By B.C. Mahesh, Executive Vice President and BU Head – Industrial Products
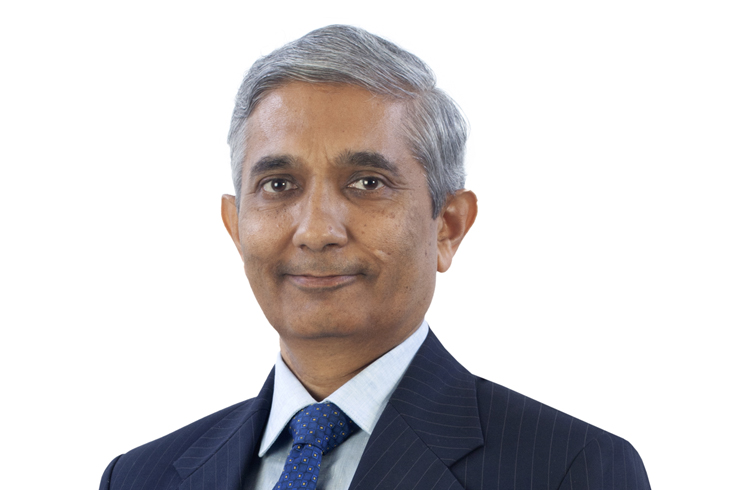
Textiles, one of India’s oldest heritage industries, plays a pivotal role in driving economic growth and creating employment opportunities. It provides livelihood to approximately 45 million people, including 3.5 million handloom workers across the country.1 India currently has a 4 per cent share in global textiles and apparel trade, and the industry is projected to grow at a CAGR of 10 per cent between the years 2019-20 and 2025-26. However, certain processes and materials used in the industry pose environmental challenges.
The global textile and garment industry contributes 6-8 per cent of the total carbon emissions,2 while the dyeing and treatment processes are a cause of water pollution. Generating almost 95 trillion gallons of wastewater each year, the textile industry accounts for a fifth of the total industrial wastewater generated worldwide, endangering aquatic life and human health.3 Moreover, operations such as spinning, weaving, and dyeing consume a lot of power and emit copious amounts of greenhouse and noxious gases. Adopting sustainable practices and investing in cleaner technologies will help the Indian textile industry address such issues and embark on a journey of energy transition.
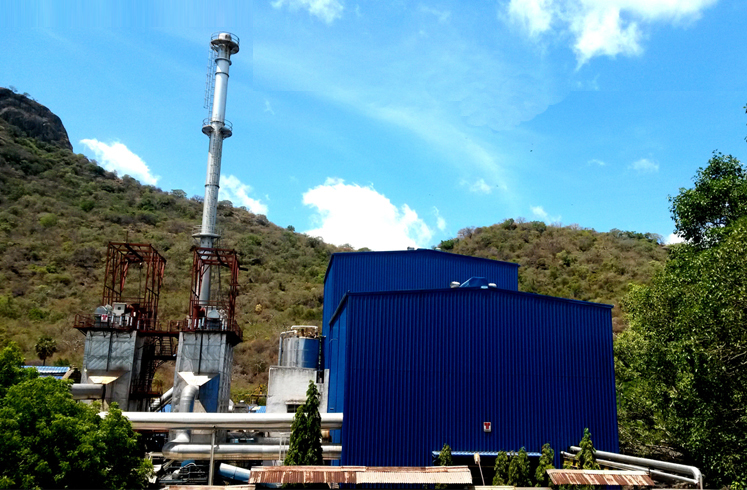
Thermax, a global leader in energy and environment solutions, can guide and assist them in this respect with its large portfolio of products, services, and customisable solutions for the textile industry.
Traditional heating methods in textile manufacturing entail the use of fossil fuels, which leads to greenhouse emissions and the release of noxious gases. Thermax’s heating solutions enable textile manufacturing facilities to use cleaner, renewable alternatives such as biomass, waste-to-energy, waste heat recovery, solar power and so on, which have significantly less emissions.
