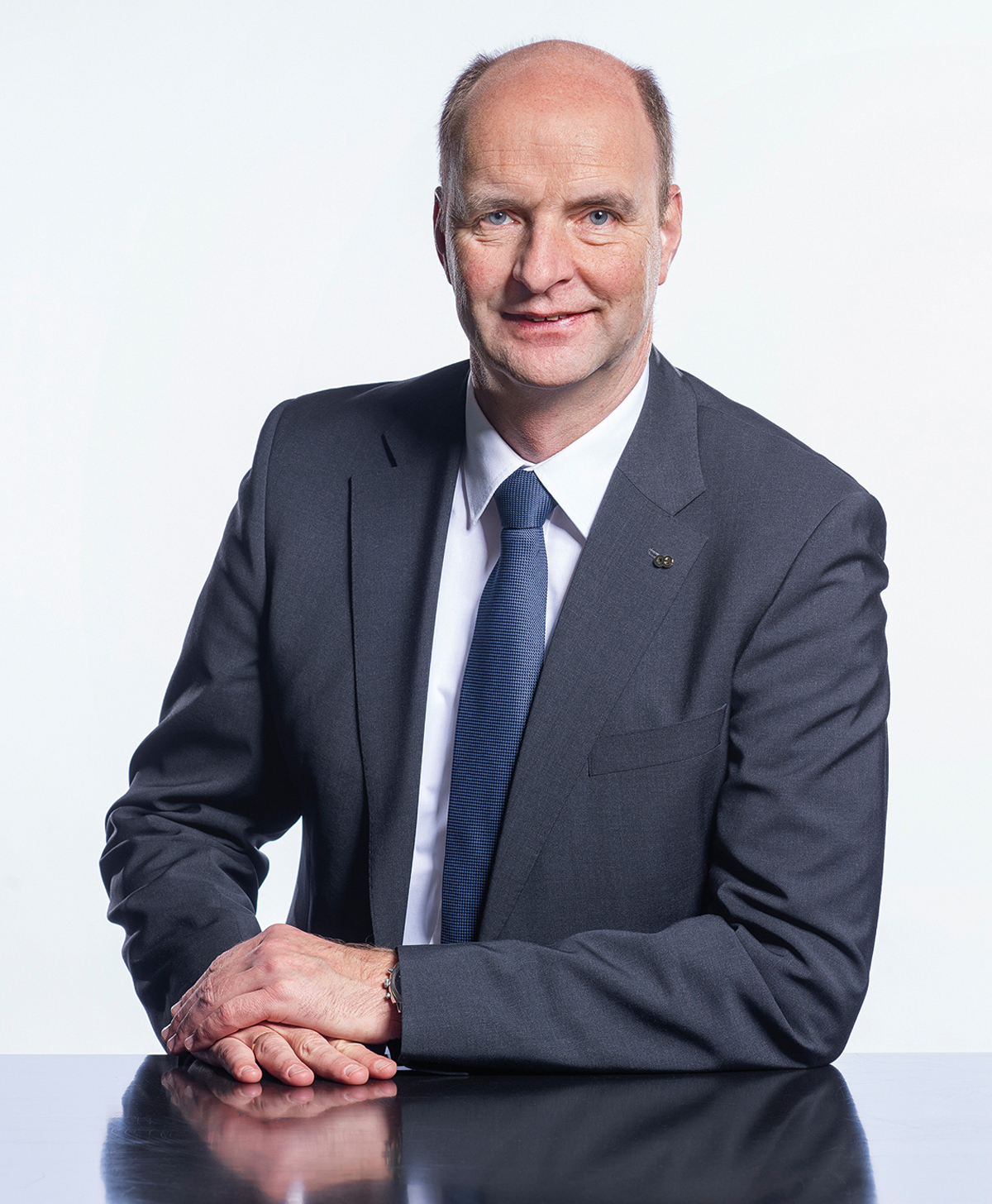
Oerlikon Barmag can proudly look back on 100 years of history – in a sector that has experienced the ups and downs of a turbulent century. What is the secret to this company and its fiercely-fought success, which has made it a leading manufacturer of manmade fiber spinning systems and texturing machines? In an interview, CEO Georg Stausberg – who has had the privilege of shaping 33 of these 100 years in various positions – goes in search of the answers.
