Unveils path-breaking innovations in weaving technology
Picanol, the global leader in weaving technology, had the largest participation at ITMA 2019. The company showcased 10 machines in its huge pavilion which was packed with visitors from all across the globe on all the seven days of the show which proved the launch pad for future manufacturing technologies. Picanol has always set standards in the weaving segment. Be it the digitized insertion on rapier for denim fabric or the world premier of OmniPlus-i, the new benchmark set in airjet weaving, Picanol showcased the latest and the most advanced weaving technology setting the platform for future growth.
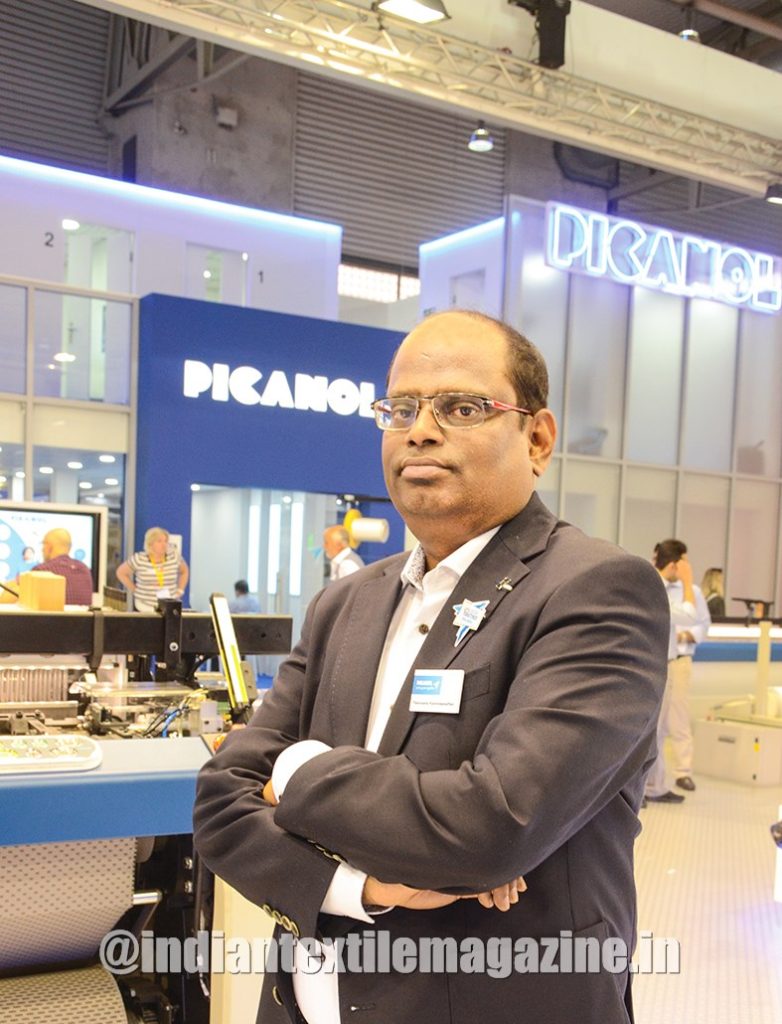
We spoke to Mr. P. Kasiviswanathan, Gravity Point Manager & Director, Picanol India Private Ltd., to know more about the latest innovations launched by the company at ITMA and the response from the Indian and global visitors.
Excerpts:
Picanol undoubtedly had the largest participation at ITMA. Let us start with your presence at the show?
The Picanol booth was located in the biggest hall dedicated to weaving at ITMA Barcelona. In total, Picanol had 12 machines on display at the event, as well as five new airjet weaving machines. We also presented five rapier weaving machines featuring many new developments. Furthermore, a rapier machine in Jacquard execution was on display at the Bonas booth and a terry airjet machine was shown at the Stäubli stand. The Picanol Global team was made up of Sales, Service, Product Managers and technicians.
How was the overall response at ITMA?
Overall it was a good ITMA for us. Given the more difficult and uncertain worldwide economic situation, we arrived at ITMA with moderate expectations. Pleasingly, those expectations were greatly exceeded. A good number of visitors came from Asia, Europe and the US, and our team was subsequently busy interacting with the new prospects and customers, all of which rather contradicted the ongoing negative situation in the market.
You had launched new airjet loom OmniPlus-i which was a major attraction in your stall. Can you throw some light on this?
We intentionally timed the display of our premier, brand new airjet machine, the OmniPlus-i, for ITMA 2019. OmniPlus-i unquestionably represents the benchmark in airjet weaving. It further builds on the solid base of nearly 40 years of experience in airjet weaving, during which over 100,000 airjet machines have so far been shipped. OmniPlus-i combines this extensive airjet expertise with a clear vision for the future!
