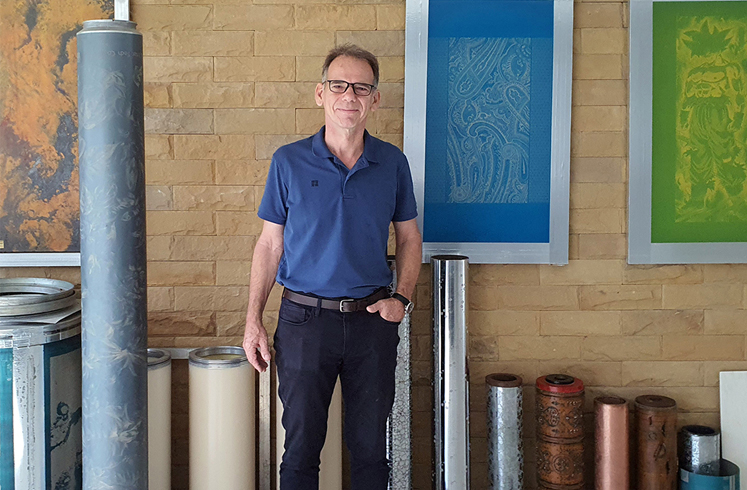
Nova Inter Tech, already a well-established name in Thailand and other countries, has also made significant inroads into the Indian market and has emerged as a leading supplier to the textile industry. The Textile Magazine caught up with Managing Director Thomas Heym for an exclusive interview.
Thailand-based Nova Inter Tech Co, Limited has made a mark for itself with its range of print- related services. The company is a leading name when it comes to providing recycling service for rotary screens. It also sells machinery for rotary and flat screen production. The company is also into designs for the apparel and home furnishing industries, apart from offering digital printing services. In the interaction with The Textile Magazine, Managing Director Thomas Heym said, “In the year 2000, cooperation between Inter Silk Screen Co. Ltd., Thailand and CST GmbH, Germany was established to set up a new company named Nova Inter Tech Co. Ltd.”
“The objective of this company was to support all rotary printers in the local market with a 100% pollution-free recycling service for their rotary screens. During that time printers were not paying much attention to the environmental issues and their workers used highly toxic chemicals without any protection to recycle the screens. It took us about 2-3 years to convince 90% of the local printers to change from chemical stripping to our pollution-free recycling process. The textile world is small and soon we received requests from printers outside the country. So, in 2006 we started to sell the first machines internationally,” he added.
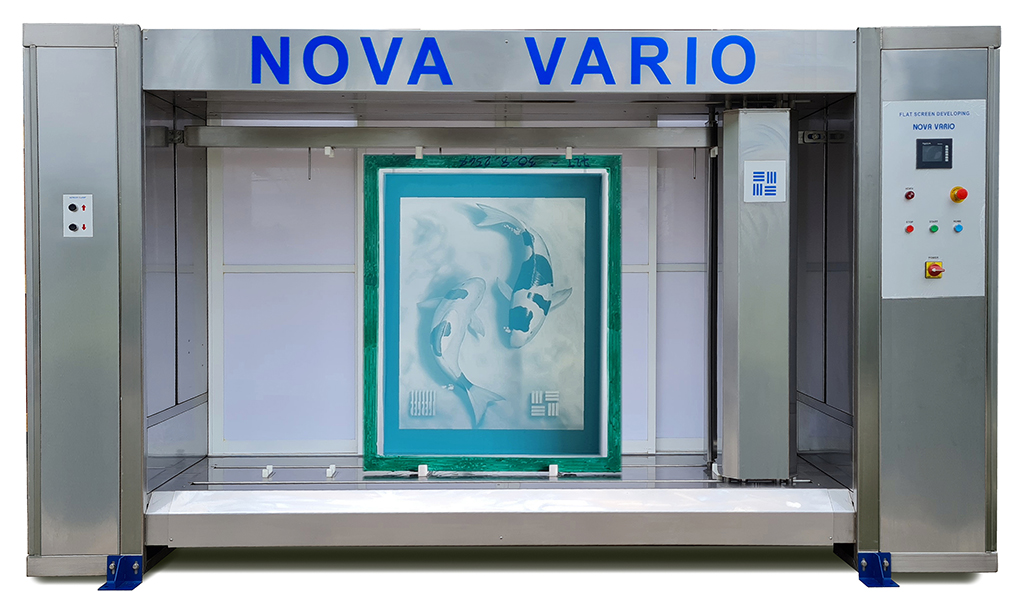
“Next to the Nova Jet recycling machine, we are also selling all other machinery used in the rotary and flat screen production. We are also a service hub for commissioning rotary and flat screen engraving for the textile and graphic markets in Southeast Asia,” he further stated. According to Thomas Heym, Thailand has a very good manufacturing infrastructure. “There are a large number of metal processing factories locally where we are able to source the best quality materials for our machines. Our local suppliers focus on the machine body and consumable items, while the main high-pressure components and electrical parts are from the best suppliers internationally,” he stated.
