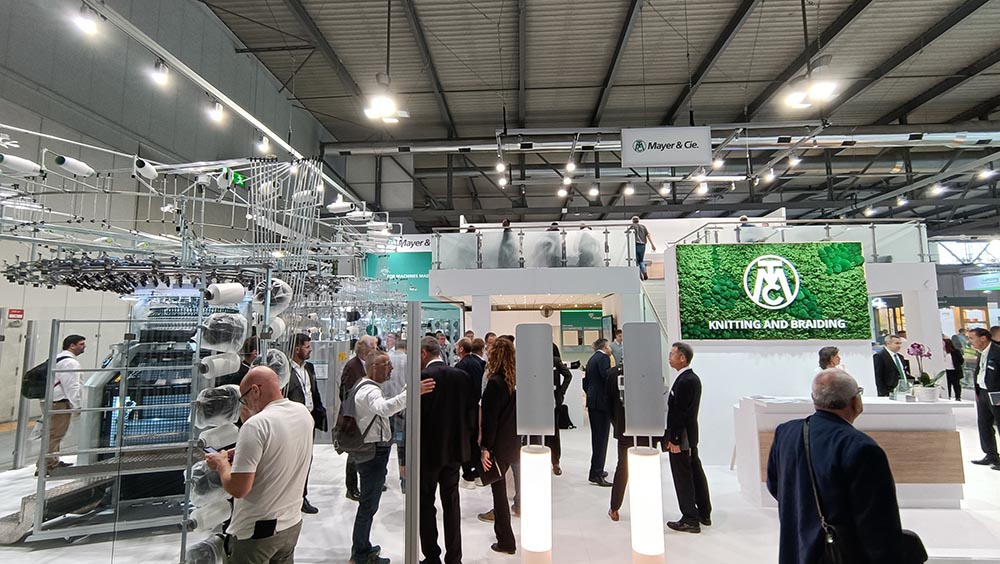
A leader in the circular knitting world, Mayer and Cie sets standards in developing new processes and new approaches through its depth of production, know-how and market knowledge. In this exclusive interview, the company’s Managing Director Benjamin Mayer outlines how the company has been maintaining this lead and expanding it in the field of braiding machines while highlighting its growth strategies and the products it will showcase at the forthcoming ITMA trade fair
Could you share details about your company’s journey so far?
Established in 1905, Mayer and Cie has been an innovation leader in the global knitting industry. We are heading for our 120th anniversary and that is something to be proud of. What characterises us is, for one, the fact that we are an owner-managed family firm. The family firm aspect extends to our employees who have a high level of identification with Mayer and Cie and are loyal and committed to the company. It also extends to our claim, since the firm’s foundation, to be a step ahead of the competition. The spirit of innovation and the desire to stay ahead of the game has been part of our DNA since our very first days. Together with partners of many years we have repeatedly managed to revolutionise circular knitting and keep ahead of the competition, right up to this day.
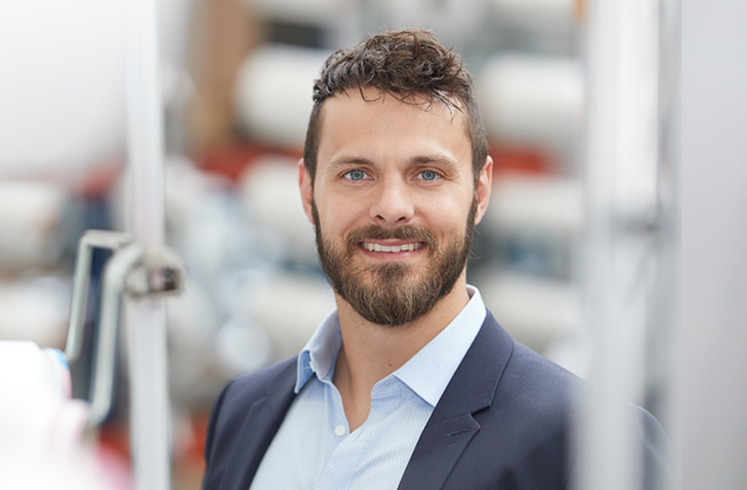
In this illustrious history, what were the key milestones or defining moments that laid the foundation for future growth?
The first and fundamental milestone was the start of series production of circular knitting machines. That was not until the late 1930s. The company had previously concentrated solely on sinker wheel machines but in about 1935 began to develop more efficient circular knitting machines. German post-World War II reconstruction – a difficult phase – marked the start of internationalisation and growth of Mayer and Cie. Today’s factory on the outskirts of the town was built and Mayer do Brasil was founded. Then, in 1967, came the OVJA 36, a legend to this day.
