RFID readers in the dye house read the contents of radio tags, robotic dispensing systems supply the precisely constituted dye mix. If sensors report excessive shrinkage of the textile goods, the smart machine controller corrects the process parameters. If delivery deadlines are not met, downstream production processes are adjusted immediately. For Mr. Andreas Hannes, Marketing Manager with Sedo Treepoint GmbH, the company has been on course for Industry 4.0 for a long time. Based in Mengerskirchen, Hesse, Sedo Treepoint specialises in digitising and automating the manufacturing processes for textile finishing. As a member of the VDMA, it is listed in both the Textile machinery and Software divisions.
In the run-up to ITMA, Mr. Nicolai Strauch, press officer VDMA Textile Machinery, spoke to Mr. Hannes.
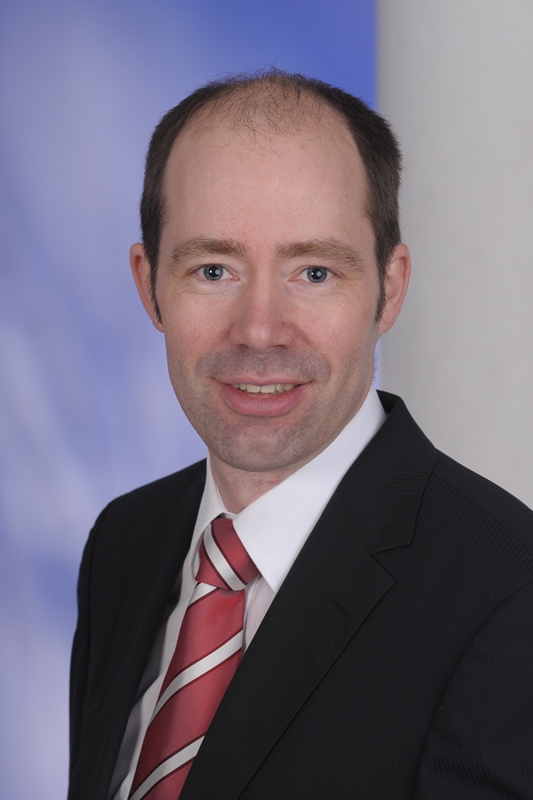
Strauch: Mr. Hannes, how do you set about creating a digital network for the purposes of Industry 4.0, and how does this affect the human operators?
Hannes: In the case of the new textile finishing facility for the Shandong Ruyi Group, one of the largest textile manufacturers in China, in 2014 we carried out a total digitisation project. In terms of data integration, the project involved networking all continuous machines, production data acquisition, an energy management system, the enterprise resource planning (ERP) system, and even printing management as well as other elements. We keep ourselves very closely informed about new trends like the Internet of Things and include them in our developments. This removes much of the burden from human operators. The installed central system is self-explanatory and easy to operate. All information can be accessed at the workstation and machines can be operated and controlled from the work desk. Machine parameters are fine-tuned and production is planned by the system. Maintenance and diagnosis can also be carried out remotely. Consequently, human operators are more mobile and their role becomes one of supervision rather than hands-on intervention.
Strauch: You describe yourselves as trendsetters for IT and automation in textile finishing. Could you explain what this means specifically?
Hannes: Sedo Treepoint earned its reputation as a manufacturer of machine controllers in the form of touchscreen PCs and in hardware automation. This includes the software that runs on the machines, the importance which is growing. Dyeing machines were automated for the first time anywhere in the world 30 years ago in Mengerskirchen. Since then, we have developed many integrated systems. After all, the technology has not ceased its advance. Today, our company offers integrated software and automation solutions for all textile finishing applications and for other departments too. If a production facility is responsible for multiple processing stages, for example spinning, knitting and weaving, we can offer products for these areas as well.
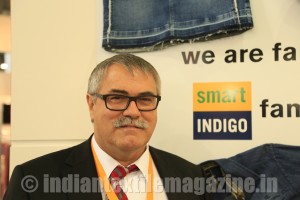
Sedo was one of the first companies in the world to carry out integration, that is what we call the networking of data from various systems, of colorimetry in the laboratory and in production. One milestone was an additional software package for energy management, which we introduced onto the market four years ago, at the last ITMA. There are no products like them in the textile industry with such versatility. The customer can effectively create his “own” product from the Sedo module system and expand it one step at a time. In the case of a completely new investment, we can carry out a deep integration with all systems, functions and departments.
