The new woven plant of Shahi Exports at Shimoga happens to be the most automated textile plant with perfect layout to minimise material movement. It contains automated yarn and greige fabric storage, fully automated finished fabric storage system connected with online packing, auto draw-in for weaving, and automatic dispensing of chemicals and dyes for both dyeing and printing, and all this has been made possible by A.T.E.
When it comes to introducing the latest global technologies to India, the one name that crops up instantly is that of A.T.E. Moreover, A.T.E has further established its reputation in India through its commitment to providing perfect after-sales service support while supplying hi-tech machines. The company has been serving its customers for more than eight decades and has therefore gained deep insights into the Indian textile business. It has therefore been meeting the expectations of Indian textile manufacturers to a great degree of satisfaction. A.T.E represents almost all leading machinery manufacturers by which they can offer a package of machinery for spinning, weaving, knitting, nonwoven, carpet and processing.
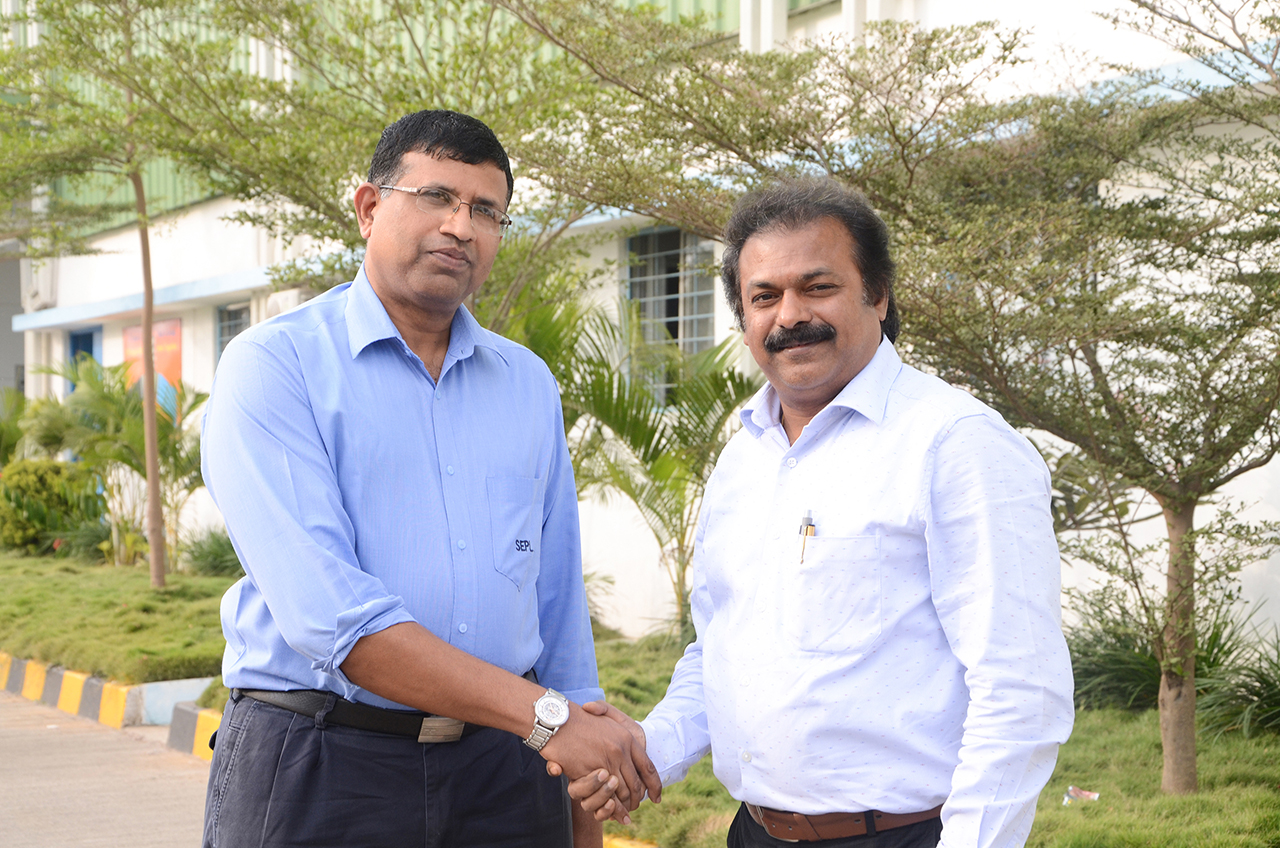
Apart from capital machinery, A.T.E also offers accessories for spinning and processing plants. With such a wide portfolio of machinery backed by a strong after-sales service team, A.T.E has gained rich experience of executing many textile projects across India, including for such clients as Vardhman, Nahar, Trident, MI Industries, PC Colours, Arvind, Sintex, Birla Century, Welspun, Mafatlal, Morarjee, Indo Count, Premier and Himatsingka. One of the remarkable project executions has been at Shimoga in Karnataka for Shahi Woven, which was commissioned a year ago with a production capacity of 2,00,000 metres per day. The plant has been set up for processing various substrates like cotton, viscose, synthetic and its blends. The process house has been designed to process bi-stretch lycra fabrics too.