The oil crisis directed attention toward leisure wear and, with it, to single jersey. Mayer and Cie’s response to the corresponding demand came in 1987 with the Relanit. Today, we are focussing on further increasing our machines’ efficiency and longevity to make a Mayer and Cie circular knitting machine a sustainable investment – also in terms of environmental aspects. Our digital services, grouped under the name of ‘knit link’ also work towards this end. They are designed to improve our customers’ results when working with our circular knitting machines.
How is business at Mayer and Cie, particularly coming out of the pandemic and still under the impact of war?
Textile is an early cyclical industry and we feel the impact of economic changes very quickly. That has always been the case. Relatively recent, however, is the short time span of economic cycles that require a much more immediate reaction than only a few years ago. They are triggered by occasions such as the pandemic or the conflict between Ukraine and Russia. Irrespective thereof, our current order position is, gratifyingly, around the long-term average.
Currently what is the manufacturing infrastructure of the company?
Since 1905 the company has been headquartered in Albstadt in South Germany, where most of the Mayer and Cie machines and knitting heads are manufactured. It is also home to the administration and research and development departments. Mayer and Cie has about 350 employees in Albstadt. Our factory in Czechia has a payroll of around 60 employees. They manufacture individual components and a few selected machine types. A small team in Vsetín is engaged in research and development. In our factory in China we only assemble machines sold in the Chinese region and, to some extent, neighbouring markets. Locally manufactured components are used along with components from our European works, including the knitting heads. Our team in China numbers around 30 employees.
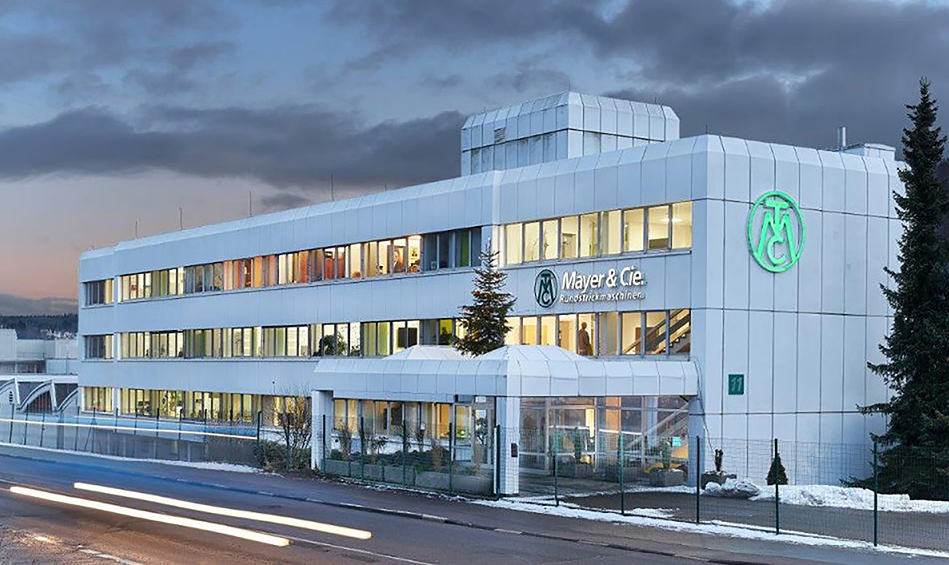
Can you elaborate on the products and solutions offered for the global market?
The focus of our machine portfolio is on core market applications such as single jersey, double jersey, interlock, eight-lock structures and three-thread fleece – demand for all of which is sound. The same applies to a number of niche applications, the first and foremost of which are mattress cover fabrics. We also provide solutions for spacer and fine gauge fabrics.
Can you highlight some of your key global markets?
Our strongest markets have been unchanged for quite some time. Along with China, India and Turkey are the most important single markets. A relative ‘newcomer’, and a very sound one too, is Uzbekistan. In about 10 years, our circular knitting machine sales there rose from single to triple digits.