Mr Stausberg, Barmag was a pioneering machine manufacturer during the time the manmade fiber industry was born. What were the reasons for the company’s success during the first decades?
Stausberg: Success came, on the one hand, with the rapid rise of artificial silk and synthetic textile fibers, with the manmade fiber industry swiftly expanding at the beginning of the 20th Century. On the other hand, Barmag set a clever course following World War Two. The advance of purely synthetic fibers such as nylon and perlon demanded more research and development along with other machine technologies. Barmag launched its innovative grate spinning machines back in 1948, entering the texturing market in 1954 and introducing extrusion technology in 1958.
The desire to develop new products continues to make Barmag strong to this very day. Where did this strength of innovation come from?
Stausberg: Innovation and technology leadership have always been Barmag’s guiding stars. There is a strong entrepreneurial spirit behind this, even during the early years. This resulted in the consistently close cooperation with customers, market-oriented innovations, interdisciplinary, team-oriented development work and the creative utilization of the full scope of experience and knowledge potential. In the name of progress, we also occasionally question established processes and change conventional procedures and ways of thinking. This was demonstrated in the development of the at the time revolutionary WINGS technology, among other things. And we also quickly focused on such growth and future issues as automation and digitalization. Vision has always been part of it.
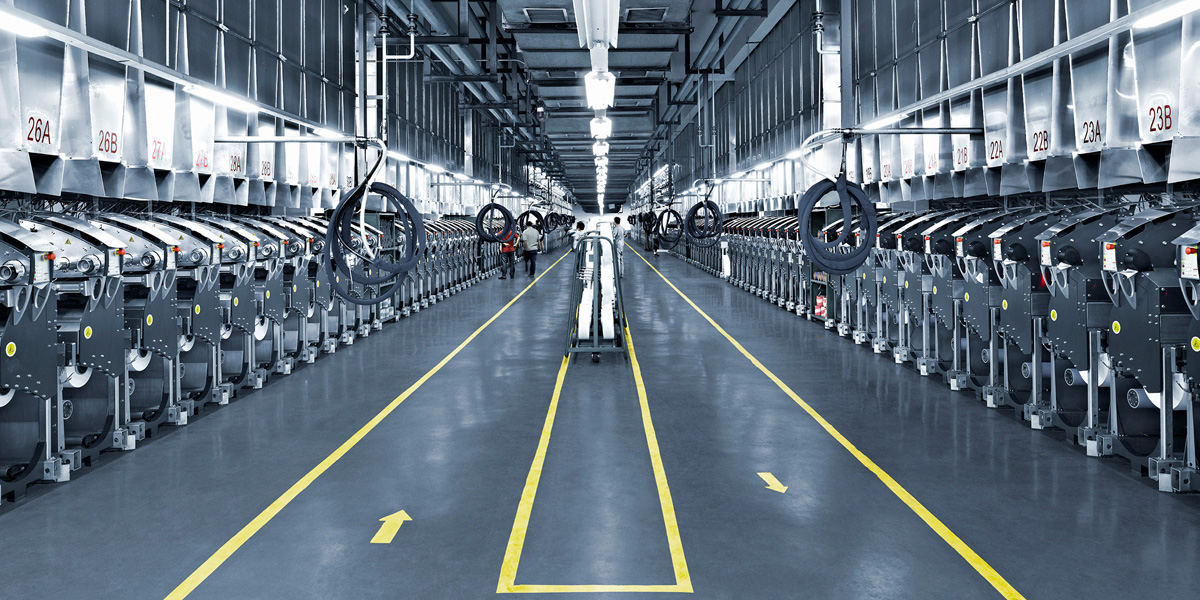
Vision is also a requirement of globalization. Was it not its early global orientation that made Barmag a market leader?
