JP Modatex is promoted by Mr. Jindas Pukhraj Jain and Mr. Rakesh Kumar Sharma, who come with strong background in yarn manufacturing and trading for more than three decades.
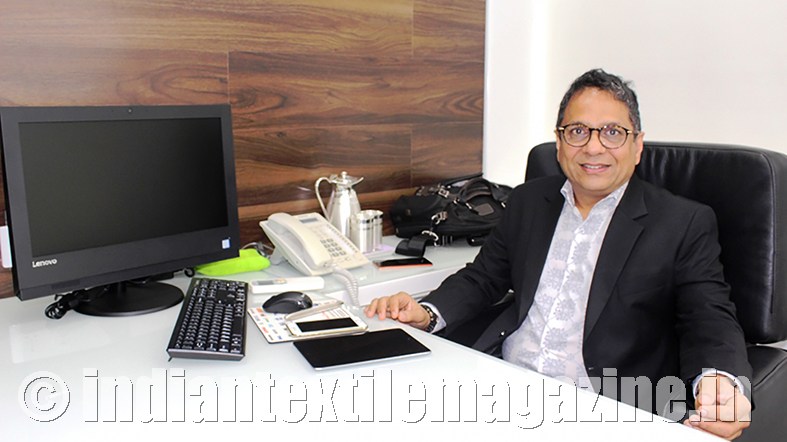
JP Modatex’ state-of-art manufacturing unit at Silvassa commenced production in October 2016. With a strong sales and marketing network covering Mumbai, Bhiwandi, Surat and Ichalkaranji, the company proposes to expand into Bhilwara, Tirupur / Erode and Amritsar / Ludhiana.
The product mix of JP Modatex is of speciality cellulogic-based yarns – Modal, Lyocell, linen, cotton and blends of all these – focusing on dress material, shirtings / suitings, home textiles – weaving / knitting with count range from Ne 10s to Ne 60s. With its consumer-driven approach and a series of technological collaborations, JP Modatex aims to emerge a key producer of premium quality yarns in western India.
We recently had a tete-a-tete with the Designated Partner of JP Modatex, Mr. Jindas Jain, and here is the gist of the enlightening discussion.
Please tell us in brief about the J P Modatex Group.
We have an experience of more than 35 years in yarn manufacturing and marketing. Presently we have 17,000 spindles in production and additional 18,000 spindles are proposed within this financial year.
What is your present product mix?
We produce speciality yarns for premium apparels fabric manufacturers for domestic and export markets. Our speciality is in Modal, Lyocell, Linen blends.
Your criteria for selection of machines for your project?
We were in search of latest technology machines which were most energy efficient in their class. We have a vision that India would remain an export hub for garments. International retailers are looking for quality products from India. In the last few years our customers were buying the latest weaving and knitting machines. It was always at the back of our mind that the yarn sold by us would have to perform well on those hi-tech machines.
With these criteria, how did you decide to buy Savio winders?
We co-promoted RG Spinning Mills, Erode, where we had a good experience on Savio Orion machines and later the Savio Polar winders on PC yarns. This time we needed winders which would run best on cellulosic and synthetic blends. We had the first look at EcoPulsarS winder at ITMA 2015, Milan. We were much impressed with its special three features. First, the Suction on Demand system provided, which reduces energy costs. Second, the Duo Air Feeding system which gives best quality splicing strengths compared to any other winder in the market. The third and the most important feature of Savio EcoPulsarS winder is its scalability through which we can add drums if required in the same machine. These were very important features that tilted our decision in favour of Savio EcoPulsarS.
At present, how many Savio winders do you have?
We have 12 EcoPulsarS with 30 positions each. All the machines are running to the full satisfaction of our production and maintenance teams. The efficiencies achieved by the machines and the quality of yarn produced are all as desired by our consumers. Recently there is a change in requirement of our product mix, and due to the scalable feature of the machine we are adding 2/4 positions each to our link winders. This would not have been possible had we purchased any other brand of automatic winder. We are proud that we made the right decision of buying EcoPulsarS.
How was your experience with A.T.E. during the sales negotiations?
A.T.E. is a well-known brand in India with many world-class manufacturers already in its basket. It was pleasure working with its sales team that stuck to the finer details during finalisation, deliveries and aftersales service. It was a win-win situation for us.
Will A.T.E. feature in your future expansion plans?
As said earlier, we are adding 18,000 spindles this fiscal, and we are buying Truetzschler blow-room/cards and Savio Pulsars link winders.