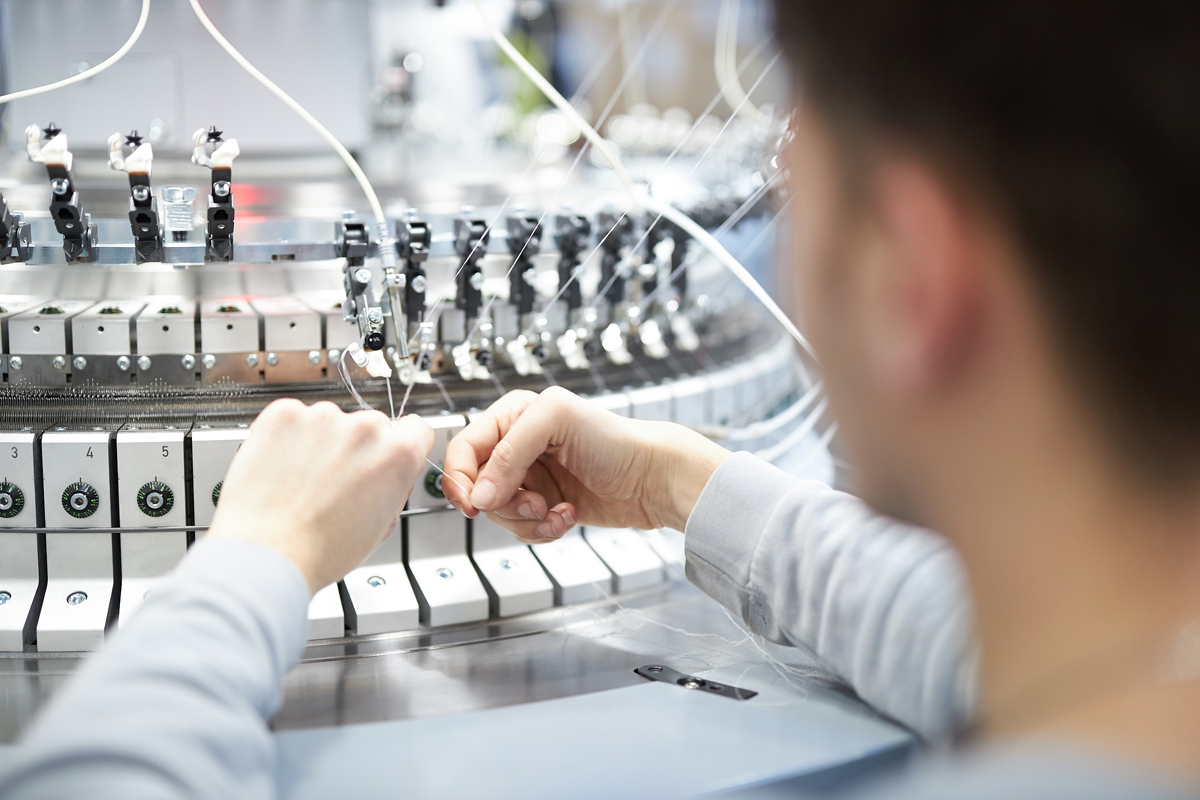
What are some of the global innovations by Mayer and Cie in the knitting segment over the last many decades?
The most prominent one is surely relative technology, which is used in our Relanit machines. Ever since these machines were launched in 1987, the Relanit has been in continuous strong demand. On average, more than 300 machines with relative technology are ordered every year. That is because they offer customers tangible benefits. These benefits are based mainly on a single property of Relanit machines: their gentle processing of the yarn. There is less strain on the yarn due to the relative movement of the sinker in relation to the needle. As such, there are only a few deflection points for the yarn. Electronic individual needle selection is another concept that has revolutionised circular knitting technology. Each system works with an individual magnet and so electronically controlled pattern adjustment is extremely fast.
What are your thoughts on ITMA? How important is the show for the global textile industry?
I really can’t say when we took part for the first time since we have participated so many times. I can, however, recall a few memorable occasions. In 1969, in Basle, we presented the OVJA 36 for the first time. It featured 36 feeders with individual jacquard drums and was able to produce jacquard-patterned piece goods. This machine became legendary. In some cases, there was a trade in order confirmations – the earlier the delivery date, the higher the price. In 1987, we presented the Relanit for the first time. These memories show that our company’s calendar is in some way based on the ITMA trade fairs. It’s an event we are all working towards – an event where we will present our new developments. The ITMA is the industry’s benchmark.
What can visitors expect from Mayer and Cie at this year’s ITMA?
At the ITMA fair we are concentrating on making our products of even more lasting value for our customers, especially more efficient and more durable, leading to greater sustainability. In terms of machines, there’s one novelty: the three-thread fleece machine SF4 3.2III. The revised OVJA 2.4 EM and Relanit 3.2 HS are established in the market. All three serve classical uses. With sustainability and efficiency in mind, we offer various machine-specific upgrades and digital services, which we summarise under the name ‘knit link’. An important individual product is ‘knit hawk’, a watchdog that recognises errors during the knitting process and ensures that the machine is switched off in the event of major or recurring errors, thereby reducing waste output significantly.