Stausberg: We would undoubtedly not be a market leader without global expansion. By the way, Barmag was supplying equipment to countries such as the Netherlands, Czechoslovakia, the US, Austria and Japan even before World War Two. We then actively set our sights on other foreign markets. And it is figures that demonstrate the result of this: the foreign share of sales rose from 7 to 311 million deutschmarks between 1955 and 1975. Barmag always wanted to go where the music was playing. When we entered the US market in 1965, the country was the world’s largest producer of synthetic fibers with one-third of all global output. We have actively accompanied the increasing shift of the textile markets to Asia from the very beginning, traveling to China for the first time as far back as 1959, establishing a company representation in Hong Kong in 1973 and setting up a first joint venture in China in 1984. Today, we are present outside Germany with 1,200 employees, ten sales and service sites and seven production and R&D centers in the primary markets of China, India, Turkey and the US.
Is globalization no longer a problem with regards to the pandemic?
Stausberg: Globalization is less of a problem, it actually helped us during the pandemic. Because countries such as China initially overcame the crisis more quickly, becoming economic driving forces, while other regions were still recovering. Overall, this has contributed to our economic stability. Furthermore, we are able to better support our customers through our local employees and service cen-ters as well as our long-standing network of suppliers.

How important is service for machine manufacturers?
Stausberg: The pandemic has clearly underlined the huge importance of service. We initiated our hybrid customer service as a way of solving problems – with video streaming to Germany, temporary recruitment of additional staff locally, online consultation and training, remote analysis and optimization. To this end, we have been able to maintain almost all services and once again prove that we will not let our customers down! And we have a name for this: Partnering for Performance. Our aim is to make the customer’s production and business ever more efficient, competitive, profitable and sustainable. It all kicked off in 1969 when Barmag established its own service department with six technicians recruited from the development division. Today, we have more than 18 service stations and offices and in excess of 60 representations in all important textile centers across the globe, with more than 400 experienced service engineers and employees and 24/7 hotline support. The Service business is one of the key cornerstones of the corporate strategy for achieving customer loyalty throughout the entire lifecycle of the sold machines – and hence for boosting new sales as well.
Service, along with all the progress made by your company, cannot be provided without competent employees. How has Barmag consistently been able to recruit, and retain, qualified people over the years?
Stausberg: An innovative, successful company is, of course, very appealing to employees. But that is not the only factor. Employees have always felt a close bond with Barmag and have supported the company even through difficult times. Why? Because social responsibility has always been, and remains, a determining principle of our corporate policy. And there are many examples of this. Barmag established a housing association in 1927, providing company-owned homes to employees at low rents. World War Two saw the initiation of the Barmag pension fund – a pioneering voluntary company pension. Also acquiring legendary status were our Family Nurses, an institution that was the contact point for a wide range of employees’ social concerns, as were the Christmas parcels full of goodies that brought joy to employees for many decades. Both in the past and today, Barmag has always set social standards – ranging from the company health insurance fund, our HSE (Health, Safety, Environment) program all the way through to work-life balance measures.
