The technology fully geared to E³
The Autoconer 6 was delivered to the first customers at the beginning of the year. With its ground-breaking innovations, Schlafhorst’s new automatic package winder caused a global sensation – “The best original ever”. The German textile machinery manufacturer presented the Autoconer 6, in a brand-new version geared to E³, to the general public at ITMA 2015. E³ is synonymous with triple added value in the Energy, Economics and Ergonomics categories.
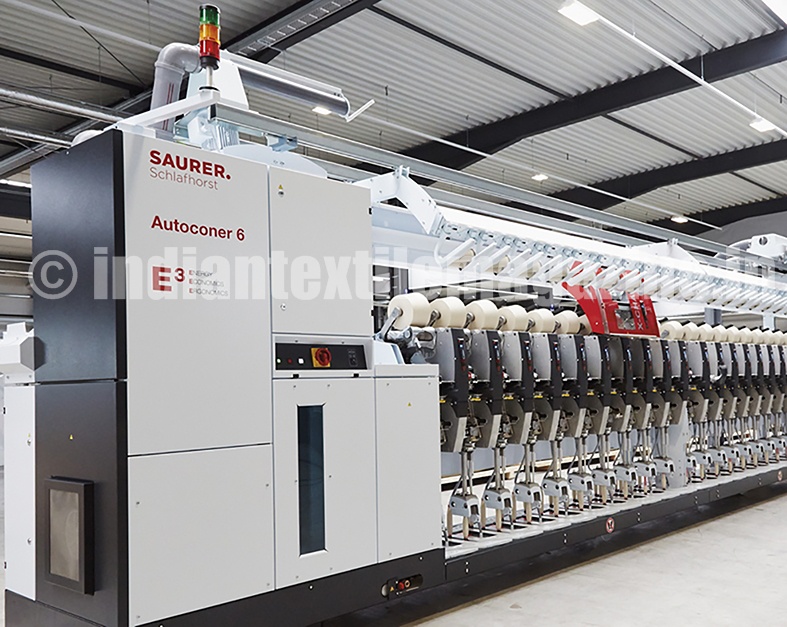
A string of unique innovations has enabled Schlafhorst to reduce the energy consumption of the Autoconer 6 by up to 20 per cent compared with its predecessor. A key contributory element here is the new Eco-Drum-Drive System in the selfadjusting winding unit. Thanks to the latest drive and bearing technology, the system saves a considerable amount of energy. In addition, the suction system motor and frequency inverter always work at the most effective operating point due to improved performance efficiency. To generate further energy savings on the spot by optimising the winding process, energy consumption at any moment can be monitored online centrally at the Informator. The Autoconer 6 can be equipped with the new energy monitoring facility for this.
SmartCycle and the new intelligent vacuum adjustment system work together according to the “power on demand” principle, i.e., creating a vacuum as required. This lightens the energy demand in the winding mill significantly between yarn end pick-up cycles. SmartCycle is the new, intelligent upper and lower yarn end pick-up function in which the winding unit, the Informator, the suction system and the doffer co-operate optimally and are self-adjusting. The flow-optimised suction tube makes an effective contribution to energy saving too: in one customer’s mill, the vacuum could be reduced by 20-25 mbar while retaining a reliable upper yarn end pick-up.
Economics – 2 x 6% more productivity
The new Autoconer 6 also achieves a double-digit increase in productivity. Even the basic model is six per cent more productive than its predecessor. LaunchControl boasts the latest process intelligence for a slip-free, self-optimised start-up. Higher acceleration and faster deceleration of the winding system are possible using the innovative Eco-Drum-Drive System. The advantage is obvious: the Autoconer 6 winds faster at maximum speed and can be decelerated later.