A Model Company
Shahi Exports (P) Ltd. is a perfect example of modern-day rags-to-riches story which not only entails a humble beginning but also showcases how a group of visionaries can transform the way business can be conducted. The company was set up in 1974 by Sarla Ahuja who started her journey as a sewing machine operator in a factory. “With a group of dedicated colleagues who worked and continue working day and night relentlessly towards converting a dream into reality, the entrepreneurial project proved to be a hit not only because of the numbers but also by earning a place in people’s hearts. Due to this unique approach the company has now become the largest apparel manufacturer and exporter in the country,” says Harish Ahuja, Managing Director, Shahi Exports.
In 2014, the company started with a project in Shimoga, Karnataka over an area spread across 250 acres of land, comprising spinning, knitting and processing units. This facility has a capacity of around 65,000 spindles and houses one of the best-in-class technologies available in the market. This project was a part of an expansion policy and the result of the success witnessed at its plants in Ghaziabad and Delhi, which are certified by Organic Content Standard and Global Organic Textile Standard. After tasting success in spinning, knitting and processing businesses, the company expanded to start weaving and processing plants in 2018 and now includes production of lightweight top fabrics to heavyweight bottoms fabrics.
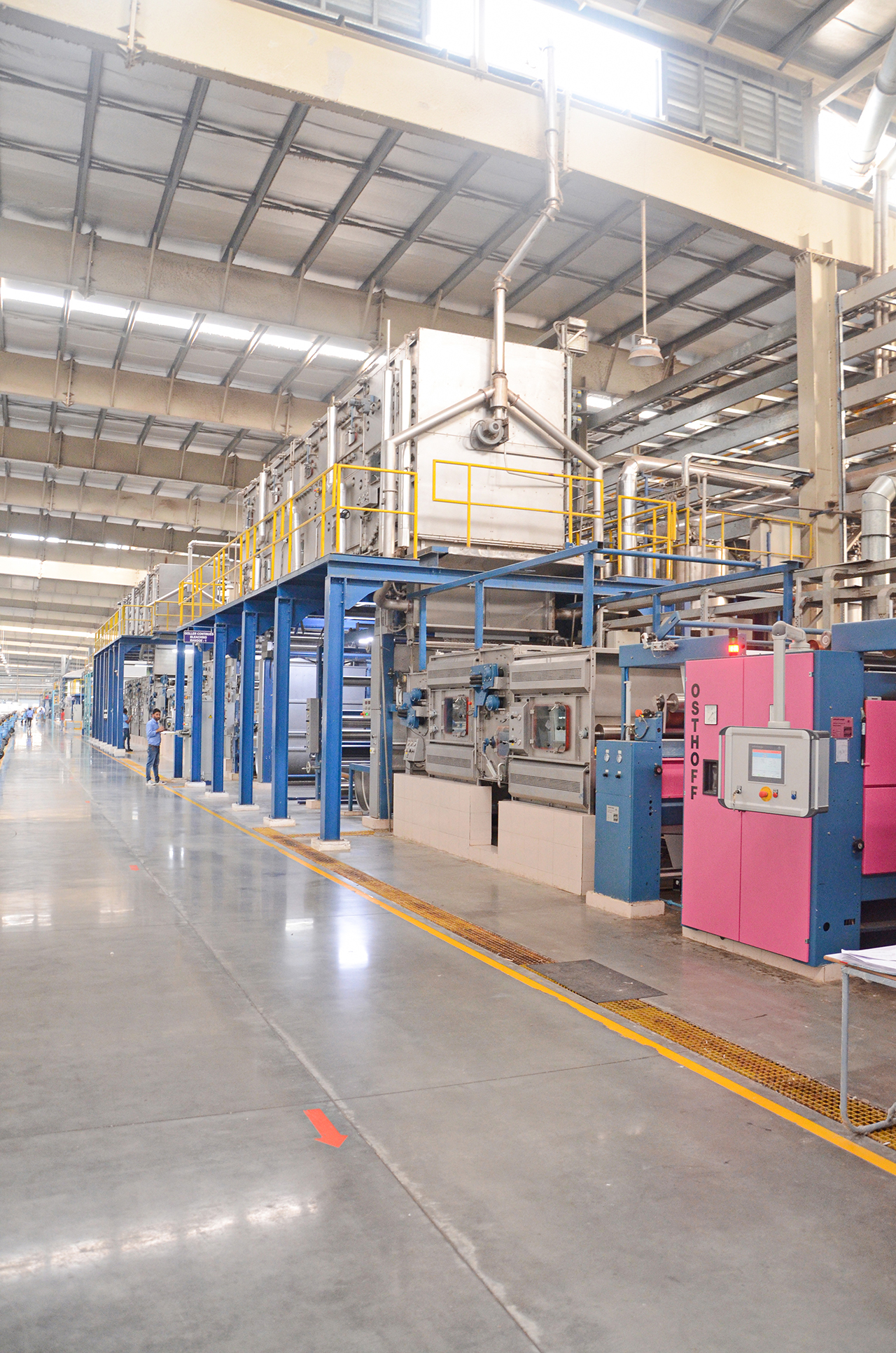
Technology and Social Obligations
Using the best technology available with strict quality control systems in place, the company was able to achieve unthinkable targets. In weaving, the company is now able to produce 5 million metres per month while the processing unit manufactures around 6 million per month. The company proudly holds the title of owning one of the biggest and most successful multifunctional projects that the country has ever witnessed. Highlighting the advantages of having such a facility, Jayaraj Engal, General Manager, Shahi Exports, says, “The plant at Shimoga has been able to create a backward integrated facility wherein the entire manufacturing process of yarn-dyed, piece-dyed and printing of lightweight fabrics to bottom weight fabrics takes place under one roof. Our quality standards are set high to meet the requirements of our customers and create top brand sustainability.”