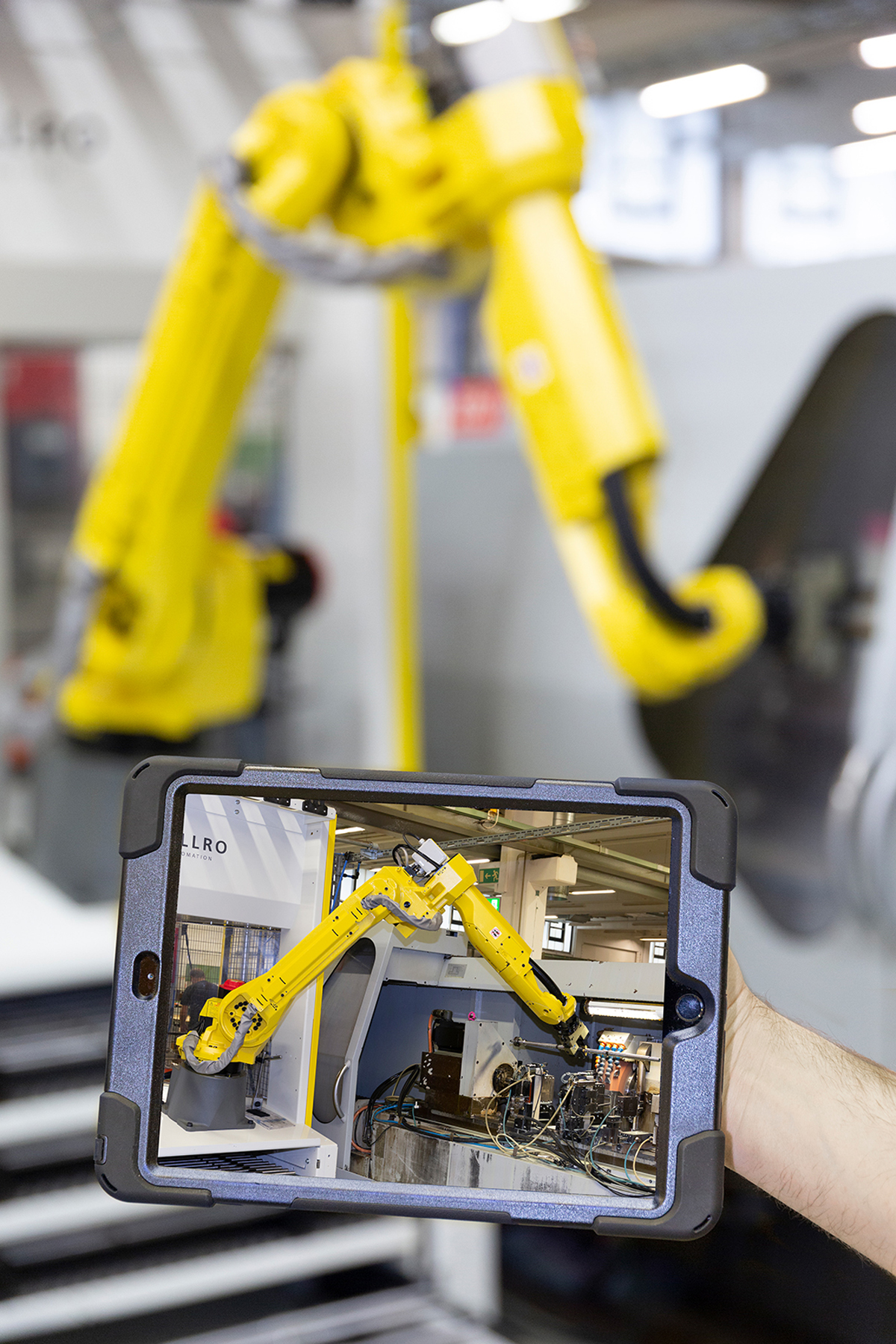
What role does in-house training play in recruiting staff?
Stausberg: From the very beginning, the skilled workers and their talents have formed the backbone of our company. Even today, the in-house apprenticeships and supporting skilled workers are corner-stones of the Oerlikon Group. Currently, Oerlikon Barmag is offering apprenticeships in 14 different professions in Remscheid. Here, our training workshop model, in which all trade apprentices undergo fundamental training to start with, has proved itself – from 1922 through to the present day. Of course, learning has changed dramatically over the past century. Industrie 4.0 and digitalization are transforming apprenticeships, with further training and career development for talented recruits further important topics.
Digitalization has been mentioned in several of your statements. How much is it shaping the future of Oerlikon Barmag?
