Integrated robotics replaces hard manual labour. High-tech equipment like the ultra-efficient iCone yarn dyeing machine from Thies can reduce the error rate in dyeing plants dramatically and diminish harmful work as well. In many of these factories, the dye is still brought to the preparation vessel in buckets by the operators, to ensure that the correct mixture is supplied for dyeing the next batch. While this is still standard practice in many factories in Asia, for example, in state-of-the-art machine parks, the work is done by robots. Thies GmbH is a market leader in this segment, and systematically continues to compress tasks in all production workflows as well as in the finished products. Marketing expert and Joint Director of Sales Mr. Jürgen Brockmann explains how function integration works at Thies GmbH. The company has manufactured bleaching and drying equipment as well as yarn and fabric dyeing machines from its headquarters in Coesfeld for 123 years.
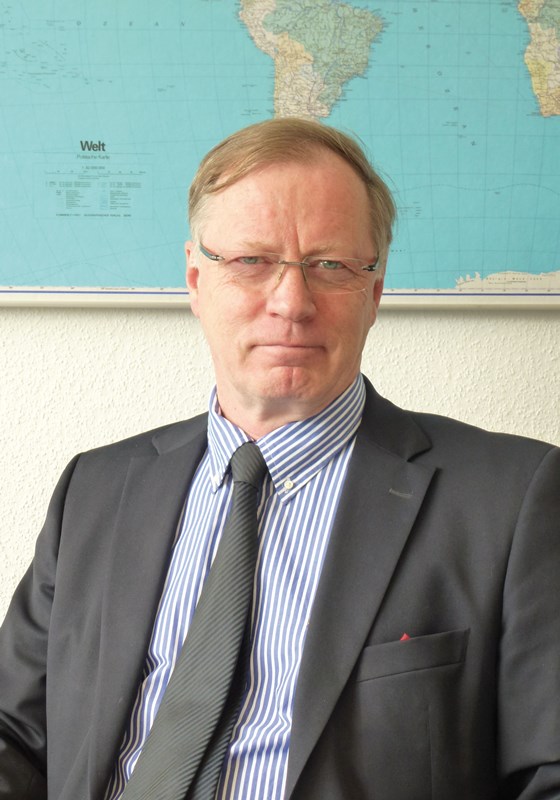
How does function integration work in a VDMA member company like Thies GmbH?
It is no secret that yarn dyeing is an extremely complex process, and a great deal of work goes into ultimately achieving a world-class right-first-time rate with regard to the finished goods. A certain degree of automation is essential for this, which means we must minimise mistakes in the operating procedures and automate system in such a way that the process can be carried out without hitches. To do this, we have to address the entire dye weighing and dye delivery systems, processes which, in most dyeing plants in the world, are still carried out by hand. And as a result of our technology, the number of factories where these process steps are automated is growing.
What exactly are the error sources that automation is intended to eliminate in this context?
Wherever people work, mistakes are made, dyes are not added in the ordered quantity, or they are not at the right temperature. Sometimes they are not even delivered to the dyeing machine when they are needed. The dye delivery system itself also represents a possible source of error, making it difficult to achieve perfect dyeing results. We try to remove this from the equation by automating everything from weighing to delivery.
How does that work specifically?
The dye silos receive a signal from the control system, which might order, for example, Dispense 30 grams each of red, yellow and blue dyes! Upon receiving this signal, the dyes are automatically weighed, dispensed into a container and transported to a dye dissolving station. Here, the dye is brought to the required temperature and then runs into the dyeing machine at the correct time. Before dyeing, the product undergoes the bleaching process. The same thing happens here with the chemicals. For bleaching too, the chemicals must be delivered to the system by a pump in exactly the right quantities, at exactly the right temperature and at exactly the right time. The same applies for solids such as salts and hydrosulfite for vat dyeing, for example. This method is capable of achieving very high levels of colour authenticity. And the procedure for ensuring that the liquor is introduced into the dyeing machine in the best possible condition is similar.
The recently developed yarn dyeing machine, iCone, features many energy-efficient functions …
The iCone has been on the market since 2014, and it works extremely economically with an optimised liquor ratio. This means that it needs less water to bring the dye or the chemicals into the fibres. The guidance system has been redesigned, which has enabled considerable savings to be made. One advantage is that the liquor flows through the coil bodies from both sides, that is to say from the inside out and from the outside in. Additional functions such as the new DynamicRinsing system, or DyeControl for measuring bath saturation so the rinsing times and baths can be adjusted make the processes even more economical in terms of resources, more easily monitored, and more reliable. Water consumption is an important contributory factor in dyeing costs. If you can cut water input, you can also reduce the quantities of chemicals, steam and cooling water. Less water also means less waste water, which after all would have to be purified at considerable expense. And on top of all this, the overall effect of the design optimisations has been to reduce the space requirement. With the same number of dyeing operations per unit of time, output in production is about 23% higher in each case than with the previous version, which has been in service since 1995.
With the new machinery line, it is not only the actual dyeing that is carried out by robots?
That is correct. They also take care of all upstream and downstream process steps. A robot system picks up the bobbins with the yarn, individually or in batches, and loads them onto a self-propelled bobbin carrier for transporting to the dyeing machine or the dryer. This means that the lids on the dyeing machine and dryer must open and close automatically at the right time as well. Unloading of the bobbin carrier after drying is also automated. Humans do not longer have to handle chemicals but have a monitoring role in this system.
Does this high degree of automation create competitive advantages for you?
Absolutely. With automation, the result of the dyeing process is unmistakeably better, of very high quality. Subsequent additions of dyes and chemicals to correct the result are significantly reduced. Making repairs after the run is very expensive for dyeing companies, and it seriously impacts the already very tight profit margins.
Is function integration a viable solution for your customers in low-wage countries?
There are some customers who buy our entire programme, and others are only interested in parts of it. For many dyeing operations in Bangladesh, for example, it is not worth buying a robot bobbin loading system because the wage level there is so low. But it is very well worth their while to automate the delivery of dyes, chemicals and solids. Because this raises the quality of the product, and they can offer their customers a better result.
What trends do you see in the future?
Until about ten years ago, the major subject of discussion in the textile industry was labour costs. Nowadays, labour costs have yielded the spotlight almost everywhere to the topic of energy. In particular, economising on water and power, and generally improving process times. If processes and cycles are shortened, energy consumption is also reduced. We and other textile machinery manufacturers in Germany will continue to work on that.
What do you say to competitors who try to copy your products?
They will always be there. But there will also be enough buyers in the world who would rather buy a Thies original because of its superior quality, efficiency, longer service life and better energy footprint. The best protection against cheap imitations is to never stop developing.