ITMA 2019 was all about Industry 4.0, automation and digitisation. How has Mayer and Cie progressed on these aspects and what next?
Over the past four years we have worked hard on developing Industry 4.0 digital services for our customers so that the networking of our machines can first be transferred securely into everyday working life. Industry 5.0 naturally offers a perspective for the textile machinery industry, but we must realise that our industry, in contrast to information technology, is a follower as far as digital change is concerned.
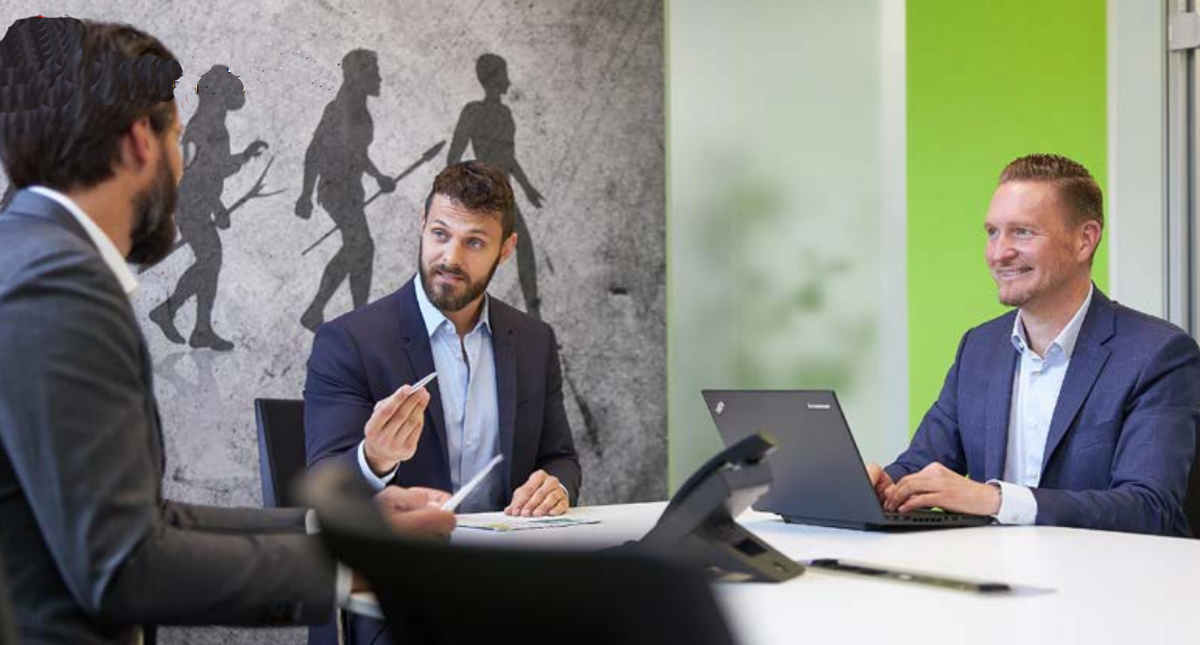
What is Mayer and Cie’s sustainability philosophy and how are you supporting your customers’ goals?
As a manufacturer of innovative goods we understand sustainability in terms of the efficiency and durability of our machines. We want our customers to be able to work successfully with our machines for a long time. This, no doubt, has been a strong point of our machines for decades. To reinforce it, we are working on upgrade kits to enhance our existing machines in special aspects to make them faster, more versatile or simply more durable. To the same end, we have invested a lot of effort into developing digital services.
Given the highly competitive market place, why should a customer consider Mayer and Cie for his requirements? What are your key strengths and advantages?
We are experts in producing premium circular knitting machines backed by the experience of several decades. We have an extremely experienced team and we are flexible and inventive. We know how to transfer trends and requirements into machines and solutions. We are reachable and approachable either via our headquarters in Albstadt or via our agents. There is an established network of Mayer and Cie representatives worldwide. To put it bluntly, we offer our customers peace of mind.
Finally, with the fourth generation successfully managing the company, what is the future vision you have set for Mayer and Cie? What can we expect in the years to come?
In times of change, stability and reliability are precious assets that we as an owner-managed family firm can offer. Apart from that, our claim is as simple as it is exacting. We want our customers to be able to knit the applications they require efficiently and reliably with our machines. We want to support our customers as they forge ahead.