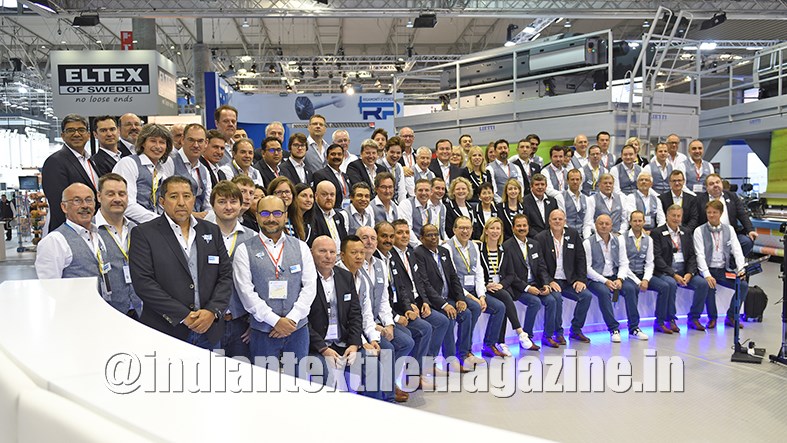
OmniPlus-i features a redesigned reed motion, an optimized relay nozzle set up, and it can be combined with Smart Shed, which is the full electronic-controlled shedding motion.
At Picanol, we believe that in this fast-changing world of weaving the needs of weaving mills in general and the expectations of our customers and their operators are evolving rapidly. Our market is now driven by an increasing concern for environmental topics, higher costs and the lower availability of resources and skills, as well as the digital revolution that is affecting all industries.
This is why the OmniPlus-i was built around our four leading design principles:
- Smart performance
Picanol machines have always been built for maximum performance, and this will always be the case. Nevertheless, Smart Performance focuses on ensuring the highest industrial speeds in the market, even under difficult conditions.
We have realized this in the new OmniPlus-i, thanks to a completely new reed motion whereupon more insertion time permits the smooth handling of even less-than-perfect yarns.
- Sustainability inside
The further reduction of energy consumption is not an optional extra; it has to be embedded in the machine design. With its modified relay nozzle distance, the new OmniPlus-i offers more stable insertion and consequently new possibilities for the further reduction in air consumption, even by automated algorithms. In other words, sustainability is inside.
- Driven by data
Picanol has pioneered the digitization of weaving machines for many decades now. SmartShed – the fully electronically controlled shedding motion which is incorporated in the new OmniPlus-i – is a logical next step in this evolution. Together with an abundant use of sensors, this generates lots of data that fuel real-time optimization algorithms and promises even further gains in productivity when combined with other data, even from other, different machines. Therefore, weaving with Picanol truly becomes Driven by Data.
- Intuitive control
Picanol machines are always designed to be as user-friendly as possible. Thanks to the new large interactive touchscreen and the new signal lamps on the new OmniPlus-i we are able to offer an enhanced level of Intuitive Control. This enables the weaver to navigate quickly and easily through all of the machine settings and adjust them, even without having to stop the machine.
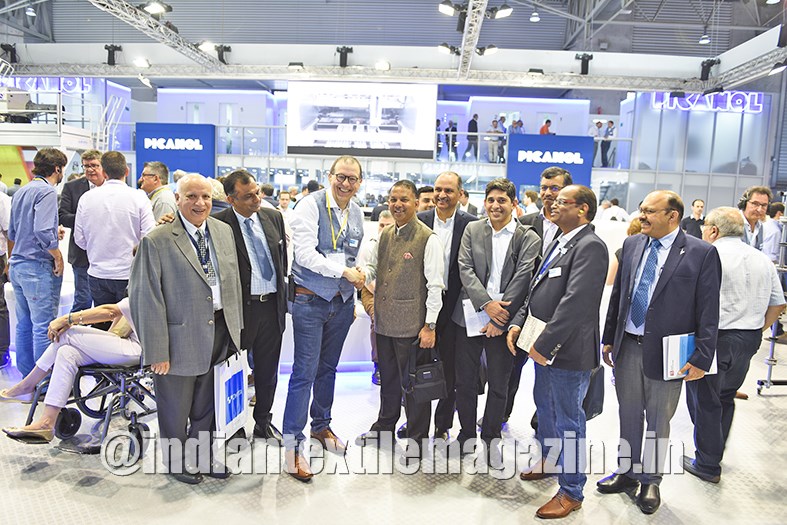
The major talking point about Picanol’s participation in ITMA was the digitised insertion on Rapier, particularly for denim fabrics. Can you elaborate more on this technology and how was it received by visitors?
