Plain bearings often have to withstand considerable adverse influences such as abrasive dust, high speeds or chemicals. To enable indication of the degree of wear of such plain bearings in good time, igus has now developed the world’s first intelligent bearing with iglidur high-performance plastics. This warns of imminent failure in good time. Machine and equipment operators can plan maintenance, repairs and part replacement in advance.
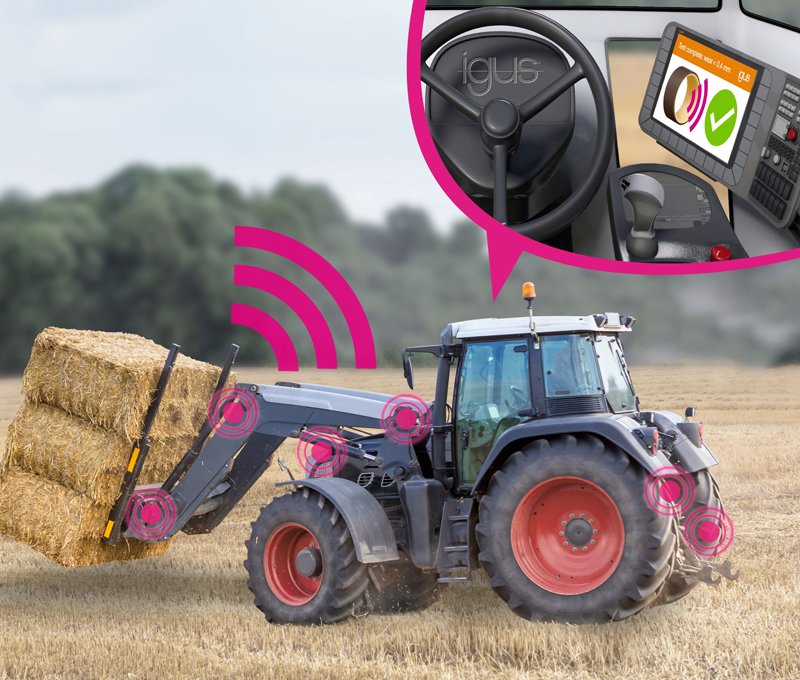
If a building machine fails, packaging equipment comes to a standstill or a wind turbine no longer turns due to a bearing failure, this causes a lot of trouble for the operators of such machines and equipment. igus has therefore added the world’s first intelligent plain bearing to its range of smart plastic products. It detects wear in extremely stressful applications in advance and sends a signal to the user in good time if the bearing threatens to fail. Maintenance work can therefore be planned and operators of agricultural machines, for example, are not surprised during the harvest season. “We have primarily developed smart iglidur for difficult-to-access bearing points and for applications where no regular maintenance intervals have been planned”, explains Stefan Loockmann-Rittich, Head of the Business Unit iglidur Plain Bearings at igus GmbH.
Smart plain bearings individually designed
The body of the new smart iglidur plain bearing consists of two components: the internal, lubrication-free iglidur material and an outer hard polymer shell that protects the bearing. “The customer can choose the material that is most suitable for his application. The complete range of iglidur materials is available to him”, says Loockmann-Rittich. In order to measure the amount of wear, an intelligent sensor is used between the two components. The measured data of the sensor can be integrated by the machine and equipment operators in their systems in different ways. For example, it is possible to inform the operator about the plain bearing’s wear by means of a warning light, where an automatic cut-off is also a possibility for integrated use of the sensor data. For high-end applications, the data can be sent directly to a control system, which, after their analysis, passes the data on to a customised web interface via the icom communication module for the purposes of maintenance and repair. In this way, the user can plan maintenance and replacement by means of a terminal device of his choice.
Small, compact and cost-effective: new lubrication-free toothed belt axis from igus
Lightweight and compact toothed belt axis ensures Low Cost Automation in the tightest of spaces
Fast automation in confined installation spaces: igus has now developed an extra-compact toothed belt axis based on its flat drylin N linear system. The new axis consists of a completely standard fitment of components and is thus easily assembled within a few minutes and cost-effective. Equipped with motor and control, the new system can carry loads of up to 20 N and a translation of 60 mm per revolution.
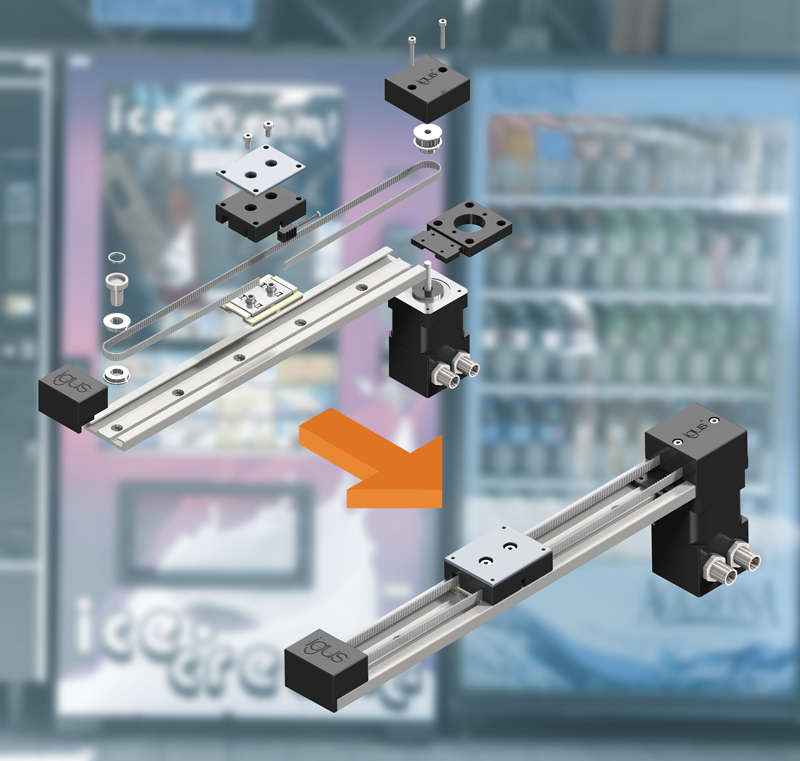
From the lubrication-free plain bearing and the maintenance-free linear guide up to the completely ready-to-install linear robot, igus develops solutions for the industry with its plastics – either as a single part or as a system. With the help of its linear construction kit, the motion plastics specialist has combined its drylin N low-profile linear guide with a toothed belt and has now developed the new cost-effective drylin ZLN toothed belt axis as standard. Whether in vending machines, service robotics or even in automation systems, the new compact toothed belt system can be installed quickly and easily in the smallest of spaces. The flat drylin N linear guide ensures compact construction, which is just 27 mm high and 40 mm wide. The toothed belt mounted on ball bearings enables high speed dynamics. With the combination of low-profile linear guide and toothed belt, loads up to 20 N can be moved vertically at a ratio of 60 mm per revolution. By using high-performance polymers in the sliding carriage, users can completely dispense with lubricants and get maintenance free unit. Moisture, dirt and dust are no problem for the drylin ZLN: great advantages, especially for machines that are in use 24/7.
Plug in, install, low cost
The new toothed belt axis for Low Cost Automation consists of standard components from the drylin modular system that can be fitted together and assembled quickly. Thus, the new axis is not only lightweight due to the use of plastic components, but also cost-effective and delivered quickly. A completely ready-to-install drylin ZLN can be ordered with NEMA stepper motors or with EC/BLDC DC motors as well as a suitable dryve control system. The new, cost-effective toothed belt axis can be delivered in the desired size with a maximum length of up to 750 mm within 24 hours.