Targets a million spindles by end of 2017
In April 2016, the first Made-in-India Zinser ring frames manufactured at Saurer’s Indian plant was delivered to Morarjee Textiles Ltd. With a total of 1,824 spindles, the ZinserImpact 72 latest-generation compact spinning machine was an impressive testament to the successful entry of Saurer into the Indian market.
Mr. Ashok Juneja, Director of Sales & Service for Saurer Schlafhorst and Zinser (India), and his team officially handed over the first machine to Mr. R.K. Rewari, Managing Director of Morarjee Textiles. Saurer has bagged an order for 40,000 spindles from Morarjee Textiles.
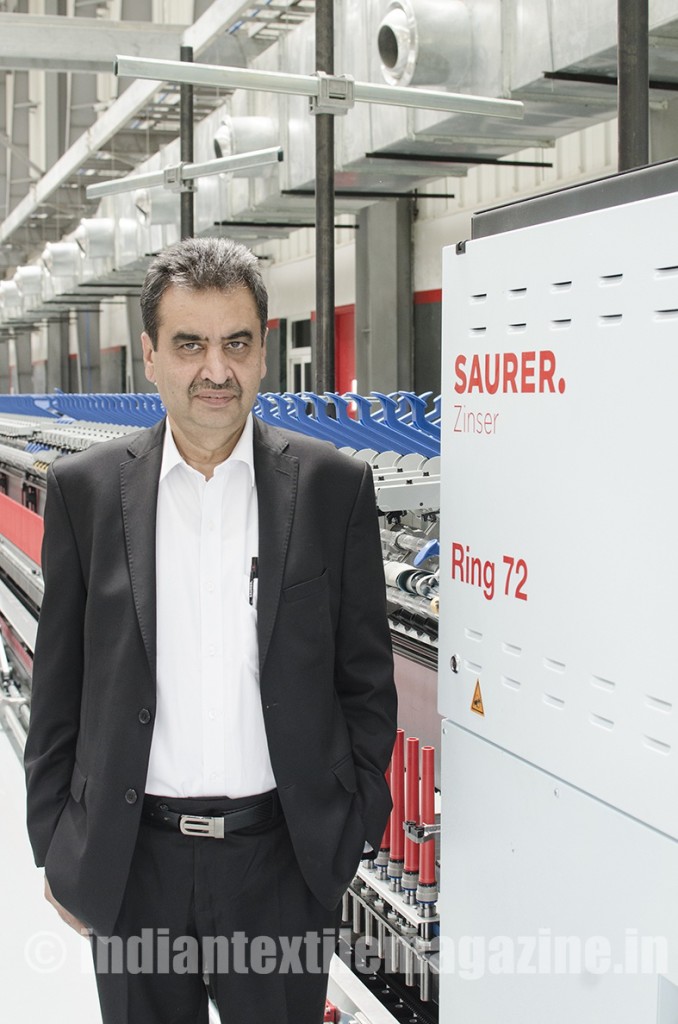
The setting up of a full-fledged manufacturing facility marked a big step forward for the 160-year-old Saurer brand in the Indian market. After going through changes in ownership in the last decade, Saurer is finally part of the Jinsheng Group of China. While many raised doubts on the future of Saurer under the Chinese ownership, the company has actually done very well in the last three years.
The Saurer Group unites the spinning brands Schlafhorst and Zinser, the twisting brands of Allma and Volkmann, pre-spinning brand Jintan and the Saurer Embroidery brand along with the Saurer Components Division consisting of the brands Accotex, Daytex, Fibrevision, Temco and Texparts.
With annual sales of around 1 billion EUR, 4,000 employees worldwide and locations in Switzerland, Germany, the UK, Czech Republic, Turkey, Brazil, Mexico, the US, China, India and Singapore, the group is well positioned to serve the world’s textile industry centres.
MAKE-IN-INDIA
With its significant presence in spinning, Saurer quickly listed down priority markets globally and identified India as one of the most important destination for investment and future growth. Accordingly, the company decided to set up a manufacturing facility in India and purchased land near Vadodara, Gujarat, in November 2014. In less than 10 months, the new facility was ready. It clearly demonstrated the commitment of Saurer and the Jinsheng Group to the Indian market, marking the beginning of a new chapter for Saurer in India. The company has invested Rs, 120 crores on its Indian plant.