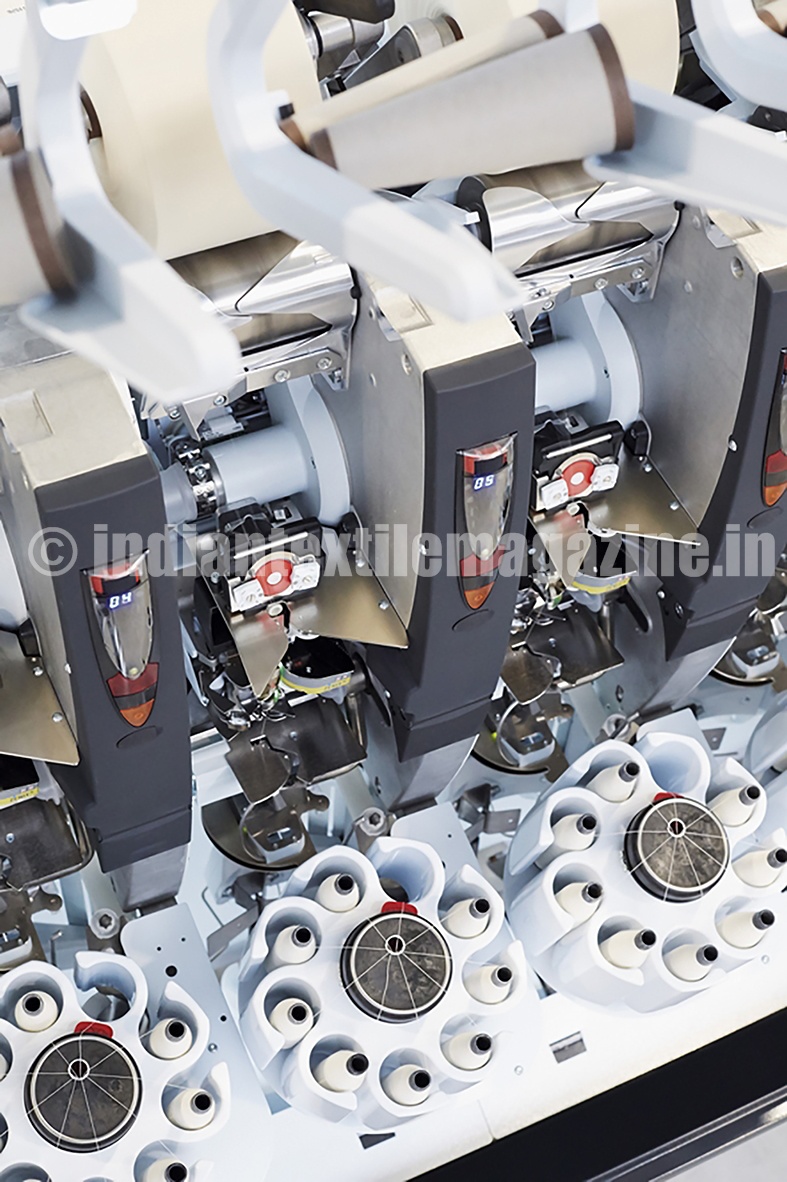
Non-stop productivity is the distinctive feature of the new generation of machines. In combination with the new suction tube, SmartCycle cuts unproductive cycle times. Upper yarn faults are reduced as far as possible, while optimized cycle sequences minimise downtimes. TensionControl, the standard yarn tension control system on the Autoconer 6, prevents unnecessary tension breaks during bobbin unwinding. All these factors signify higher efficiency ratings and productivity right from the start.
With the technologically optimised, high-performance Speedster FX module and the new SmartJet function with which the doffer supports the upper yarn search, another six per cent productivity can also be gained optionally. In practical tests with the SmartJet function, the doffer aids the upper yarn search so effectively that “red light periods” are reduced by up to 70 per cent. That’s 12 per cent more productivity in all – a unique leap forward.
Ergonomics – Intelligence inside
Intelligent sensor technology and smart process control turn the Autoconer 6 into an automatic package winder that pushes the textile-technology limits outwards of its own accord and winds at the most productive settings virtually without any operator input. The functional design and optimised process sequences minimise downtimes and malfunctions, so that manual intervention by the staff is practically unnecessary. Smart electronics and mechanical innovations complement one another in this design.
Autocalibration of the splicer feeders and suction tubes relieves the burden on the operators substantially, because manual settings are rendered superfluous. The X-Change doffer assumes additional functions too: with Tube Check it detects tubes that are not round via laser and removes them automatically. This not only enhances the package quality, it increases staff safety. And it effectively aids the upper yarn search with Smart-Jet, meaning that operator intervention is rarely required.
Even the time and labour-intensive consumption measurements for optimising the energy utilisation of processes are no longer required on the new Autoconer 6. The integrated energy monitoring and the new operating console supply all the information needed for conserving energy at a glance.
Smarter splicing
Once again the Autoconer 6 sets the benchmark in splicing with the new SmartSplicer model family. Its completely revised splicer geometry ensures the best splice quality in every application with the simplest handling. The splicing parameters can be entered conveniently at the Informator. The system guarantees spliced joints that are identical with the yarn, maximum strength, outstanding dyeing results and full added value in downstream processing.
