Whatever the end-use, knitted fabrics today need to measure up to the standards that critical customers demand: top quality fabrics that are good to wear and easy to care for. Textile finishing processes play a key role in that and Santex has the technology and the engineering know-how to ensure its machines keep the customers satisfied. The benefits are even greater when a mill operates a range of several machine types, as illustrated in the example here of a company from Uzbekistan. Santex AG’s machinery was featured at the CAITME trade show in Tashkent last September.
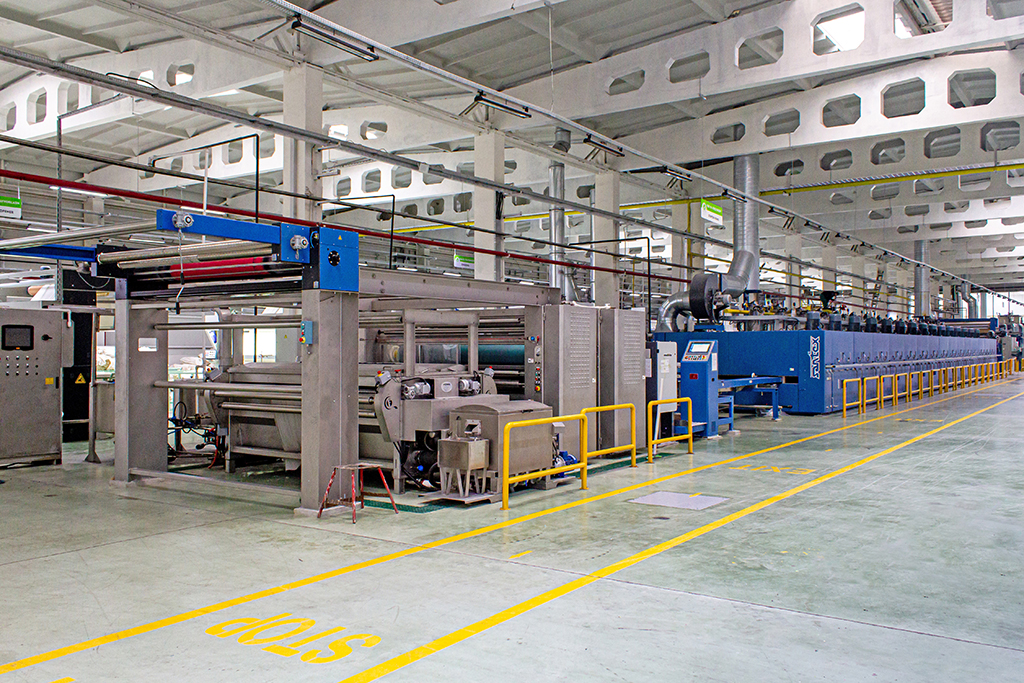
This was when a Santaframe high-performance stenter by Santex was already in operation at the Uzbekistani Global Textile mill in Fergana. As well as a leading spinning operation, the brand has a strong business in dyed knitted fabric. Global Textile is an export-oriented company with a strong focus on Europe striving for highly ambitious sustainability targets. It chooses advanced technology equipment for knit goods finishing, meeting its goal of high-quality output for apparel applications in fashion, sport and leisurewear. The Santaframe stenter is an integral part of this policy.
Tradition and Innovation
Santex has always upheld the traditional Swiss attributes of innovation and precision, and its machinery range supports that with specialised solutions for finishing open-width and tubular knitted fabrics. Energy-saving options also benefit customers through sustainable production and low CO2 values. In line with these values, the Santaframe offers unmatched performance and ground-breaking technology. It employs a novel air flow technique, carrying the fabric on a cushion of air. The resultant fabric has a softer handle and better shrinkage values. Customers are impressed with these and other advantages in heat-setting and drying.
Performance and Energy Savings
The Santaframe’s heat source is based on locally available energy. The heating system is located above the fabric track in the upper part of the treatment zone. A circulating fan draws air from the nozzle and treatment zone through the filter panels, leading it along a short path to the heat exchanger, from where it is fed to the nozzles. A regulating flap in front of the nozzle boxes allows top and bottom air flow to be continuously adjusted. The arrangement of the heat source on the pressure side of the circulating air fan allows high-speed circulating air to provide high drying capacity. This technological excellence combines both energy savings and cost reduction in the drying and heat-setting of textile fabrics.
Better Results
Global Textile’s mission is to be an undisputed leader, founded on the latest and best technological advances and uncompromising quality. For the treatment of knitted fabrics, that means more Santex machines are installed and more orders expected including two Santaframes to ensure the best possible results throughout processing. Santashrink is used for the shrinkage, relaxation and tensionless drying of tubular or open-width knitted fabrics. Fabric guidance – single, double or multiple strands – is possible at one treatment level. The extracting and over-stretching machine known as Santastretch combines in a single continuous operation the processes to open, unravel, extract, over-stretch and wet-compact the knitted fabric.
Santaspread sets new standards for unique finishing quality for tubular knitted fabrics. It surpasses existing quality levels and secures the results of preceding shrink and relax dryer’s basis, for minimal residual shrink values in the final goods. The goal of Santex machine development is maximum performances at low energy to achieve low residual shrinkage, soft handle and excellent lustre on textile surfaces. “We consider Santexto be at the forefront of technology for textile finishing of knitted fabrics,” says Natascha Meier, Global Director Sales and Marketing, Santex.