CLEANtube – the option for intelligent control of the coiler speed on the Rieter draw frames – prevents trash particles and short fibers from accumulating in the sliver duct. The result is a mouse-free sliver that assures constant quality and reduces not only operator work but also the amount of waste and the number of ends down.
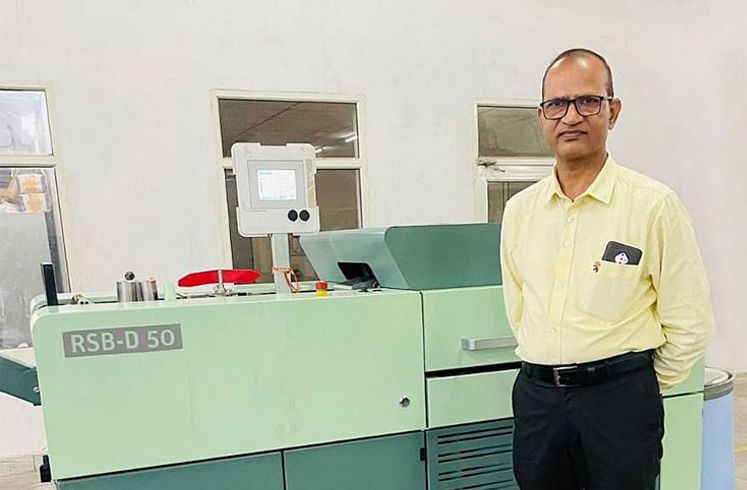
When processing waste- and noil-rich blends on a draw frame, trash particles and short fibers can accumulate in the sliver duct of the coiler during can filling. Once the can is full, the draw frame stops and this accumulation, known as “mouse”, comes to rest on the top sliver layer. This can cause trash deposits in the rotor groove, which in turn result in ends down in spinning. If the mouse gets into the yarn, it causes significant yarn and fabric defects. To avoid this, the mouse is usually removed by the operator which causes additional work & generates soft waste.
CLEANtube – coiling without trash accumulation
CLEANtube ensures that the sliver touches all surfaces of the coiler tube and, thus, keeps it free of accumulations. Pratap Singh Chouhan, General Manager at Gupta Threads states: “CLEANtube is an excellent feature of the Rieter draw frame RSBD 50 for mouse-free sliver which results in quality assurance while reducing the operator’s workload”. The CLEANtube function of the RSB-D 50 ensures consistent sliver quality and keeps the spinning process at a high efficiency level. It also ensures good quality.
In-mill study shows advantages of CLEANtube
Founded in 2012, Gupta Threads Ltd. is based in Samana, District Punjab, India. In their spinning mill with 3 744 rotor spinning positions, they produce 100% cotton yarn with a count range from Ne 7 to Ne 30. The raw material used is mainly a blend of 60 to 70% waste or comber noil along with 30 to 35% cotton.
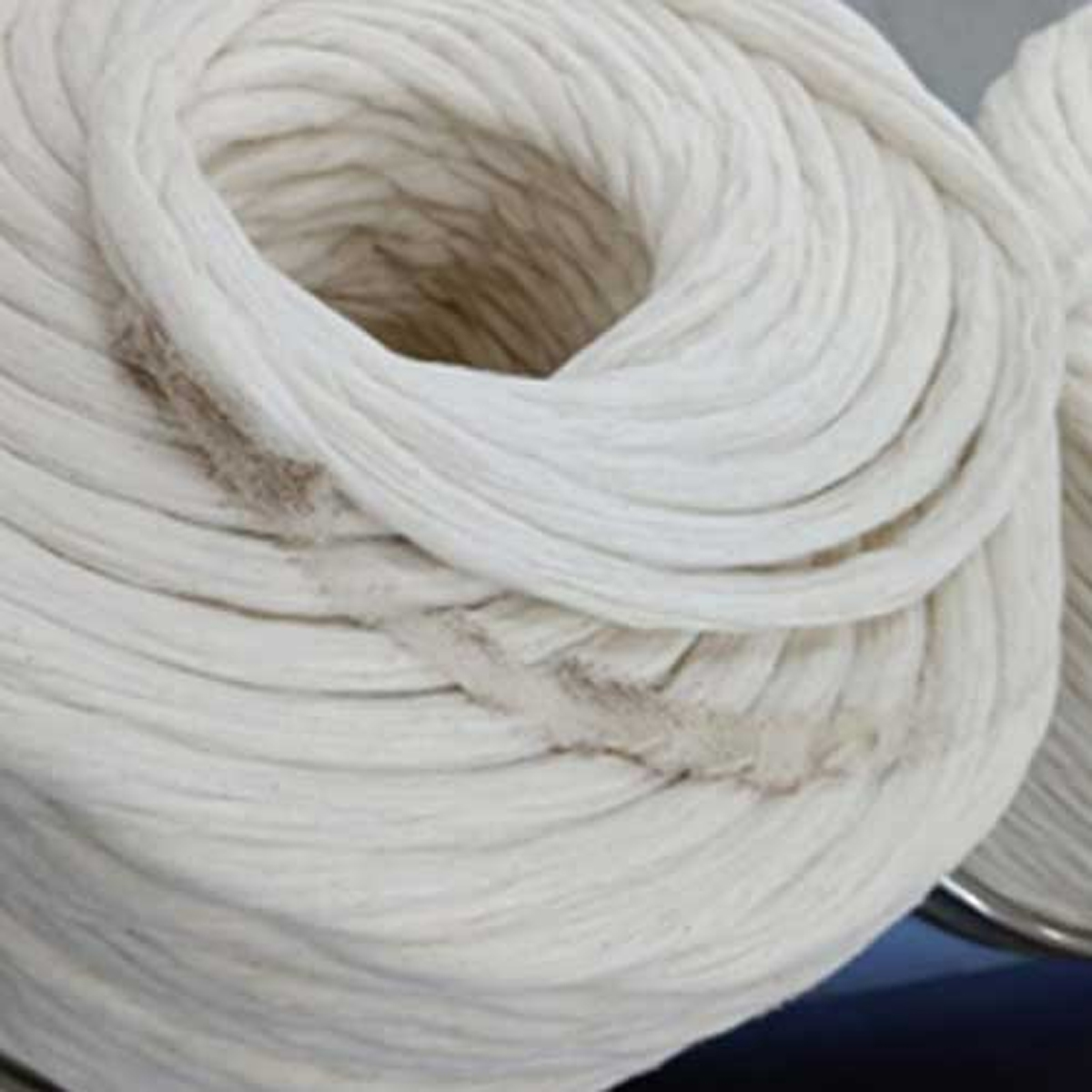
An in-mill study at Gupta has shown the following advantages using CLEANtube:
- 500 work-hours can be saved per draw frame per year as the operator no longer needs to remove the mouse manually.
- When removing a mouse by hand, the operator typically takes away about half a sliver layer. This corresponds to about ten meters in length. Even if it can be reused as soft waste it leads to additional conversion costs in blowroom, carding and drawing – those further expenses of up to EUR 1 300 per year and RSB can be saved.
- By eliminating the mouse, ends down are reduced. Approximately around every tenth mouse results in an ends down at the rotor spinning machine.
- Spinning a mouse into yarn leads to an increase in yarn mass of up to 100% with a length of about six meters. Finally, these defects are clearly visible in the woven fabric and mean a high risk of rejection of the fabric. Such financial damages are avoided.