By Dipali Goenka
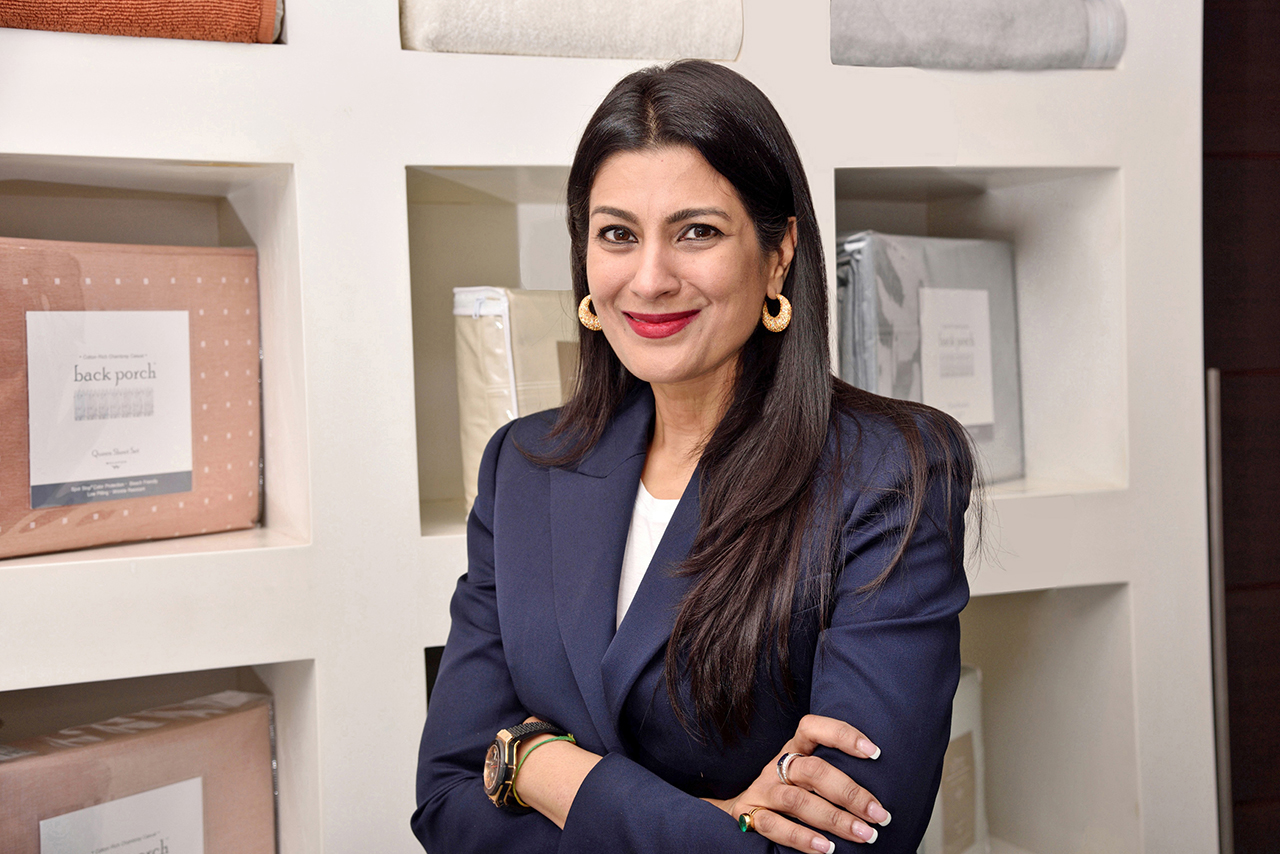
With the new world being as volatile as it first was since the beginning of 2022, businesses across industries are grappling with methods and processes to optimize their supply chains. According to recent reports by IBEF, despite COVID-19, the nation’s home textile exports in FY21 grew at a whopping rate of 9%, with a valuation of US$ 29.8 billion within the duration of April-December 2021. However, recent developments such as the Russia-Ukraine war, sanctions by the United States, and the fresh wave of infections in China combined with subsequent lockdowns have brought in fresh disruptions in supply chains worldwide, which has led many organisations to re-evaluate their supply chain strategies, in the wake of the new normal.
Strengthening the supply chain has to go beyond just looking at recovery from the recent lull and instead focus on how processes can be made more sustainable with a long-term perspective. At Welspun, one of the leading textile companies in India, we have been taking steps to switch to a circular system and practice sustainability and circularity throughout the value chain.