Stausberg: Digitalization is a major trend. There is no area of the company it does not impact. We were one of the first systems builders worldwide to implement a fully-networked smart factory for a yarn manufacturer. All processes within the production chain are digitalized. Artificial intelligence is being used in initial products. Our company and its organization have been oriented on digital transformation and the requisite agility for the past few years. Basically, we have been working towards this since the 1960s – initially with our own electrics and electronics department, then with our entry into process control engineering and later with the development of our Plant Operation Center (POC), one of the first manufacturing execution systems (MES) for the manmade fiber industry. Today, around 80 percent our spare parts business is conducted online using our myOerlikon.com customer portal. These highlight the importance of digital applications, as well as remote support, video conferencing and webinars. We have developed our own IT infrastructure solution for the textile industry. The data from all work, production and service processes flow together on our ‘Common Service Platform’. But we are not alone here: the entire textile world is on a digital journey. One-off items of apparel can already be configured and ordered online and delivered in the shortest time.
Digital concepts have undoubtedly become part of your own manufacturing environment?
Stausberg: Our Oerlikon Barmag production sites in Remscheid and Bernkastel-Kues, Germany, and Suzhou and Wuxi, China, are also in the process of transforming themselves into smart factories – with digitalized information flow for predictive production planning and steering, with automated continuous flow production and with CNC technology. But digitalization is not an end in itself, it is more about greater efficiency. Our production is therefore based on lean management principles, ensuring optimized throughput and manufacturing times and low inventory costs. Virtually all parts are delivered to the conveyor belt ‘just in time’. Our competence and one of the most decisive success factors now lie in the optimum manufacturing of special core components and precision parts such as pumps and chucks – consciously also as a way of protecting our know-how. In the past, we had a high manufacturing depth with the associated huge demand for space, material flow and highly-challenging intralogistics. Today, we purchase parts, modules and electronic components that others can manufacture better or less expensively.
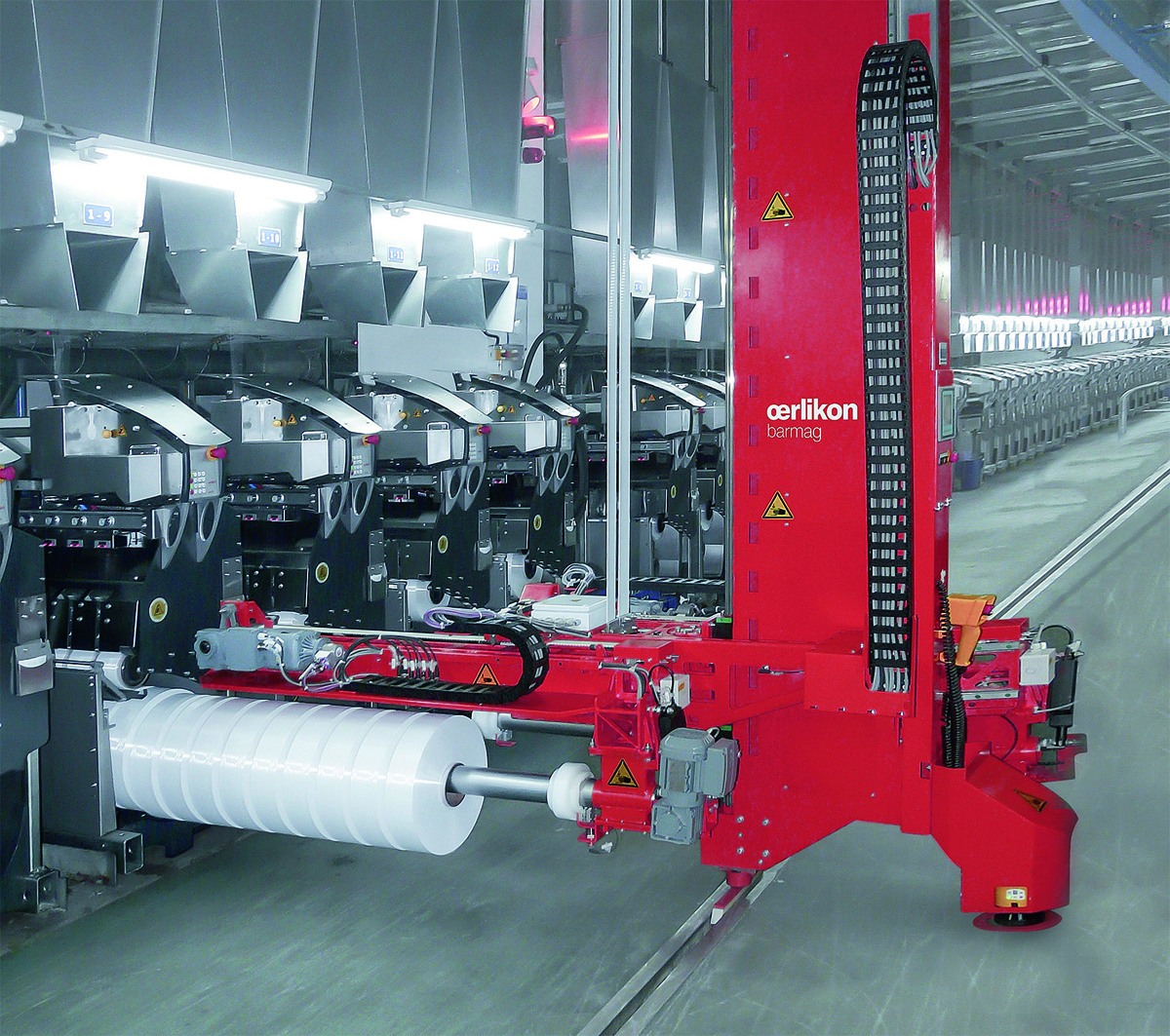
But logistics have also become more demanding in other areas, haven’t they?