“This woven plant at Shimoga happens to be the most automated textile plant with perfect layout to minimise material movement. It plant contains automated yarn and greige fabric storage, fully automated finished fabric storage system connected with online packing, auto draw-in for weaving, and automated dispensing of chemicals and dyes for both dyeing and printing. Major brands have compared the technological advancement of the plant to those in China and Europe. Above all, the plant fulfils its social obligations by being environment-friendly. In March 2017, Shahi Exports established Good Business Lab which aims to improve the lives of the low-income workers by reducing the skill gap. This and various other initiatives have proven to be employee-friendly and created a healthy work environment while improving productivity,” he adds.
The threat to the environment due to industrial activities is a rising concern for all and thus it is crucial, especially now, that companies use alternate means of resources available instead of using the ones that are depleting rapidly. As an emerging business, Shahi Exports understands the role that the textile industry has played in terms of being a source of environmental pollution. In its attempt to avoid usage of non-renewable resources of power, the company has made the Shimoga plant run on solar energy to the extent of 98% of their electricity requirement. It has a separate solar power plant to facilitate the conversion. Further, it has initiated a rainwater harvesting system in the main plant and around 100% of the rainwater received is collected in a pond for further use.
Shahi Exports has got a complete zero liquid discharge (ZLD) system in place with 95% of the effluent getting recycled and reused. Further, better systems of condensate and heat recovery have helped to reduce coal requirement in the boiler by 15%, which enables to reduce the carbon footprint. These are some of the tactics used by the company to keep in check the impact on the environment. In fact, Shahi Exports is a shining example of a successful business that has grown over the years by facing the toughest hurdles successfully. “One of the main ingredients to build a successful empire is to manufacture products which are long-lasting and match the expectations of the customers. To achieve high benchmarks a company needs to choose its partners well as also the machinery and technology it uses,” Engal states.
