Coimbatore-based Indo Texnology has been creating ripples in the market with its automatic cone packing system. A team from The Textile Magazine visited one of the company’s client – Lucky Yarn Tex to take a closer look at the system in operation. Lucky Yarn Tex’s success story with Indo Texnology’s automatic cone packing system is a beacon for other mills, urging them to embrace automation and spin their own tales of winning efficiency and quality.
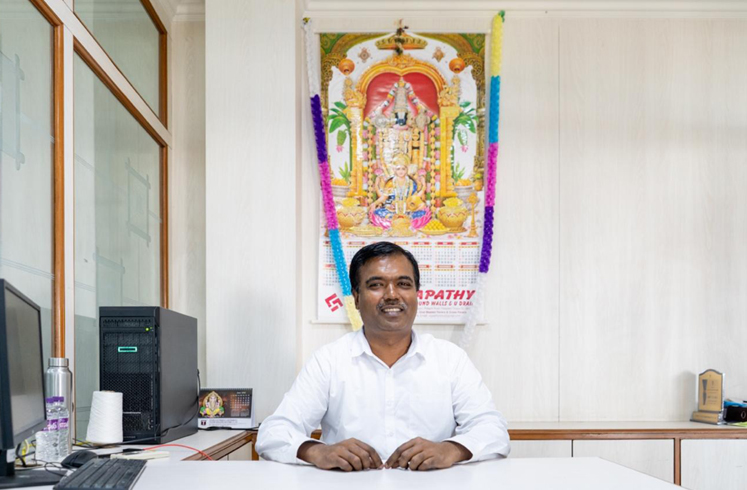
For decades, the final chapter of yarn production – packing – remained stubbornly stuck in the manual age. Labor-intensive, monotonous, and prone to human error, packing presented a unique challenge for spinning mills. But for Lucky Yarn Tex, turning the page on manual packing proved to be a game-changer.
“In the four stages of yarn production, packing required the highest manpower,” explains Mr. Kumaraguruparan, Vice President at Lucky Yarn Tex. “Managing this department with its dependencies on skill, accuracy, and consistency was a constant headache.”
Enter automation
By embracing an automatic cone packing and cone inspection system, Lucky Yarn Tex spun its way to a new era of efficiency and quality.
The benefits, as Kumaraguruparan enthusiastically testifies, are manifold:
- Avoids excess weight in packing. Complete weight control is achieved by setting our weight tolerance on the packing machine. This avoids packing excess or lower weight in the bags.
- Eliminates mix-ups and defective cones to be packed. The artificial intelligence based cone inspection system ensures count mix-ups and packing of defective cones does not happen.
- Cones travel first-class. Damage during transit is eliminated after implementing the automatic cone packing system.
- Data Accuracy: Integration of packing details through an ERP system ensured zero errors in data entry.
- Tracking and Tracing: QR coding and stickering facilitated precise monitoring of produced bags.
- Uninterrupted Operations: Absenteeism, once a production disruptor, no longer throws a hassle in the packing process.
- Online packing eliminates cone stocking, further contributing to productivity.
- Productivity soars: Minimal manpower requirement after automating the packing process.
- Savings pile up. Elimination of cone inserts not only reduces material costs but also saves precious time and manpower.
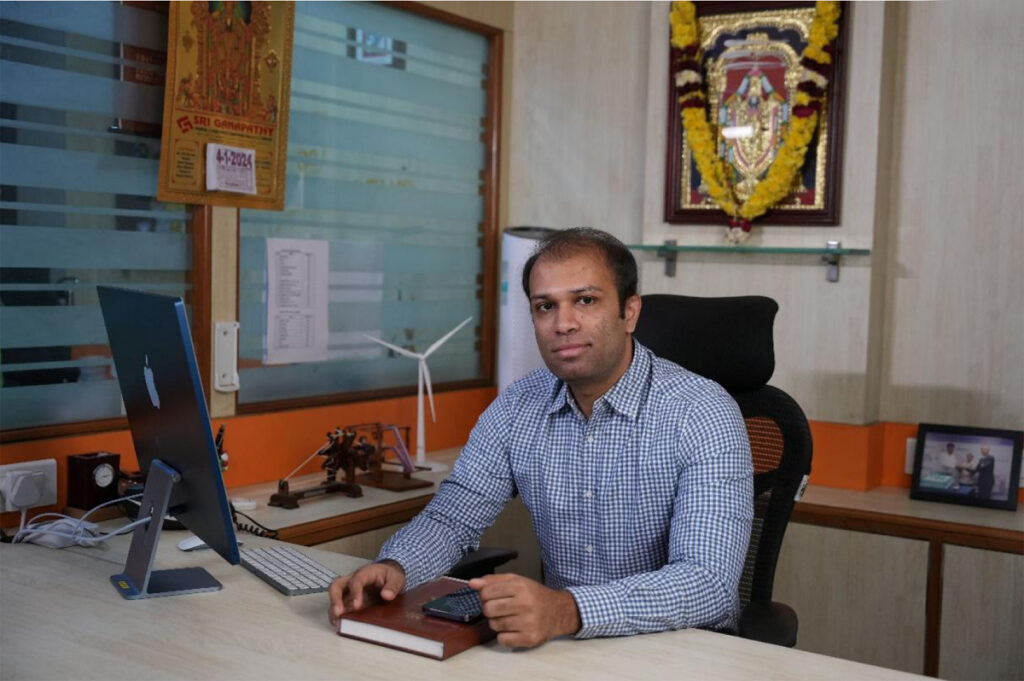
Beyond the Bottom Line:
The impact extends beyond numbers. Kumaraguruparan notes, “My customers started appreciating the packing quality.” Packing, it seems, has become a point of pride for Lucky Yarn Tex, reflecting their commitment to delivering excellence in every thread. But the story doesn’t end with packing perfection. To guarantee flawless yarn reaching the market, Lucky Yarn Tex deploys Indo Texnology’s Cone i – an AI-powered cone inspection system. Defective cones with stitch problems or yarn variations are seamlessly identified and removed, ensuring zero tolerance for imperfections in packing.