“We are assembling all of these parts in-house, including the electrical and software programming. The QC of all our machines is done by our operators who are using the same machines in their daily production,” he added. “Our biggest benefit over our competition is that we only sell those machines which we use in our own screen-production. We also give our customers the opportunity to use the same machines in our production prior to the installations at their factory,” he further explained. Giving an overview of the product range offered by the company Heym said, “We offer our customers the complete range of rotary and flat side equipment.”
“This also includes auxiliaries for screen preparation from the first step (unpacking of screens) to the final step, which is printing on fabric. Also, all chemicals involved in the screen processing are supplied by us. Due to our company philosophy, we avoid any toxic chemicals being utilised in our production. We also offer digital printing solutions locally from Konica Minolta, Reggiani and HP, as well as all requirements and know-how for digital printing. Of course we are also offering a commission-stripping service to our local and some international customers. Since two years we have also been supporting the packaging market with new technologies for flexo printing,” he elaborated.

Global Presence
Nova Inter Tech has made rapid inroads in key global markets. Sharing details, Thomas Heym said: “As of today we have our equipment in over 150 factories in 22 countries around the world. It is extremely important to have a local partner to bridge the gap between our customers and ourselves and ensure that there is always a strong support team. In India we are satisfied with our local agent who is supporting the customers with service and maintenance and of course also promoting our machines. Here in India our strong partner is Bludigit Technologies, represented by Rajendra Patil. Of course, the majority of our customers are in textile countries such as Brazil, Mexico and Argentina in the west and China, Korea and Japan in the east. Our strongest region is Southeast Asia with countries like India, Indonesia, Thailand, Pakistan and Bangladesh making up the majority of our customers.”
“Of late we have been observing growing markets in Africa and we have been successful with some machine installations in that region,” he said. Speaking about a recent launch, Thomas Heym remarked: “Our company has always been developing new technologies and methods to improve our in-house production and machines. The development process never ends. We have just introduced our new flat developing machine, the Nova Vario, into the market which will be included in-line for future projects. Our Nova Jet 3500 machine is the fourth generation of our market-leading Nova Jet series of plain water stripping machines. The next generation will follow soon.