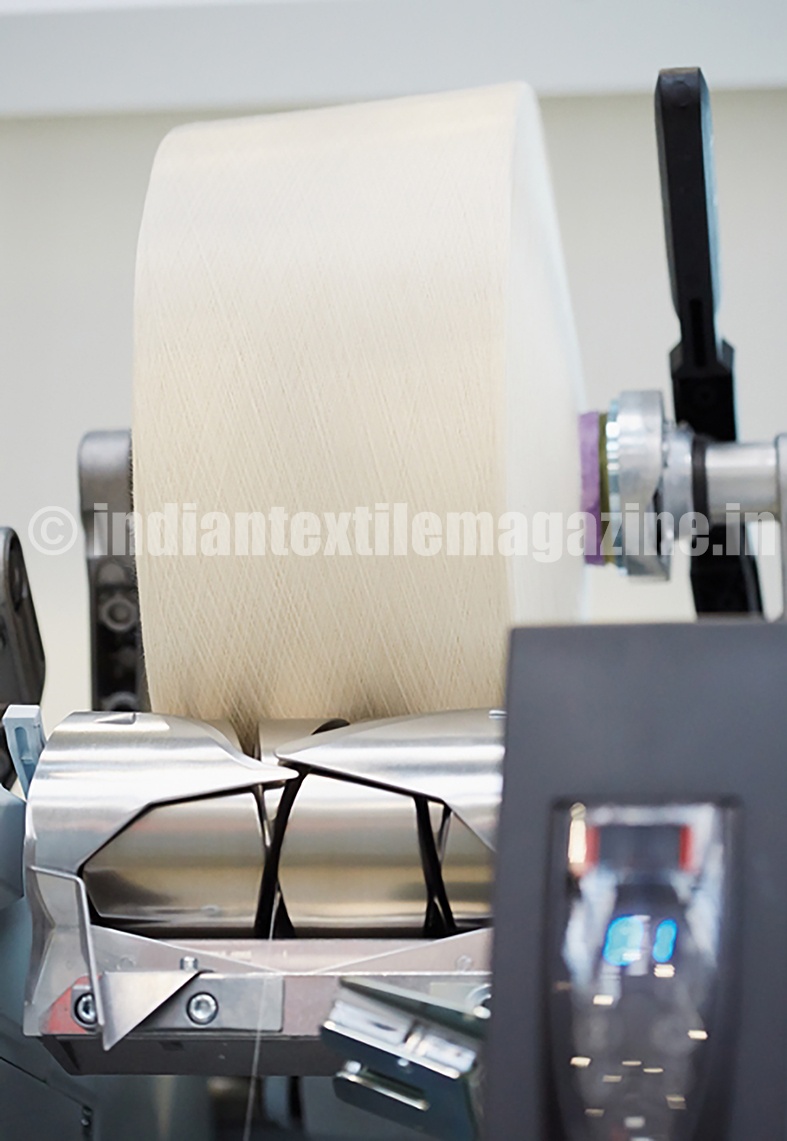
The SmartSplicer will splice all common standard, compact and blended yarns. For extreme strength and an even better appearance, especially for denim, linen and OE yarns, the SmartSplicer Injection is used. The SmartSplicer Thermo is recommended for wool and wool-blend yarns, while for elastic core yarns Schlafhorst offers the SmartSplicer Elasto. The splicers are supplied ready for use and can be adjusted very easily in a few simple steps if required and adjusted to the process reliably.
Leading automation solutions
The Autoconer 6 has the most intelligent material flow system in the world. Schlafhorst offers its customers automation solutions that lead the way in every respect. With VarioReserve, Intelligent Bobbin Sharing, High Speed Feeding and various automation units, Schlafhorst ensures profit-enhancing process reliability and minimal reliance on personnel in every spinning mill. A new standard has also been created for the Autoconer 6, type RM machine with its unique new circular magazine and the 9+1 bobbin feed concept.
The superb, convenient package handling of the Autoconer 6 is especially important for automation purposes. The X-Change doffer has no equal with its innovative empty tube strategy and practical multitube handling. In Teaching Mode it learns to distinguish between tubes autonomously, and starts up automatically following a lot change. With the new Tube Check and Smart-Jet features the X-Change is consolidating its leading position in automation.
The various machine types (RM, D, T and V) permit automation of individual stages in every spinning mill.
Schlafhorst quality packages
The Autoconer package is the benchmark for quality and added value in downstream processing. The perfect interaction between the new standard yarn tension control system TensionControl, the unwinding accelerator, the new Eco-Drum-Drive System, effective electronic anti-patterning and optionally the new gate tensioner or the disc tensioner produces a package density of unsurpassed uniformity.
The Autoconer 6 introduces reliability and quality into the production of process-optimised packages through a broad range of package formats: cylindrical and tapered up to 5°57’, with traverse widths from 3” to 6”.
Packages with a diameter of up to 326 mm can be produced on the Autoconer. It goes without saying that a precisely measured yarn length is achieved for all package formats.
FX high-performance technology components
For spinning mills that want to design their winding process to be more efficient and geared to added value, Schlafhorst offers the innovative FX high-performance components. The Autotense FX, Variotense FX, Propack FX, Variopack FX, Ecopack FX, Speedster FX and PreciFX modules hugely boost production performance and raise quality, productivity and cost-efficiency to the most advanced level, both in winding and in downstream processing.
The best original ever: just a year after its market launch, the Autoconer 6 continues to raise the bar in the winding mill with its brandnew functions. That will please customers of Schlafhorst. Once again they will be a decisive step ahead of the competition.