Rieter develops and manufactures machinery, systems and components used to convert natural and man-made fibers and their blends into yarns. The company is the only supplier worldwide to cover the complete spinning process across all technologies established on the market. With 15 manufacturing locations in ten countries, the company employs a global workforce of some 4 400, about 20% of whom are based in Switzerland.
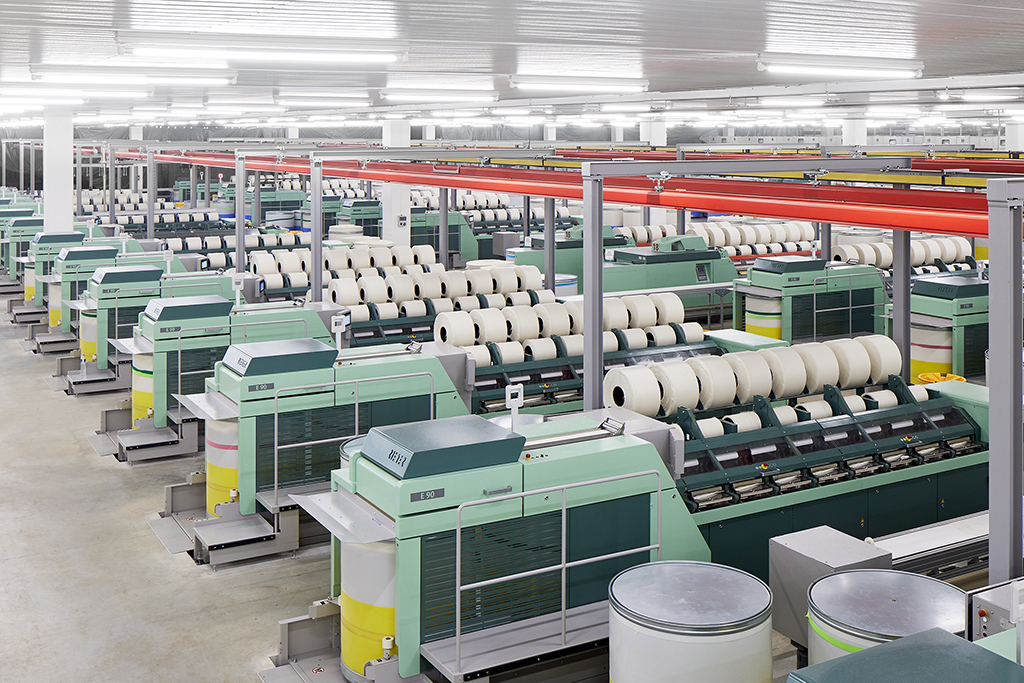
Rieter offers customized spinning systems thanks to a broad range of products and services for every customer requirement: This is how the company provides spinners the chance to achieve maximum profitability and competitiveness – throughout the mill’s entire service life.
Rieter’s product portfolio is unique (Fig. 1), covering the complete spinning process across all technologies established on the market. Building on centuries of experience, the company offers extensive technological expertise from fiber to yarn and even through to the textile fabric. Rieter customers can always count on having only a single contact person in charge of all their needs.
After installing Rieter machines, the company offers trainings so that customers can unlock the full potential, achieving efficient and profitable production and correct maintenance. As a matter of course, customers benefit from advantageous upgrades, high-quality parts, and service packages designed to increase production.
