InspirOn Engineering is focussed to serve the industry with innovative technology by understanding the user perspective, requirement & business aspects. Sustainability emerged as one of the major driving force for development, covers following four aspects, Environmental, Economic; Social & Culture.
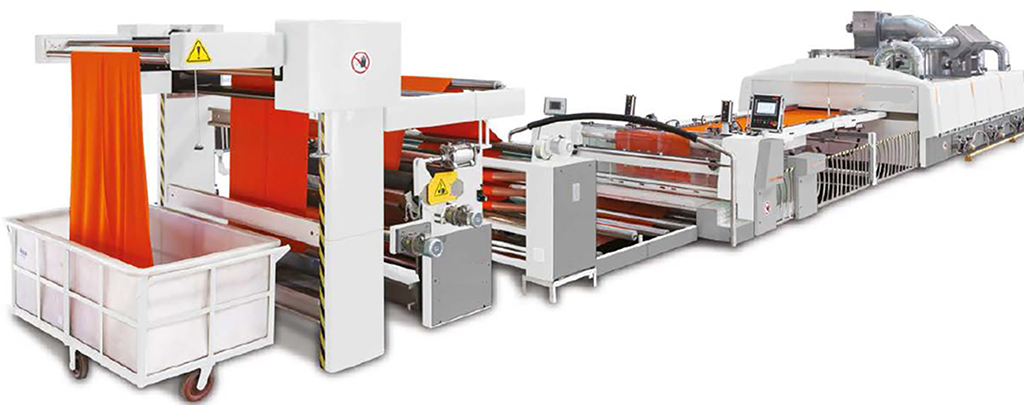
Having started in technical collaboration with A.Monforts in 1996, we have come a long way in terms of developing our own technology as the said licensing arrangement came to an end in 2012. InspirOn has shifted the responsibility of Product Development from A. Monforts to its own designing strength, MOTEX 15000 UNIFLO Designed by the team of young and energetic design professionals, supported & trained by German technologists, MOTEX 15000 is conceived with unprecedented features with state-of-the art aesthetics.
Development aspects: At InspirOn Engineering it is our constant endeavour to offer improvements and advanced technology to our valued customers.
Development through our own R&D efforts in line with the user industry requirement and sustainability as prime focus.
Development of Highly efficient (15% Higher Drying Efficiency) Uniflo Airflow system-
Achieving optimum solution for higher throughput of Hot Air is the prime objective in order to achieve higher drying efficiency: Series of experiments, CFD analysis for nozzle development, finally resulted into development of unique “Uniflo” air flow system by R&D team. Validation process of the newly developed system was performed at state of art R&D Centre located at our Chandiel location & further augmented by running in an established process house at Ahmedabad. Comparative study between MOTEX 4560 (Installed in 2012) and MOTEX 15000 UNIFLO (Installed in Dec. 2015) with technical details is validated by DKTE Ichalkaranji, that MOTEX 15000 is 15% higher than previous model MOTEX 4560.Currently 40 installation of Motex 15000 is in working and benefited the customer in higher output and less operational cost and recognised by the customers of all spectrum e.g. Arvind, Vardhman & Jagadamba Processors, Sanwariyaji Texfab, Sulzer Process & Arvind Knits etc.