We are undoubtedly witnessing a digital revolution in weaving that has been propelled by the wave of Industry 4.0. For this reason, as a pioneer in weaving as well as in electronics, Picanol has made it one of its four principles to be Driven by Data. By demonstrating an OptiMax-i weaving denim fabric with almost fully digitized insertion we were able to prove that this is not just a slogan.
As the major weaving machine supplier in the denim business, we are in the best possible position to find out the future needs of our customers. Together with our customers, we are able to work out solutions and make this revolution actually happen right away.
Therefore, we demonstrated a denim machine with insertion that has been almost completely digitized. Thanks to the integrated concept, all of the settings are available and these can be retrieved on the central microprocessor.
It starts right from the prewinders which are equipped with a tension display (TED). Having a digital setting of the brake on the prewinder not only gives the user a tension which is reproducible in the future, but it also enables the user to manage possible differences between prewinders in a much easier way.
The filling tension during insertion can be electronically controlled with the programmable filling tensioner TEC in order to eliminate possible tension peaks. The signals from the filling detector – either standard or SmartEye – are continuously monitored and analyzed by the machine’s microprocessor.
With the QuickStep filling presenter, different timings for the presentation, insertion and rest position can be programmed. While the QuickStep is not a new innovation, it remains the benchmark on the market.
New to this machine is the Electronic Right Gripper Opener (ERGO). Developed as a gripper opener to tune the machine for minimum waste length when weaving different types of weft yarn, the ERGO represents an additional step in the digitization of the weaving machine, enabling the possibility of full electronic setting of the right-hand-side gripper opener, even while the machine is running.
In addition to these “Driven by Data” features, we are also able to demonstrate an impressive “Sustainability Inside” capability, with the EcoFill in 4-color version which is installed on this OptiMax-i.
Picanol was the first machine manufacturer to eliminate the left-hand side waste ribbon on a rapier machine. This feature was first introduced in 2011 in a 2-color version aimed at technical fabrics. The Picanol system for a catch cord-free set-up on the left-hand side has been extended to a 4-color version, with no limitations for the designers in terms of, for example, color patterns. Furthermore, as the EcoFill settings are fully digital, this feature is also very intuitive to control.
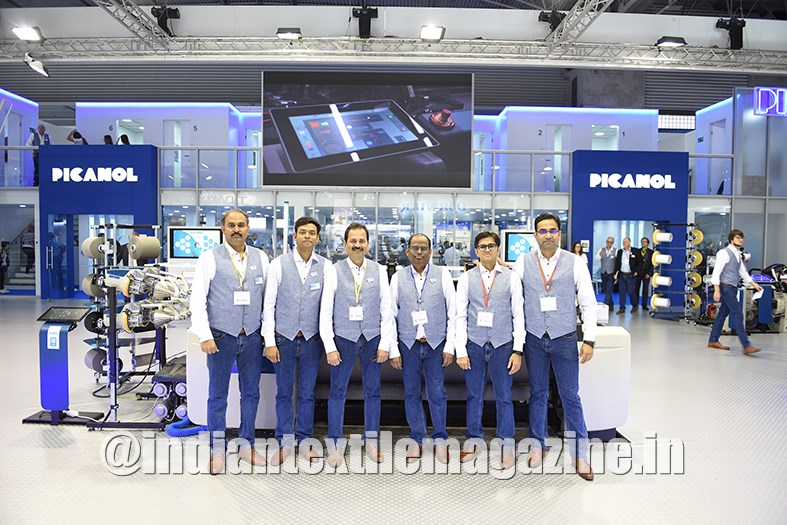
What are the other major highlights of Picanol’s participation at ITMA which impressed and attracted the attention of visitors the most?
We presented our latest developments in rapier and airjet technology. When it comes to rapier technology, Picanol has once again set the benchmark in various aspects. We have delivered the proof, on a denim application, that a machine can be performant, versatile, sustainable, digital and user-friendly at the same time! Our brand new airjet machine, the OmniPlus-i, was however the première we reserved for ITMA 2019 Barcelona. It is definitely the benchmark in airjet weaving. In total, Picanol had 12 machines on display at ITMA Barcelona: 5 airjet machines and 5 rapier machines at its booth. Furthermore, a rapier machine in Jacquard execution was on display at the Bonas booth and a terry airjet at the Stäubli booth.