The new plant located at Karjan near Vadodara aims to strengthen Saurer Group’s operations in India, catering to demands in the domestic as well as the International export markets. The Indian plant will allow the Saurer Group to blend German technology with Indian experience and provide customers with the latest generation of world class products combined with passion for innovation and quality – and close to the customer.
The Indian spinning industry is undoubtedly the largest with fierce competition among the domestic and global machinery manufacturers. LMW, Rieter and KTTM are present with very high level of localization. Given the scenario, it was always a challenge for Saurer to sell the Zinser ring frames by importing them. Hence it was a logical step for Saurer to set up a plant in India and localize the components so that they are in a position to compete with the rest.
Whereas a considerable part of the machine is already manufactured in India, either by Saurer or external supplier, some key components are still being imported. With a high degree of localization and the closeness to customers, Saurer is confident that it can offer a superior next-generation technology machine at competitive prices.
Global hub for ring spinning
Saurer has some big plans for the Indian market. In the initial stage, the Saurer India plant will manufacture the Zinser models 71 and 72, both for conventional and compact ring spinning. The target for capacity is over one million spindles per year and the ramp-up is going very well.
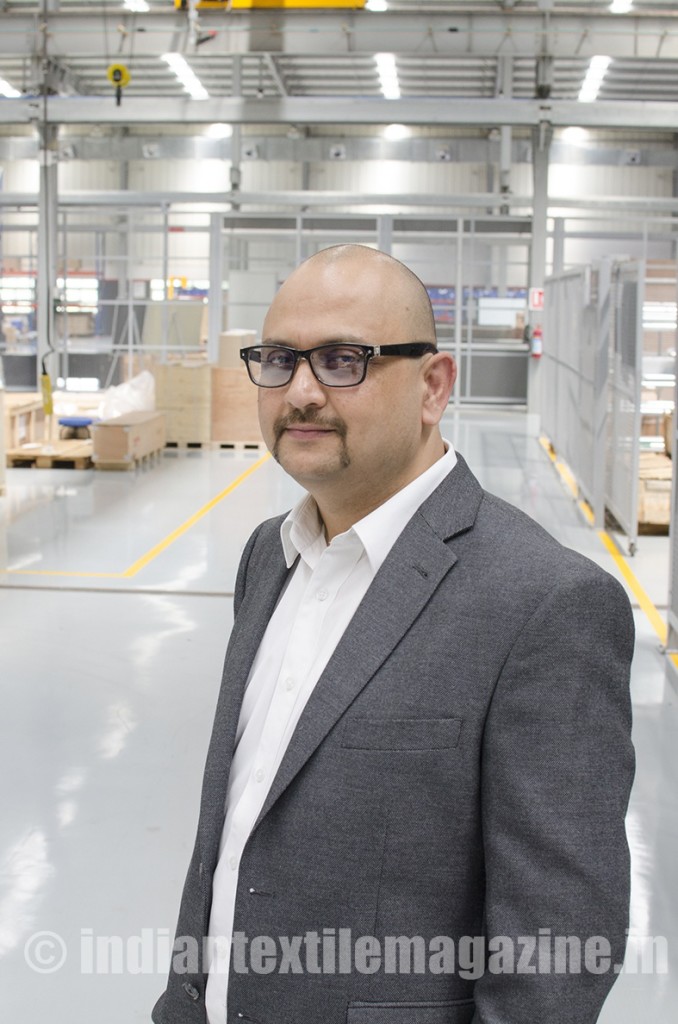
At a length of 2.016 spindles, the Zinser 72 ring spinning machine breaks the 2000-barrier and sets new standards for efficiency in the commodity business. The machine is super-long, super-economical and extremely user-friendly. It lowers production costs by up to 11% and has a footprint that is up to 21% smaller compared with shorter rival machines. The new both-end TwinSuction system saves two-thirds of the energy consumption in the suction process in combination with the sensor-controlled OptiSuction yarn break suction system.