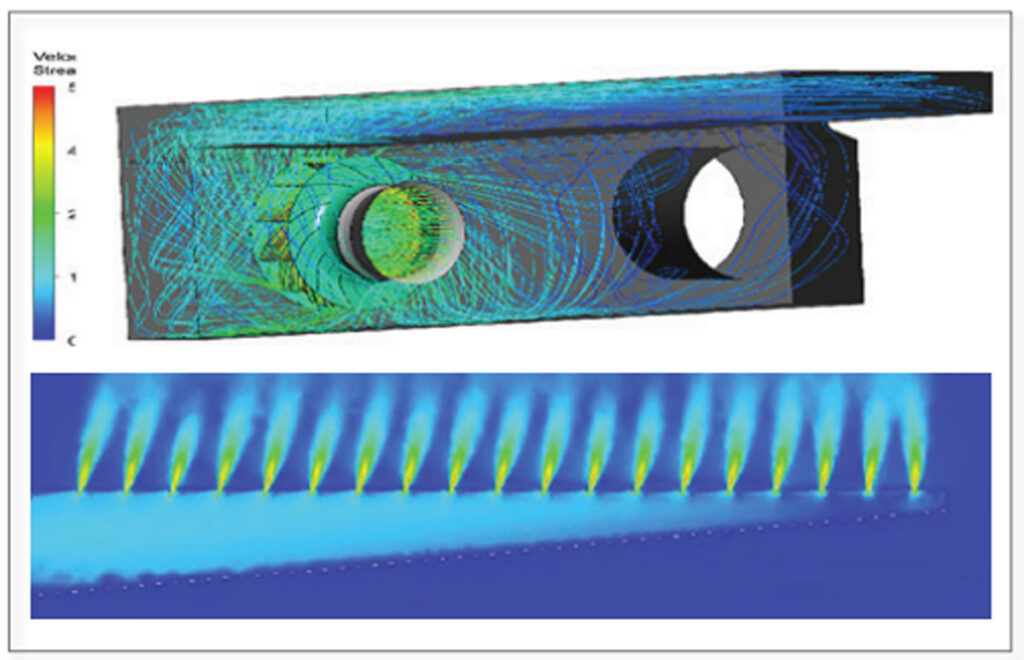
UNIFLO Airflow System (Special Nozzle Design) is patented in almost all over the world (Europe, Turkey & China, etc.)
Development of High Squeezing Padder: Development of High Squeezing Padder for exceptional & uniform squeezing with delicate treatment to Substrate.
Achieving higher squeezing efficiency was the prime objective specifically for Knitted fabric which results into considerable saving of heat energy (up to 10%) in subsequent process of drying in Stenter chambers. This result is achieved on account of squeezing at high efficiency to ensure initial moisture retention in fabric is at desired optimum level. Sliding and tilting trough for easy draining and cleaning has also resulted in better productivity at Customer’s end as also saving expensive residual finishing chemicals successfully at 25 installations, Somany Evergreen, Shri Hari Processors, Om Processors, Arvind Denim Knits are the few name of this list.
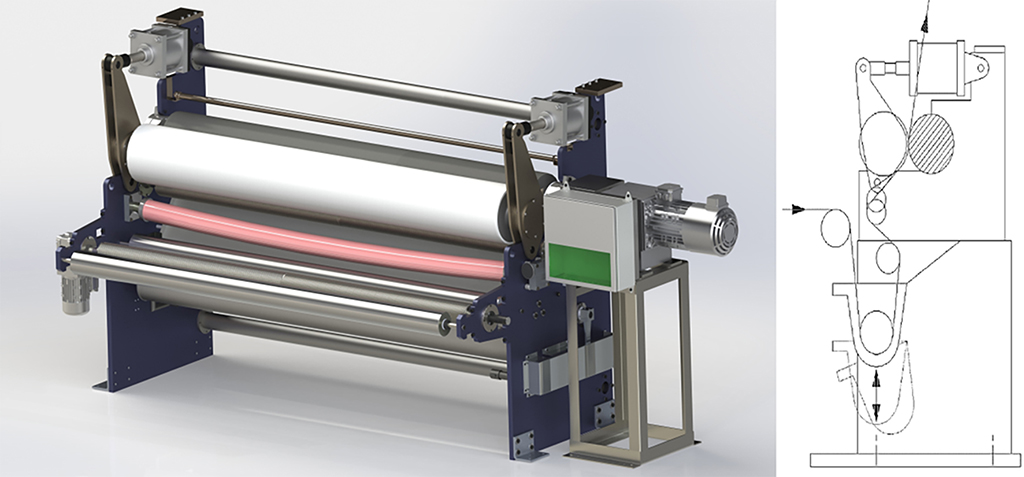
Heat Recovery Unit: MOTEX 15000 UNIFLO equipped with Air-to-Air Heat recovery Unit makes it more energy efficient.
Compact unit concept design of HRU; Enables the stenter machine in High energy savings, with lesser payback period, Approx. 150 units installed till date. Easy mounting / Easy maintenance; can be Integrated on the existing machine. Low cleaning frequency. Main advantages of the KAPrec HRU over conventional Centralized HRU System are-
1) Comparative low cleaning frequency of 3-6 months than other HRU system which required to be cleaned monthly.
2) Compact design easy to dismantle & clean than centralized or other HRU designs
3) Substantially lower down time due to time of cleaning required for KAPrec is 8-12 hours than the other systems where it takes 2-4 days, depending on the condition.