Stausberg: Absolutely! Our logistics specialists are fighting on many fronts in the age of free trade and punitive tariffs, increasing delivery speeds and pandemic-related slowdown. Challenges include seamless documentation, transparent supply chains and cross-border inventory planning. For this reason, we are optimizing many aspects of our logistics: our Global Logistic Execution System networks all production sites worldwide, including warehouses, internal and external suppliers, and allows transparent, real-time tracking of goods transports, including consignment and automated dispatch of delivery documents. Another software solution is predicting spare parts orders 18 months in advance, making inventories at sites across the world visible and accessible. Because delivery advantages have become increasingly important – also with regards to environmental friendliness and preserving resources. For this reason, Barmag is committed to purchasing, manufacturing and delivering as closely to the customer as possible and minimizing packaging materials and freight space. This reduces transport distances, resources and helps the environment.
Sustainability and climate protection are major trends as well. When did Oerlikon Barmag start focusing on these?
Stausberg: We have had comprehensive environmental management at our main plant in Remscheid since the 1980s. Environmental protection is one of our company’s declared strategic targets. And ecology also helps us save. We operate, for example, two high-performance cogeneration plants for supplying in-house energy. Furthermore, direct benefits are generated by our intensive HSE (Health, Safety, Environment) activities. To this end, we were able to halve the number of annual accidents over the ten years leading up to 2021. Although, compared to other sectors, the textile industry is not particularly energy-intensive, customers have been trying to optimize their operations for many years now with the aim of cutting energy costs. This is why we introduced our own e-save label for particularly energy-saving technology as far back as 2004. And recycling is also an important topic: our Oerlikon Polymer Processing Solutions division is the only manufacturer offering the entire mechanical PET recycling chain – from processing the recycled materials and the melt through to the textured package. There is, of course, a benchmark here: sustainability is one of the permanent mission statements of our parent corporation. Here, the guiding principles are the 17 UN Sustainable Development Goals (SDGs). We at Oerlikon are endeavoring to make all our sites carbon-neutral by 2030 and to acquire our energy exclusively from renewable sources.