Saurer is planning to make India one of the major hubs for ring spinning machines. The Indian plant will manufacture machines for the domestic market and global markets. The company has already received the first orders for ring frames from Turkey and South America and these machines will be delivered soon.
The new Saurer plant, spread across 85,000 sqm of land, houses world-class production facilities for two premium ring spinning brands of Saurer: Zinser & Texparts. The new facility also includes a sourcing hub for the whole group and a central service hub, and is built to cater to demands in the domestic as well as international export markets. Out of the total area of 21 acres only 50% has been utilized and the balance space is available for future expansion.
Next step would see all the variations of Zinser ring spinning machines and superior automation to be produced at the facility making Zinser the only ring spinning machine manufacturer with 4 ring spinning technologies: conventional short staple, compact short staple, conventional long staple and compact long staple. This is also complementing the already existing Zinser speed frame production in India allowing attractive packages, including automation.
Saurer is currently working on the next generation Zinser 7 model which will set new standards in ring spinning. The Zinser 7 model is being jointly developed by the R&D team in Germany and in India taking inputs from domestic customers.
Saurer Texparts
Components’ is a key part of the overall investment made in India. Since 2008 Saurer already had its Saurer facility in rented premises in Halol. The Indian facility manufactures for the local market PK 2025+ weighing arms and CS1 Spindles with a doubled capacity and would in the future also include the addition of other components within the premises. Saurer Zinser and KTTM (Toyota) are major customers for component supplies in India. Saurer Texparts also supplies to customers across all machine types in the replacement market. Saurer Components has doubled its capacity after moving from Halol to Karjan.
Texparts is the clear technology leader offering highest quality weighting arms for all machine types and all processes, from speed frame and short staple to long staple weighting arms for worsted ring frames. Next to weighting arms, Texparts also manufactures high speed spindles in India, catering to the high end spinning market in India where spindle speeds >20,000 rpm are the rule rather than the exception.
India is one of the most important ring spinning markets in the world. With the establishment of a new facility in Vadodara, Saurer is in a better position to cater to its customer needs. Being close to the customer is essential for speed and the Indian location not only allows Saurer to supply to the Indian market but also to the essential South-East Asian markets. The Saurer Group has always been driven by the passion for its customers, and consistently invests in innovations that foster customers’ profitability.
The Indian textile market is highly sophisticated with challenging customers. The new project in India will allow Saurer to blend German technology with Indian experience and provide customers with the latest generation of world class products combined with our passion for innovation and quality.
Rotor spinning and winding machines
Saurer is a global leader in rotor spinning and winding machines. In India, Saurer enjoys very strong presence with its semi-automatic and fully automatic range of machines.
The fully automatic Autocoro 9 machine with its intelligent individual spinning position technology sets new standards for energy-saving yarn manufacturing, productivity, economic efficiency, ease of operation and quality. The machine outperforms its legendary predecessor with conventional technology with sensational output data. 25% lower energy consumption, up to 30% more productivity, proven rotor speeds of up to 180,000 rpm, take up speeds of up to 300 m/min and a 60% lower servicing outlay. The Autocoro 9 is thus the production platform of the future.
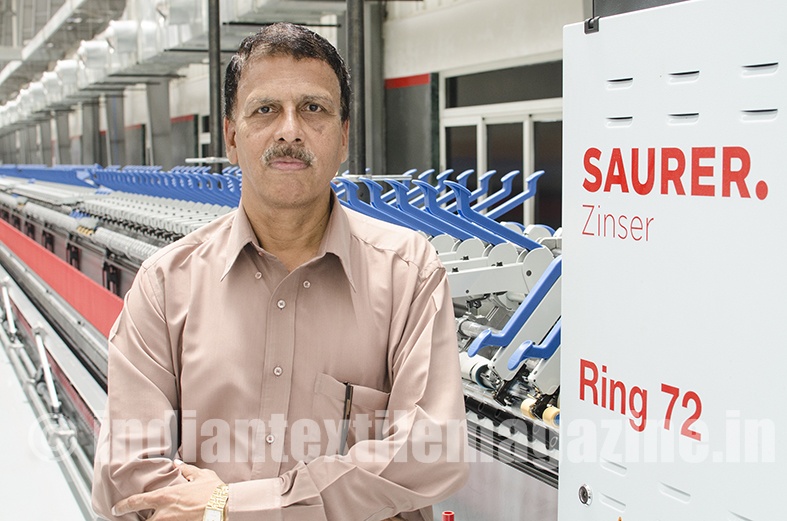
The new semi-automatic BD 7 machine, which has been launched at ITMA Asia 2016 is also in a league of its own, producing packages in Autocoro quality across the entire range of yarn counts and with package sizes of up to 320 mm in diameter. Its low energy consumption, rapid take-up speeds of up to 230 m/min and high piecing reliability cut spinning costs and increase the profitability of spinning mills.