An overview of all the machines shown at ITMA 2019, the styles woven, as well as the highlighted features can easily be found by using the brand new integrated Picanol App. This app has been designed to give everyone a clear overview and more in-depth information of everything that was on display at ITMA. Download it now and keep in touch with our latest innovations, read the latest news, experience Augmented Reality in weaving and make your life easier with our integrated weaving calculators. You can download the app via www.picanol.be/app.
Coming specifically to India, how was the representation from the Picanol India team at ITMA? How many Indian visitors came to the stall?
We had a Machine Sales team from India comprised of eight people that attended part of the show to receive Indian visitors and spend time explaining the new features to customers alike. Our team members are strategically located across different parts of India, including Ludhiana, New Delhi, Bhilwara, Ahmedabad, Surat, Mumbai, Kolhapur and Coimbatore. They help us serve India by ensuring they are very close to the market.
India is a big market for us and we have over 25,000 weaving machines installed in the country. Therefore, we obviously have a strong customer base in India. Most of the customers came from the north to south, central and western regions, which include the existing customers and prospects. There were many opportunities to discuss new projects and we were satisfied with the interactions.
Which are the technologies relevant for the Indian market?
Being a big country, India has presence in various fabric segments. However, machines displayed relating to bottom wear, denim, poplin and sheeting always attract considerable attention from Indian visitors, and we saw great interest when the machines were running at our stand at regular intervals. The major focus was on airjet machines due to the commodity product base Indian market, although synthetic suiting, Poly Viscose & wool were interested to find out more about new innovations regarding rapier weaving machines.
Another important development: Industry 4.0 and the emerging trends in automation and data driven approach to business. What is Picanol’s development in this direction?
Everybody is aware that digitization will become ever more important in the coming decades. Data has to be captured, made accessible and usable for both production optimization and artificial intelligence. Since the first introduction of electronics on weaving machines in the 1970s, Picanol has been at the forefront of digitization. With every new machine we develop, we continue to be a trendsetter in this field and we are committed to further deploying Industry 4.0 in the weaving industry. In this regard, the self-setting machine is just around the corner.
In order to emphasize our technological capabilities when it comes to capturing data from our machines, we demonstrated our PicCon App at ITMA Barcelona. This App enables us to retrieve a wide variety of data from the machines in a mobile way. We also had two large interactive screens at our stand to help our visitors visualize these possibilities and exchange ideas, together with our customers, on future applications.
Picanol recently achieved a milestone of 100,000 airjet machines sold globally? This is a great achievement? What would you attribute towards the success of Picanol’s Airjet machines? How important is the Indian market in this Airjet success story?
It was definitely a proud moment for us when the 100,000th airjet loom was produced. This OMNIplus Summum forms part of a larger order that was recently made by Naveena Export Ltd., Karachi, Pakistan.
Airjet weaving at Picanol started in 1980 following the release of the revolutionary PAT (Picanol Airtronic) weaving machine. The PAT was first presented at the ATME exhibition in Greenville (US) in the same year. This was then followed by the PAT-A, the Delta, the Delta-X, the Omni, the OMNIplus, the OMNIplus 800, and finally the OMNIplus Summum. Many customers around the world have been growing with us through all of these different generations of airjet machines.
Over the years, the market has understood and accepted that Picanol machines can be performant, versatile, sustainable, digital, and user-friendly at the same time! We were able to meet stringent quality standards for customers over the years and we always grow together with the market. Service is one of the most important criteria and our customer has given us extra preference thanks to our 100% subsidiary company, Picanol India Pvt. Ltd., which comprises over 40 employees in India for machine sales, service, the print repair shop, the After Market team, and the general administration team.
In recent years, the major share has gone to airjet rather than rapier weaving machines in India. Indeed, we had one of our biggest successes in India with our OMNIplus Summum machine. India is a very important market for us – and for this reason we created our subsidiary company in India in order to be in direct contact with our customers and to be aware of their needs. As we approach the 11th anniversary of Picanol India we are very happy with our decision to “go out on our own” and the results have proven we made the right decision at the right time.
Finally, going forward, aftersales service and spares are going to be very critical to the success of any machinery manufacturer. How is Picanol gearing up on its service infrastructure?
The Picanol Group has a dedicated After Market team that is available globally and in India, as well as three people who are strategically located – one each in Delhi, Mumbai and Coimbatore – and two CSRs in our Head office who are responsible for producing quotes for the aftermarket. We also have a fully equipped PCB repair shop in the Delhi office to repair prints from our new airjet and rapier weaving machines. Most of the cards are repaired in India and there are four electronic engineers available in the print repair shop who are trained by the Belgian team.
As regards India, we can say that Picanol India is the country’s largest sales and service team of weaving machine suppliers and we have kept adding employees with each passing year in order to maintain a long-term focus on the Indian market.