KPM Processing Mill started their relationship with A.T.E. when they decided to set up a new project for processing tubular knitted fabric. Fong’s fabric dyeing machines were supplied through A.T.E. and KPM Processing Mill subsequently bought Corino slitter and Monfongs stenter

Growth mentality is essential for any organisation that wants to prosper by setting goals and achieving them as well as continually moving forward and progressing. It’s all about growing, progressing, expanding, and seeing the opportunity and promise in every moment, individual, setback and success. This is the only way to be successful. Possessing a growth mindset can help your firm move forward and position itself for future growth, profitability and success. KPM Processing Mill Private Limited is a living example of an enterprise that has worked extraneously hard to become one of the most well-known processing companies in the Tiruppur area. Since its inception in 2011, this enterprise has not looked back.
The company’s journey has been rather tumultuous. When asked to summarise the company’s progress, Managing Director Sekaran cites how they began with tubular knitted fabric processing and now have the ability to operate in open width form. KPM Processing Mill started their unit with Fong’s and Theis dyeing machines for processing the knitted fabric in tubular form. Subsequently, when they decided to go ahead with open width finishing, they installed Corino slitter, Monfongs stenter and Bianco open width compactor. Right now, Erbatech bleaching and washing ranges are under commissioning.
After installing the said machines, KPM Processing Mill will be capable of handling the fabric preparation in open width form. With bleaching, dyeing and washing, Sekaran estimates the company’s current manufacturing capacity at 20-25 tonnes. The company has adequate land for further expansion. It is also having a plan to set up a spinning project in the near future. Says Sekaran: “I have 34 years of expertise in this industry. After completing my textile course in 1984, I immediately began working in this industry at Tirupur. The ITMA expo, which takes place every four years, keeps us abreast of the latest machinery and technology. It inspired me to start my own business with the latest technology available in the global market. That’s how I started a process house in Tirupur for doing commission processing.”
While the business was declining during the last year on account of the pandemic, it has picked up very well since the last six months. Sekaran is confident that if the business situation continuous, probably he might achieve at least threefold of the current turnover within the next two years. In terms of sustainability initiatives, KPM Processing Mill is one of the pioneers in Tirupur. “Our approach is based on ensuring there is no waste. To reduce pollution, we have switched to using a gas-fired boiler. We heat up the water to 80 degrees Celsius using solar energy, which is being used for processing,” Sekaran informs. Further, he adds that the goal is “modernisation while keeping sustainability in mind.”
Relationship with A.T.E.
KPM Processing Mill started their relationship with A.T.E. when they decided to set up a new project for processing tubular knitted fabric. Fong’s fabric dyeing machines were supplied through A.T.E. and KPM Processing Mill subsequently bought Corino slitter and Monfongs stenter. According to Sekaran, A.T.E. is not just an agent for supplying machinery but also advises the customer to go in for the right technology based on the end products. A.T.E. has capable sales force having rich experience in textile processing by which they are able to guide the customers properly. A.T.E. has well-trained engineers for after-sales services and they constantly educate the operators on maintenance as well as for achieving optimum efficiency.
Sekaran was very much impressed with the technology of Monforts stenter especially the uniform heat distribution across the length and width of the fabric. Also, he pointed out the advantage of the unique fabric handling system.
When A.T.E. introduced Monforts technology through Monfongs to the Indian market, Sekaran was very happy to purchase the stenter since it was available at an affordable price. He is very happy with the performance of the stenter and the after-sales services of A.T.E. Sekaran is excited about the performance of the Corino slitter, which is running at a very high speed. After he installed the Corino slitter, many processing units in Tirupur have followed KPM Processing Mill. Sekaran has rich experience in dyeing and he is using Fong’s fabric dyeing machine for the past 35 years. According to him, the latest Fong’s fabric dyeing machine has many unique features by which all kinds of substrate can be handled. There is a strong bonding between KPM Processing Mill and A.T.E., which will go for a long way since the former is planning for expansion processing as well as planning to set up a spinning project.
Note from A.T.E.
“We are proud to be a part in the success journey of KPM Processing Mill since the beginning. Since Sekaran has thorough knowledge about textile processing there is a comfort level for us to deal with him. He is keen to learn the latest technology and ready to take challenges in his business. Sekaran is an ambassador for A.T.E. since he is using many of the machines supplied through A.T.E.. After supplying the machines to KPM Processing Mill, we have increased our market share in Tirupur. When we introduced Monfongs stenter in India, Sekaran in Tirupur was showing great interest to buy the machine since he is well aware of Monforts technology. Subsequently many processors have followed him. We are very happy to be associated with KPM Processing Mill and look forward to serve them in the future too.”
—
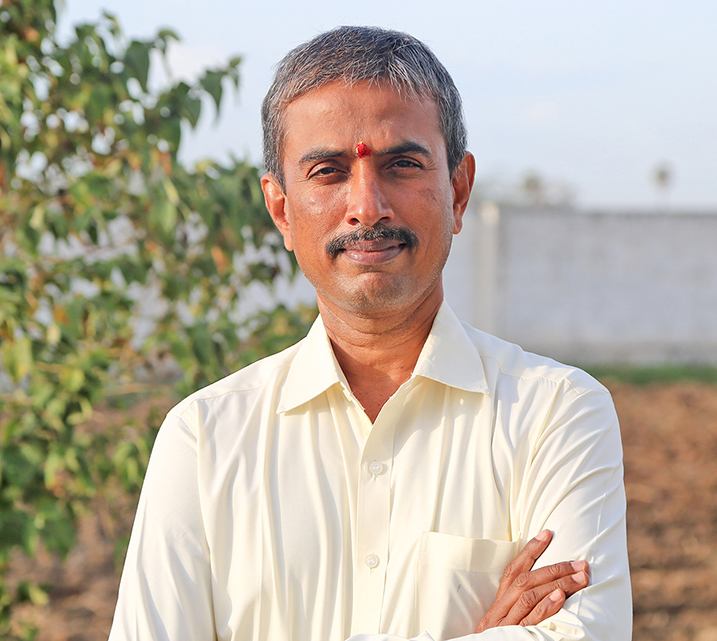
“I have 34 years of expertise in this industry. After completing my textile course in 1984, I immediately began working in this industry at Tirupur. The ITMA expo, which takes place every four years, keeps us abreast of the latest machinery and technology. It inspired me to start my own business with the latest technology available in the global market. That’s how I started a process house in Tirupur for doing commission processing.
– Sekaran