Intelligent sensor technology and smart process control turn the new Autoconer 6 into an automatic package winder that pushes the textile-technological limits, means winding at the most productive level. Innovations such as LaunchControl, SmartCycle and SmartJet boost productivity by up to 6% compared with the previous model.
The new Eco-Drum-Drive system, SmartCycle and the intelligent vacuum control system “Power on demand” reduce energy consumption on the Autoconer 6 by up to 20%. Unique features like autocalibration of splicer feeder arm and intelligent doffer functions like SmartJet and TubeCheck make winding more ergonomic and so independently of personnel. Also the Autoconer 6 sets the benchmark for package quality and added value in downstream processing. This is true both for commodity applications by new basic functions and for the very sophisticated demands of high-end applications, using the high-tech FX modules.
The new Saurer Group has also recently entered into a joint venture with the Premier Group of Coimbatore for manufacturing yarn clearers.
Saurer recently acquired A.T.E.’s stake in Zinser Textile Systems, making it a fully-owned subsidiary. The plant at Ahmedabad manufactures high quality roving frames ZinserSpeed 5A and 5M.
Service
The success of Saurer in India is based on service. One of the major customers in India who does process audit of its facility every year has rated Saurer as the best in service. Saurer is catering to over 1,000 customers across India with a team of 125 service people in India. The company has three full-fledged repair centres at Mohali, Ahmedabad and Coimbatore.
Saurer also has a complete stockyard for spares at Coimbatore and another warehouse for ring frame spares at Ahmedabad. Saurer has also set up a Technology centre in Coimbatore which helps connect with all its customers. Customers, who would like to see demonstration of its machines or do some trial runs, be it ring frames, open end or winders, can make use of the facility at Coimbatore. The technology centre can also be used for training of customer’s employees on the various machines.
As for its vision for 2020, the company would like to have more products manufactured in India, increase global sourcing of components and achieve an annual output of million spindles out of India.
Saurer Group appoints new global leadership team
Saurer has announced the appointment of Clement Woon as CEO and Jesse Guan as COO of the Group. This adjustment is intended to prepare the group for its next phase of development. Dr. Martin Folini will continue to be engaged with Saurer in a consulting role.
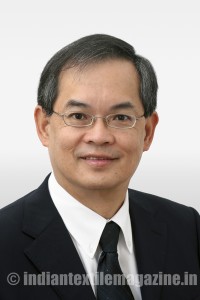
Clement Woon is a Singapore citizen and was co-CEO and co-President of the Jinsheng Group. He has the proven ability in the strategic development of multi-businesses firms to ensure growth and profitability. In the past, he was active as CEO of Oerlikon Textile, President and CEO, SATS Ltd., a public-listed Singapore Company and President of Leica Geosystems Division, a Swiss firm.
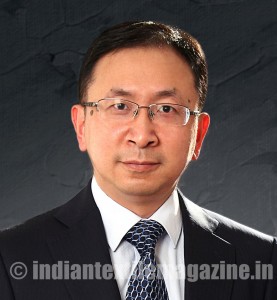
Jesse Guan, a Chinese citizen, has been working for Jinsheng since 2011 and was Co-President & Executive President of the Jinsheng Group. He brings in a variety of experiences to the Senior Management and had full P&L responsibility in industrial MNCs (such as Ingersoll Rand & TI Automotive) for product & manufacturing focused businesses in Asia.
By K. Gopalakrishnan and Ganesh Kalidas