Energy efficiency is a very important element of energy transition. Around the world, energy cost accounts for a significant percentage of operational costs – as high as 30 per cent in process industries. Thermax conducts comprehensive energy audits for its textile customers to assess their energy consumption patterns, identify inefficiencies, and accordingly recommend customised solutions to optimise their energy usage. This helps textile manufacturers lower their operating costs and improve overall productivity.
Thermax also helps its textile clients optimise their energy utilisation by harnessing waste heat generated during the textile manufacturing process. By capturing and repurposing this ‘waste’ heat, textile companies can cut down their new energy requirement and reduce their dependence on conventional fuels. This not only lowers the environmental impact of their operations but also makes the manufacturing process more cost-effective.
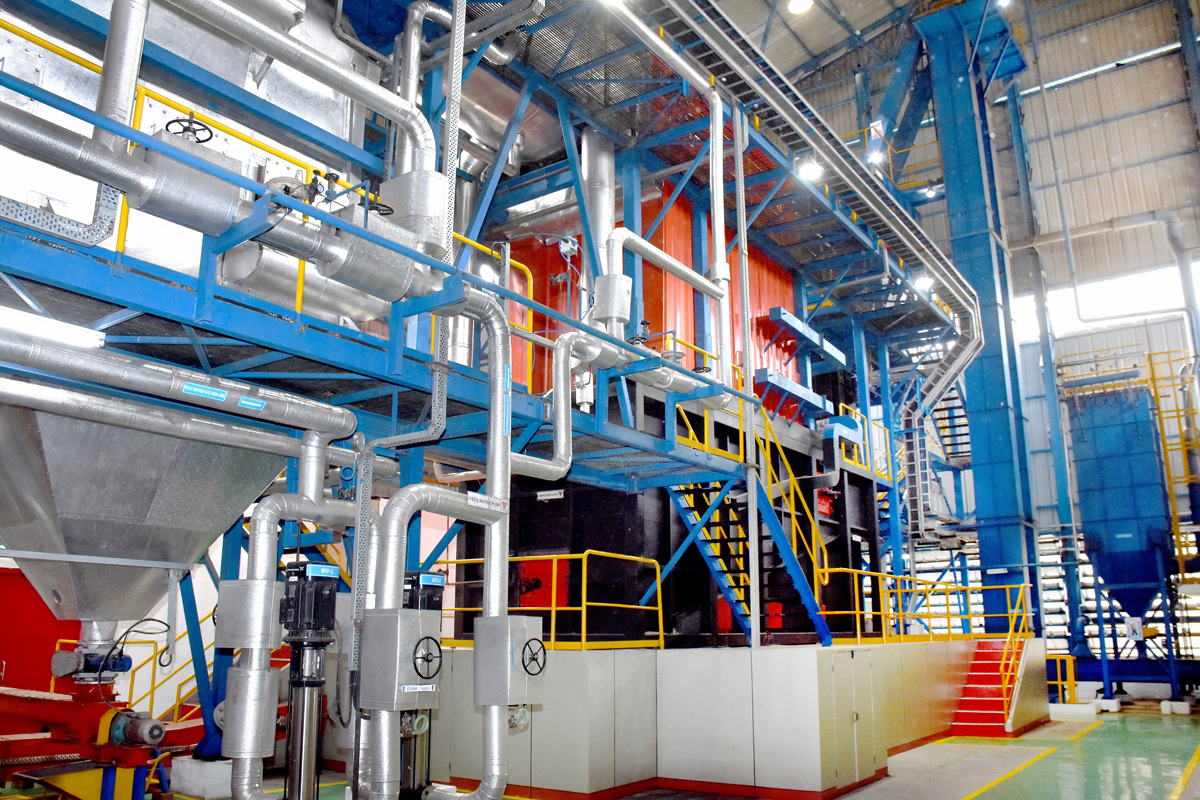
Besides providing energy-focused solutions, Thermax also offers water treatment and wastewater management solutions for the textile industry. These solutions facilitate the recycling and reuse of water, which reduces freshwater consumption and eases the burden on natural water resources.