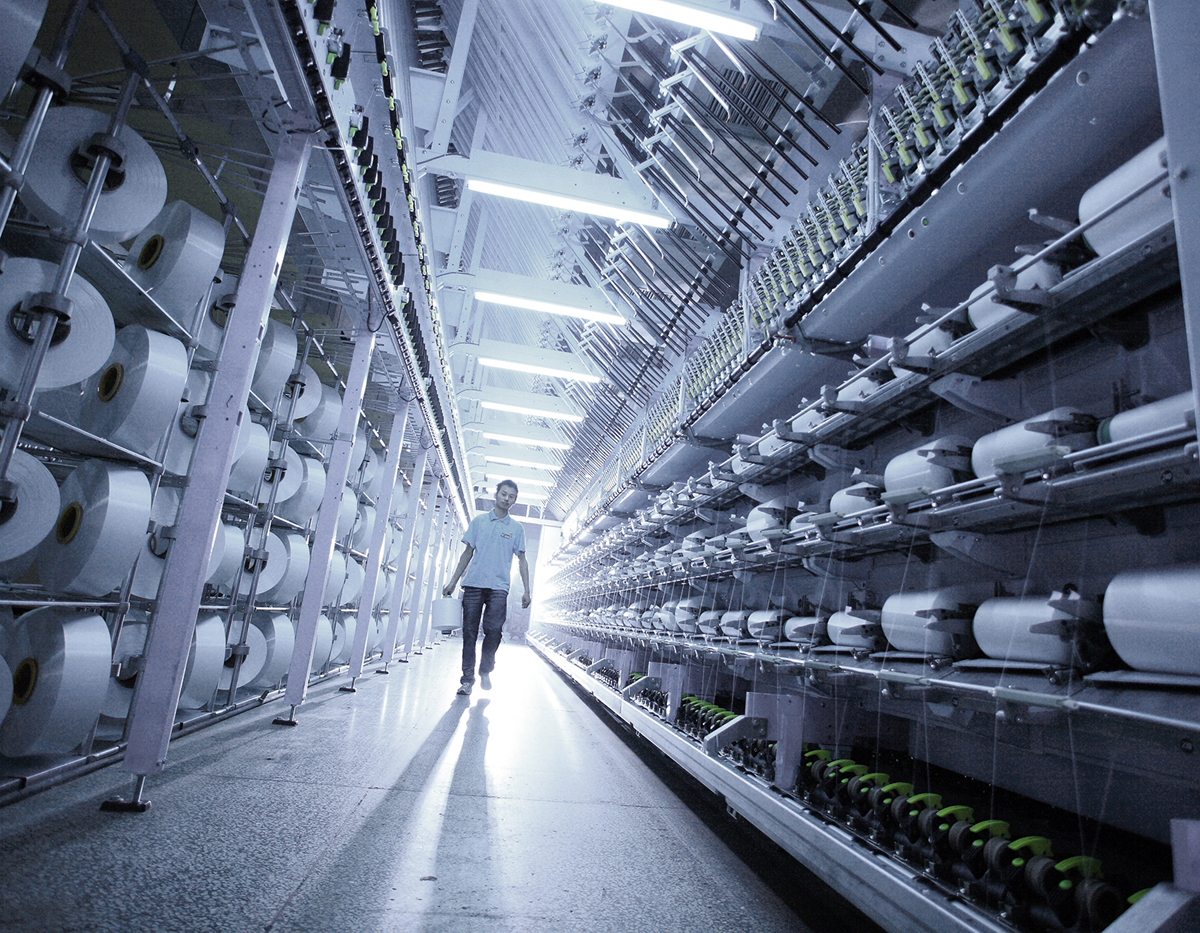
You yourself have helped shape 33 of the 100 years of Barmag. Why are you optimistic that Oerlikon Barmag will have a further 100 years of success?
Stausberg: When reading our anniversary volume, you will discover that the stories and comments of various contemporary witnesses have many things in common. Their statements and our history converge to form the very core of our corporate culture. This constant is showcased by the will and the ability to always adapt to social and economic change and to change ourselves. It is tangible in many decades of consistent innovativeness, striving towards technological leadership, in-house social commitment, stable jobs and long-standing relationships with our customers. This is something that all former and active employees can be proud of. And that makes me extremely confident when looking at the future.