Here are 5 effective strategies that organizations can adopt to Strengthen Supply Chain, as we begin to define the new way of working.
- Go for multiple sources in the supply and production One thing that the pandemic has taught us is that borders and transportation can shut down at any time, and businesses that are dependent on sole suppliers can find their operations brought to an abrupt halt. Whether it is the textile industry or other sectors, depending on just one supplier or production source, even geographically, is not a feasible option anymore. The US-China trade war and further acceleration during the pandemic-led global businesses to reassess their supply chain dependence on China, thus providing momentum to an otherwise slow adoption of the China Plus One strategy. For textiles, India, some countries in SE Asia, and a few locations in Eastern Europe remain top contenders. This means that the strategy is to go Plus One, Plus Two and beyond, such that not only the needs of the moment are addressed but also in the long-term bottlenecks are identified and vulnerabilities are mitigated. In fact, under the Union Budget 2022-23, the textile industry in India saw generous allocations for various schemes that are sure to boost the industry exponentially – such as the India-UK free trade agreement that is poised to propel the garments sector
- Consider going local to build the supply network for our business Honourable PM Shri Narendra Modi first spoke of being self-reliant or ‘Atmanirbhar’ at a time when the pandemic had ravaged our economic standing. The concept of Atmanirbhar or ‘Make in India’ resonated with the entire nation as a much-needed reckoning. So far, we have been unilaterally dependent on suppliers, a system which got severely disrupted due to COVID. This served as a wake-up call and made billions realise the power that we could harness from within India. Supply chain managers need to consider increasing production in the region where they are sold or consumed. This can not only facilitate faster deliveries, but the proximity allows for in-person meetings and easier coordination, thereby reducing the chances of mistakes. Moreover, it allows businesses to be more agile in the production process.
Using local suppliers can significantly bring down expenses. This has the added benefit of making business processes more environment-friendly while also doing good for local communities. As part of Welspun India’s sustainability efforts and the Better Cotton Initiative, we stress on using organic cotton, thus adding to the livelihood of the farmers and having a green process from farm to shelf. - Leverage technological advancements Over the past few years, the use of artificial intelligence has ushered in the age of Industry 4.0. To cite Welspun’s example of using automation in the textile industry, we are focusing on investment in Industry 4.0 Technologies. To optimise the value chain ecosystem, we have developed an end-to-end traceability technology called Wel-Trak 2.0 that traces raw materials every step of the way in the supply chain. This next-gen Blockchain and AI-based traceability platform includes water usage, fair pay, power consumption and gender equality among other ESG parameters. A well-trained team of analysts collaborate with teams working on onshore replenishment, thus working towards reducing volatility in demand forecasting.
- Adapt the workplace to the future of work As supply chain management and operations need to be more adaptable to the future, so does the workforce. The frontline workers are among the core strengths of businesses; more so for textile manufacturing companies. A business’ responsibility does not end with hiring the right manpower. Companies need to invest in educating and upskilling the workers regularly. For example, at Welspun we launched the DigiSmart programme to help all our workers. Built on an inclusive approach to learning, the programme provides training towards building critical capabilities of the workers aimed at a smart factory of tomorrow. Intensive training on data analytics, e-commerce, and Industry 4.0 skills and applications deployed on shop floor are some of the programs covered.
In addition, our ‘Manthan’ programme, based on the Welspun’s Value of innovation, encourages our blue- as well as white-collar employees across locations in India to share their ideas and innovations and serves as a platform for them to voice their views. This also benefits the organisation as employees can put forward solutions to overcome real-time business challenges. - Find workarounds that work for you As businesses look for ways to strengthen their operations, it is important to remember that there is no one-size-fits-all approach here. Globally, companies have been forced to look for innovative solutions to manage disruptions in supply chain. Shifting to lot size handling flexibilities, airfreighting, making containers, logistics acquisitions to boost e-sales, expanding factory capacities, and diverting resources to more profitable product lines, are some of the workarounds that major businesses have adopted. We found that since Welspun’s sustainable fabrics are also majorly distributed in the foreign market, setting up warehousing facilities in USA and UK helped in smoother distribution.
Another practice at Welspun India aimed at augmenting operational efficiency is integrated manufacturing. Spread across different locations in the country, the integrated lines in farm-to-shelf production not only make processes efficient, but also environment-friendly. One thing is for certain, the pandemic has changed supply chains for good. The future demands a model with renewed priorities and optimised solutions; and the right mix of innovation, sustainable practices, and use of technology can help us reach there.