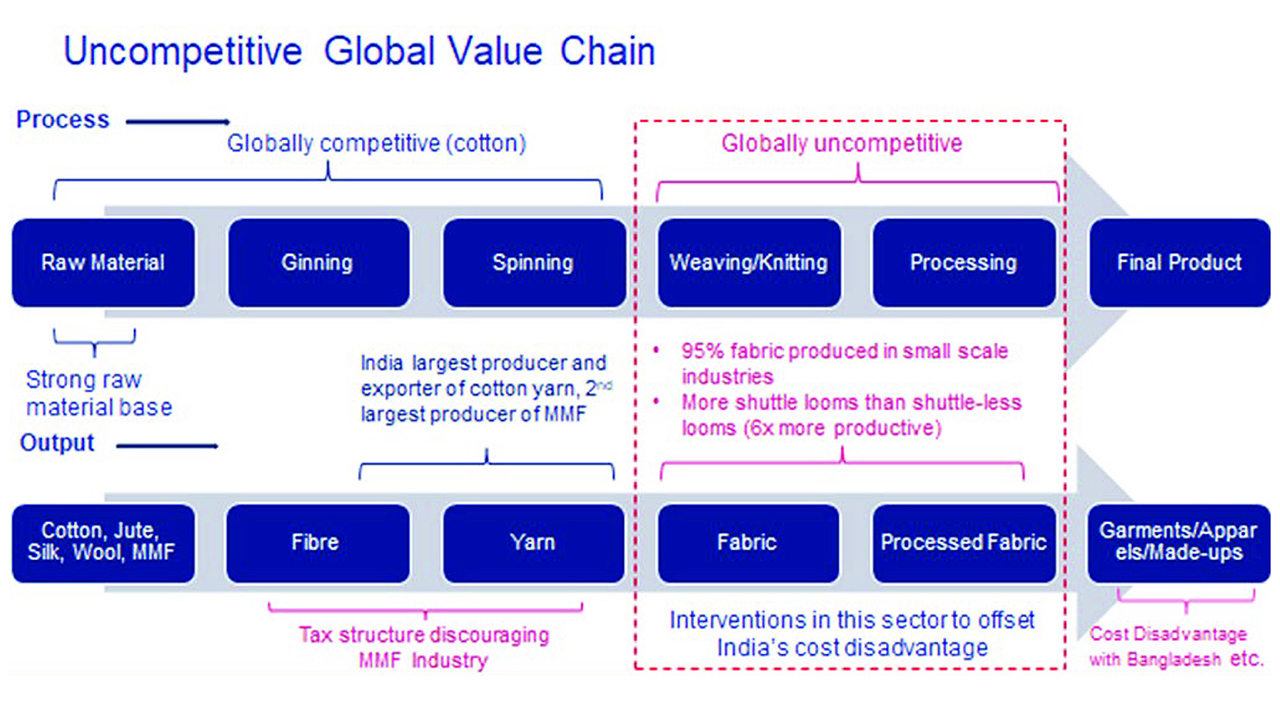
While India leads in cotton yarn exports, it has been a very marginal player when it comes to cotton fabric in world exports. China has a substantial share of 69% in cotton fabrics when compared to India’s 9%; the situation is almost the same in case of MMF fabrics. This comparison suggests that India is not able to scale up the value chain significantly enough to meet the global demand despite being the largest producer and exporter of cotton yarn. In India, out of around 25 lakh looms’ weaving capacity, the share of shuttle-less looms is about 4%. This indicates a low degree of modernisation in the Indian weaving industry. Power looms contribute 60% of total cloth production in the country. According to NITI Aayog, India currently has 23.7 lakhs shuttle looms as compared to 6.5 lakhs in China. However, in China, there are 6.3 lakhs shuttle-less looms compared to 1.2 to 1.4 lakhs in India. This indicates the huge productivity gap India must bridge to become competitive in the global markets.
India has one of the largest installed production bases in the world in the weaving sector but at the same time it uses old technology with low productivity and quality levels. In terms of technology adoption in the weaving sector, India has only 2% share in global shuttle-less looms (i.e. modern looms) installed capacity. The cost of production in India also goes up due to poor technology levels and low scale of operations as 95% of the weaving sector in India is unorganised and in the small scale sector. India also lacks the presence of large fabric manufacturers when compared to China and the US.
