By Yvan Schwartz, Head Product Management Combing, Winterthur
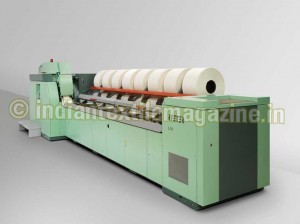
With the launch of the E 80 comber, Rieter is again shifting the boundaries of what is possible in combing. New superlatives in performance are being achieved in terms of quality, output and economy.
Flexibility is the ability to adapt to changing circumstances and conditions. Flexibility is essential also in spinning mills which must be able to respond quickly to changes in the market or raw material. The new E 80 comber (Fig. 1) supports the customer in this as never before.
For the first time in the history of high-performance combing, the improved combing geometry of the E 80 comber enables a 130° circular comb (Ri-Q-Comb) to be used without having to make concessions in the nip rate. 130° means an increase in the combing area of some 45 per cent compared to the predecessor model (90°).
The possible increase of up to 60 per cent in the number of points per circular comb that this brings enables the fibers to be combed out even more thoroughly than with the 90° circular combs used to date. The result is a high-quality combed sliver which is reflected primarily in an improvement in yarn quality. Customers can thus choose whether they wish to exploit this quality advantage (E 80 Quality) or to convert it into higher output (E 80 Productivity) or improved raw material utilization (E 80 Yield).
As for E 80 Quality (Fig. 2), in principle the focus in combing is on refining the raw material and thus improving the end product. No spinning mill would comb and accept a relatively high loss of material if no significant enhancement of yarn quality were to be achieved as a result.
The E 80 focuses precisely on this point. The new comb geometry enables yarn quality to be improved by up to 20 per cent compared to the predecessor model with the same output (Fig. 3). No other comber available in the market permits this symbiosis of superior quality and high economy at the same time.
E 80 Quality thus stands for higher quality with unchanged productivity and noil extraction compared to the E 66 / E 76 predecessor model.
The main advantages for the customer are up to 20 per cent fewer imperfections compared to the E 66 / E 76 comber, up to 30 per cent fewer imperfections compared to other combers on the market, maximum uniformity of the finished goods, and greater flexibility in the choice of raw material.
With E 80 Productivity (Fig. 4), references to combing output to date primarily meant the number of nips per minute. The fact that the batt weight and feed rate are at the same time also equally important factors with regard to a comber’s production performance was usually neglected.
With the advent of the E 80 there is again more emphasis on these two factors. The improved combing technology of the E 80 means that there is no longer any barrier to using a higher feed rate, i.e., the quantity of lap now fed per nip. Output can therefore be increased in an energy-saving and economical manner without also having to compromise on the quality achieved to date (Fig. 5). A finer subdivision of feed rates also helps to enhance flexibility still further.
In conjunction with a high batt weight of up to 80 g/m, depending on raw material, the E 80 achieves production figures of up to two tonnes/day, which have been out of reach in practice to date.
The productivity of a comber can also be improved by the use of large can formats or automated lap piecers. It has recently become possible to use cans 1,000 mm in diameter exclusively with Rieter combers. This halves the number of can changes and thus reduces operator effort by some 10 per cent. Together with the familiar and unique ROBOlap automated lap piecing system, this enables machine efficiencies of up to 96 per cent to be achieved.
The advantages for the customer are up to two tonnes/day of combed sliver, up to double the output compared to other manufacturers, a superior price/performance ratio and up to 10 per cent lower labor costs.
Now about E 80 Yield (Fig. 6). The largest cost factor in combing is fiber waste. In times of widely fluctuating cotton prices the quantity of noil removed during combing is therefore of even greater economic importance. The less material has to be combed out to achieve the required level of yarn quality, the more economically a combed yarn can be produced.
The E 80 offers a unique advantage here, since the achievable improvement in yarn quality can be converted into raw material savings of up to two per cent compared to the predecessor model (Fig. 7). Compared to other combers available on the market, raw material savings of as much as four per cent can be achieved.
The larger combing area and the increase in combing action associated with this also enable raw material of lower quality to be used, depending on the application, without having to make concessions on the quality produced to date.
Here the advantages for the customer are upto four per cent raw material savings compared to other manufactures, up to 20 per cent lower yarn manufacturing costs, high material utilization and up to 10 per cent lower energy costs.
The E 80 brings an enormous increase in flexibility in combing (Fig. 8). The three options – E 80 Quality, E 80 Productivity and E 80 Yield – can also be combined at any time. This enables the correct blend of quality, output and economy to be selected individually for each product and each customer.