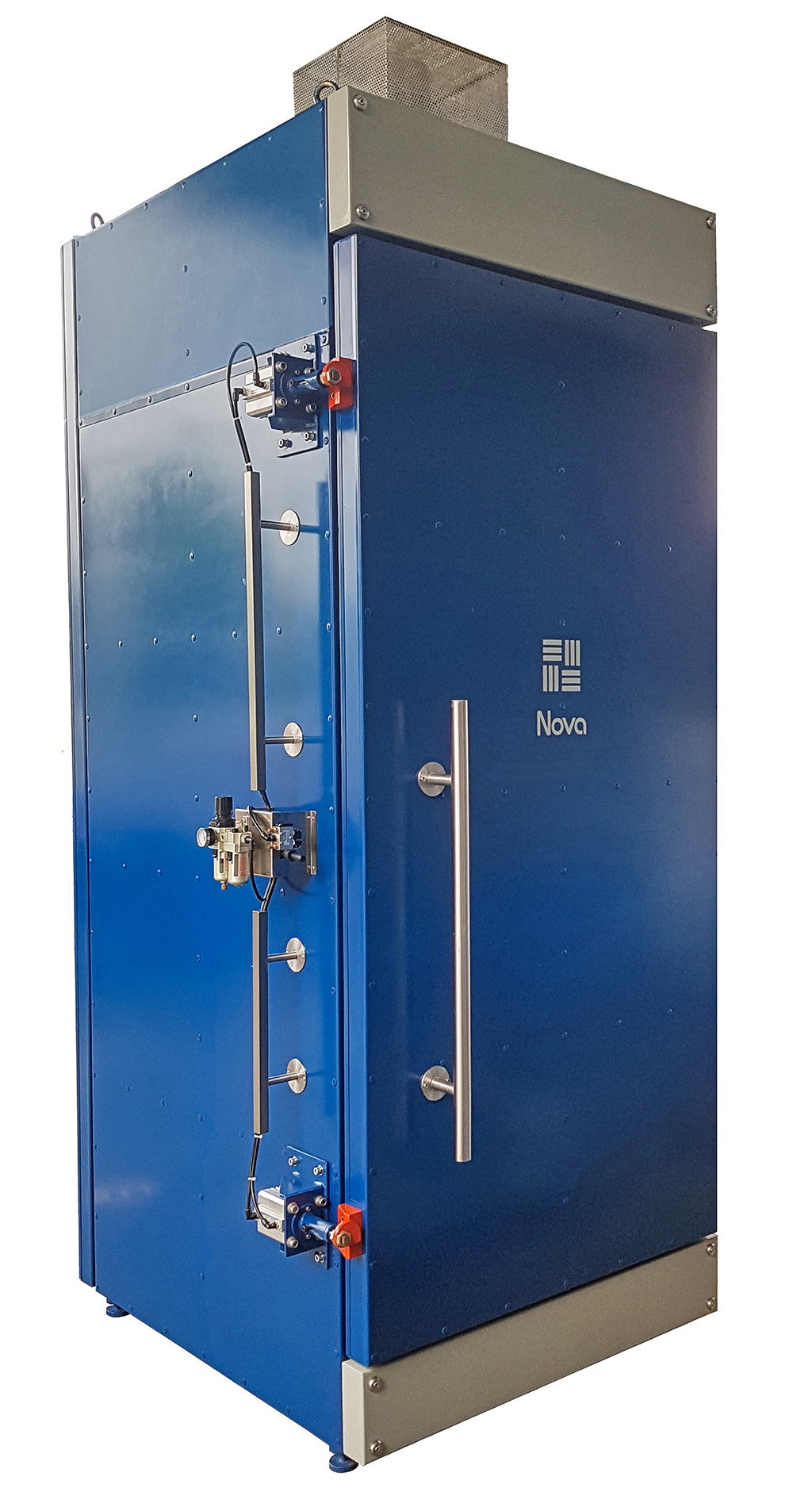
Competitive Edge
Throwing light on the advantages and strengths of the company as compared to its competitors, Thomas Heym observed: “We were the first company worldwide to introduce the plain water stripping machine to the textile industry in the year 2000. Being the pioneers of this technology gives us a responsibility to continuously improve and develop. We are proud that even our first machines, installed in 2006, are still running well and in a good condition. Selecting the best parts and using them inside our own production machines, of which we have several in Thailand, ensures that we always have an edge on our competitors.” “The constant drive to implement new features, such as low-pressure de-clogging of screens after printing, have been added through the years as we become more confident in the technology,” he added.