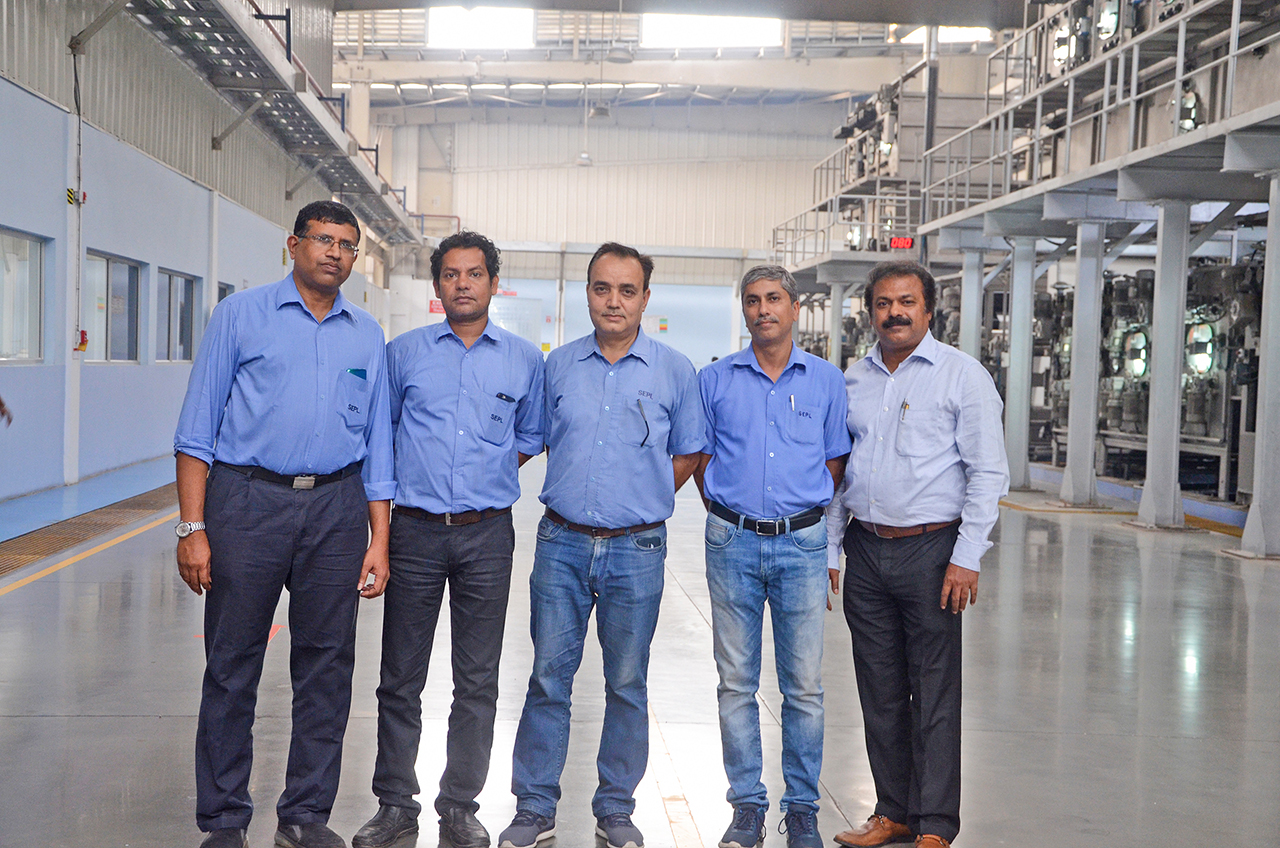
Perfect Partnership
At Shahi Exports, the team is particular about the quality of the products that the company sells and their efforts are supported by the management in terms of choosing the best machines possible. It was by keeping all such parameters in mind that Shahi Exports chose A.T.E as a partner for providing the most important machines and solutions. The two companies have been associated with each other for more than 10 years. A.T.E and Shahi Exports’s first association was at Sarla Fabrics’ plant. A.T.E supplied a majority of the machines like the Then-Airflow® dyeing machines, Fongs’ yarn dyeing machines and Monforts stenters to the knit processing plant which are performing extremely well.
Recalling the time when the deal was to be closed, Engal says, “The A.T.E. team took us to their plants in China and Bangladesh where we were shown their running machines. The people at A.T.E were so patient yet persistent for more than nine months. They were always available to clarify all our doubts and satisfy all our queries. We met a lot of experts who guided us in our decision-making process. They shared with us their in-depth knowledge and also gave us technical insights concerning the configuration of the machines.” Some of the A.T.E machines used by Shahi Exports include the Goller continuous bleaching, mercerising, pad steam and washing ranges, Osthoff singeing machine, Monforts e-control continuous dyeing ranges, Monforts stenters, Monfongs shrinkers, Zimmer rotary printing machine, a complete package of Color Service chemicals, dyes and print paste dispensing system, and also Karl Mayer sizing machine for their weaving plant.
Further, the after-sales service team of A.T.E has been a true helping hand. “This team happened to be one of the most efficient during our start-up and stabilising period with their patience and technical support. They solved queries within the shortest time which helped the business in functioning smoothly and thereby reduced the breakdown losses. The reason why A.T.E and Shahi Exports have worked so well together is that their principle of serving the best to the customers has synchronized beautifully. A.T.E has proved to be a backbone for the company and this partnership has proven to be beneficial to both,” Engal states. With a workforce of over 2,000 dedicated employees in the new woven project and the same complimented by a visionary management team, Shahi Exports has been able to rise to the top, and intends to remain there.