Established in 1991, the Sheltronics Group of companies, with its headquarters in Coimbatore, has emerged a leading manufacturer, exporter and supplier of textile machinery accessories and components of cutting-edge technology. Keeping in line with its tradition of being an industry frontrunner, the company is showcasing what, according to it, is the ‘first DSP autoleveller without differential gear drive but with E-Draft Technology’ for drawframes at India ITME 2016. This technology (Sedac-14) was introduced at ITME-2012 and well accepted by the market.
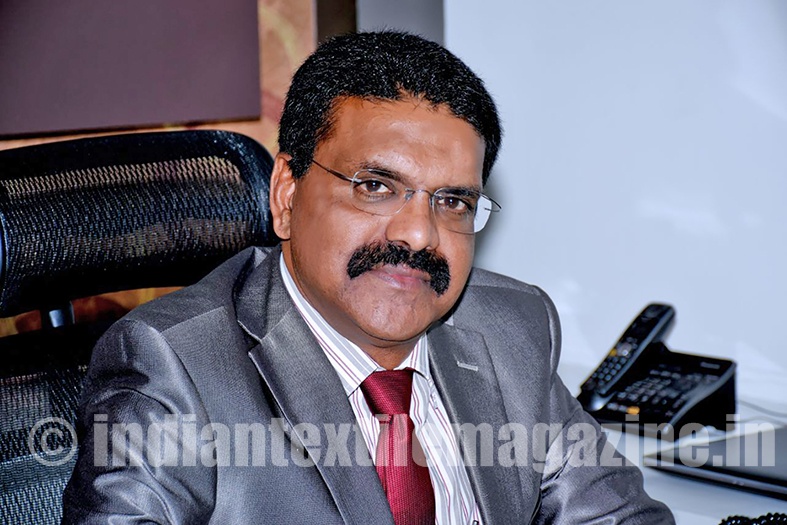
Sheltronics is proud to announce that the new autoleveller technology concept is now followed by the European textile machinery manufacturers for its uniqueness.
In an exclusive interview, Mr. C.M. Chandrasekaran, Managing Director of the company, an entrepreneur with wide ranging experience in electronics, textile and spinning, gave detailed insights in the new product launch. “The DSP autoleveller without differential gear drive unit with E-Draft technology for Drawframes is a truly one-of-its-kind product. It is a testimonial to our strong R&D focus.”
According to him, some of the salient features of the unique product include being the first autoleveller with ±35% infeed variation correction, electronic draft system which eliminates differential gear box and draft change wheels, energy saving, autolevelling action from the first to the last mm of the feed sliver, superb sliver evenness at highest delivery speeds achieved through high dynamic servo motor, and cost-effective automation technology.
Speaking further about the company’s participation in the premier event Mr. Chandrasekaran said: “We are clear about our expectations from the trade show. For us ITME is not only about gaining business. It is an excellent networking opportunity. We get to meet all our customers under one roof. It also helps us to discuss the latest technologies with industry peers as well as customers.”
The company which has moved into a latest state-of-the-art facility in 2012 caters to a wide range of clients. The products are moving all around the world through reputed textile machinery manufacturing OEMs. The company’s products have already made a name for themselves in countries such as Thailand, Zimbabwe, Bangladesh, Vietnam, Peru, Turkey, Iran, Pakistan, Egypt, Nigeria, Argentina, Russia, Guatemala and Indonesia.
Listing down the key strengths of the company, Mr. Chandrasekaran observed: “For us quality, technology and customer support services are of paramount importance. We have implemented a unique tracking system which allows for timeline analysis and traceability of a product. We can find out literally any information about a product – which month, date, to employee who assembled the product, the commissioning report, the board or the particular component on the board, etc. Every minute detail can be traced and analyzed using the system”.
Continuing further on the topic Mr. Chandrasekaran stated: “We also have implemented another system, namely, ‘FMEA’, i.e., Failure Mode Effective Analysis. In case of a failure, the system allows for a thorough analysis and helps us find the right solution. We are a systems driven company. It is the kind of systematic approach that has enabled our success story.”
In keeping with its image as a technology driven company, Mr. Chandrasekaran has ambitious plans lined up going forward. “We are already in the process of implementing IOT, i.e., ‘Internet of Things’. With this concept you can have control everything from a remote location. Whether it is to stop the machine or change certain specifications, every control will be there at your fingertip. We are already using the latest ‘Ethercat Technology’. We are a member of the Ethercat Technology Group of Germany. This kind of intelligent technology enables high-speed communication between machines and leads to increase in productivity with higher precision in control automation and less human interface.