Right from its inception, Nova Inter Tech has been known for its commitment to sustainability initiatives. “Sustainability is at the epicentre of most decisions that we make and this has been so ever since Nova Inter Tech started in 2000. We will continue to promote sustainable technologies in the screen-making process and always pursue the target of zero emissions. Internally we have achieved ISO 9001 and ISO 14001. Since 2006 we are using our own water treatment plant to recycle all water utilised by our machines. It is a must for textile companies to adopt the new environmental standards, especially since big brands are now very conscious of environmental issues,” Thomas Heym explained.
Automation
Going into details regarding the company’s focus on automation and digitization, Thomas Heym said, “We are currently developing machinery for automation of certain processes involved in screen-making. So far this development is targeted more for non-textile customers who depend on repeatable quality. Especially, high labour cost countries benefit from automation in the production.”
India: A Key Market
The company views India as one of its key markets. “We are proud to say that India is one of our biggest markets and we are active since almost 20 years here. Most of the largest printing concerns in India already have our equipment,” Thomas Heym said, adding, “We see that India is a growing market and slowly replacing China as the main supplier of textiles internationally. India has the right environment – from machinery to labour – to be successful in the future. There is no question that currently the Indian textile market has one of the best opportunities to grow and expand, particularly with technology and services that can have a huge impact on the waste and water treatment at existing factories.”
Growth Plans
The company has charted out a well-defined growth path for the future. Sharing details and outlining the target for 2025, Thomas Heym stated: “Our aim since the beginning has been to support the printing industry with the best equipment and know-how. As long as screens are used for printing, we will support the printers to make the process effective and sustainable. The change we see with the strong growth of digital printing is a good step to reduce water consumption and waste of printing pastes. We are supporting this trend with digital printers and software from Reggiani, Konica Minolta and HP.”
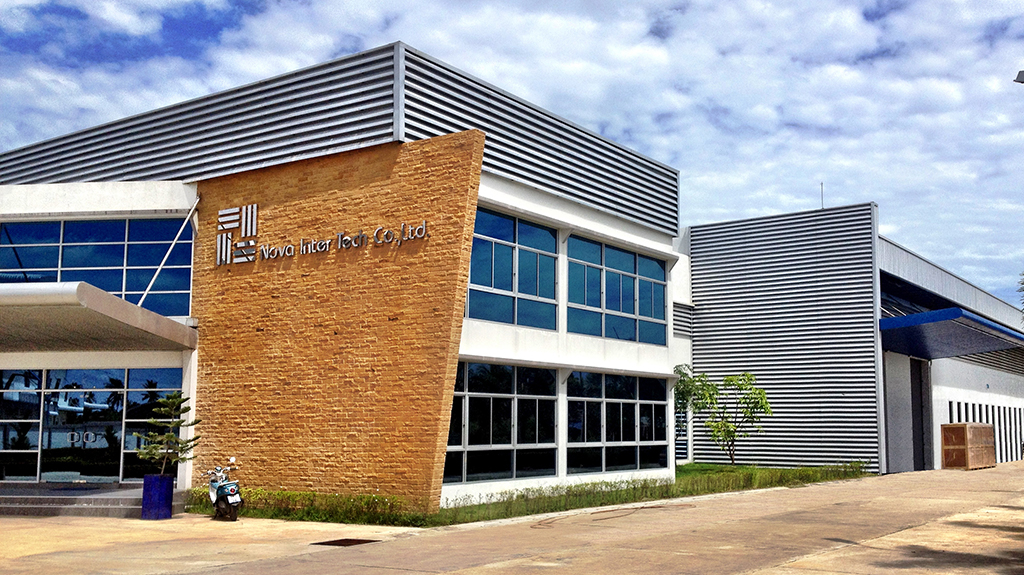
“Nevertheless, we still believe that on long runs and speciality prints, conventional screen printing will always exist and have its earned share in the industry. Only with screen printing, printers are able to show knowledge and experience which they have accumulated over many years. We will always support the screen printers to make even small runs possible and cost-effective with conventional printing. We believe that it is important for textile printers to have screen and digital printing to support their customers in the best possible way. With new and more sophisticated engraving equipment from our partner, CST, we are able to also grow in non-textile fields like security printing and packaging,” he added.