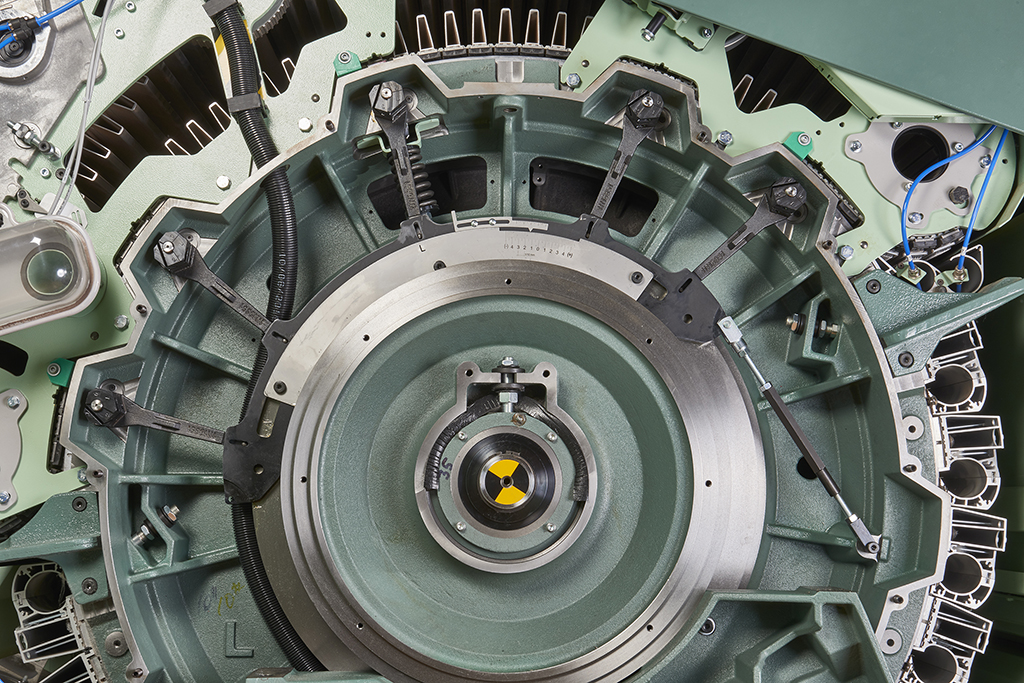
Choosing a Rieter system means that customers get much more than just the sum of the parts. They can produce the right yarn in consistent quality and at competitive costs. What is more, better raw material utilization, significantly lower energy consumption as well as less space and personnel requirement give rise to additional cash flow, an important business metric.
Digitization
ESSENTIAL – the Rieter Digital Spinning Suite – helps spinners to get the most out of their spinning mill. The all-in-one mill management system monitors and analyzes data over the complete spinning process, shows potential areas for improvement, identifies abnormalities and their root causes, and predicts failure. It integrates Rieter’s digital offerings, provides customized interfaces to ERP systems and connects third-party machines and all auxiliaries that influence the production of yarn. ESSENTIAL is a modular system. According to their needs, customers can add the modules individually. ESSENTIALbasic is the starter module and is available free of charge for all Rieter customers. This module includes solutions such as the Rieter calculator, ESSENTIALorder, and ESSENTIALconsult.
After Sales
Rieter accompanies customers’ equipment throughout its lifecycle by providing original parts and modernization solutions. Through premium and innovative parts, Rieter maintains and even enhances the original performance of existing spinning machines.
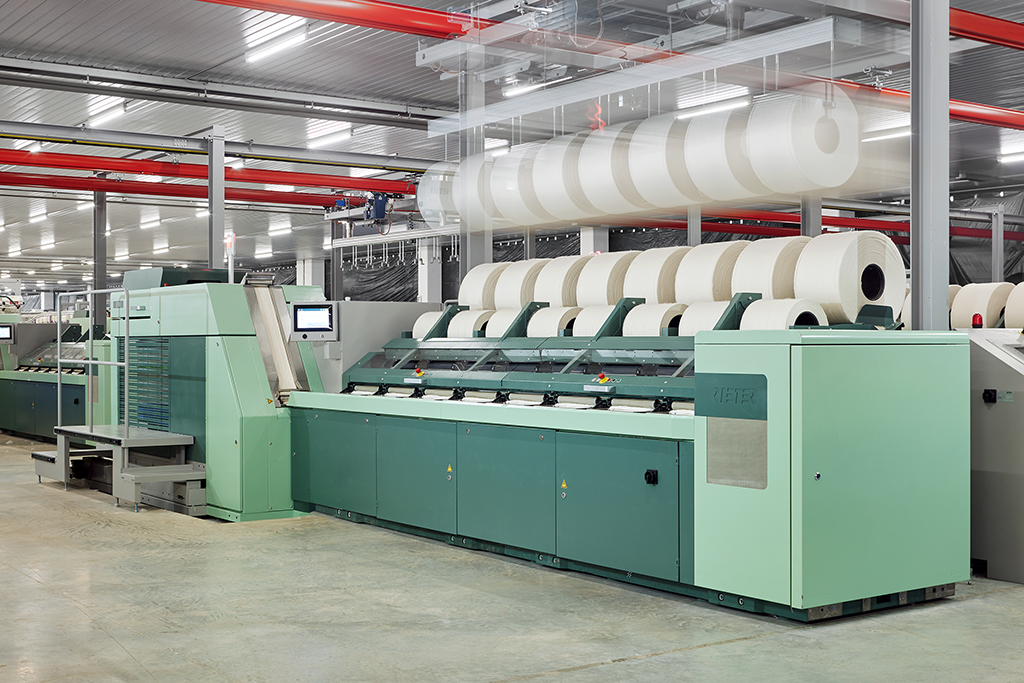
Services
Rieter deploys specialists around the world to help customers achieve success. From installation through to repairs and training, Rieter’s specialists are always at hand to assist customers in growing their sales and business.