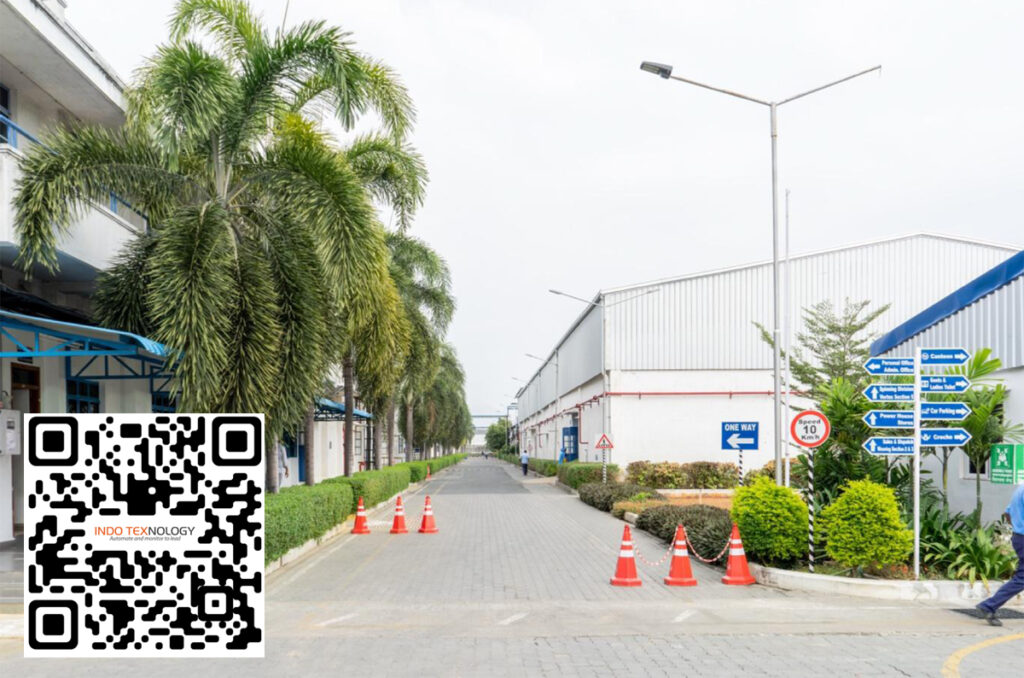
Integration and Intelligence:
Data, the lifeblood of modern manufacturing, finds its place in Lucky Yarn Tex’s automated ecosystem. Packing details are seamlessly integrated into their ERP system, eliminating data entry errors and ensuring complete transparency. QR code and stickering systems further enhance traceability and monitoring, allowing the mill to track every bag from creation to destination. Eight months into their automation journey, Lucky Yarn Tex has woven a compelling narrative of success. They’ve spun a web of efficiency, eliminated quality nightmares, and emerged as a shining example of how embracing technology can transform the textile industry.
Their story serves as an invitation to other mills – a call to action to rewrite the final chapter of yarn production with the precision and innovation of automation.
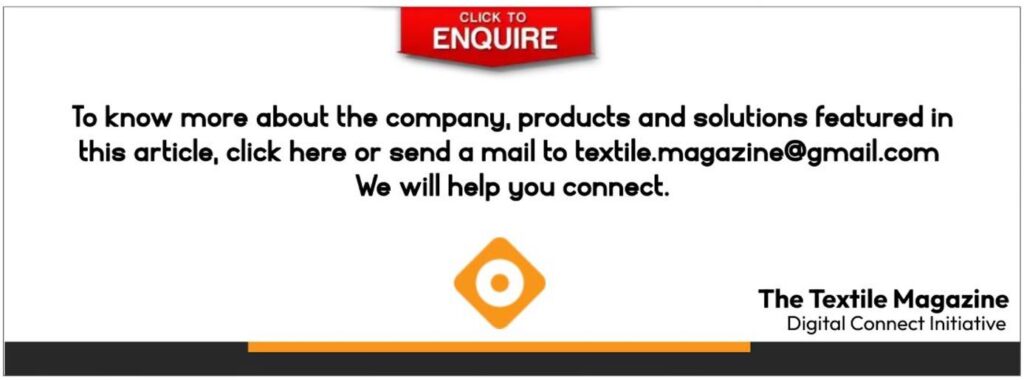