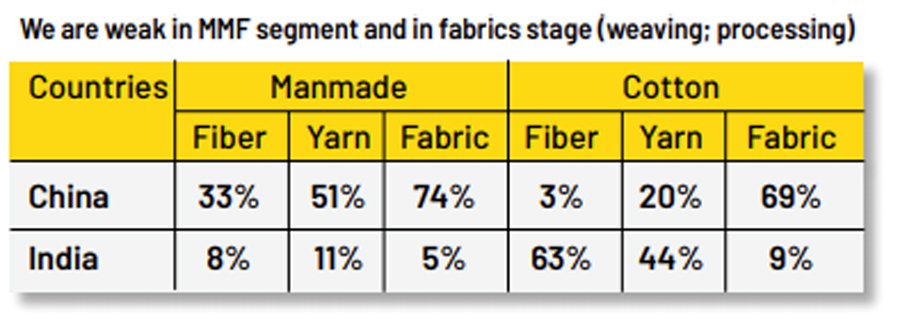
Maharashtra, Gujarat and Rajasthan comprise 85% of total shuttle-less looms installed in India, driven by large integrated mills that have invested in shuttle-less looms. However, most of the total fabric production comes from largely unorganised mills in the power loom and knitting sector. The weaving or processing sector in India is dominated by small-scale enterprises, which has challenges such as inadequate know-how, low focus on research, limited innovation in new product development and low technology upgradation.
The production-linked incentive (PLI) scheme was launched for 10 sectors recently to promote domestic manufacturing by providing financial incentives on incremental turnover for five years. The textile sector has been allocated Rs 10,683 crore under the scheme which, the concerned ministry has decided, will be offered for incremental production in 40 identified man-made fibre items and 10 technical textiles products. “The 40 MMF lines identified for the PLI push are the ones where India’s share in the world market is negligible while the 10 technical textile products are the top globally traded lines,” a source said.
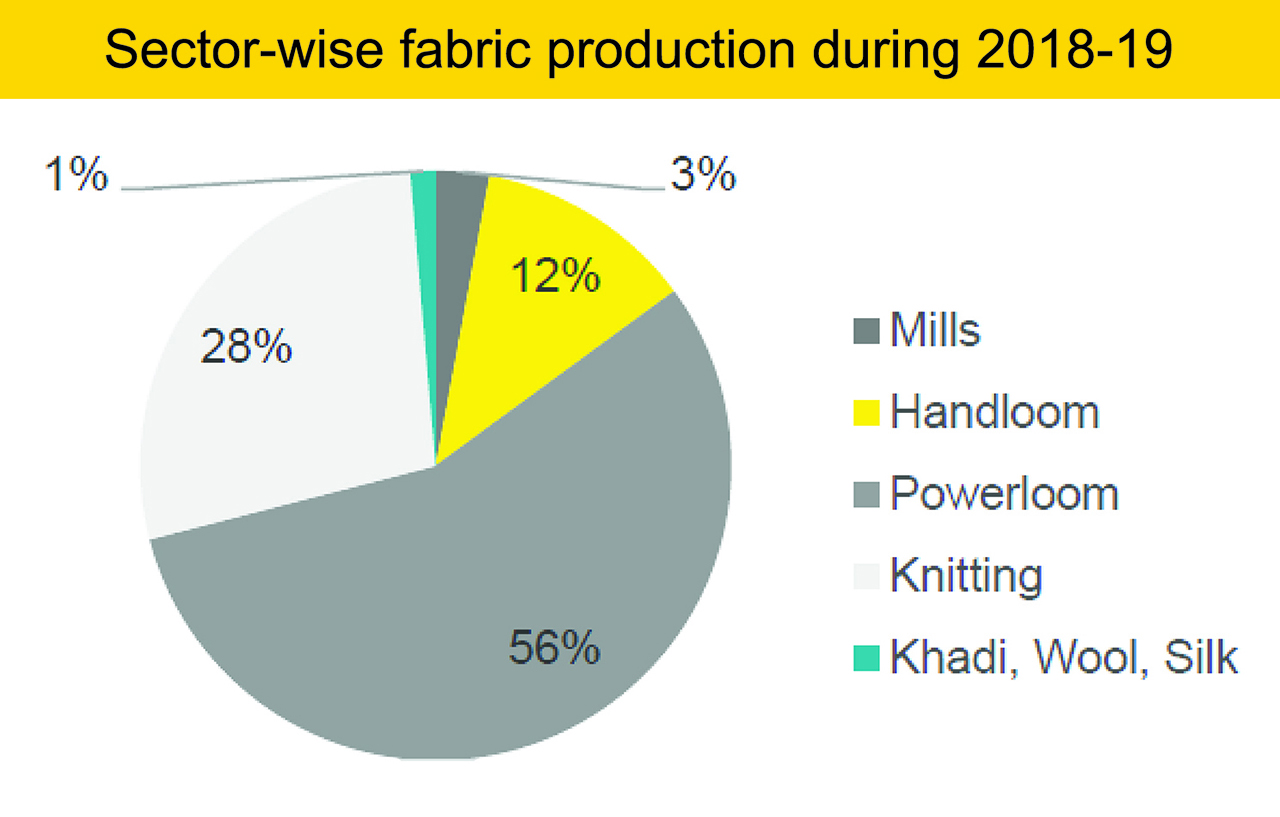
The fabric stage of the value chain in the Indian textile and clothing sector is relatively a weak link in terms of global competitiveness. It largely comprises MSME units. The vision to position India as a fully integrated and globally competitive manufacturing hub cannot be achieved unless flawless and processed wider fabric is available. In order to produce international quality with highest productivity, investment should be done in latest generation shuttles air-jet and rapier looms available in the global market.
