The Coimbatore-based Tex-Tech Industries (India) Private Ltd. specializes in critical spares for all types of combers. The company which also upgrades old combers to the latest versions launched two new products – ‘Mirra Combs’ and ‘Mirra Top Combs’ – at Texfair 2016 held in Coimbatore.
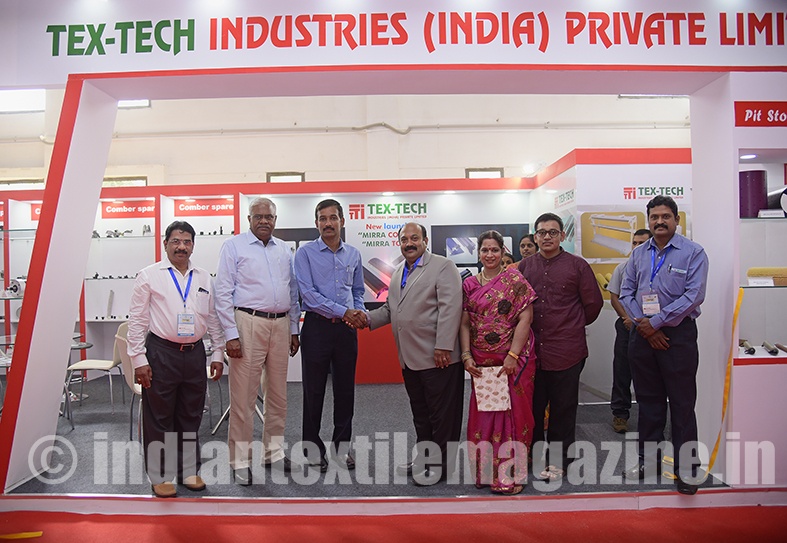
The company has rich and varied experience in the field of cotton combers, being in the field for over 40 years. Going into details on how it all started, Mr. S. Malligarjunan. Managing Director of the company, said: “Tex-Tech Industries was started in 1975 by my father, S. Srinivasan. Initially it was a partnership concern. Later on in 1981 it became a proprietorship concern. In 1985 I joined the business. Since then we have been specializing in critical spares for combers plus upgradation of combers. Subsequently in 2005 we became a private limited company.”
Tex-Tech Industries has developed unique retrofit kits for combers that have become popular in the industry. Highlighting what makes these retrofit kits special, Mr. Malligarjunan stated: “The retrofit kits have been designed in such a manner that they can be mounted (retrofitted) at mill premises. Earlier combers used to be sent from mills to the factory for upgradation. After I entered the business, we came up with the retrofitting concept. We prepare the kit in-house and the same is mounted at the mill site without any modification to the existing machine. This ensures that just in case the retrofit does not perform well, the machine can be converted back to its original state by dismantling the kit.”
The company boasts of excellent infrastructure. Listing down the various types of machinery available in the company’s manufacturing facilities, Mr. Malligarjunan said: “Our state-of-the-art manufacturing facilities are equipped with all the latest models of CNC VMC machines, CNC turning centers, CNC surface grinders, plastic injection screw moulding machines, special-purpose machines (SPMs) imported from Germany to produce brushes, Mirra combs, etc., We also have a modern metrological lab, with latest equipment such as spectrometer, co-ordinate measuring machine (CMM), Vision measuring system, 3D printing, height masters, surface roughness tester, etc., to mention only a few.”
According to him, the company products are designed and manufactured with the computer-aided manufacturing process by using Edge CAM. Firstly 2D drawings are done in Autocad and are the converted to 3D by using Solid works. Adding further on the facilities available, he pointed out: “We are among the few companies which use 3D modeling and printing for the development of plastic components. Upon completion of the drawing, we print the pilot piece using 3D printing and check it for size, dimension, performance, etc. If any small modification is required, the same is done immediately. This ensures enormous cost savings because otherwise even for small modifications the Dies have to be entirely redone which leads to heavy losses down the line.”
Speaking about the company’s new launches at Texfair 2016, Mr. Malligarjunan said: “We have launched Mirra Combs which do not need any ‘run in’ period. We have also launched Top Comb Strips anti-loading type which suits the latest 4th generation combers.”
The company is using the ‘Chemical DE burring Process’ to polish the wires for manufacture of “Mirra Combs”. By adopting this process, the Mirra Combs, which when mounted on the combers, don’t require a ‘run in’ period. Normally, you need to run the machine anywhere from a week to ten days for the wires to get polished.”
The company has lined up ambitious expansion plans for the future. It is already in the process of adding 20,000 sq.ft. to its existing manufacturing facility in Coimbatore.
Going into further details on the future plans, Mr. Malligarjunan said: “We have recently developed E80 type retrofit kit for LK 54 and LK 64 combers. Upon installation of this retrofit kit the speed of the machine increases by 12-15% along improvement in quality levels up to 7%. We have also developed E80 type retrofit kit for E65 and E66 combers. This ensures 1-1.5% Noil savings along with improvement in quality levels.”
The company, which has a windmill division has also diversified into the manufacture of industrial brushes for exports in recently times. “We have imported brush making machines from Germany. We offer specialized brushes for all industrial segments,” said Mr. Malligarjunan while speaking about the particular division. Adding further, Mr. Malligarjunan said: “Tex-Tech has also started manufacturing spare parts for wool and worsted combing processes. Going by the trends in the industry, we see huge potential in this particular market segment.”
The company exports around 40% of its produce to countries such as Egypt, Turkey, Indonesia, Argentina, Vietnam, Bangladesh, Peru, Pakistan, Brazil and Thailand.