Components
The component manufacturers of the Rieter Group – Bräcker, Graf, Novibra and Suessen – provide key components suitable to produce short- and long-staple fiber yarns made of natural, man-made fibers or blends. The components are available for both spinning mills and machinery manufacturers and are supplied for new and existing machinery alike – without any compatibility issues. Top quality components for the twisting operation and the nonwoven industry complete the product line. The latest innovations are the CARBO ring traveler from Bräcker for highest demands in man-made fiber spinning and the new Solidring from Suessen for rotor spinning designed to reach the best yarn quality with the longest lifetime.
Furthermore, with SSM Rieter is a leader in the field of precision winding and texturing machines.
Tried and tested innovations
The high-performance card C 80 has been completely revamped and now sets a new benchmark in terms of quality, productivity, and energy saving (Fig. 2). It has a carding length of 3.2 meters and its 40 engaged flats spread over a 1.5-meter working width. This creates the basis for a significant increase in production that also achieves optimum sliver quality.
The draw frame module RSB-Module 50 can be used in combination with the high-performance card C 80. The RSB-Module 50 can be configured to a highly efficient direct process with the new semi-automated rotor spinning machine R 37 or the fully automatic rotor spinning machine R 70. Both machines are characterized by low energy consumption, high productivity, and high machine availability with low raw material costs.
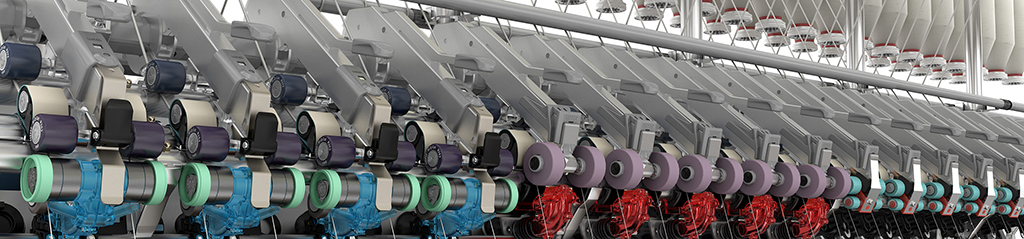
Several new machines have demonstrated stellar performance in the field, increasing the cost-effectiveness of the ring spinning and compact-spinning process: the comber E 90, the roving frame F 40, the piecing robot ROBOspin for ring spinning machines (Fig. 3). The compacting devices COMPACTapron, COMPACTdrum and COMPACTeasy allow production to easily switch between ring and compact yarn by simply plugging the devices in or out. This offers great flexibility in the face of fast changing market requirements. The compacting devices are impressive thanks to innovative technology, excellent yarn quality and low energy consumption. They can be incorporated into the specifications for new ring spinning machines and are supplied as part of the machine. Machines that have already been installed can be retrofitted easily (Fig. 4).
All these innovations combined help make the difference for our customers as they reduce raw material, energy and labor costs while increasing productivity and flexibility in the spinning mill.