Strauch: How is this integration organised?
Hannes: Vertically, let’s start at the top of the automation pyramid, for example. The apex is the ERP system, in which the orders are entered or invoices are written. The orders then pass right through to the machine level at the bottom. Of course, machines are not intelligent in and of themselves. We equip them with an industrial PC, which makes them “smart” so that they are able to communicate. We are then able to include these machines in the overall business process by means of software, and thus make the information available to all other parts.
Horizontally, textile finishing consists of a very large number of different departments, preparation, washing, continuous finishing, then drying. Many different machines are used, which in turn are subject to specific requirements and run within individual stand-alone systems. Our production management system, SedoExpert, makes it possible to connect all of the manufacturing execution systems (MES) in the various departments, from the spinning mill to fabric inspection, and also provides production management functionalities. Open interfaces allow both existing and new partner systems to be integrated. We already have the ability to run integration not only in finishing but also to extend to other areas. One innovation we are presenting for the first time at ITMA is the rotary screen printing or digital printing area, a section that even we have only succeeded in integrating very recently.
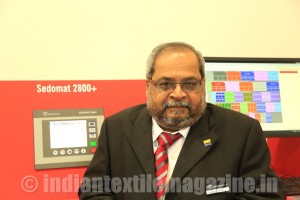
Strauch: What conditions have to be in place for Industry 4.0?
Hannes: In general, there are many machine manufacturers active in the textile industry with various systems. In this context, it is important to have an open architecture with globally standardised interfaces to ensure that digital data exchange is even possible. I think that only an “external party” is able to provide optimal integration of the various systems, a certain independence is often a great advantage. Most importantly, there must be a central information hub that stores and distributes the data to all recipients, horizontally to the production controller, to the machine level, to other auxiliary systems such as the printing press, the colour management or energy management systems, and also exchanging data “upwards” with ERP. All knowledge relating to the process is stored in the system, including colour values, formulas, recipes, tolerances and optimisation options, for instance. The system then uses batch parameters to optimise the process.
Strauch: How will Industry 4.0 evolve in the textile industry?
Hannes: As yet, Industry 4.0, the interconnection of everything and everyone, has barely affected the businesses in the textile industry. The base technologies such as real time and industrial Ethernet, IP protocols, mobile devices, interfaces, Windows, Linux, SQL or HTML are already in place. With regular updates, Sedo Treepoint is providing an evolutionary path that will accelerate the integration of mobile devices, sensors and automatic identification systems such as RFID in the next few years.
Strauch: The advantages?
Hannes: Optimised production processes and improved plant efficiency, more economical production processes, energy savings, more flexible production, to name just a few.
Strauch: Sedo is a member of the VDMA’s Blue Competence Initiative, which champions the cause of sustainable business practices. To what extent is your company committed to this objective?
Hannes: Sedo Treepoint introduced and began offering systems to improve energy efficiency and conserve resources in production even before this issue received the attention it has now. Consequently, we are already able to recommend appropriate best practice solutions to our customers, and ultimately to implement them as well. Our energy management system helps companies to save energy sustainably and for the long term. Prospective customers can take advantage of our comprehensive consulting services for optimal process design in the interests of ecologically responsible, energy efficient production. Our energy management software, EnergyMaster, documents energy consumption for all key variables, correlates these with production and shows where potential for savings lies. This enables significant economies to be made in electricity, gas, compressed air, water, steam and waste water. In addition, calculations of the CO2 balance can be made, and the carbon footprint can be worked out.
Strauch: What innovation is Sedo Treepoint presenting at the ITMA ?
Hannes: Our showpiece innovation at the trade fair in Milan is SedoExpert. This is a software package designed specifically for modern textile manufacturers, which features interfaces with our production management systems SedoMaster, ColorMaster, PrintMaster and EnergyMaster, and thus operates within a fully integrated, automated environment. Besides production functions such as production orders, production planning, simulation, routing and so on, it also provides functionalities like inventory management and preventive maintenance, and can be adapted to the customer’s needs. Also we are presenting PrintMaster for the printing and digital printing area, a section that even we have only succeeded in integrating very recently.
“I think that only an external party is able to provide optimal integration of the various systems. Each machine manufacturer has its own system, so a certain independence is often a great advantage” said Mr. Hannes.