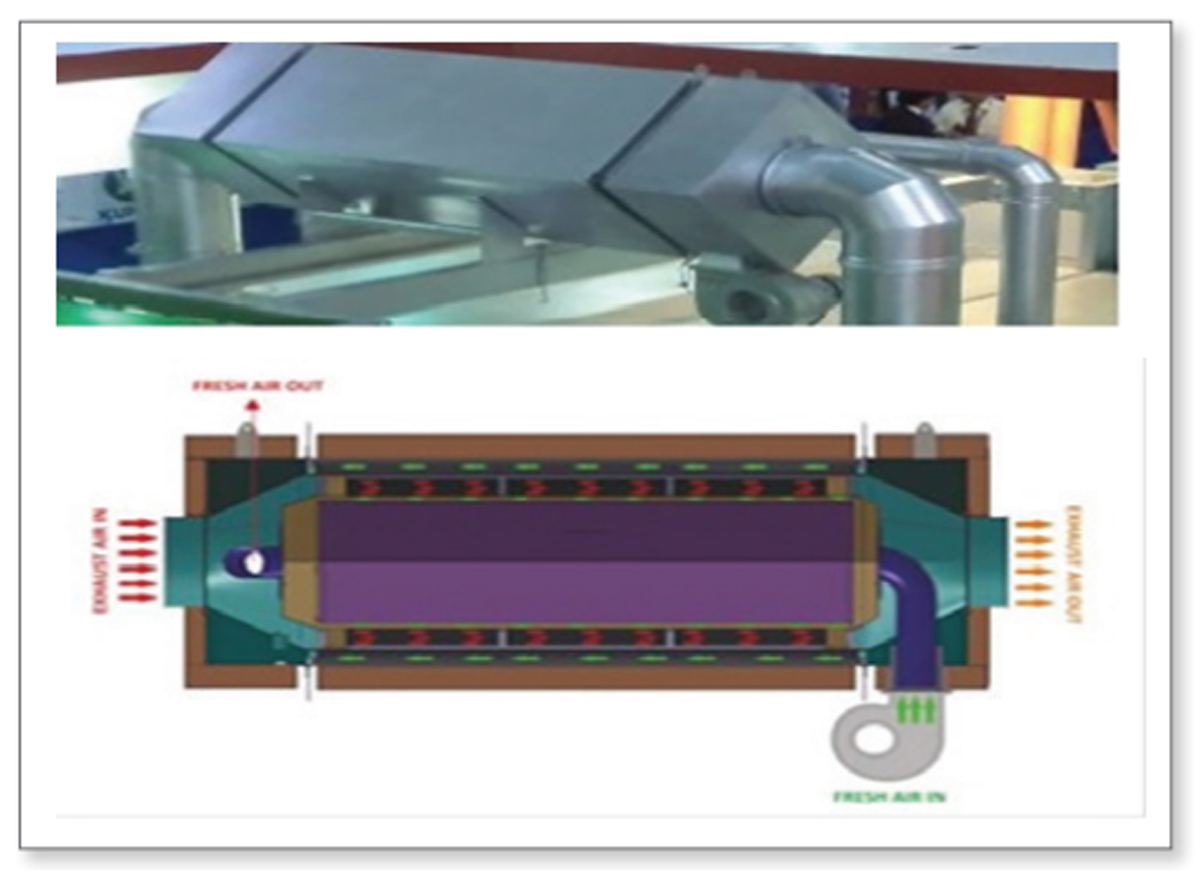
MOTEX 15000 UNIFLO Artificial Intelligence:
At InspirOn Engineering it is our constant endeavour to offer improvements and advanced technology to our valued customers. In this age of Information technology, Industry 4.0 plays a significant role. Besides, in today’s competitive world, information is most critical. InspirOn Engineering leading manufacturer of Stenter for technical application and textile finishing is advancing in the field of automation considering industry 4.0.
- Process Control: InspirOn has developed Process control for optimising machine performance. With the help of dwell time controllers, exhaust and residual moisture controller, it is possible to improve machine productivity and at the same time maintain top class quality. Sensors used of Pleva and controller of InspirOn.
- SCADA –Data Analysis: InspirOn has developed SCADA (Supervisory Control and Data Acquisition) which collects real time data from the machine PLC. This data is verified with the inputs and any deviation is immediately notified.
- TABLET Monitoring: with its latest web app for remote visualisation of HMI screen via smart phones and tablet devices.
- Remote Access Facility: for online Diagnosis and rectification of faults through remote server.