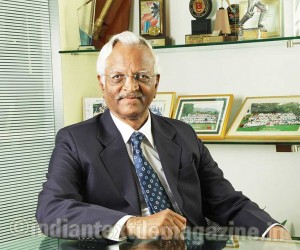
Advanced Graphic Systems (AGS) was founded in 1992 by Mr. Ravi Goyal. It was initiated as a proprietary company with just four members, and AGS started sales & marketing of computer-aided textile designing products. It provided application and after-sales service support to customers such as the Bombay Textile Research Association (BTRA), MANTRA, NRK and Zodiac.
Mr. V.C. Gupte, currently heading the Color Business Division, joined the company in 1995. He has thorough knowledge and expertise in color matching systems.
AGS became the exclusive dealer in India for Macbeth of the US for its sales & marketing of computer colour matching systems, QC systems and light boxes, which were preferred by most retailers like GAP, Wal-Mart, Target, etc.
Initially AGS developed in-house software, NovaScan which was coupled with Macbeth spectrophotometers and launched it in the market as AGS Color Matching Systems. The product was well received by textile process houses. Soon AGS signed an agreement to promote Macbeth systems covering both hardware and software from Macbeth.
With Macbeth systems, AGS was catering to most colour industries like textiles, paints and plastics. With multi-angle spectrophotometers from Macbeth, AGS was also able to cater to automobile industries, Tata Motors being the first customer. The company slowly created the brand Macbeth in India and not only marketed the software but evolved as color solution providers. In 1998, Macbeth was merged with Gretag, a Swiss company, specialising in graphic arts.
With GretagMacbeth, AGS started covering printing ink manufacturing and packaging industries and soon established leadership in alongwith Micro inks (now Huber Inks), DIC, Siegwerk, Toyo, etc. With total help from AGS, these companies started offering GretagMacbeth systems to their dealers/colour centres and made the concept of providing colour matching at retail colour centres very popular. Micro Ink launched their ‘ATM’ (Any Time Micro) and installed over 300 systems with GretagMacbeth systems.
In 2006, GretagMacbeth changed hands. It was acquired by X-Rite of the US, which was subsequently acquired by Danahar, another US company, in 2012. The GretagMacbeth brand no longer exists. It is now X-Rite.
In order to supplement and compliment X-rite products, AGS has tied up with 4 other worldwide companies. These are:
• Digital Information, Switzerland provides close loop systems for any printing ink machine. These are interfaced with X-rite systems. A production print sample is measured using X-rite scanning device and using the colour data, Digital Information System adjusts and controls the production keys. It saves paper, ink and prepares the machine for ‘print ready jobs’, thus saving time.
• ColorGate. Germany, provides proofing solutions. Its product, ProofGate helps printer to deliver digital contract proofing based on ISO 12647-7 and FOGRA standards.
• Alwan a French company provides ink optimization and press optimization. It optimizes ink cost to the tune of almost 30%. It delivers near perfect proof match.
• CutCNC China – This machine makes small samples, mock ups for printer or packaging person. It makes smaller quantities of samples for customers. It helps put his design in his thought to reality. It makes it very easy, fast and accurate. Correction is also very fast and the buyer gets clear idea of what is being offered.
In 1996-1997, AGS partnered with Fluid Management, The Netherland Company (now it is Fast & Fluid Management & Idex, USA company) and started marketing automatic and manual retail paint dispensers to all major paint companies like Asian Paints, Nerolac Paints, Berger Paints, Shalimar Paints, ICI (now AkzoNobel Paints). To meet the growing demands, AGS established manufacturing facility at Daman and started assembling very popular dispenser, BT Tintmaster under Fluid Management license. Till today, AGS have installed over 50,000 dispensers in the market and hold over 60% market share. To provide service support for these dispensers, AGS has built a team of 350 engineers across India covering 102 cities.
Around the same time, AGS made a joint venture with a French company, Fillon Technologies for manufacturing and marketing mixing systems used in refinishing industries (automobile industries), and not only established leadership but had 100 per cent market share. The major customers are Asian-PPG, BASF, AkzoNobel and DuPont.
Marching ahead, AGS tied up with CoPower Technologies, a Taiwan-based company dealing in textile laboratory dispensing systems and dyeing machines. Soon AGS partnered Hang Jie, another Taiwanese company specialised in innovative yarn dyeing machines for textile laboratories. These yarn dyeing machines are based on innovative ‘Magnetic Levitating Vortex techniques’ which stimulate production conditions in the lab using small samples, like 5-200 gms. It comprises a composite unit consisting of a winding machine to make bobbins for dyeing, a dyeing machine, a cleaning machine and drying machine thus providing a complete solution. There are 56 customers and many have placed repeat orders, major customers include Arvind Mills, NSL Textiles, Donear Textiles, Raymonds, Mandhana, Alok, Dicitex, D’Decor, etc. Both these equipment contribute to the automation in textile laboratories and provide Right-First-Time in the production.
For textile printing AGS supplies screen engravers for flat bed as well as rotary screen engravers from CST, Germany. AGS also represents, CST GmbH, a German company and ZUND, Switzerland for rotary screen engraver and also rotary screen engravers which are essential part of textile printing department. This business is handled from Surat office.
AGS provides a complete colour solution to any colour industry wherein colour is very critical. AGS has a team of colour professionals like colour technologists, textile technologists, paint technologists, printing technologists who understand most colour businesses and together they provide installation, software training, customer training and also after-sales service support.
AGS colour professionals offer solutions not only to the conventional colour industries like textiles, paints, plastics, packaging & printing ink industries, but also provides solution to food, cosmetic, soaps & detergents applications. Very shortly, AGS will provide a solution for beauty parlour customers (ladies only) for suggesting ‘right foundation crème’ depending on skin colour which will be measured using a special X-rite measuring tool. It will also suggest matching nail enamel and other beauty aids.
For handling spares & instruments, there is advanced packaging machine which prevents any damage during transportation. For non-dispenser colour business AGS has a team of 14 service engineers who are trained by X-rite, Copower and Hang Jie.
In an exclusive interview to The Textile Magazine, Mr. Gupte says: “It is very well established that the colour matching systems provide significant help to the colourists in his day-to-day colour problems. However, the color matching system works best where there is a reproducibility or repeatability of the process. Indian processing houses have a long way to go in-terms of standardizing their processes and raw material. Through various forums such as seminars and conferences, AGS contributes to this industry by imparting knowledge about best practices and ways to maximize profits.”
AGS also have a Test & Repair Centre at Navi Mumbai wherein all major instruments are repaired at board level. There is specially designed calibration room for calibrating all sensitive X-rite products. AGS stocks all spares parts for most spectrophotometers, dispensers & lightboxes. This takes burden off the customers for stocking spares parts.
AGS infrastructure includes a state-of-art help desk which operates 24×7 on all 365 days. Through this Command Centre, AGS offers first level service & technical support. All service calls are logged and closed within specified SLAs. There is escalation matrix in place and all unresolved calls beyond 72 hours are reported to the top management. The regular statistical analysis provides a wealth of information which is shared with the customers. This is mainly applicable to the paint dispensers and paint companies.