Case Studies and Customer Testimonials
In 2012, Thermax Onsite Energy Solutions Limited (TOESL), a subsidiary of Thermax Limited, proposed a steam supply solution to a client. The client’s plant heavily relied on fossil fuel consumption, particularly around 24,000 tons of furnace oil annually, resulting in soaring energy costs and substantial carbon emissions. To align with sustainability principles, the client embraced TOESL’s offer of a biomass-fired boiler based on the Build-Own-Operate (BOO) model. TOESL’s comprehensive project approach included surveying biomass fuel sources within a 300 km radius, leveraging Thermax’s multi-fuel technology for an optimised biomass-fired boiler installation, and providing thorough operation and maintenance services. The resulting benefits for the customer encompassed cost reduction, CO2 reduction of over 21,000 tons annually, reliable boiler performance, zero investment in utility machinery, emission reduction, and consistent fuel quality through a dedicated supply chain. Despite the remote location, effective execution led to a successful project, evident in its renewal, underscoring sustained impact and cost-effectiveness.
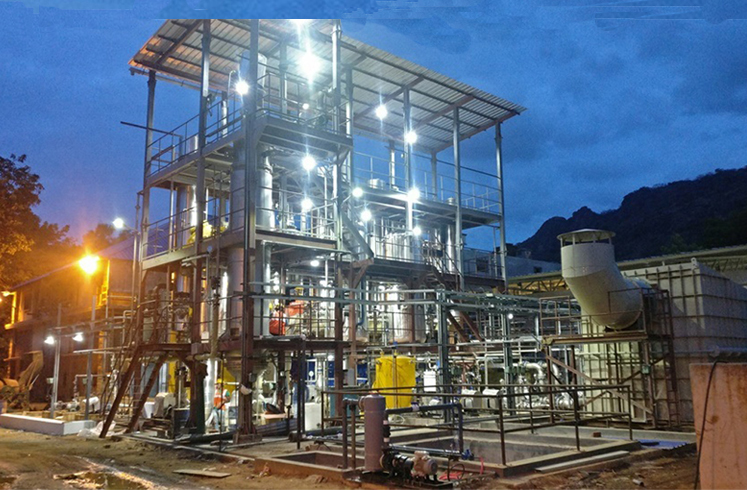
Thermax has delivered similarly excellent results working with other clients from the textile industry too. The company’s heating solutions, energy audits, waste heat recovery systems, and advanced water treatment solutions, have helped textile manufacturers reduce their environmental impact and improve their sustainability quotient significantly. With its unwavering commitment to a greener future, Thermax continues to be a trusted partner in driving positive change for the textile industry and, ultimately, our planet.
1 https://www.ibef.org/industry/textiles
2 https://www.ilo.org/static/english/intserv/working-papers/wp053/index.html
3 https://edition.cnn.com/2023/04/21/middleeast/textile-wastewater-pollutant-cleaner-hnk-scn-spc-intl/index.html
Sources of additional data points
https://www.thermaxglobal.com/wp-content/uploads/2020/09/Energy-Audit-Services-min.pdf
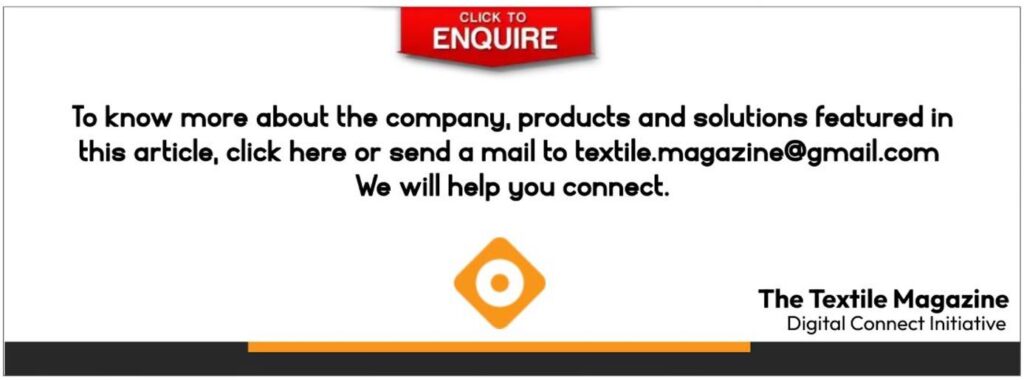