In case of airjet, today highly capable technology are available which has wide range of width from 190 cm to 400 cm ogether with highest insertion rate. The focus is on lowest power consumption and highest quality of fabric in denim, bottom wear, poplin, sheeting and shirting, etc. These days air-jet looms are capable of running up to a speed of 1,250 rpm.
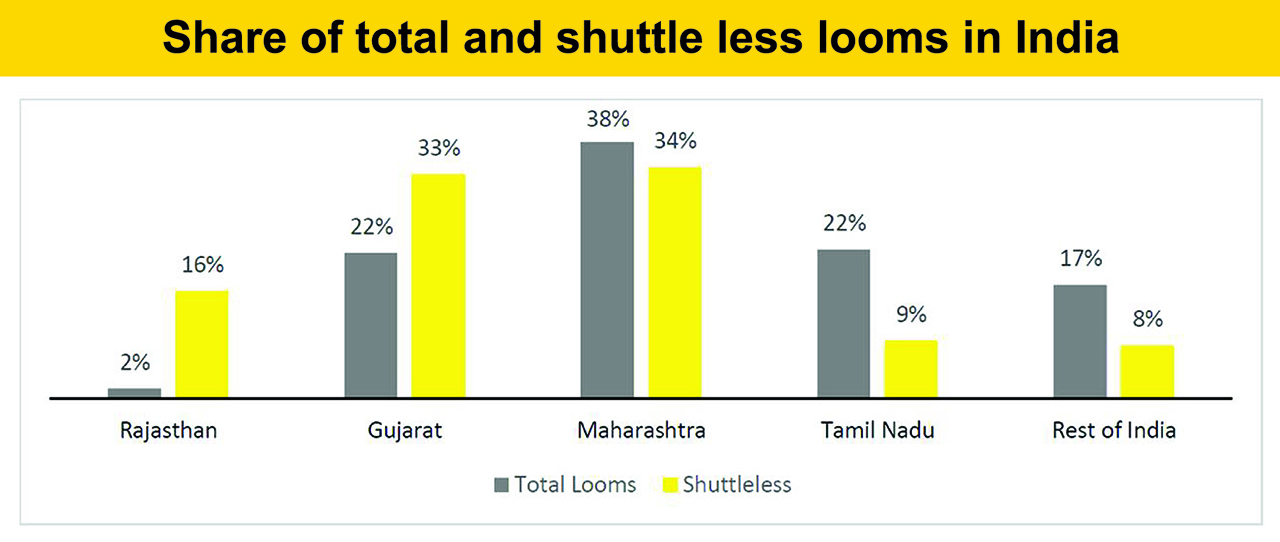
There is also rapier technology available in the market which has a wider range of width starting from 190 cm up to 540 cm, capable of weaving count range spun yarns Nm 200 – Nm 3 (Ne 118 – Ne 1.8) free flight up to Nm 1 (Ne 0.6) filament yarns 20 den – 3,000 den (22 dtex – 3,300 dtex) at the highest industrial speed for technical textile and non-technical textile like synthetics suiting, yarn-dyed shirting, denim and poly wool fabric. It can reach a speed level of 750 rpm for 190 cm loom width.
Meanwhile, the government has unveiled a scheme for setting up mega textile parks in the country as part of the centre’s efforts to position India as a fully integrated, globally competitive manufacturing and exporting hub for the sector. Finance Minister Nirmala Sitharaman made the announcement while presenting the Union Budget 2021-22, stating, ‘A scheme of mega investment textile parks will be launched in addition to the PLI scheme.” She informed that seven mega textile parks will be launched in three years as part of the scheme.
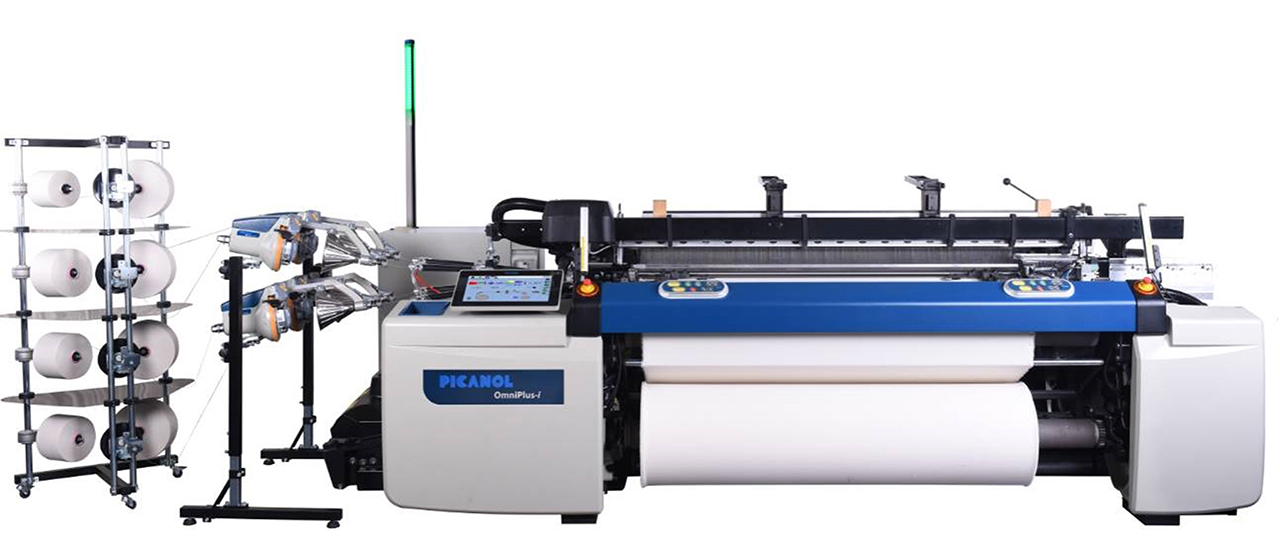
The mega textile parks will have integrated facilities and quick turnaround time for minimising transportation losses and eyeing big-ticket investments in the sector. The textile ministry had recently said that mega integrated textile region and apparel (MITRA) park spread over 1,000 acres of land with state-of-the-art infrastructure, common utilities and research and development laboratory is under consideration. If India is to become a global fabric producer, a lot more investment has to be made in weaving technology to improve quality and productivity and make the players competitive in the global market.
—
* About the author
Mr. Kasiviswanathan is an eminent personality in Textile Industry and is spearheading the Operations of Picanol Group in India. He is B.Tech in Textile technology from well-known ANNA University, Chennai 1983-87 followed by M.B.A in Marketing management from Regional Engineering College Trichy (TN) year 1987-89. Leadership, Prominent Speaker, Business Head, Team Motivator, Editorial & article Writer, having In-depth knowledge of Indian textile industry and close follower of Indian textile policy and implementation. Well-known in Indian textile industry deeply involved in the selling of world class imported spinning, weaving and processing industry and positioned in Delhi for last 32 years.
Majority of textile overseas countries are visited which gives insight of where we are placed in global scenario.
Picanol India Private Limited is a Member of the Picanol Group (NYSE Euronext: PIC). Established in India since 2008 focusing on sales and service of Picanol Airjet & Rapier Looms made in Belgium and China, Sales of original Picanol spare parts and accessories, the PCB repair station in New Delhi for the repair of electronic circuit boards of Picanol looms and the complete servicing of Picanol looms. In recent years, Picanol India has seen a steady growth in its market share, which has led to it becoming the leading provider of weaving machines on the local market today.
Picanol India has regional offices in New Delhi, Mumbai and Coimbatore followed by strategically locating sales and service members in Ludhiana, Bhilwara, Ahmedabad, Surat, Kolhapur etc. the company currently employs approx. 45 people in India.